It is reported that the original intention of the cooperation between the two manufacturers is to use additive manufacturing to develop large-scale steel strain wave gear flex lines. Strain wave gears are a special type of gearbox used in robotic arms and precision motion systems. They are compact, feature zero backlash, and transmit torque through a gear thin-walled cup called a flexline.
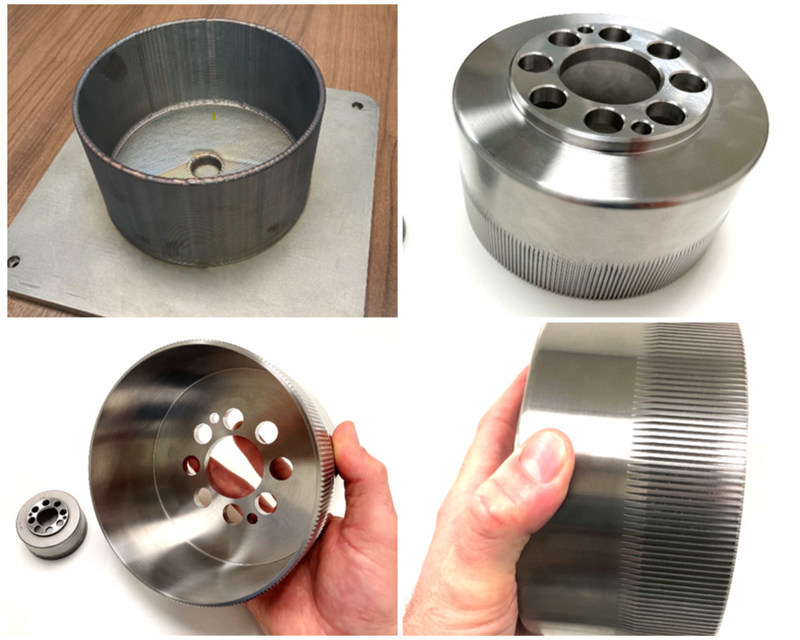
Go the 3D printing route
Dr. Yash Bandari, Business Development Manager at AddiTec, said: “We are delighted to be partnering with Amorphology to provide them with a solution to make parts by drastically reducing expensive machining. We look forward to working together to drive innovation.”
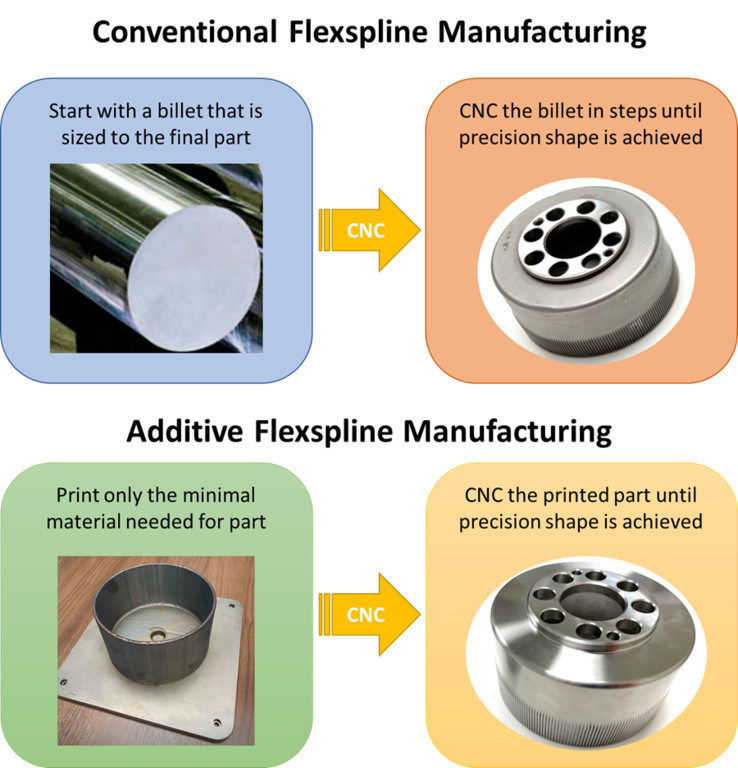
Meltio’s Laser Metal Deposition Technology
AddiTec CEO Brian Matthews added: “Meltio’s ability to integrate with CNC machines makes it a hybrid system. Hybrid manufacturing is a one-stop solution for the production of seamless metal parts that combines additive on a common platform and subtractive operations, thereby reducing the overall cost and time to manufacture parts.”
Amorphology and AddiTec have said they plan to advance their partnership into flexible lines of multi-material and functionally graded materials that are impossible to produce with traditional manufacturing techniques.
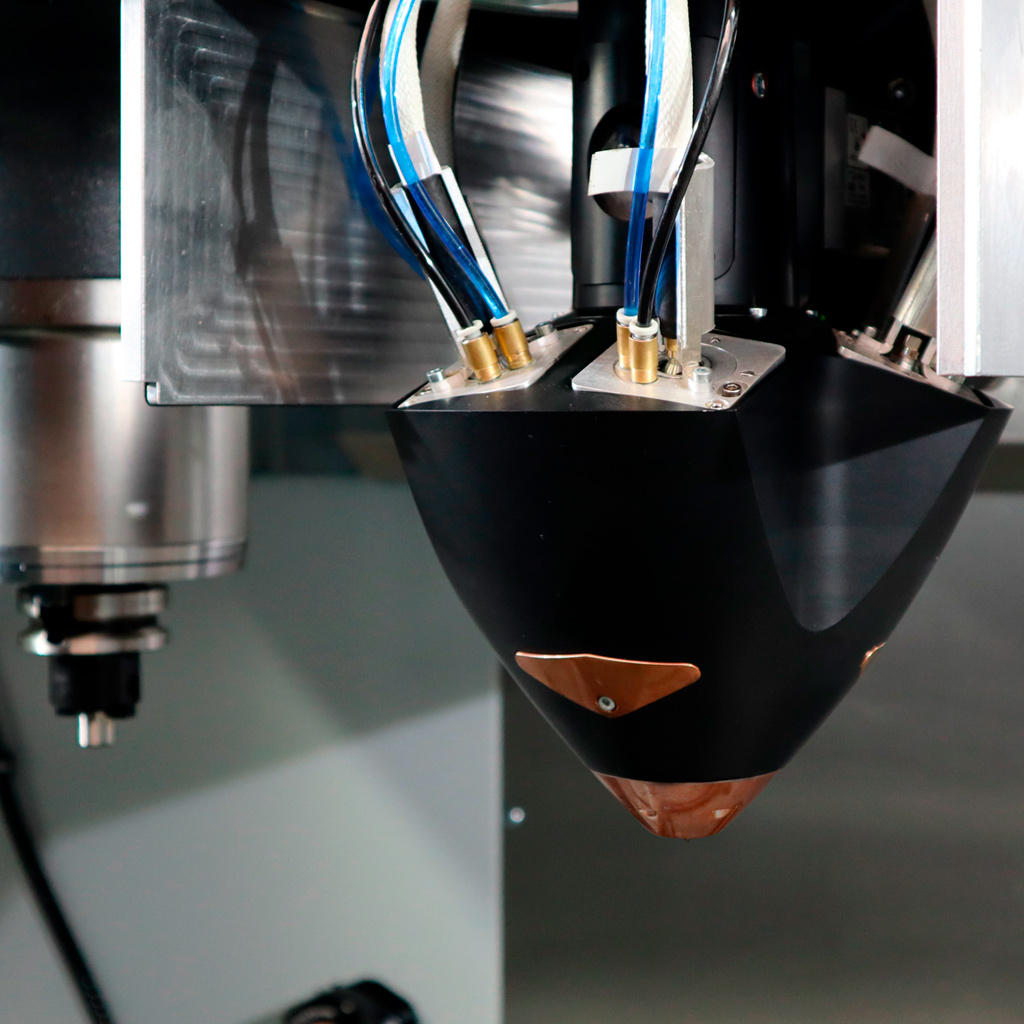
DED 3D printing has a wide range of applications. Just recently, an additive manufacturing consortium including Airbus, Safran Landing Systems and the National Manufacturing Institute of Scotland (NMIS) began working on a new hybrid DED 3D printing process for the aerospace sector. The technology will be used to 3D print critical aerospace components, such as those that make up aircraft landing gear, as well as in MRO applications.
(responsible editor: admin)
0 Comments for “Additec and Amorphology Collaborate to Hybrid Additive Manufacturing of Cost-Effective Strain Wave Gears”