Researchers from the Department of Mechanical Engineering of the National Institute of Technology in India willAdditive Manufacturing TechnologyandTopology Optimizationcombined, yesaerospaceThe bracket has been redesigned to reduce the weight of the part and improve the safety factor, thus proving that integrated topology optimization design and additive manufacturing can be an effective tool for designing and manufacturing lightweight parts.Additive Manufacturing (AM) Technologyis an advanced manufacturing process that can be used to manufacturebiologymedicine,carandaviationParts in aerospace and other fields. The main advantage of AM process is that any complex structure can be freely designed, reducing material waste and shortening production time, but in metal AM processmineral powderhigher cost. With the help of topology optimization, production costs can be minimized by reducing material usage.Topology OptimizationYesThe process of estimating optimal material distribution in a given product design space.
An overview of the research content:
In this study, the researchers used topology optimization to redesign the aerospace scaffold. The researchers considered not only material usage but also minimum residual stress during the design process (since residual stress is larger in AM processes due to higher temperature gradients). The researchers used CAD to redesign the aerospace support and completed the topology optimization through numerical simulation.based on
level set
The topology optimization method of the numerical simulation redesign and safety factor analysis of the part cloth was carried out. Through topology optimization, the weight of the part is reduced by 44.8%, and the safety factor reaches 2.3 (numerical analysis using AlSi12Mg alloy material data).The researchers carried out the printing process of the optimized parts
simulation
, so that the manufacturing time is minimized and the residual stress is minimized.simulated
SLM process
The parameters are 80W laser power, and the scanning speed is 1000 mm/s, and the simulation result is that the residual stress generated by the printing pitch of 90 μm is the smallest. The researchers validated the results using published research data on different types of parts.
The aerospace mounts designed in this study are under static load conditions in aerospace applications. In order to ensure the lightweight of the parts, the AlSi12 Mg material with good corrosion resistance and light weight was selected in this study. Aluminum alloys are commonly used in the aerospace industry for their lightweight properties and excellent corrosion resistance. The physical and mechanical properties of AlSi12Mg are shown in the table below.
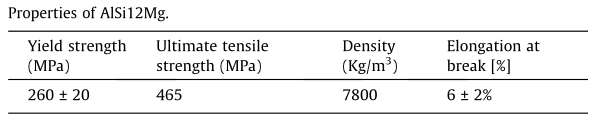
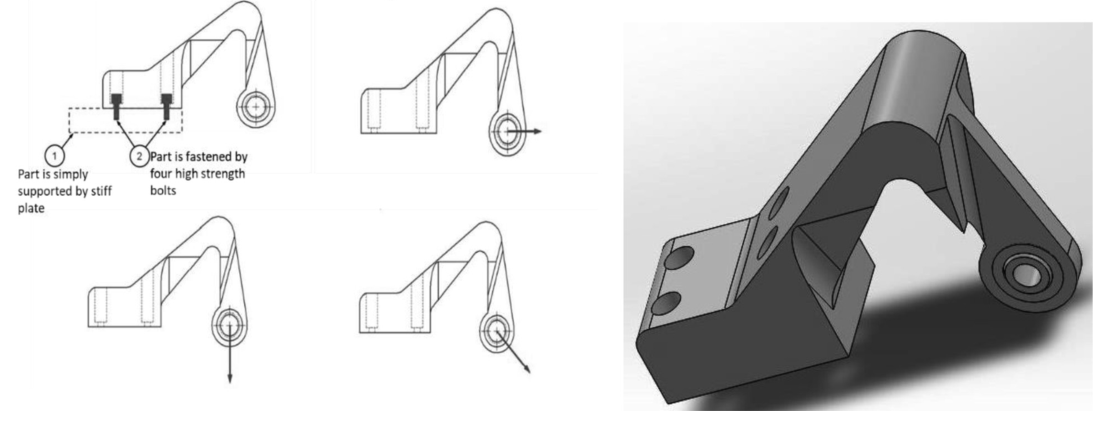
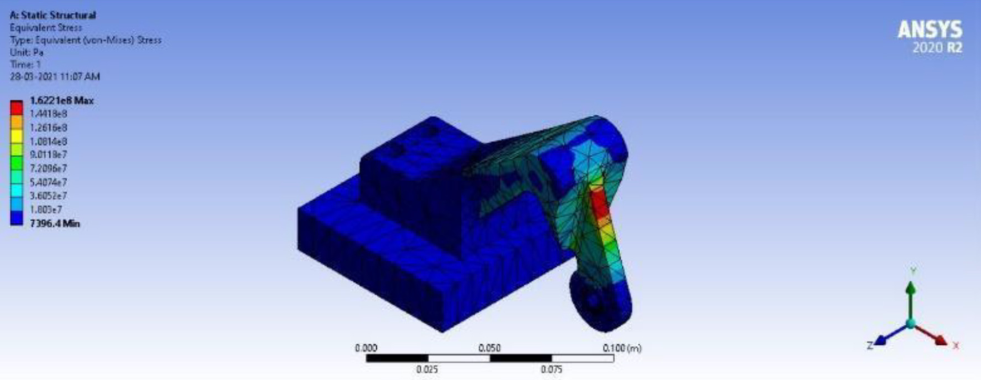
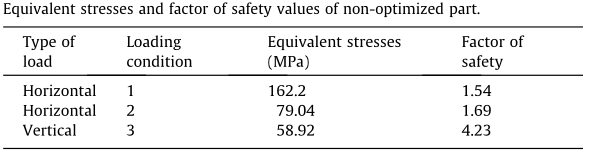
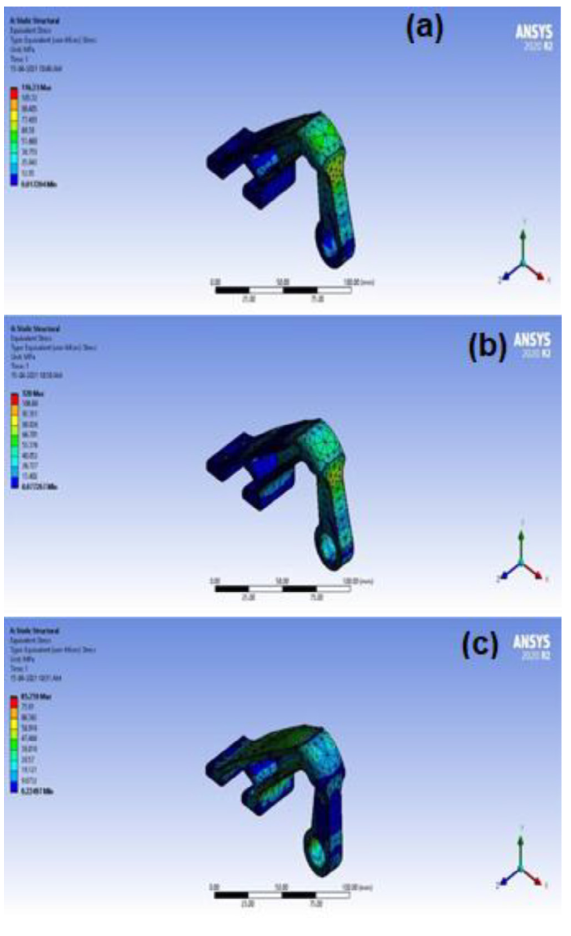
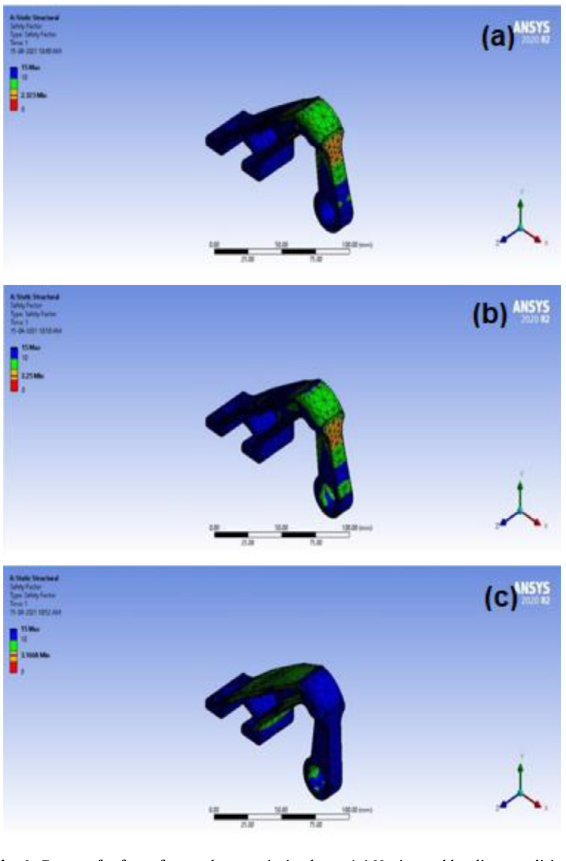

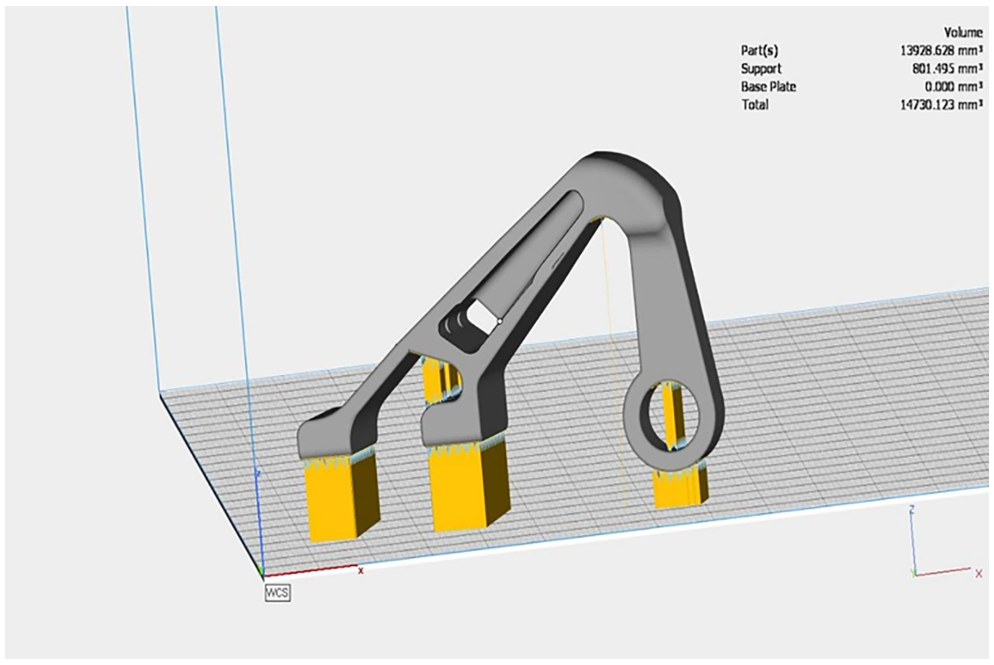
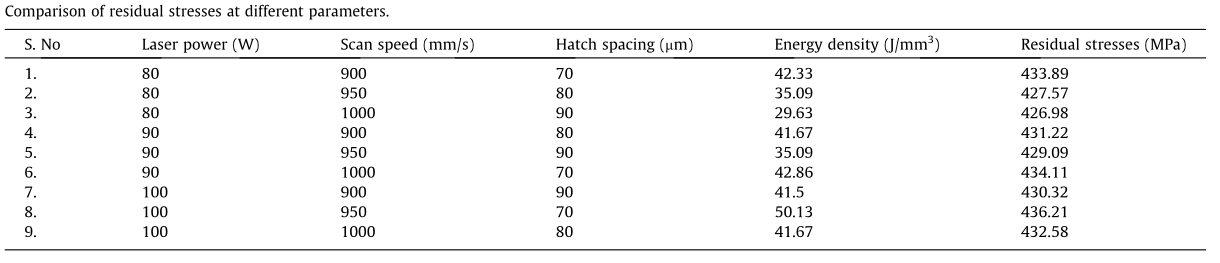
(responsible editor: admin)
0 Comments for “Additive Manufacturing & Topology Optimization: Improving Aerospace Part Performance”