Introduction: This article describes a systematic alloy design strategy to develop high-strength aluminum alloys for L-PBF. First, based on the composition of the reference Al-Cu-Mg alloy, three kinds of Al-Cu-Mg-Mn-Zr based alloys were studied using computational thermodynamic tools. Subsequently, the L-PBF processing behavior, microstructure and accompanying mechanical properties of the alloy made by L-PBF were studied. Alloys with different compositions show significant differences in microstructures: alloys without Zr added show coarse columnar microstructures and solidification cracks, alloys with low to medium Zr (1-1.98 wt%) show mixed The columnar and equiaxed microstructures, with high Zr addition (3.72 wt%), show a completely equiaxed microstructure, accompanied by a reduction in grain size to 0.7 ± 0.3 μm. All alloys containing ≥ 1.98 wt% Zr are crack-free. The designed Al-4.40Cu-1.51Mg-1.15Mn-3.72Zr (wt%) alloy has a yield strength of 561 ± 24 MPa, an ultimate tensile strength of 580 ± 16 MPa, and an elongation at break of 6.0 ± 1.3%. The current work shows the inherent potential of rapid solidification that occurs in the L-PBF process for the manufacture of geometrically complex, high-strength lightweight parts made of ultra-fine-grained ultra-peritectic aluminum alloys containing transition element additives.
Laser-based powder bed fusion (L-PBF) is an emerging additive manufacturing (AM) technology because it promotes huge innovations in the manufacture of metal components that require geometric complexity, functional integration, and advanced performance. It minimizes the integration of a large number of connections and processing steps required in traditional subtractive manufacturing routes.due toaviationaerospace,carwithenergyThe demand for high-strength lightweight structures in the field is increasing, so the use of L-PBF to make high-strength aluminum alloys (such as Al-Cu-Mg based alloys) is particularly attractive.
The rapid cooling rate (10^3 -10^7 °C/s) and spatial temperature gradient of the L-PBF process help to form a unique microstructure different from traditional casting or forging alloys. The characteristics of L-PBF include non-equilibrium microstructure with supersaturated phase, metastable phase, fine solidified structure and high dislocation density. Extensive solute capture occurs in materials cured under L-PBF conditions, resulting in higher supersaturation and reduced solute separation. According to reports, in the Al-11.5 at%Cu alloy solidified by laser spot melting, the extended solid solubility of Cu in Al ranges from 2.3 to 11.2 at%, which is significantly higher than the equilibrium solid solubility limit of 0.9 at%. The solubility can provide a large amount of solid solution strengthening and precipitation strengthening for the built alloy by forming well-dispersed nano-scale precipitates during the post heat treatment process.
However, the high temperature gradient (~10 7 °C/m) and directional heat dissipation of the L-PBF process also bring additional challenges, such as the formation of slender grains with strong morphology and crystalline solidification texture, and the Thermal cracking. Large columnar grains produced by epitaxial growth are often observed in materials made of L-PBF, resulting in undesirable orientation-dependent physical and mechanical properties. Hot cracks in high-strength Al-Zn-Mg, Al-Cu-Mg, and Al-Mg-Si based alloys have been widely reported. The formation of thermal cracks is closely related to the formation of high-texture columnar microstructure, high thermomechanical stress and high strain rate, both of which originate from the high cooling rate and high temperature gradient process of L-PBF solidification characteristics. Refining the grains and inducing a columnar to equiaxed microstructure transformation has been proven to be an effective remedy to eliminate the formation of hot cracks in L-PBF processed aluminum alloys, while achieving isotropic mechanical properties. Inoculation by incorporating transition elements such as Zr, Ti, Sc, and Ta has been considered an effective practice for grain refinement of aluminum-based alloys.
The laser scanning speed used in this study is relatively low at 83 mm/s. Increasing the scanning speed may lead to an increase in the cooling rate during L-PBF, which leads to a significantly higher level of element supersaturation in the Al matrix, and enhances the solid solution strengthening in the as-built state and the precipitation strengthening after heat treatment. Therefore, in order to explore the rapid solidification potential of the L-PBF process and make full use of the beneficial strengthening effect derived from the non-equilibrium microstructure, further research on inoculated aluminum alloys with higher hyperperitectic composition is needed.
Here, researchers at Leuven University designed an Al-Cu-Mg-Mn based alloy with low thermal cracking sensitivity and high strength. First, use CALPHAD-based thermodynamic tools to design alloy compositions. Adding Cu, Mg, and Mn can improve mechanical properties through solid solution and secondary phase strengthening, while avoiding the formation of hot cracks. In addition, different contents of Zr are added to form primary Al 3Zr phases with different contents to refine grains, relieve thermal cracks and enhance strength, and form supersaturated Al-Zr solid solutions to enhance solid solution in the as-built state Precipitation strengthening after strengthening and heat treatment. Subsequently, the microstructure and mechanical characterization of the system was performed to evaluate the workability of L-PBF and the performance of the designed alloy. The finite element method was used to conduct numerical L-PBF molten pool simulation to understand the influence of L-PBF process parameters on the sensitivity of thermal cracks and the formation of non-equilibrium microstructures. In this way, the potential of L-PBF in forming non-equilibrium microstructures and exploiting its inherent strengthening effects will be explored. Relevant research results were published on Additive Manufacturing with the title “Exploiting therapid solidification potential of Laser Powder Bed Fusion in high strength and crack-free Al-Cu-Mg-Mn-Zr alloys”.
Paper link:https://www.sciencedirect.com/sc … i/S2214860421003717
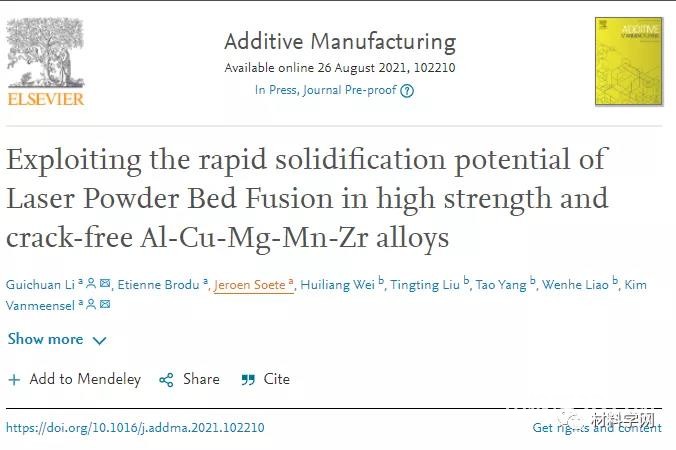
The L-PBF process can form a unique non-equilibrium microstructure in Al-Cu-Mg-Mn based alloys. In alloy A without addition of Zr, epitaxial growth and the formation of coarse columnar grains occur without nucleation particles; in alloys B and C, at low to medium nucleation particle levels, equiaxed formations are formed at the molten pool boundary Crystal grains, a bimodal microstructure of columnar grains formed in the center of the molten pool, with 1.00 and 1.98% by weight of Zr added; in alloy D containing 3.72 wt% of Zr, complete formation with a large number of nucleated particles The microstructure of the shaft. Therefore, the FCC-Al grain size is reduced from 58.2 ± 31.9 μm in alloy A to 3.3 ± 2.4, 1.3 ± 0.7 and 0.7 ± 0.3, respectively, in the designed Al-Cu-Mg-Mn-Zr alloys B, C and D The middle is μm. (b) There are high dislocations in the aluminum matrix of the finished sample. (c) In the center of the molten pool of alloy D, the solubility of zirconium in aluminum was detected as high as 1.3 ± 0.1 wt%. (d) The L-PBF process can form a cubic L12 structure in the Al-Cu-Mg-Mn-Zr alloy designed with metastable Al 3 Zr phase. The Al 3 Zr particles adopt a rectangular parallelepiped shape with a dendritic morphology or have obvious The “flower” shape of concave edges and protruding corners shows that the average Al 3 Zr particle size in alloys B, C and D are 46 ± 13, 156 ± 42 and 442 ± 136 nm, respectively.
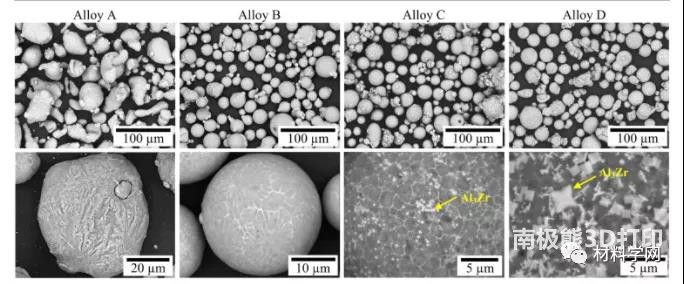
Figure 1 The morphology of the raw material powder, as seen by SEM. As indicated by the yellow arrow, Al 3 Zr particles can be detected in alloys C and D.
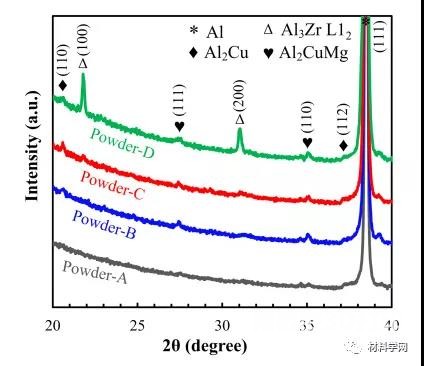
The X-ray diffraction pattern recorded in the range of 20-40 degrees 2θ in Figure 2 shows the phases present in the raw material powder.
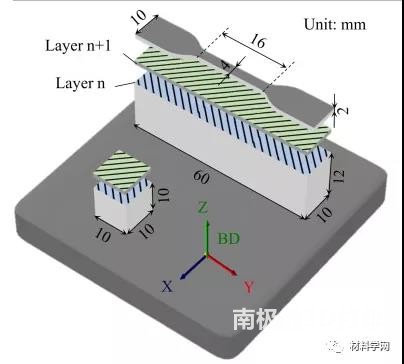
Figure 3 Schematic diagram of the sampling and scanning strategy in the L-PBF process, the coordinate system shows the construction direction. BD refers toarchitecturedirection.
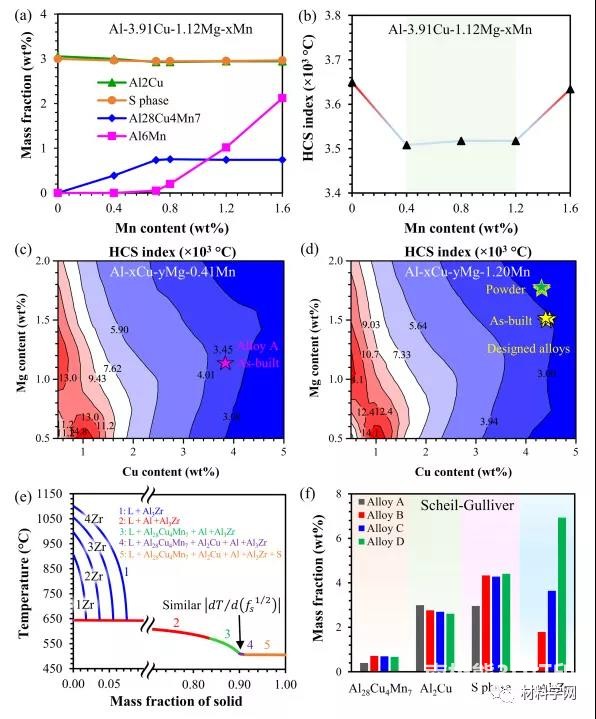
Figure 4 (a) Phase Fraction and (b) Hot Crack Sensitivity (HCS) Index, Kou based on Al-3.91Cu-1.12Mg-xMn alloy standardAs a function of Mn content. Comparison of HCS dT/dFsec12 has two Al-Cu-Mg-Mn quaternary alloy diagrams with fixed Mn content as a function of Cu and Mg content. (c) Al-xCu-yMg-0.41Mn, (d) Al-xCu-yMg-1.15Mn (wt%). (e) Phase transformation trajectories of Al-3.91Cu-1.12Mg-0.41Mn alloys with different Zr content. (f) The phase fractions of the four studied alloys solidified under Scheil-Gulliver conditions.
(Editor in charge: admin)
0 Comments for “Additive top issue: Laser powder smelting rapid solidification to prepare high-strength, crack-free aluminum alloy materials!”