Continuous fiber composite material has the advantages of low density and high strength, so it has become the main material for the structure of spacecraft at home and abroad. The traditional preparation process is complicated and costly, and at the same time, it lacks design flexibility, which limits the structure and performance of the final product.A research team from the University of Delaware developed a dynamic capillary driven3D printingTechnology, called local in-plane auxiliary heating3D printing(LITA), the fiber volume fraction in the composite material is 58%, and the mechanical strength and modulus have reached 810MPa and 108GPa, respectively.
LITA is based on the continuous capillary effect of liquid resin between carbon fibers: the heater locally heats the dried carbon fiber to generate a temperature gradient along the fiber direction, thereby reducing the viscosity gradient of the liquid polymer from the low temperature area of the fiber to the high temperature area, and the viscosity The reduction of sulphur causes it to flow between adjacent carbon fibers due to capillary force. At the same time, the high temperature will solidify the liquid resin, thereby realizing rapid and synchronized infusion and solidification. Further research found that the liquid resin quickly solidified in situ when the carbon fiber was injected. The composite material is densified due to the capillary action of the liquid resin between the fibers, thereby achieving a higher fiber volume fraction, which helps to improve the material performance.
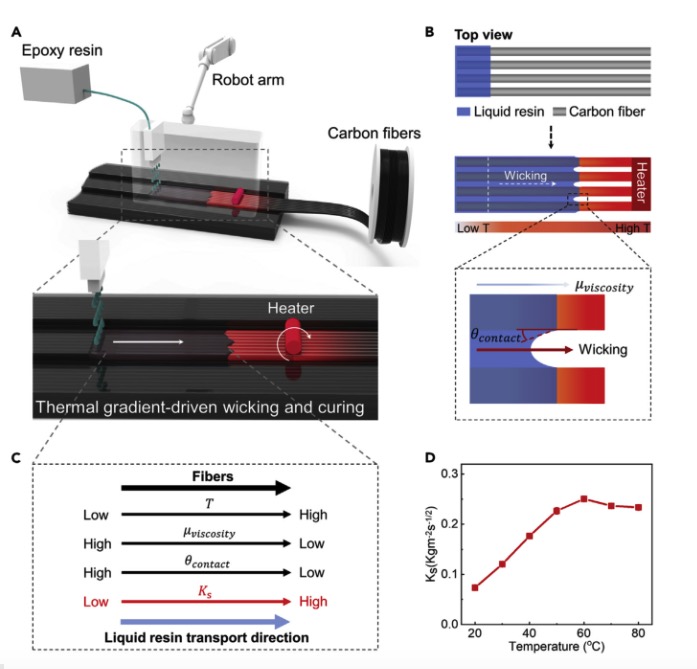
The researchers confirmed the dense structure of the printed material by observing the SEM photos, without voids and defects. The three-dimensional reconstruction results of tomography also verified these conditions, indicating that this method can prepare a continuous fiber-reinforced thermosetting composite with a good structure. The tensile strength and modulus of elasticity can reach 810MPa and 108GPa, respectively.
This technology can print complex geometric shapes on flat surfaces, as well as conformal structures on curved surfaces, and even print in free space. Compared with the existing composite material printing method, this printing technology has shown obvious advantages in terms of fiber length, polymer temperature, printing formability, geometric complexity and versatility.
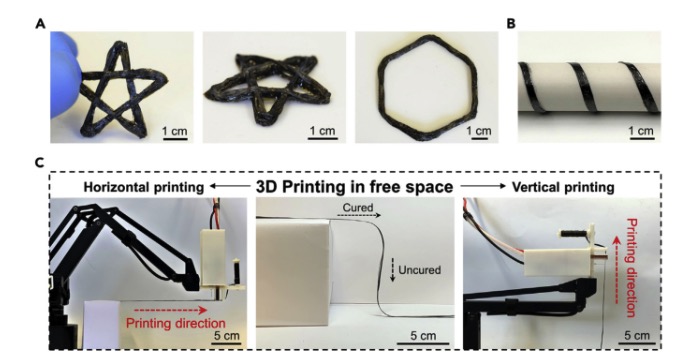
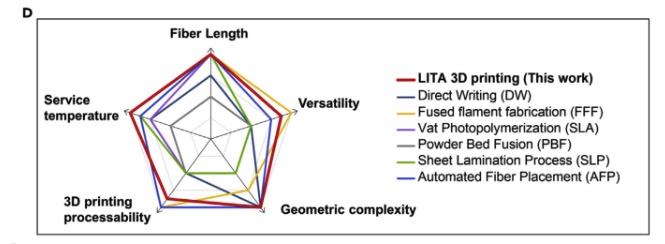
The researchers chose continuous industrial-grade carbon fiber and high-performance epoxy resin to achieve3D printingContinuous fiber reinforced thermosetting material, developed3D printingThe technology is easy to process high-performance composite materials, which is expected to provide a fast, energy-saving and large-scale3D printingThe method provides new opportunities for the design and manufacture of three-dimensional complex structures with engineering structures and multiple functions.
(Editor in charge: admin)
0 Comments for “3D printing of continuous fiber reinforced thermoset materials”