High precision3D printingThe technology is used to manufacture arbitrarily complex 3D structures with a resolution of a few microns and below. It has a wide range of applications and has become a real disruptive force in many industries.Despite the high precision3D printingTechnology has made great progress, but there are still many challenges to print out high-precision and high-quality 3D microstructures in a relatively flexible, low-cost, and versatile way.
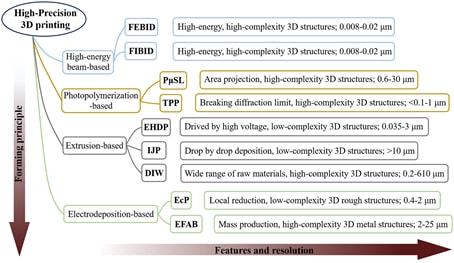
Direct Ink Writing (DIW)
Direct ink writing is based on extrusion molding3D printingTechnology, by extruding viscoelastic ink with shear thinning behavior in the form of microfilaments, and then stacking layer by layer to form a set 3D structure. However, so far, in most reports about DIW, the accuracy of the printing structure is still in the range of tens to hundreds of microns (mainly depending on the inner diameter of the needle used). The fundamental reason is that the effectiveness of extrusion molding through microneedles (with an inner diameter of several microns or less) is limited by the nature of the ink itself, because most inks that meet the requirements of microneedle extrusion usually have a low viscoelastic modulus (less than 103 Pa), resulting in poor moldability after the ink is extruded.In order to achieve the high precision of DIW3D printingTherefore, it is urgent to develop inks with suitable rheology for extrusion molding. At the same time, some additional strategies (such as heat treatment, deposition pool, UV light assistance, etc.) can also be used to achieve rapid curing of the ink after being extruded, so as to maintain its printed shape. In addition, high-temperature processing of the molded 3D structure may cause volume shrinkage, which helps to further improve the printing resolution to a certain extent, but this depends on the nature of the material itself. Because the volume shrinkage may cause new cracks in the structure, thereby weakening the mechanical properties of the printed structure. In the DIW process, the smaller the inner diameter of the microneedle, the greater the pressure required when the ink is extruded. At this stage, the microneedle is mostly made of glass, which is easily damaged during the high-pressure extrusion process, so the development can withstand high pressure The fine microneedle will greatly contribute to the high precision of DIW3D printing. In recent years, due to the combination of aerogel with multi-level nanoporous structure and DIW,3D printingAerogels have received extensive attention. At the same time, DIW printing hydrogels, flexible materials, and shape memory polymer materials are used in soft robots, smart devices,
biology
medicine
There will be great demand in many fields.
Two-Photon Polymerization (TPP)
Two-photon polymerization, as a non-linear laser direct writing process, uses a femtosecond pulsed laser to focus on a photosensitive material through a high numerical aperture objective lens. Non-linear two-photon absorption (TPA) occurs at the focal point of the laser beam, thereby initiating polymerization and cross-linking reactions. Since two-photon excitation causes a chemical reaction in the focal center and can break through the limit of diffraction limit, TPP can easily print ultra-fine structures that can achieve feature sizes below 100 nm (such as 65 nm).In order to achieve the high precision of TPP3D printing, First of all, high-efficiency photoinitiators and monomers/polymers with large TPA cross-section and high photoinitiation efficiency are required; secondly, photopolymer materials must have sufficient hardness to maintain a finer 3D structure and sufficient stability To deal with the volume shrinkage caused by the monomer to polymer; finally, it is necessary to precisely control the printing parameters (such as laser power, printing speed, incubation and slicing distance, etc.) to match the appropriate material system. At present, most TPP materials suitable for 3D micro/nano structures are patented materials, and it is difficult to modify them and add active ingredients to achieve specific functions. Therefore, protein-based biological macromolecules serve as TPP
3D printingThe continuous development of materials is expected to achieve 3D simulation of complex structures in the future, replacing biological tissues or organs. In addition, printing objects or structures containing inorganic components and nano-scale microstructures (which can reduce the weight of structural components), and TPP with a mixed material system with flexible selectivity and customized functional diversity
3D printingIt also has important research value in special fields.
Electrochemical Fabrication (EFAB)
The electrochemical preparation process involves the organic combination of semiconductor process and additive manufacturing, mainly including: 1. Dividing the 3D model into a multilayer flat mask file; 2. Using a photolithography process to produce multiple transients containing each layer of flat pattern structure Mask; 3. After repeated electrodeposition and planarization; 4. Final etching to obtain a 3D structure or device. The design freedom of additive manufacturing, coupled with the high precision and mass production of semiconductor manufacturing, enables the mass production of millions of high-precision components or equipment without assembly. It has a wide range of applications in the prototyping of monolithic micro-devices and integrated systems. It is an ideal technology for mass production of solid 3D metal micro-devices/micro-devices composed of a single layer with a thickness of 2-25 μm. The process involves multiple independent sub-processes, including structure layering, instant mask manufacturing, electrodeposition, planarization, and etching. Therefore, EFAB technology relies on the perfect integration of these multiple independent sub-processes, and its complexity increases as the number of manufacturing layers increases. Especially in the manufacturing process of a single micro device, multiple independent sub-processes make EFAB low efficiency and high cost, which brings huge challenges to laboratory research. Therefore, this technology is usually used to produce millions of micro devices/micro devices in batches to reduce costs. However, its unique layer-by-layer manufacturing mode will bring huge challenges to the alignment between layers. There are two main keys to improving the resolution: one is to minimize the layer thickness, which depends on the precise control of the planarization process and the precise positioning of each layer; the other method is to minimize the micro-holes formed by the photolithography process /Micro channel. EFAB technology has unprecedented capabilities in the manufacture of arbitrarily complex 3D metal microdevices/microdevices, especially for the preparation of multiple moving parts.
surgical
Operation
Micro devices and MEMS micro devices. In the future, research on these challenges will make breakthrough progress in improving the efficiency, quality and solutions of the EFAB process. Further development depends on technological breakthroughs and application opportunities.
In this review, mainly from the perspective of preparation methods and materials, the above three types that can achieve high precision are proposed.3D printingTechnology, mainly focusing on these3D printingThe materials used in the technology, such as Metallic Inks, Polyelectrolyte Complexes, Sol-Gel Inks, Photoresists, and Protein-based Biomass Molecular (Protein-Based Biomolecules Materials), hybrid materials (HybridMaterials), biocompatible alloys (Valloy-120, Edura-180, and Palladium), etc.; and their application fields, including microelectrodes (Microelectrodes), photonic crystals (Photonic Crystals, Tissue Engineering Scaffolds, Micro/Nanoscale 3D Templates, Biological Tissues or Organs,
Medical treatment
Equipment (Medical Devices), Micro-Electromechanical Systems, etc.At the same time, these3D printingThe development and challenges of technology provide a comprehensive view for the future of high-precision3D printingTechnology research and development provide benchmarks.In short, we are3D printingThe domain provides a comprehensive view of future trends and makes a general summary.Hope this review can help researchers and engineers fully understand high precision3D printingThe latest developments and challenges of technology, and stimulate new ideas and research directions.
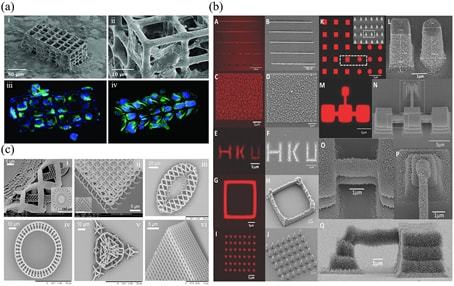
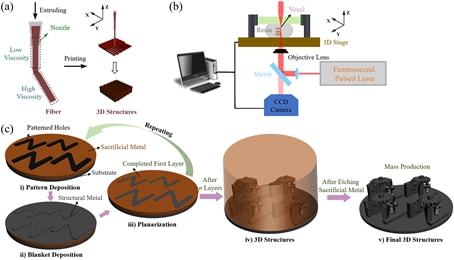
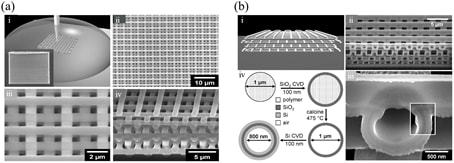
Related papers are published on “ES Materials and Manufacturing” with the title High-Precision Three-Dimensional Printing in a Flexible, Low Cost and Versatile Way: A Review. The first author of the paper is doctoral student Yang Jianming, and the corresponding authors are Associate Professor Du Ai of Tongji University, Professor Zhou Bin of Tongji University, and Researcher Li Bo of China Academy of Engineering Physics. The research team Dr. Dongxiao Han, Master Cui Ningxin, Professor Jun Shen, Associate Professor Zhang Zhihua and other authors also made outstanding contributions. This work was supported by the National Natural Science Foundation of China, the National Key Research and Development Program “Nano Science and Technology” key project, and the Shanghai Key Laboratory of Special Artificial Microstructure Materials and Technology.
(Editor in charge: admin)
0 Comments for “A joint review between Tongji University and China Academy of Engineering Physics: Flexible, low-cost and versatile high-precision 3D printing technology”