On September 29, 2021, a recent foreign “Open Dynamic Robot Project (ODRI)” has been developed3D printingFour-legged robotic dogs and bipedal robots can be remotely controlled via Wi-Fi.
At the beginning of this project, I wanted to develop a low-cost brushless motor-based module that could be used to develop various types of robots.Now this project has been in progress for 5 years and will develop the platform with3D printingThe combination of cheap PCB and off-the-shelf components can make a robot at a fraction of the cost of the Boston Dynamics Robot Dog ($74,500).
At present, ODRI’s development module has manufactured a Solo3D printingRobot dog and a biped robot named Bolt.
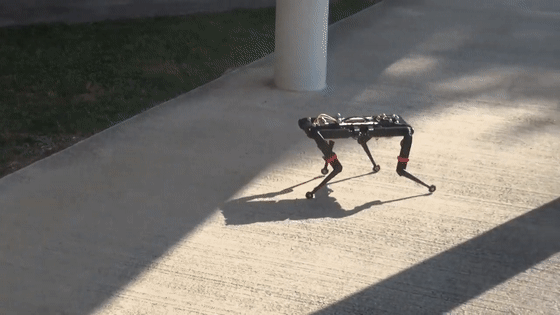
What is the Open Dynamic Robotics Project (ODRI)?
ODRI is a collaborative open source project that consists of several robotics research institutions: the Motion Generation and Control Group, the Max Planck Institute for Intelligent Systems, the New York University Tandon School of Engineering, and LAAS/CNRS.
The ultimate goal of this work is to meet the needs of the robotics research community, and many organizations are seeking a low-cost, lightweight and flexible research platform. ODRI’s robot development module can largely3D printing, And can be fully upgraded and modified, providing a low-cost advanced research and development path for robot teams with limited budgets.
According to ODRI, the robotic platform can be used to study the movement of animal-based limbs on surfaces such as gravel, soil, sand and mud, as well as the reinforcement learning of complex behaviors such as parkour. Some of these studies are very risky to try on high-cost platforms. In addition, it can also be used to study environmental manipulation actions, such as opening a door or pressing a button, and integrating with advanced communication technologies such as 5G wireless.
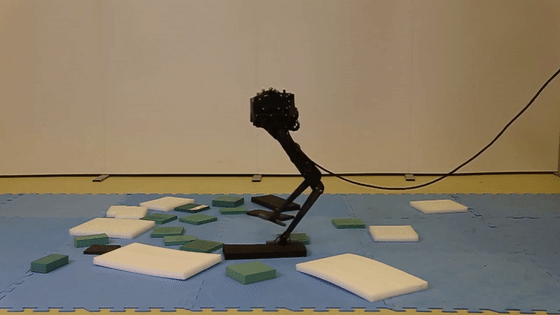
Integrate Wi-Fi together
Although this platform has been developed for many years and has achieved many results, one of the latest innovations is the integration of Wi-Fi connections. The algorithmic closed-loop control of the robot is hosted on a separate PC instead of an onboard computer. The main components installed on the robot are a control drive unit, a brushless DC motor, a wireless controller and a battery.
For such projects, the usual
standard
The approach is to use the sensor of the leg unit to calculate all positioning, torque and speed locally. However, calculating motion planning locally requires considerable local processing power, which makes development more difficult, because you must install a high-powered PC into a small space-especially if you plan to program the device to Perform complex movements.
With the smallest electronic components and lightweight3D printingComponents, ODRI successfully reduced the robot dog variant Solo to a total mass of only 2.2 kg, and the height of the hips when standing is about 24 cm.
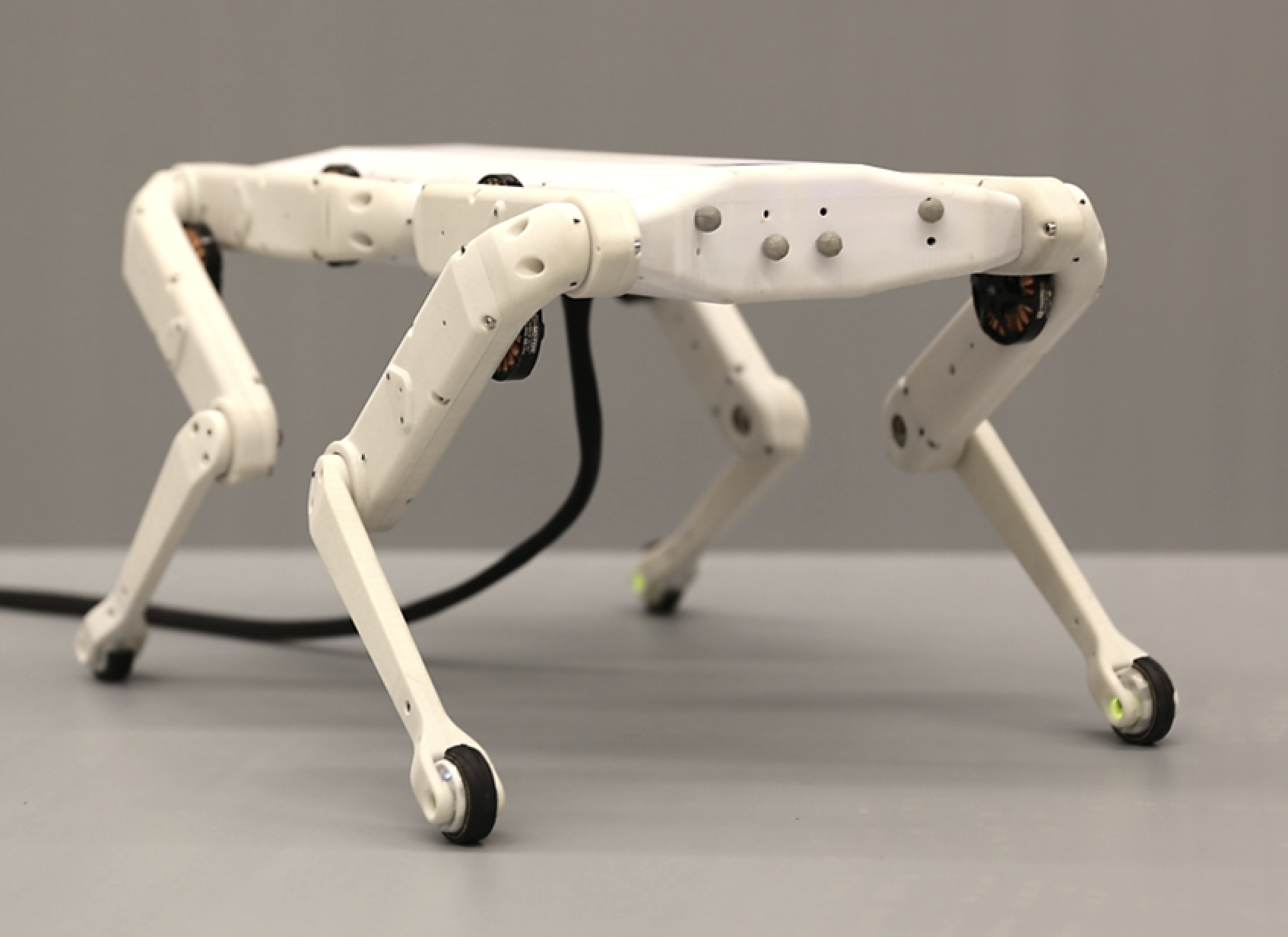
More details about the robot development module can be found in this paper “
An Open Torque-Controlled Modular Robot Architecture for Legged Locomotion Research
“In addition, the open source files of the robot can be found in the project’s
GitHub
Found on.
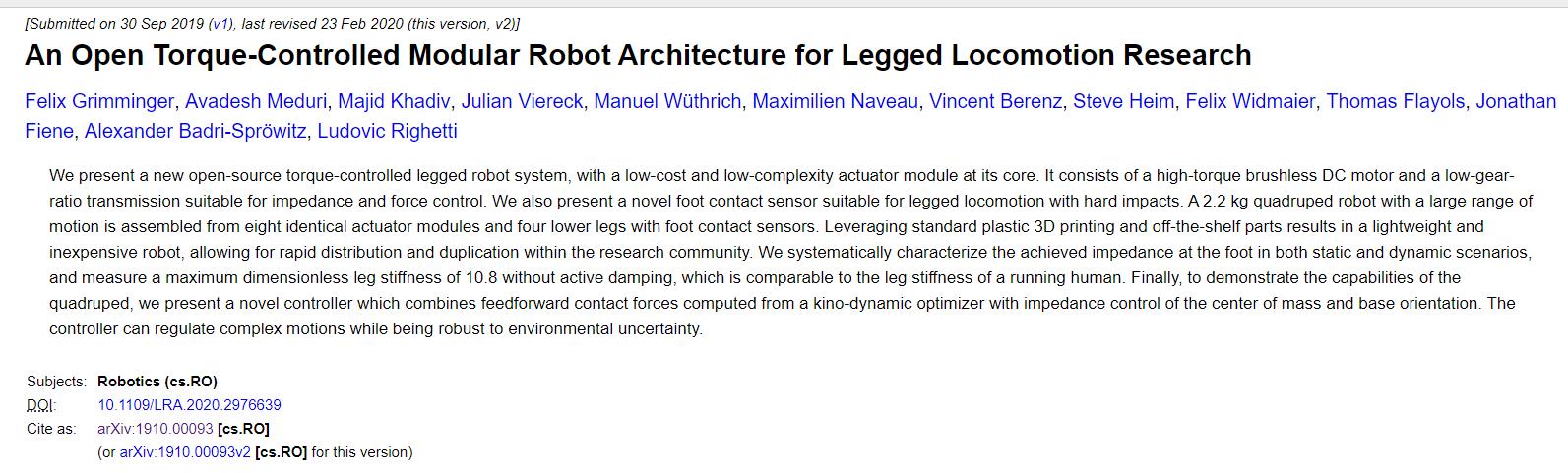
Similarly, XRobots’ robotics engineers and3D printingYouTuber netizen James Bruton recently started his3D printingThe V3 version of the robot dog works.This open-source project called openDog has been running for several years. In addition to motors, bearings and other components, it can be used at low cost.
FDM
On the system3D printing, Such as what Bruton just happened to use
LulzBot
TAZ Workhorse.
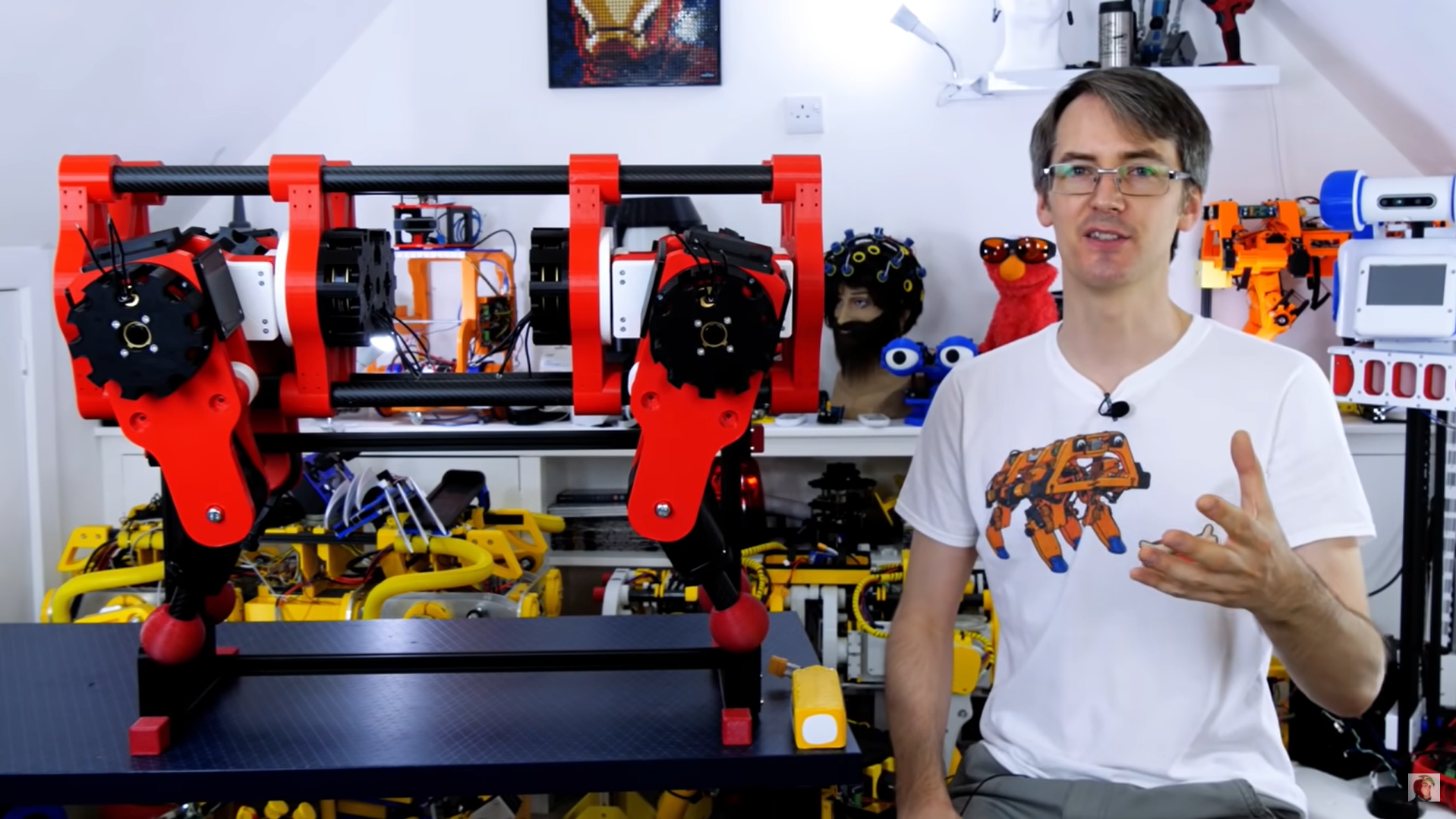
(Editor in charge: admin)
0 Comments for “3D printed open source quadruped robot dogs and biped robots can now be controlled remotely”