September 22, 2021, the University of Illinois uses3D printingThe technology produced the next generation of ultra-small heat exchangers, achieving a performance improvement of up to 2000%.
In order to design innovative geometric shapes, engineers have developed
Topology Optimization
Functional three-dimensional heat exchanger design
software
.This software is specifically designed to optimize existing heat exchanger designs to maximize heat transfer while minimizing part weight, which may be
energy
, Electronics and
aviation
aerospace
And other industries have a major impact.
William King, Professor of Mechanical Science and Engineering, said: “We have developed shape optimization software to design high-performance heat exchangers. The software allows us to identify 3D designs that are significantly different from traditional designs and are better.”
Necessity of Optimal Design of Heat Exchanger
The heat exchanger is mainly used to transfer heat energy from point A to point B. They are very important in many industries, and almost all complex systems that generate heat use heat exchangers. Including power generation systems, transportation, oil and gas processing, water desalination and thermal management of consumer electronics.
Currently, there are millions of heat exchangers in use worldwide, and their performance and efficiency are very important for reducing carbon emissions. People need high surface area heat exchangers to promote effective heat dissipation, while also being compact and lightweight. In some industries like aerospace, the size and quality of components have a direct impact on the performance, scope, and cost of the system.
In the past few decades, the design of the heat exchanger has not changed much. Mainly limited by traditional manufacturing technology, it is unable to manufacture complex structures, such as optimizing internal channels for heat flow.However, with the metal3D printingWith the development of technology, 3D heat exchanger designs that were previously considered impossible can be easily manufactured. All that is needed is a specialized software tool to design new and more effective devices.
Optimized tube-in-tube heat exchanger
The development team used three-dimensional design software to develop a special type of heat exchanger called a tube-in-tube exchanger, which is often used in drinking water systems and
architecture
Energy system. The characteristic of the tube-in-tube exchanger is that the inner tube is nested in the outer tube.They also set up a set of integrated fins inside the tube when designing, which is3D printingInternal design features that can only be achieved by technology.
After the design was finalized, the engineers printed the heat exchanger with AlSi10Mg and performed performance tests in a laboratory environment.3D printingThe heat exchanger has a power density of 26.6 W/cm3 and a specific power of 15.7 kW/kg, which is about 20 times higher than similar commercial heat exchangers.
Nenad Miljkovic, Associate Professor of the Department of Mechanical Science and Engineering, said: “We have designed, manufactured and tested an optimized tube-in-tube heat exchanger. The volumetric power density of the optimized heat exchanger is approximately higher than that of the current state-of-the-art commercial tube-in-tube equipment. 20 times”.
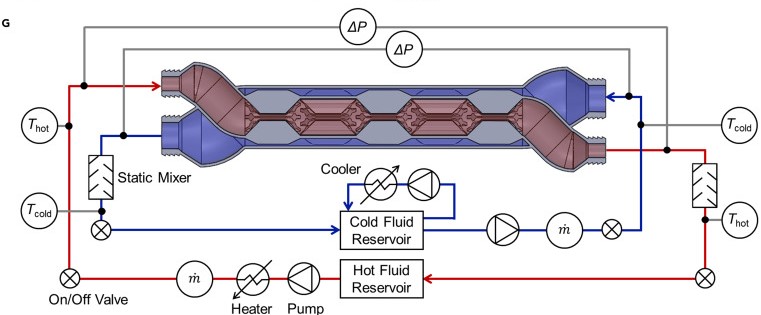
This research has been published in the paper “
Ultra-power-dense heat exchanger development through genetic algorithm design and additive manufacturing
“Medium. It was co-authored by Hyunkyu Moon, Davis McGregor, Nenad Miljkovic and William King.
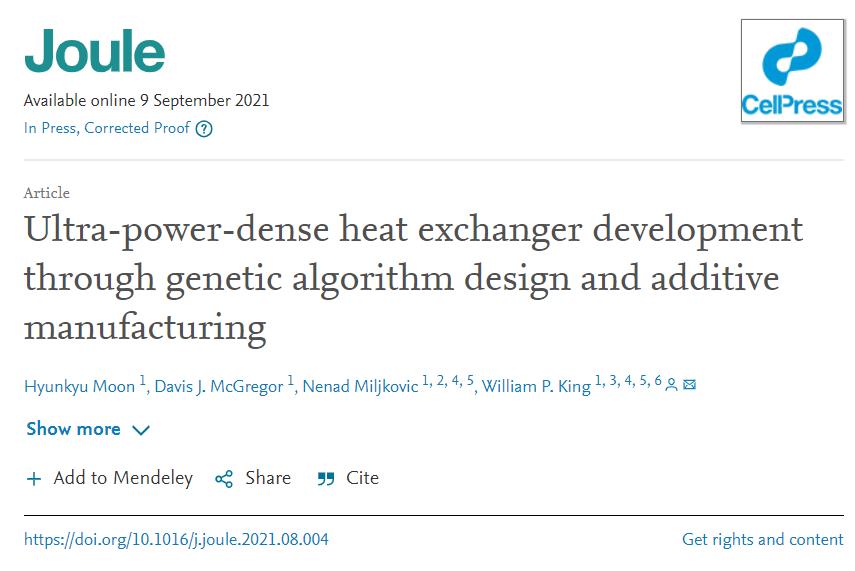
(Editor in charge: admin)
0 Comments for “3D printing optimized heat exchanger design, performance increased by 20 times”