It is reported that the traditional laser powder bed3D printingTechnology is to use meltingmineral powderThe method is layered layer by layer, and the challenge is that the manufacturing rate is low and the manufacturing capacity output is limited during large-scale manufacturing. One solution is to use multiple parallel laser beams for simultaneous scanning to improve processing flexibility. Recent studies have shown that the mechanical properties of the final product can be improved when two or more laser beams are used for scanning manufacturing.
There are still some obstacles to be solved when using multiple laser beams, such as the proximity of the molten pool and the interaction between them. In particular, the problem of the interaction between two adjacent, parallel molten pools has not been well understood. In this study, two laser beams are used to generate two parallel molten pools, which are offset in space. By using different spatial offsets, the experimental results show that in the completely merged and completely separated areas, the existence of a new area will produce periodic merging of the two molten pools. High-speed camera photography results show that there are two different situations in the formation of this merger, which we call head-head and head-tail merger. By changing the processing parameters, including laser power and spatial offset, periodic structural changes accompanied by different wavelengths can be achieved by using this dual laser beam method in engineering.
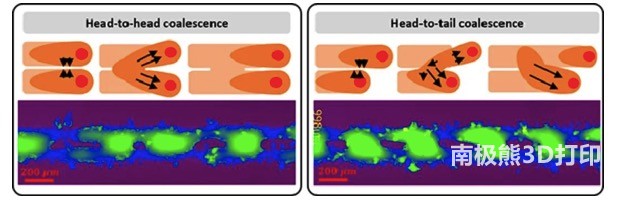
1. Background introduction
Additive manufacturing technology is also called3D printingTechnology and rapid prototyping technology is an advanced manufacturing technology that produces three-dimensional entities through layer-by-layer stacking.At present, metal AM technology is widely used
aviation
aerospace
,
car
And in many other industrial fields, this is because the technology has the ability to easily manufacture complex shapes and can economically manufacture complex parts. The powder bed (LPBF-LBM) printing technology using laser as energy is the most common metal AM technology. In the traditional LBPF, a laser beam with Gaussian energy distribution is used as an energy source to melt metal powder to manufacture the final product. However, this technology has slow manufacturing speed and other technical defects, making the technology’s application in industry still relatively small.
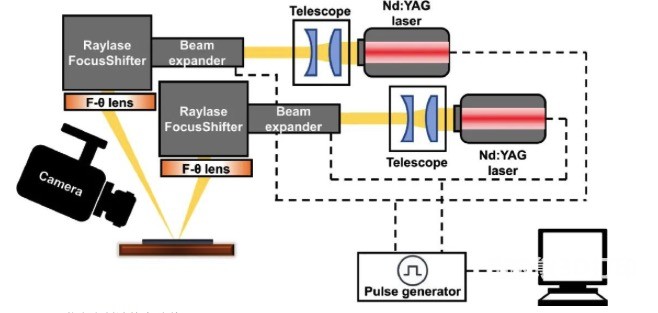
There have been many researches on how to improve the problems and challenges faced in the powder bed metal printing process. For example, a lot of research is about exploring the possibility of using multiple laser beams or customized beams to solve problems. Numerical simulation technology has also been developed to explore the shape of the energy distribution, such as how the energy of the Gaussian distribution affects the final product structure and performance. In the field of welding technology, the novel beam profile (DOE) generated by the use of diffractive optical elements (Diffractive Optical Element, DOE) is based on the theory of light wave diffraction, using computer-aided design, and using ultra-large-scale integrated circuit manufacturing technology on the substrate or Traditional optical devices are formed by etching steps or continuous relief structures on the surface), which provides a huge space for the size control of the molten pool, and thus improves the processing efficiency.
renishaw
Four independently controlled laser sources are introduced into the AM equipment. Hong et al. used this particular Renishaw device to compare the structure and performance of products made with a single laser beam and multiple laser beams. Zhang et al. conducted a similar experiment. The research of Slodczyk et al. showed that the rectangular beam obtained by DOE has a relatively large melting rate, and at the same time, the stability of the molten pool can be ensured. Sundqvist et al. also solved the analysis model of the spatial temperature field and the instantaneously changing laser beam conditions. This can help to quickly predict the profile of the temperature field during multi-laser beam welding. Furthermore, Tsai et al. constructed a three-spot powder bed printing system and introduced DOE into this device. Short processing time and at the same time low surface roughness can be achieved.
In order to better define the relative position of the two laser beams in this experiment, we introduce two parameters, as shown in Figure 2(a). The two red circles represent two laser spots, they are parallel and independent.
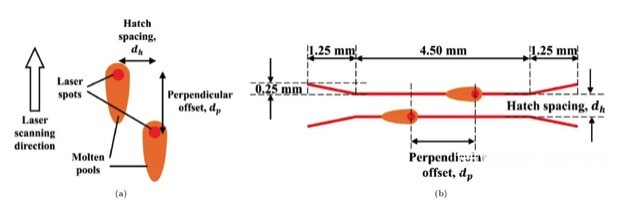
It is very obvious that the wider adaptability of powder bed printing lies in improving the flexibility of manufacturing and as far as possible using more parallel laser beams for processing in one processing. In the early days when two laser beams were used for processing. The molten pool generated by the two laser beams is used as a preheating or post-heating light source to reduce the temperature gradient and thereby improve the mechanical properties of the product. We believe that there must be a certain gap in these two situations, which is called the transition zone between the completely merged and completely separated regions. For example, the limit of the resolution of parallel beams has not been established. At the same time, despite the research and implementation of the macrostructure and morphology of a single molten pool channel, the key issue regarding the microstructure of the parallel laser beam processing is still unsolved.
In order to understand the problems faced above, we use two identical, parallel laser beams as the powder bed3D printingEnergy source for printing. By placing the melt channels of the two molten pools very close together, we studied the interaction of the molten pools when they were merged. After doing so, the resolution relationship between the two molten pools is established. At the same time, we began to understand the transition between two molten pools and melt channels gradually moving a certain distance from the beginning of the merger to form a complete separation.
In addition to the lateral spatial offset of the two molten pools, we also introduce a time offset between the two lasers, which can effectively produce a linear spatial offset. The introduction of this time shift allows us to further study the interaction of two close molten pools within this wide range of parameters. We have discovered a new region in which periodic structures can be generated in a certain spatial offset under each different laser energy. In addition, adjusting the spatial offset within this range can change the wavelength of this periodic structure.
2. Experimental system
Figure 1 shows the dual laser experimental system used in this experiment.In this system, two lasers with a Gaussian energy distribution with a wavelength of 1070nm operate in a continuous wave mode as a laser energy source and a laser beam. After being narrowed by a focusing mirror, they pass through a3D scanningThe system performs magnification, a 2D scanning galvanometer and an F-θ mirror. The scanning range of each scanning system is 178 × 178 mm exp(2). By arranging two scanning galvanometers side by side, an overlapping scanning area is 20 × 178 mm exp (2). The two laser beams and the scanning galvanometer are controlled by a control card installed in the computer. A pulse generator is used to control the emission of the two lasers and thereby generate a spatial offset in the two laser beams. However, this pulse generator only affects the switching of the two lasers. Once the laser beam is turned on, it will continuously emit laser light in the form of continuous wave.
3. Research results
Figure 3 shows a confocal photo showing how two different scanning distances affect the final weld pool. The situation at this time is the vertical offset maintaining a constant value. The different colors in the picture represent the different heights of the samples, which vary from the surface of the undisturbed base material in purple to the height of about 100 μm above the surface of the substrate to yellow. At this time, the power of the two lasers is 80W, and the scanning speed is 150 mm/s. The amount of vertical segregation was kept at 120 μm, and three different scanning pitches were used, 140, 180, and 270 μm. For all three experiments, the top line to the bottom line was achieved by vertical offset. The two lasers move from left to right.
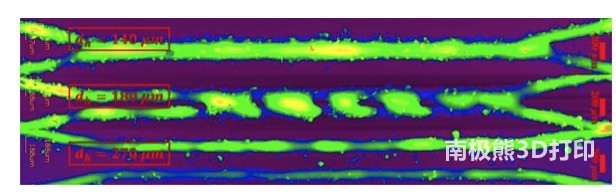

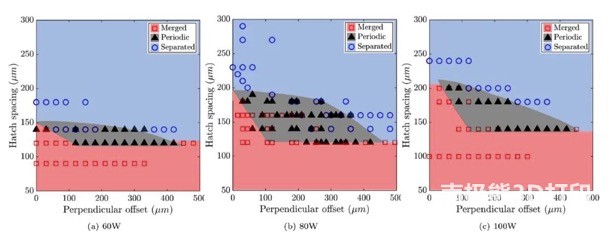
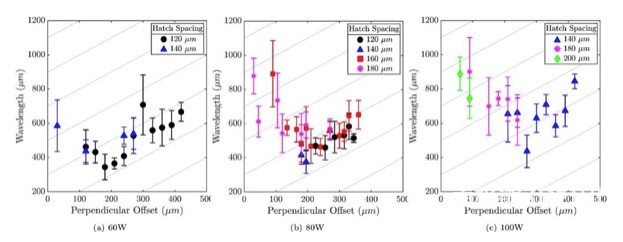
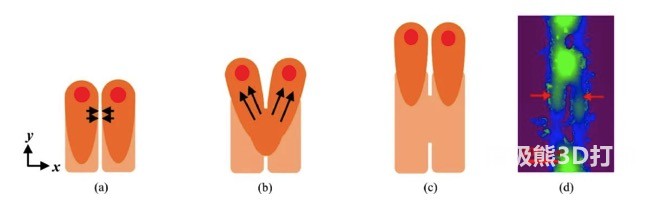
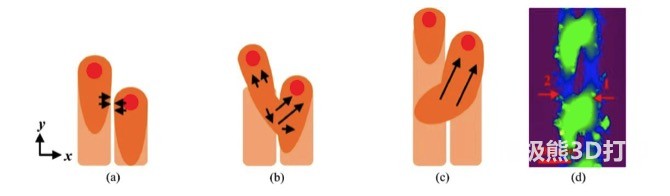
4. Main conclusions
The researchers introduced two parameters: scanning distance and vertical offset, as two identical lasers for powder bed printing. The researchers found a significant difference between the two completely merged and completely separated phases. This transitional phase produces a periodic structure that will be very difficult to manufacture with a single laser using traditional powder bed technology. For a specific laser power, the occurrence of a periodic structure makes a specific occurrence defined as the scan pitch and vertical offset. Generally speaking, in order to obtain a periodic structure, it is necessary to satisfy both the scanning pitch and the vertical offset and to have a higher laser power.
In order to further study the wavelength and formation mechanism of the periodic structure, two phenomena are revealed, one is the head-to-head merging, and the other is the head-to-tail merging. The head-to-head merger occurs when the vertical offset is less than the length of the molten pool caused by the two lasers. The head-to-tail merger occurs when the wavelength linearly increases with the vertical head-to-tail. When the offset increases. At the same time, by using the length of the molten pool to homogenize the vertical offset and wavelength, the researchers found that the wavelengths generated by different laser powers collapse into a single mode, and the situation at this time conflicts with the vertical offset.
In the next step, we will further explore this dual laser beam processing method to create periodic structures. For example, a longer molten pool produced by a higher scanning speed and higher laser power may be used to further confirm the current conclusion. The setting of this dual laser beam will help increase the manufacturing rate during additive manufacturing and it is possible to use multiple laser beams for surface texture. At the same time, we will analyze the changes in the microstructure obtained when the processing window is changed. We believe that the different energy distribution and the resulting molten pool produced by this method are different from the traditional process, and the microstructure is also different, including the size and orientation of the grains and the distribution of possible pores. Until then, this method will become a new method for manufacturing specific microstructures and customizing local properties in engineering.
(Editor in charge: admin)
0 Comments for “A dual laser beam system is used to create periodic merging of molten pools during the powder bed 3D printing process”