Analyze the scribed stress map with3D printingIn combination, MX3D built an ultra-light steel structure with a smooth mesh design and reduced its mass to 395 kg.According to Advenit Makaya, an ESA engineer, the successful manufacture of this structure shows the efficiency of MX3D technology and its development on the moon.
architecture
The potential of operations, it may also be used in the construction of thunderstone structures in the future.
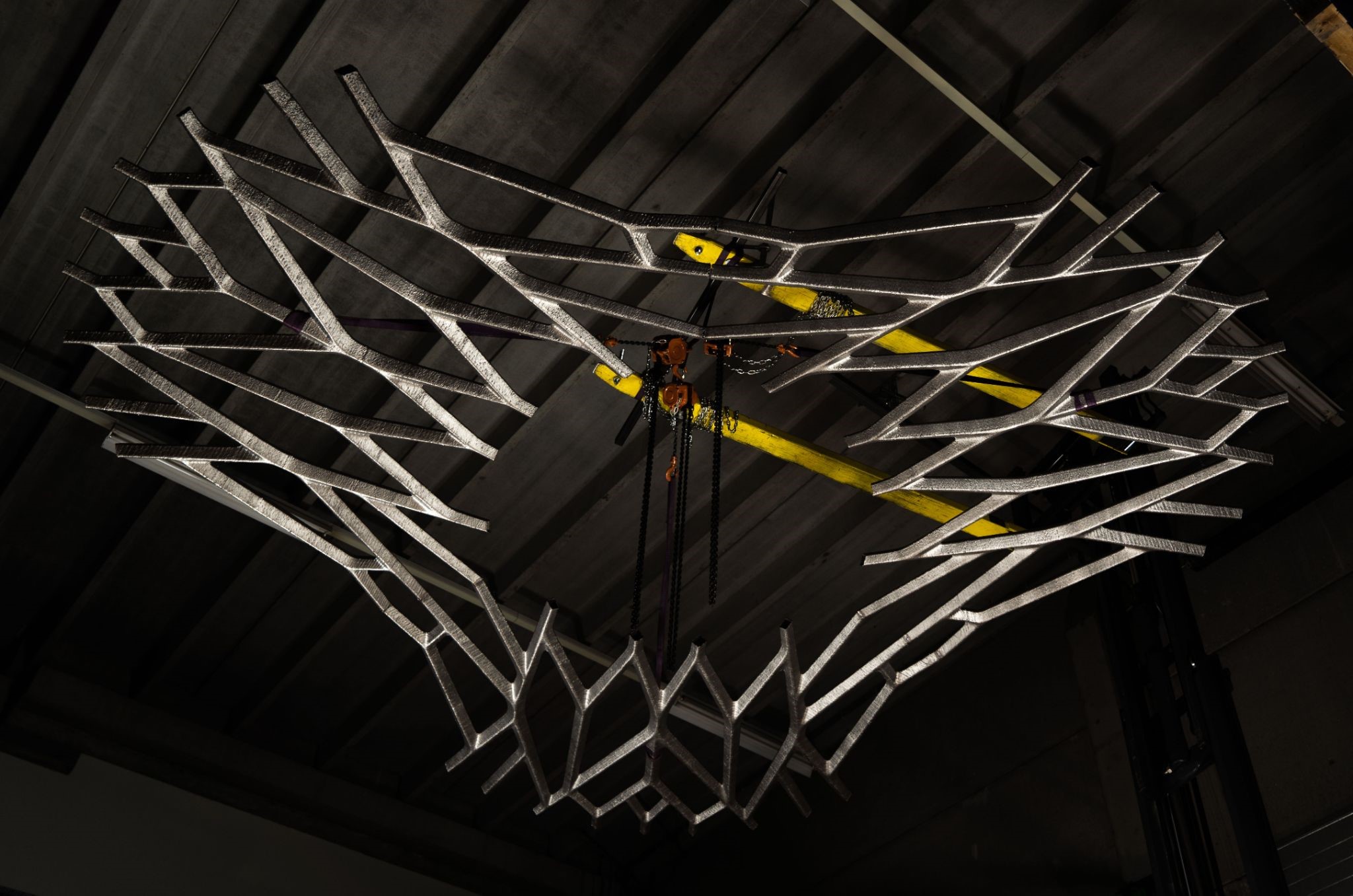
Lightweight “skeleton” design
This piece of 308LSi stainless steel floor took about 246 hours to complete. Once joined together, its width is approximately 4.5 meters. In the end, this architectural structure failed to be part of SOM’s “Life Beyond Earth” Venice Biennale as planned. However, according to Gijs van der Velden, CEO of MX3D, the project still proves the lightweight potential of its technology.
van der Velden concluded: “This is a perfect project. MX3D can use its experience in printing topologically optimized metal structures. Realizing the best use of materials is a company goal of MX3D, because it is just like when designing space applications. Similarly, every kilogram lost in the MX3D design is a direct victory for the feasibility of the project.”
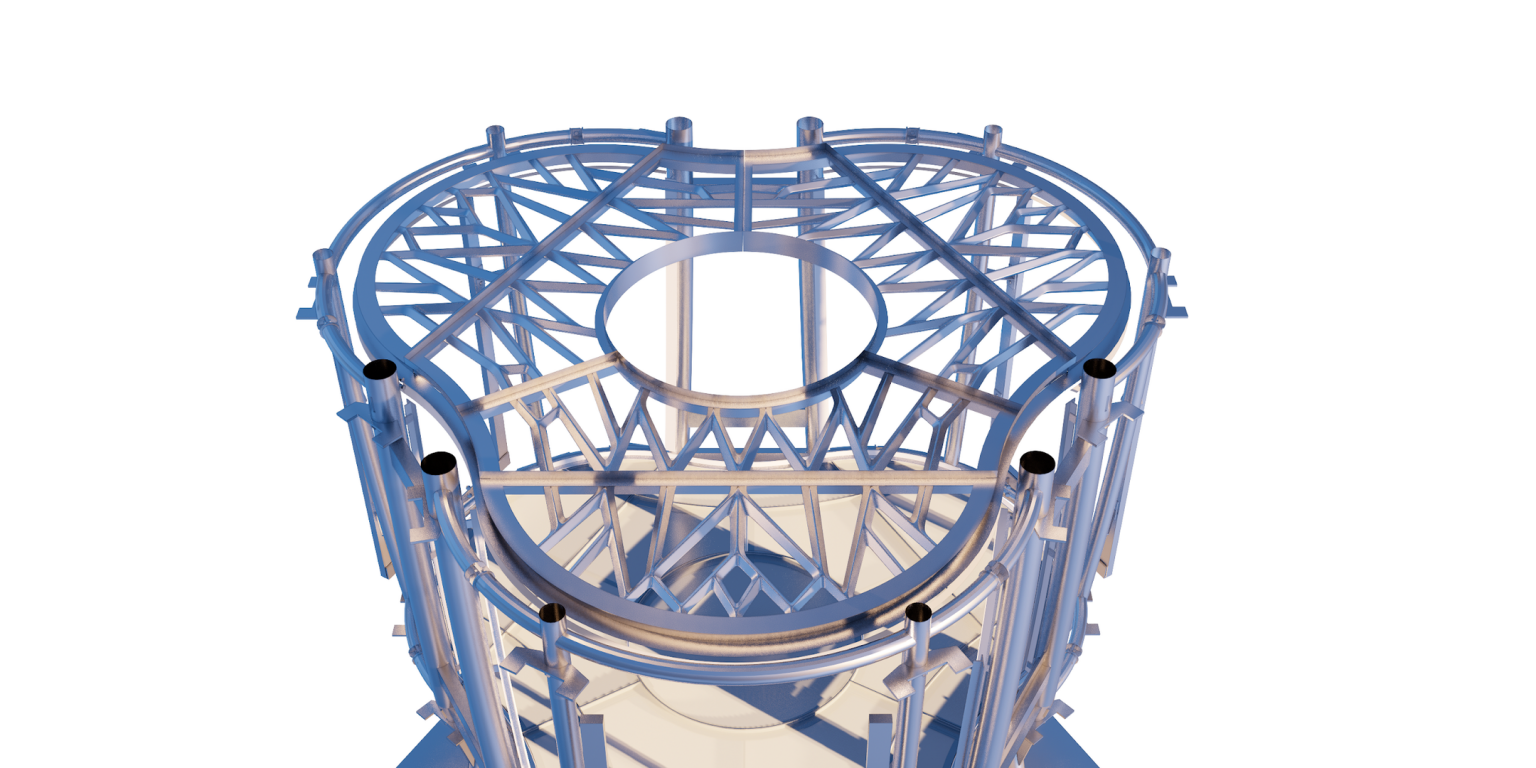
MX3D’s architectural expertise
At the time, van der Velden claimed that the bridge was just a small opening song for their company’s brilliant technology.In the nearest
aviation
After the success of the aerospace project, Thomas Rohr, the head of materials and technology at ESA, realized the aerospace potential of MX3D’s robot-led technology.
Rolle concluded: “The capabilities of MX3D demonstrate the inspiring consistency of engineering and art, and are another great example of how AM has entered our society. For space applications, this technology not only provides performance Improvements on the above, and can bring unprecedented and advantageous design solutions.
MX3D3D printingTechnology undoubtedly shows increasing scalability, but it is not the first technology used to build houses in extraterrestrial space. For example, ICON, headquartered in Texas, was entrusted by the National Aeronautics and Space Administration to develop an outer space construction system that can build a permanent lunar base using only the gypsum on the moon.
At the same time, outside the United States, scientists from the Technical University of Braunschweig and the Hannover Laser Center (LZH) succeeded for the first time in zero-gravity conditions.3D printingMoon rocks. The lasers installed on the rover by the team melted moon dust into lunar structures, so that pilots do not have to transport heavy cargo from the earth to the surface of the moon.
(Editor in charge: admin)
0 Comments for “3D printing lightweight lunar construction floor, MX3D launches sustainable space exploration mission”