Research Background
3D printingTechnology is a rapidly emerging technology dedicated to providing a good digital framework for the modern production industry,
Unique advantages of high flexibility, short cycle times, low labor costs and less waste of resources
. In recent decades,3D printinghas been extended to
architecture
industry, the technology has shown great potential in generating complex building structures that are difficult to produce through traditional construction methods.Although using3D printing technologyThe construction period and labor cost can be shortened, but in terms of materials, the technology is still expensive because it cannot incorporate coarse aggregates, resulting in greater consumption of cement. Ordinary Portland Cement (OPC), the most commonly used material in traditional construction and 3D printing, generates a large amount of CO2 emissions during its production and does not have any positive effect on environmental protection during its entire life cycle. therefore,
develop alternative low-carbon building materials that enable3D printing technologyOverall sustainability is critical.
The production temperature of activated magnesia cement (RMC) is half that of OPC (700°C and 1400°C), and once hydrated, it is able to permanently absorb carbon dioxide from the atmosphere by forming stable hydrated magnesium carbonates (HMCs), thus making micro The structure densifies and increases strength. Current research shows that,
RMC can serve as a sustainable alternative due to its ability to permanently sequester CO2 with a subsequent strength increase comparable to OPC.
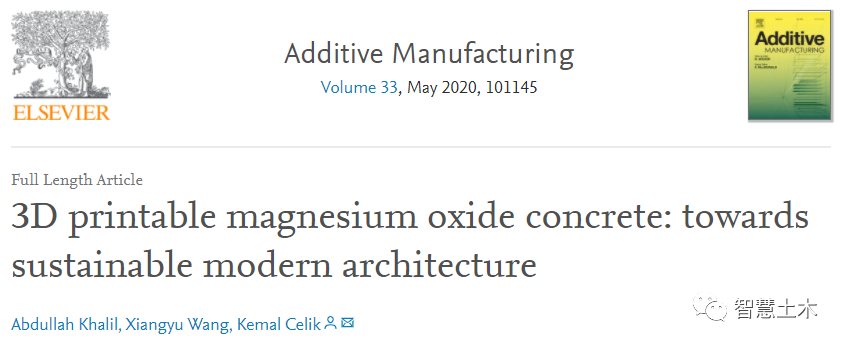
Research starting point
In recent years, 3D printing technology of low-carbon and environmentally friendly materials such as sulfoaluminate cement and potassium magnesium phosphate cement has been applied. However, the 3D printing potential of RMC is untapped, and the use of RMC and similar low-carbon building materials for 3D printing guarantees a sustainable future for the modern construction industry. Based on this, this paper proposes a 3D printed magnesia concrete for sustainable modern architecture.
research content
In this paper, microscopic test methods such as XRD, SEM, TGA, etc., combined with macroscopic mechanical and rheological measurements, were used to compare the mechanical properties, rheological properties and constructability of printed and poured RMC slurries. The results of the study show that by adding appropriate admixtures and only 3 wt.% corrosive magnesia to commercially available RMC, the proper rheology and buildability of RMC slurries are achieved, enabling 3D printing of complex structures to maintain Precise shape.
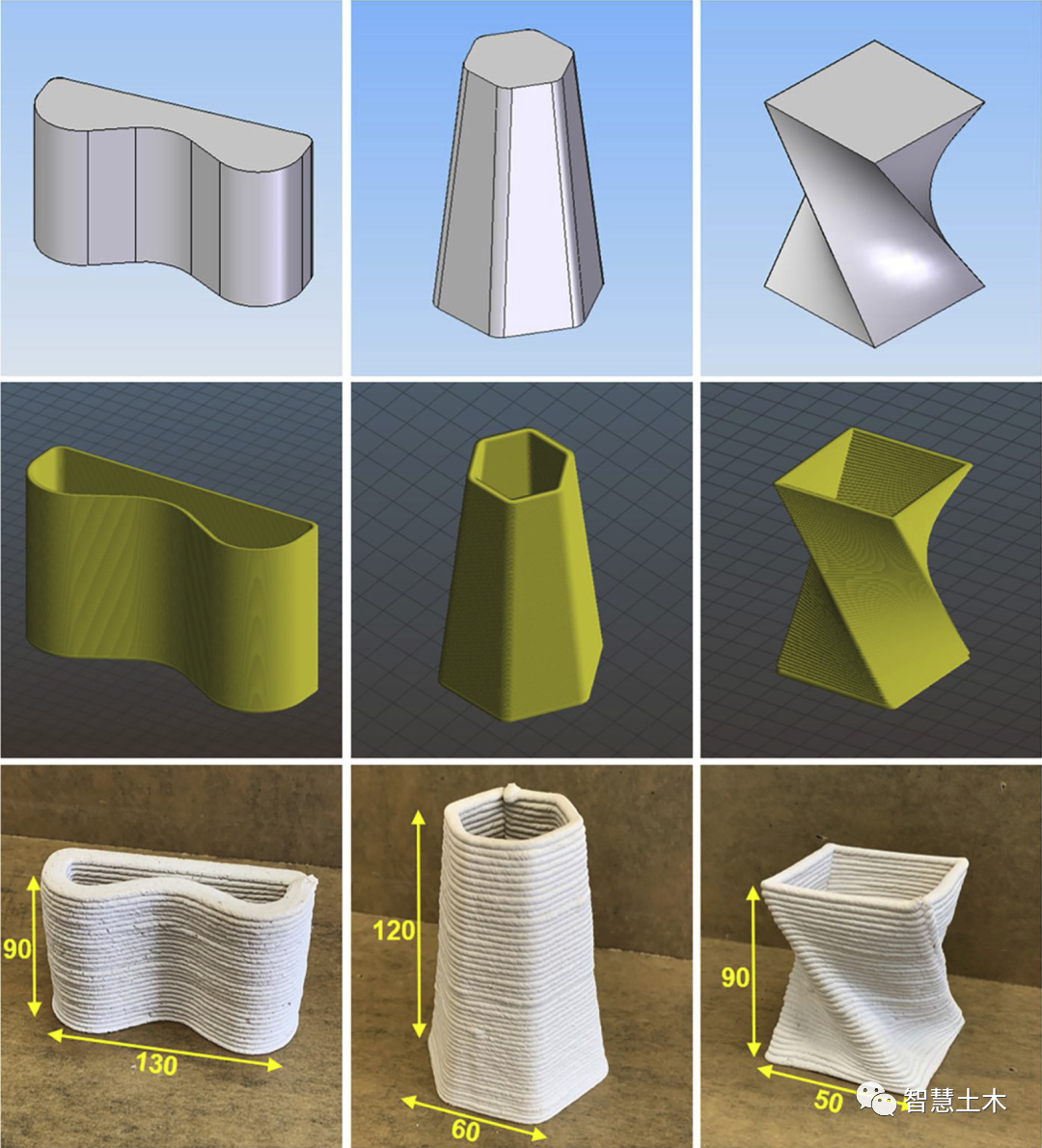
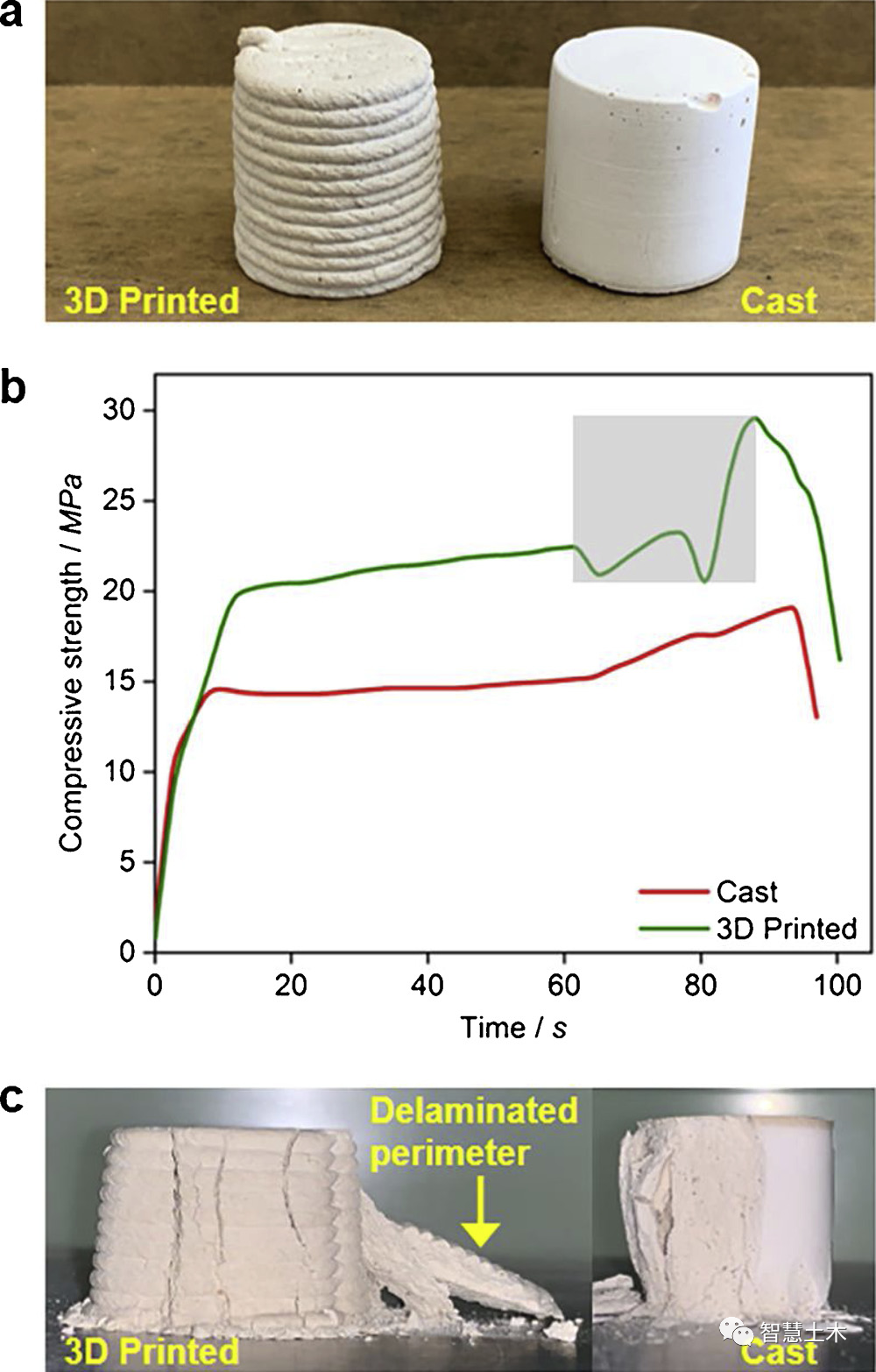
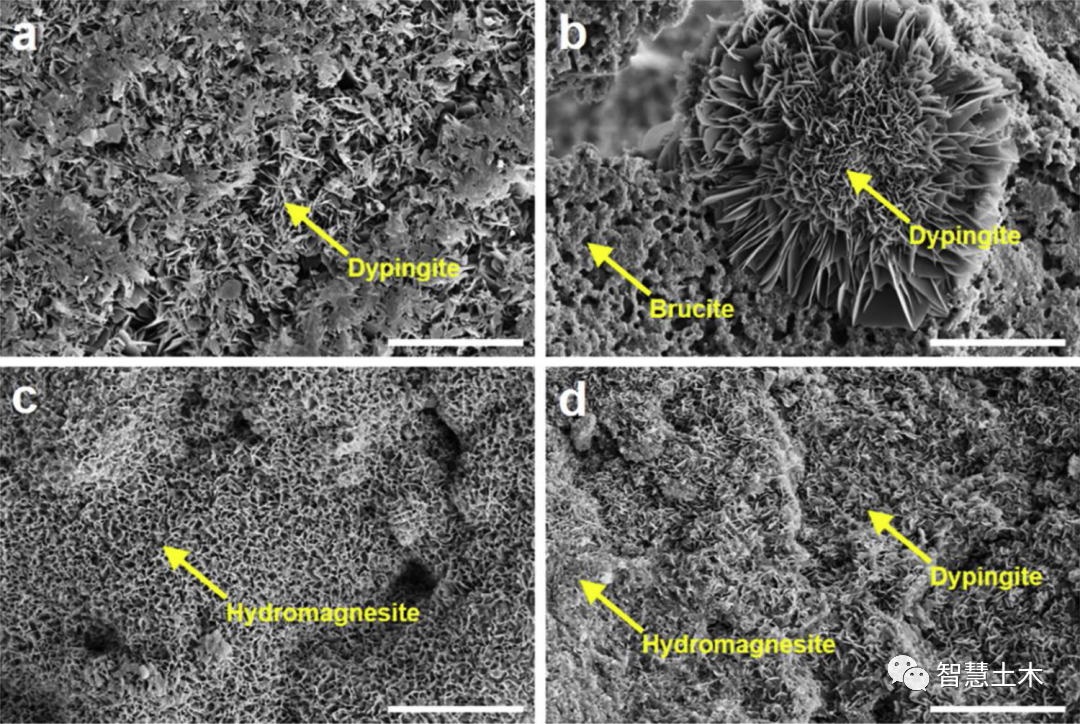
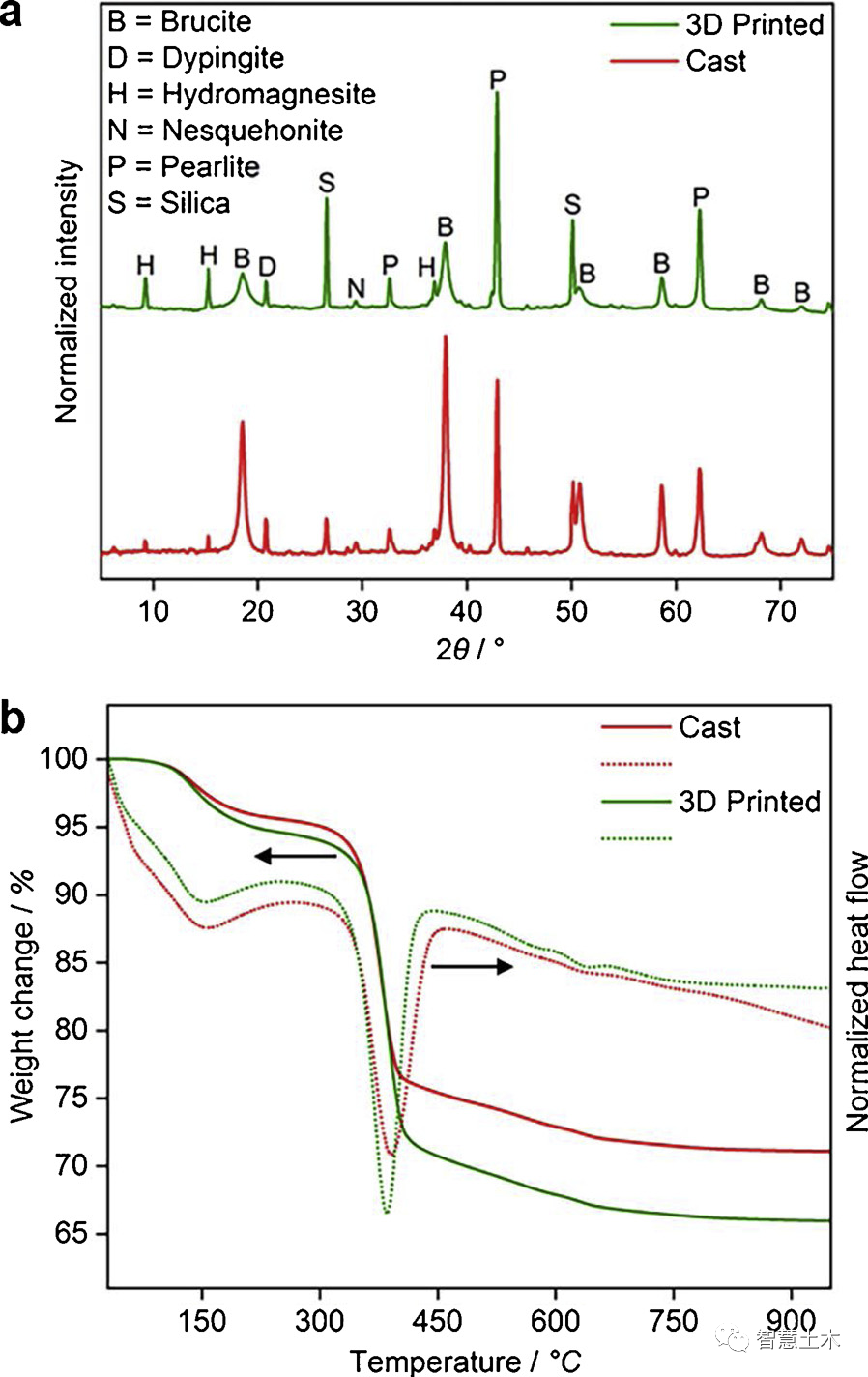
main conclusion
This study shows that,
With the addition of 3 wt. % cMgO and an appropriate proportion of admixtures, RMC can obtain excellent extrudability, flowability and buildability, making it suitable for 3D printing
. For moderately complex structures, 3D printing times were up to 60 minutes without any flow disruption or structural collapse, and they exhibited good shape retention and overall integrity even after accelerated carbonization. Furthermore, the strength of the 3D printed RMC is almost twice as strong as that of the poured RMC, which is attributed to the porosity of the 3D printed RMC which promotes the carbonization of the concrete. This study requires further research and development of 3D printing of RMC to reveal the effects of several aspects, including mixing components, printing parameters, and curing conditions, on performance to achieve higher degrees of carbonation and strength in concrete. The study also highlights the strong potential of RMC as a 3D printed building material for overall sustainability and modern infrastructure.
Literature link:
https://doi.org/10.1016/j.addma.2020.101145
(responsible editor: admin)
0 Comments for “Addit. Manuf.: 3D printed magnesia concrete for sustainable modern architecture”