Recently, Yang Yang from San Diego State University, Wang Ziyu from Wuhan University, and Chen Yong from the University of Southern California cooperated with the team.3D printingtechnology, to manufacture a new material of imitation mother-of-pearl structure with excellent mechanical properties and flame retardant properties. Such materials are expected to be used in military, fire-fighting equipment, machinery,
aviation
aerospace
and electronics. A related study was published in Research under the title “3D Printing of Nacre-Inspired Structures with Exceptional Mechanical and Flame-Retardant Properties”.
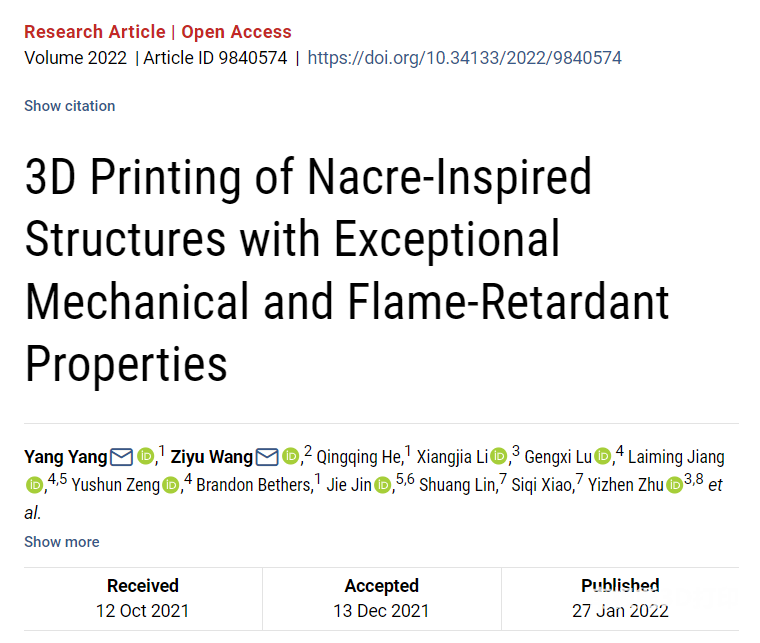
Links to related papers:
https://doi.org/10.34133/2022/9840574
Research Background
Today, many engineering fields, including industry, aviation, electronics and fire protection, require components that are lightweight, strong and heat-resistant.although
ceramics
The material has good performance in terms of heat resistance, hardness and strength, but is relatively brittle and has poor ductility and tensile strength. Although high molecular polymers have high ductility and tensile strength, their strength, hardness and heat resistance are poor. Combining these two materials has many benefits, but it is more difficult to overcome the incompatibility between different materials. To do this, the researchers found inspiration for efficient compounding in the mother-of-pearl structure of certain mollusks. Natural mother-of-pearl has a “brick mortar” (BM) structure, in which the neatly arranged calcium carbonate nanosheets are “bricks” and the silk fibroin filled between the “bricks” is “mortar”.
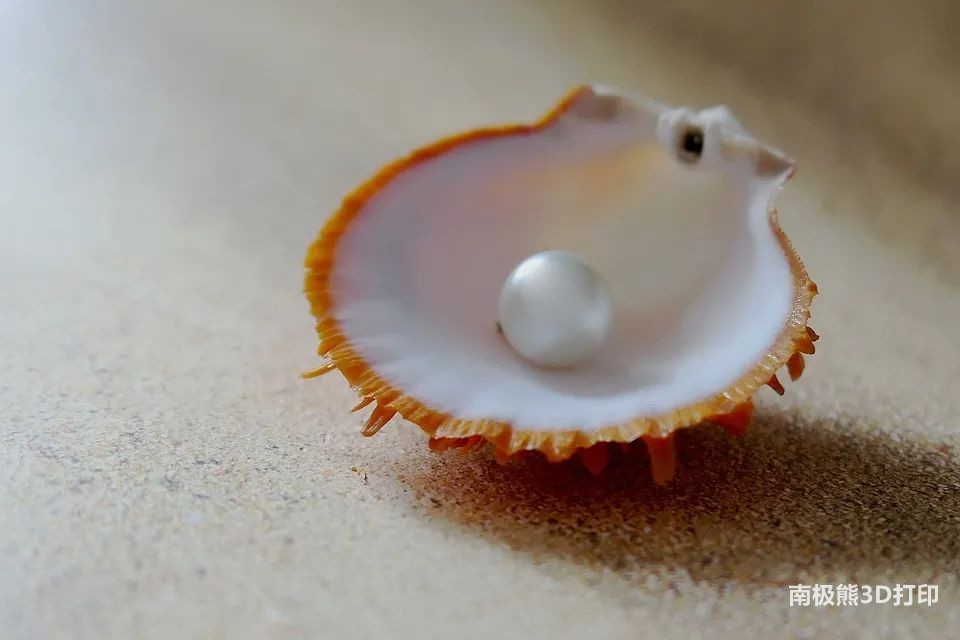
Research progress and prospect
Although there have been several studies using aligned boron nitride nanosheets (BNs) as “bricks” in nacre-like BM structures, they are only suitable for the fabrication of thin films and Block objects; based on electric/magnetic field/extrusion3D printingIn applications, the loading rate of the filler is low and the viscosity is poor. To overcome these shortcomings, the researchers developed a helical blade casting-assisted 3D printing process (rbc-3D) to produce imitation mother-of-pearl structures with complex shapes. This process can print structures with excellent mechanical, thermal and flame retardant properties at high BNs loading rates.
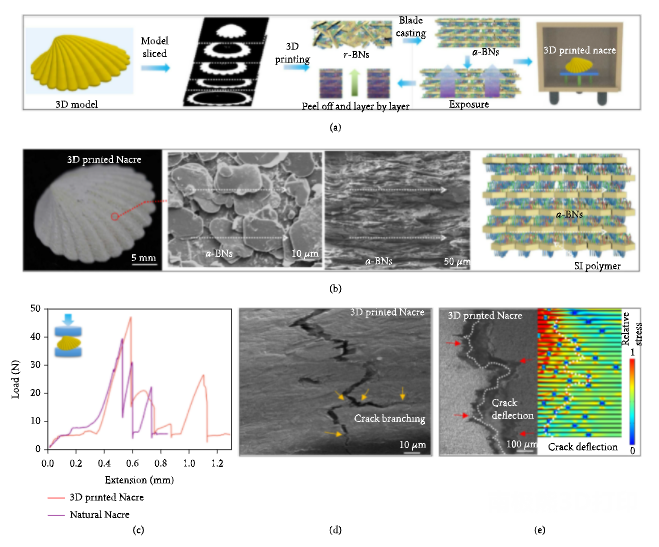
In the rbc-3D printing process, a monomer (trimethoxysilylpropyl acrylate) was first used to achieve surface modification of BNs to enhance the bond between the “brick” boron nitride and the “mortar” photocurable monomer. Adhesion, so that it forms a viscous compound with a weight ratio of 55%. This complex is then placed on a rotatable platform. When the platform is in operation, the flat-shaped blade pushes against the composite, and the resulting shear rate encourages the alignment of the boron nitride, which in turn forms the BM structure. In the composite at this time, BNs are evenly distributed, and the photocurable resin is cured into a desired shape by ultraviolet irradiation.
Using this process, researchers can manufacture helmets and armors with excellent mechanical, thermal and flame retardant properties (mechanical properties are better than natural mother-of-pearl), as well as parts with complex shapes for future military, firefighting equipment, Lay the foundation for wider applications in machinery, aerospace and electronics.
About the Author
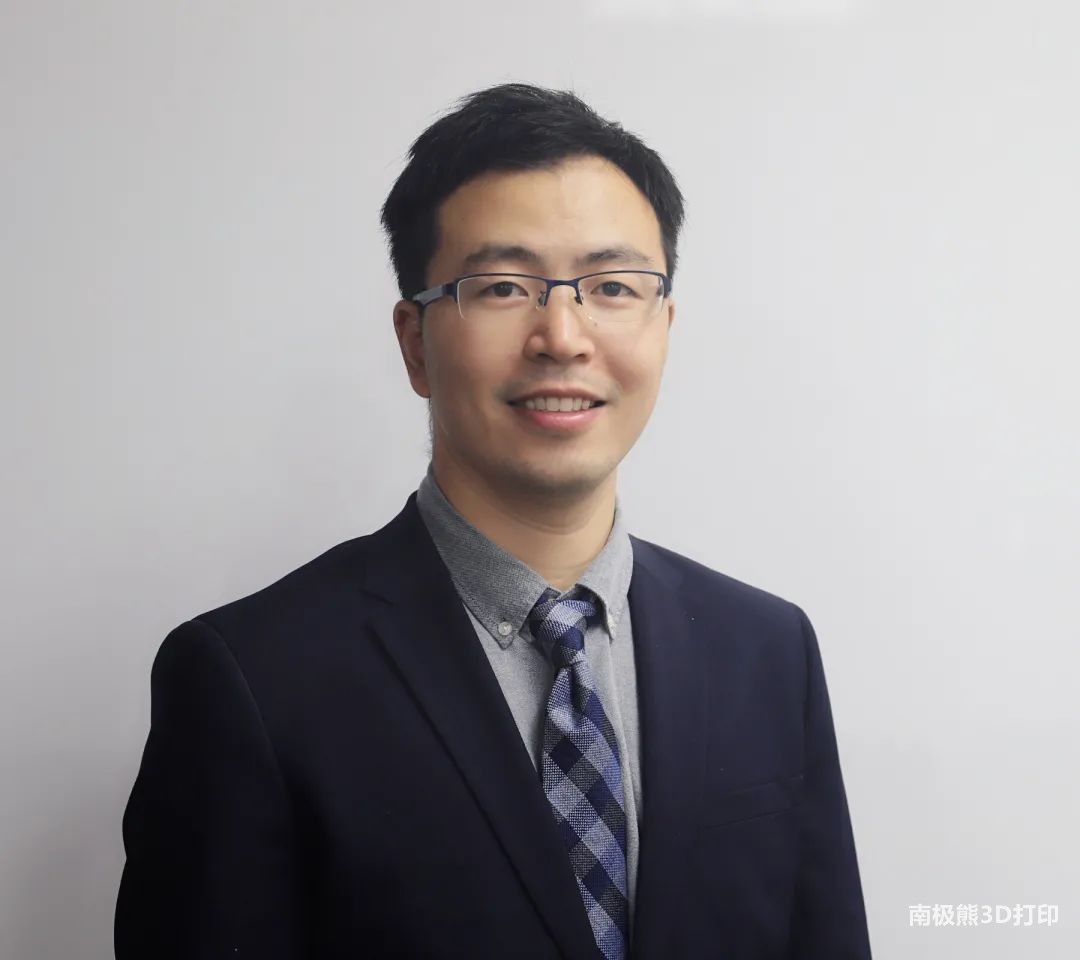
Yang Yang, Assistant Professor, Department of Mechanical Engineering, San Diego State University, USA
energy
Self-healing materials.
(responsible editor: admin)
0 Comments for “3D printing technology to create imitation mother-of-pearl structure with excellent mechanical properties and flame retardant properties”