March 25, 2022 French Industry3D printingMachine maker AddUp has announced that it has been developing a 3D device that can be printed in outer space, with plans to test it on the International Space Station (ISS) in 2023.as a European
aerospace
part of the “Metal3D” project of the Agency (ESA), which is dedicated to3D printingFor the metal parts project, AddUp designed the machine’s internal structure and operating system. Unlike conventional powder bed-based systems, this 3D printing device secures the filament stock on the frame, preventing the filament from floating and allowing the unit to operate in microgravity conditions.
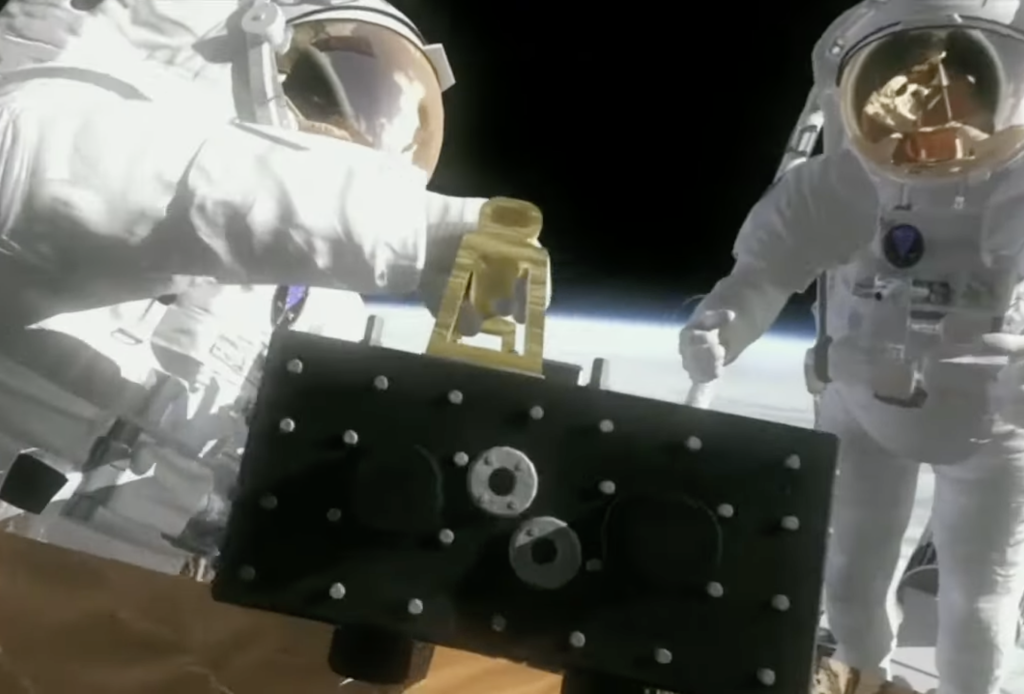
AddUp’s ground 3D printing equipment
For the past six years, AddU’s market focus has revolved around two industry-leadingMetal 3D PrintingTechnologies: Powder Bed Fusion (PBF) and Directed Energy Deposition (DED). In the case of the former, the company just launched its flagship FormUp 350 system last year, a machine designed for industrial needs such as safety, productivity and quality.
AddUp installed the FormUp 350 at Ohio State University, and since then, students and faculty have been able to research optimizing their 3D printing manufacturing methods.The company also recently released three new process monitoring
software
kits to enhance the functionality of the machine. Comprising AddUp Dashboards, Recoat Monitoring and Meltpool Monitoring, the kit is designed to increase user confidence in 3D printed prototyping and end-use part quality.
For their DED technology, in June 2018, AddUp acquired BeAM Machines and inherited most of their patented technology. Still sells the BeAM brand, the company’s Modulo 250 and Modulo 400
3D printerTechnology with slightly different functions, the former is for R&D applications, while the latter is that its “pro version” is an industrial-grade printer.
AddUp has huge ambitions, although they have nearly 40 DED and PBF machines installed at their bases in Strasbourg and Salon de Provence, France.And in the early years the company has developed a lot of
aviation
aerospace heat exchangers, etc., but ESA’s real goal is to make a space-ready3D printer.
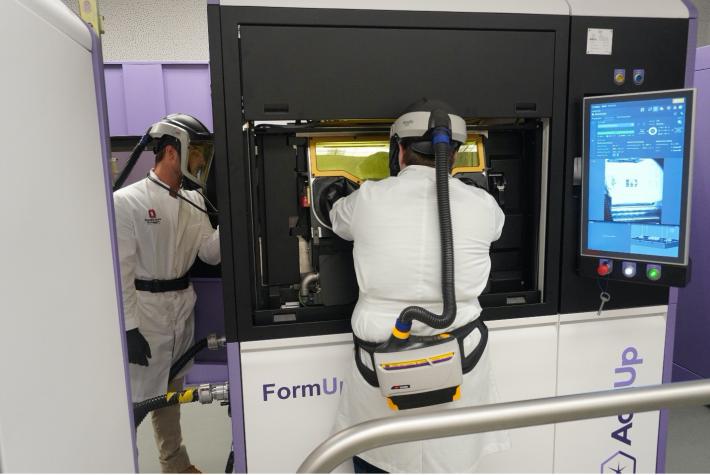
Try MicrogravityMetal 3D Printingmachine
ESA’s goal is to create the world’s first metal 3D printing system that can be used in space, and the Metal3D project will work with multiple partners to test the performance of parts produced in microgravity conditions.
To achieve this, ESA has commissioned them to build two identical prototypes, one built and tested with Airbus in Toulouse, and the other launched to the Columbus module on the International Space Station. The system is currently under development, and both prototypes share the same goal of operating both within Earth and in microgravity.
Also one of the key partners is a team from Cranfield University which oversees the unit’s
energy
and material delivery systems, as well as equipment enclosure design and Highftech fluid management.
AddUp developed not only some of the unit’s internal structure, but also its programmable logic controller (PLC), and the interfaces that allow it to communicate. According to AddUp R&D engineer Alexandre Piaget, the company also played a key role in the Metal3D project, which “lays the foundation for today’s machines”.
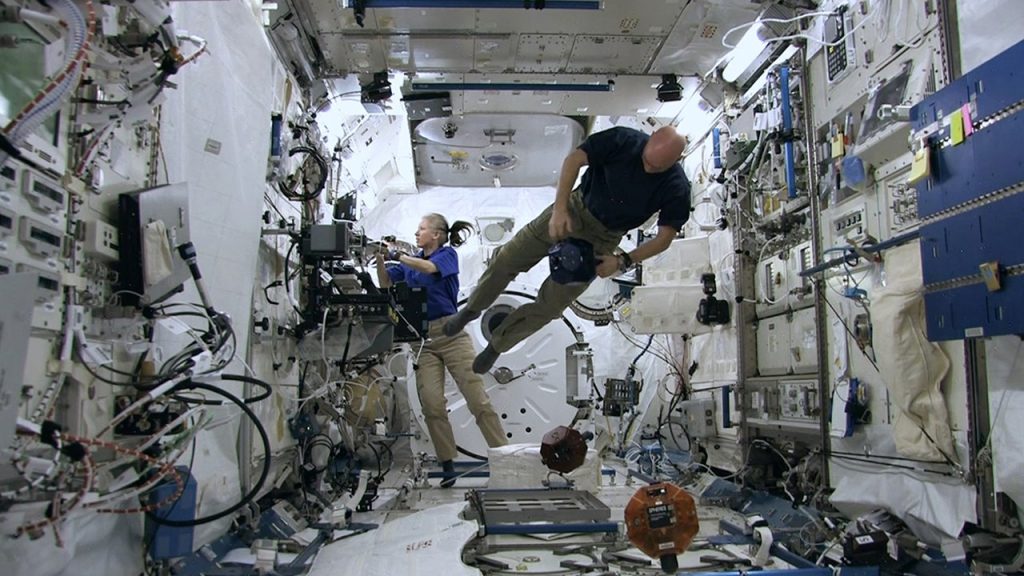
“AddUp has played an important role in fulfilling this mission,” Piaget said. “In the final version of the machine, AddUp will be responsible for the machine’s moving axes, structural parts and software.”
The machine is able to overcome a problem that conventional 3D printers are difficult to use in space, namely the risk posed by fine powder floating from the build area. The system is implemented using a wire laser combining (W-DED) process, which holds the alloy in place and then laser fuses it together while moving along 3 linear axes and 1 rotational axis.
At the same time, the 3D printer can operate under a nitrogen atmosphere as a means of limiting material oxidation and reducing the risk of burning. Additionally, given the low nitrogen supply on the ISS, the system is equipped with filtration and cooling to limit consumption and recover as much gas as possible.
While the machine isn’t expected to be launched into space until February 2023, AddUp revealed that it has worked with Airbus to develop a Metal3D-inspired machine that will “make this technology sustainable” .
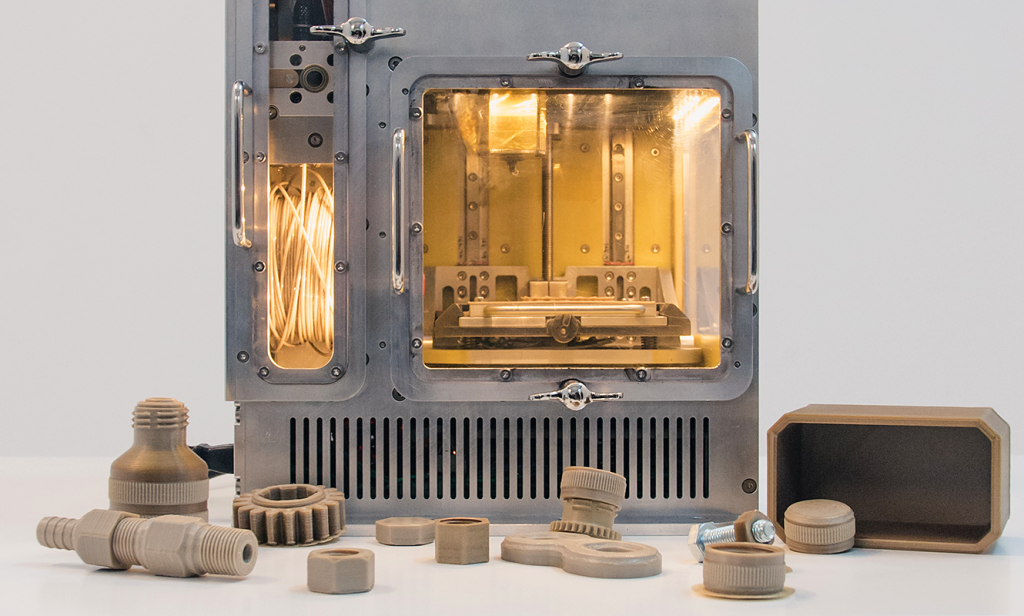
3D printing competition in microgravity
In recent years, the International Space Station has become a hotbed of 3D printing research, with both commercial and academic researchers trying to test emerging technologies in microgravity. As part of the “MELT project”, ESA, in collaboration with another partner, has also previously developed a polymer microgravity 3D printer, also designed for aerospace applications.
Elsewhere, a new zero-gravity 3D printer has been tested on a converted aircraft in a recent experiment by Iowa State University researchers. By constantly flying up and down at a 45-degree angle, the team was able to print briefly in microgravity.
(responsible editor: admin)
0 Comments for “ADDUP’s metal 3D printer will be tested in microgravity on the International Space Station in 2023”