Invisible
Glasses
Traditional preparation methods involve complex and time-consuming multiple steps and polishing processes.In recent years, various3D printingTechnology such as fused deposition3D printing(
FDM
), Ink Direct Writing (DIW) and UV-curable3D printing(SLA, DLP) has been applied to the preparation of various optical structures.In these methods, the use of resin droplets3D printingStrategies, including inkjet printing and UV curing in the droplet, have received widespread attention due to their ability to prepare 3D structures on demand and their operability. However, the traditional point-by-point or layer-by-layer additive manufacturing mode inevitably produces a step effect, which limits the accuracy of vertical printing and makes the printing structure anisotropic. Although the two-photon polymerization printing technology (TPP) can improve the surface smoothness, it is difficult to meet the needs of practical applications due to its low efficiency and complex equipment.Therefore, to reduce the step effect and achieve high accuracy for3D printingThe application of technology in optical structures is of great significance.
Aiming at the step effect in layer-by-layer printing, the researcher Song Yanlin’s team proposed a continuous liquid film limitation based on digital light processing (DLP) technology.3D printingStrategy to achieve the preparation of high-precision 3D structures. In the liquid-solid interface constraint and continuous printing mode, the liquid resin attached to the cured structure is sucked into the cured layer structure, and the excess resin attached to the cured structure is scraped off at the same time, eliminating the step effect and avoiding The post-cleaning step ensures the fidelity of printing. In addition, it also suppresses heat accumulation and thermal diffusion during continuous printing, ensuring printing stability. Based on this strategy, a centimeter-level contact lens structure with a center thickness of about 135 μm can be prepared.The structure has extremely high smoothness (roughness less than 1.3 nm), uniform mechanical properties, high
biology
Compatibility and excellent optical properties, its light transmittance and imaging resolution are as high as 96% and 228.1 lp/mm.
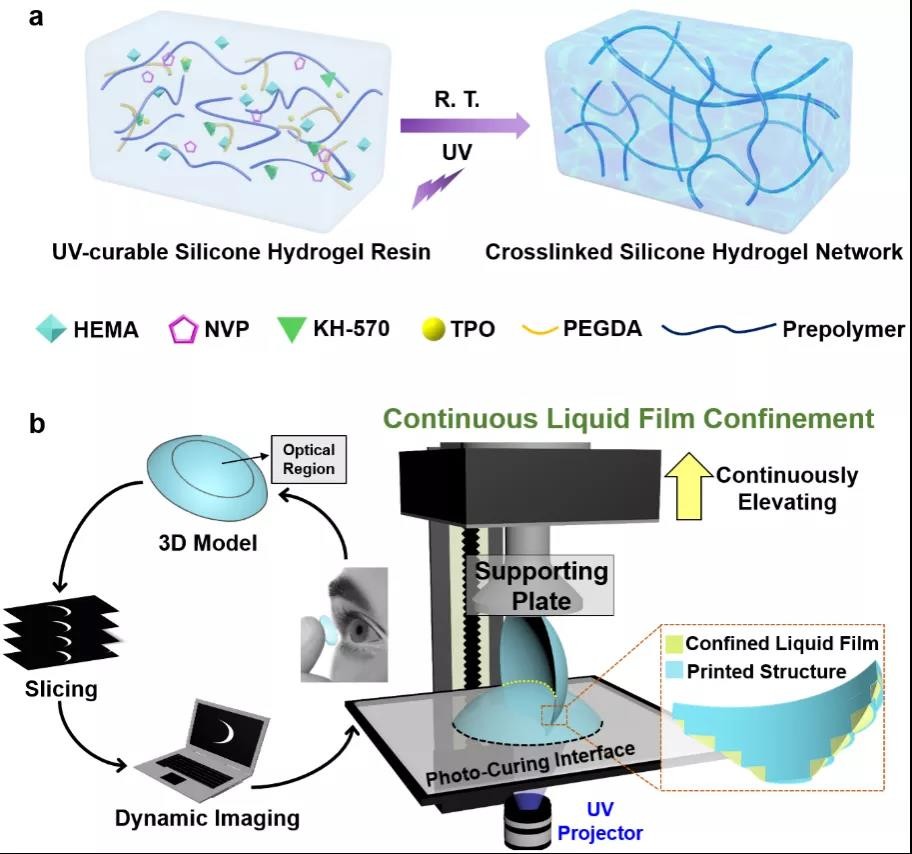
Silicon hydrogels are widely used in the preparation of contact lens structures due to their suitable water content and oxygen permeability. The team has developed a method that can be used for DLP
3D printingThe UV curable silicone hydrogel resin system is used in the preparation of contact lens structures (Figure 1a). In the continuous printing process, the cured structure is always restricted by the interface between the liquid resin and the cured structure, which makes the thin liquid resin film wrap around the cured structure. Through the control of the restricted liquid film, the gap between adjacent cured layers can be filled without excessive coating, the step effect can be eliminated, and a three-dimensional structure with smooth sidewalls can be obtained (Figure 1b).
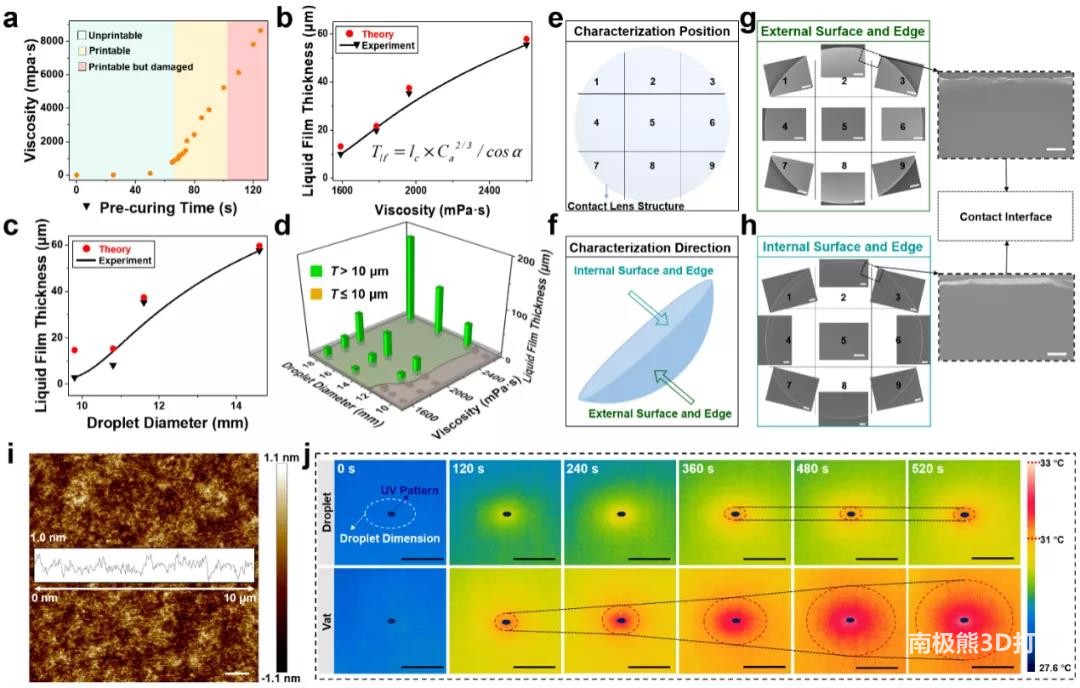
The elimination of the step effect is achieved by controlling the cover method (inhalation, filling and scraping) of the adhesive liquid film outside the solidified structure.due to3D printingThe wetting behavior and capillary phenomenon in the process, the liquid film covering the printing structure is ubiquitous, the team used these resins that are usually washed away as a transition layer to eliminate the step effect. As shown in Figure 2, in the continuous printing process, by synergistically adjusting the resin viscosity and droplet diameter, the size and morphology of the adhesive liquid film can be well controlled, so that the thickness of the liquid film can be controlled, thereby eliminating the step effect, While printing a 3D structure with smooth sidewalls, it also ensures high fidelity of the printing.In addition, the continuous liquid film limits the3D printingThe strategy also suppresses heat accumulation and thermal diffusion, ensuring the stability of long-term printing.
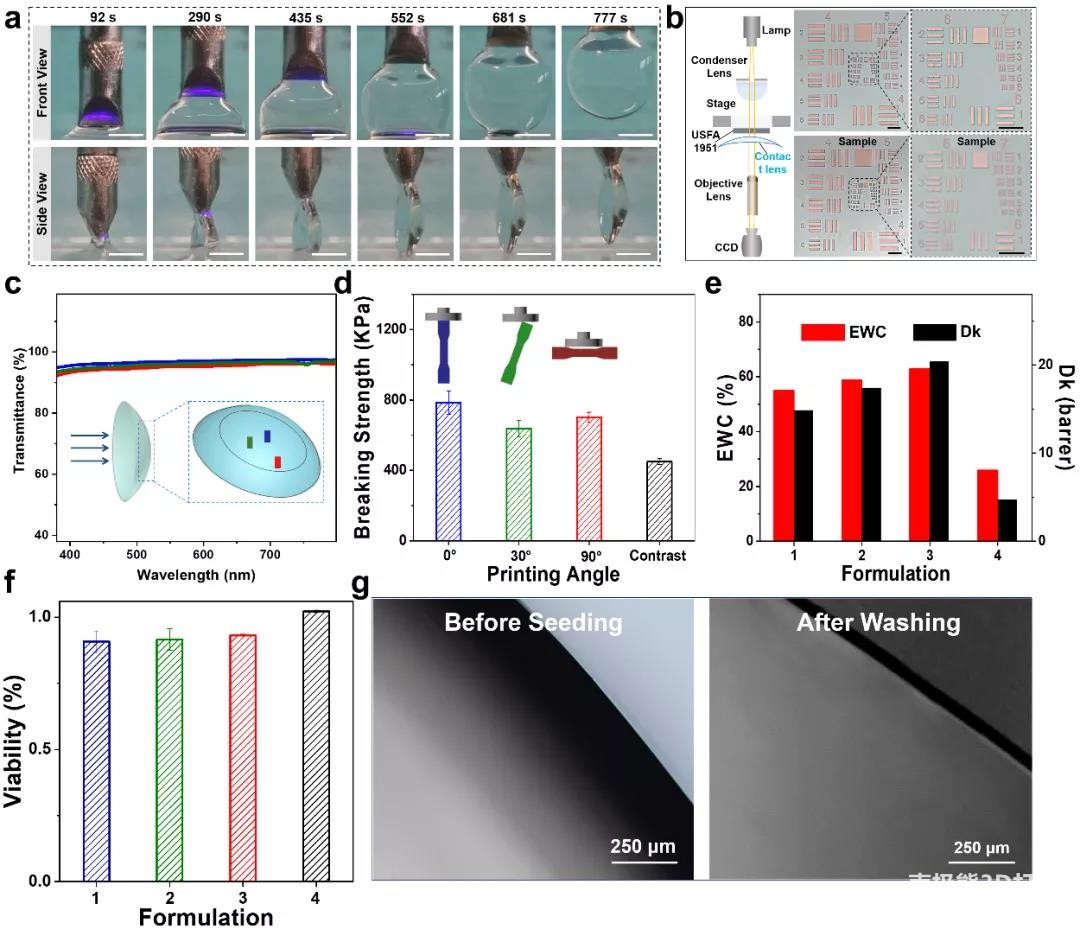
As shown in Figure 3a, with the continuous lifting of the support plate, a contact lens structure with smooth sidewalls can be obtained. The swollen contact lens structure has excellent optical properties, and its imaging resolution and light transmittance are as high as 228.1 lp/mm and 96% (Figure 3b-c). The mechanical properties of the dumbbell-shaped structure printed from different angles are characterized. It can be seen from Fig. 3d that the swollen dumbbell-shaped structure has isotropic mechanical properties without directional dependence, which further illustrates the elimination of the step effect. At the same time, the swollen contact lens has a suitable balance of water content and oxygen permeability (Figure 3e), and the swelling structure itself and the immersion solution are non-cytotoxic and have low cell adhesion characteristics (Figure 3f-g), indicating that it can Meet the biocompatibility requirements of practical applications.
The work was published on Advanced Materials (DOI: 10.1002/adma.202107249) under the title “Suppressing Step Effect of 3D Printing for Constructing Contact Lens”. The first author of the paper is Zhang Yu, a doctoral student at the Institute of Chemistry, Chinese Academy of Sciences, the corresponding author is Prof. Song Yanlin, and the co-corresponding author is associate researcher Wu Lei, Institute of Chemistry, Chinese Academy of Sciences. This work was supported by the Ministry of Science and Technology, the National Natural Science Foundation of China, the Youth Innovation Promotion Association of the Chinese Academy of Sciences, and the Beijing National Research Center for Molecular Sciences.
Paper link:
https://onlinelibrary.wiley.com/doi/10.1002/adma.202107249
(Editor in charge: admin)
0 Comments for ““Adv. Mater.” from the Institute of Chemistry, Chinese Academy of Sciences: Eliminate the step effect of 3D printing and prepare high-precision contact lens structures”