Smart soft actuators usuallyRelying on phase change materials, fluid drive, or electrostatic attraction to achieve a specific movement, which has the ability to imitate biological systems and has high efficiency. Among them, the dielectric elastomer actuators (DEAs) use the electrostatic force generated by applying a voltage on the insulating elastomer between the two electrodes as the driving force. The attractive force of the opposite charges reduces the thickness of the elastomer in the direction of the electric field, resulting in expansion and expansion in the orthogonal direction. This kind of external electric field can be quickly applied and removed by removing the voltage applied to the electrode. Therefore, DEAs exhibit a fast driving rate and a large energy density, which makes it a great place in the fields of soft robots, smart medical devices, etc. Application scenarios.
At present, most DEAs are manufactured by planar methods such as spin coating and sequential mechanical assembly. Therefore, the deformation expands in the plane during driving. By further processing these planar structures, micro-bending actuators, rolling actuators, etc. can be transformed into manufacturing. However, these devices often exhibit impaired cycling and breakdown phenomena and can achieve limited shapes. In contrast, direct ink writing (DIW) based on extrusion3D printingThe method can quickly design and manufacture soft materials in almost any geometric shapes and be used to print DEAs.
Recently published in Advanced Functional Materials magazine entitled 3D Printing of Interdigitated Dielectric Elastomer Actuators, the team of David R. Clarke and Jennifer A. Lewis from Harvard University developed and optimized a conductive elastomer with high print retention and suitable rheology. Ink and self-healing, plasticized dielectric matrix with adjustable mechanical properties.Team members use3D printingDifferent types of 3D DEAs devices are manufactured with vertical electrodes of specific shapes and packaged with self-healing dielectric substrates. The breakdown field strength is 25V·m-1 and the driving strain is as high as 9%.
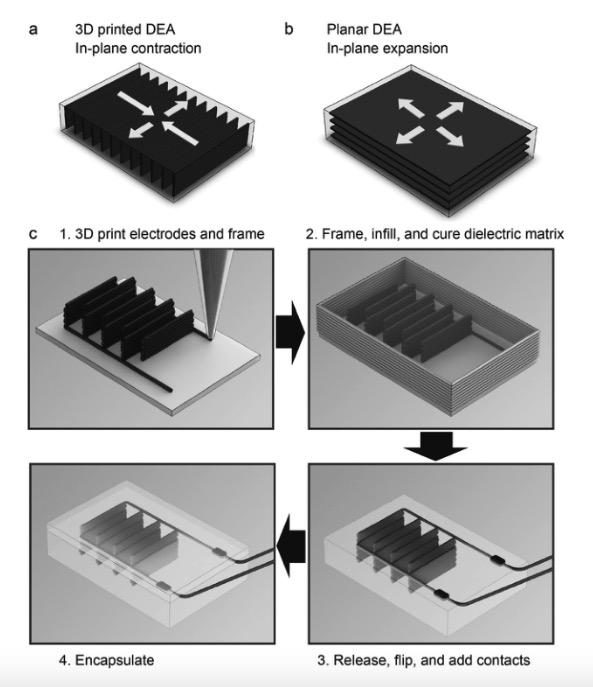
Researchers first prepared polyethylene glycol ethylene glycol sulfide (PEG-PES) oligomers terminated with vinyl ether groups, and then mixed them with dithiol chain extenders and trithiol crosslinkers. Production of chemically cross-linked elastomers. This strategy of simultaneous chain extension and crosslinking of low molecular weight oligomers separates their rheology in the uncured state from their final cured properties. The uncured viscosity is determined by the molecular weight of the oligomer, while the cured elastic modulus is determined by the molecular weight between crosslinks (Figure 2a). Finally, by adjusting the ratio of bifunctional chain extender and trifunctional crosslinker, PEG-PES elastomers exhibit excellent ultimate tensile properties, great elongation at break and low plastic deformation. In addition, the researchers used nano-carbon black as a conductive filler and as a rheology modifier to add the final conductive ink to the PEG-PES oligomer solution for basic printing. After printing, it was placed at 100°C for a few minutes to cure. The cured electrode has an EY of 0.49MPa (Figure 2d) and good cycle stability, with a conductivity of about 6.5 S m-1.
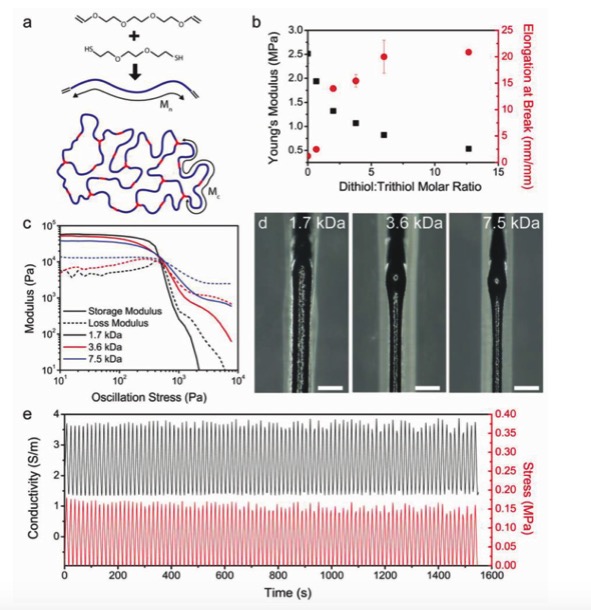
For the design of dielectric materials, the researchers used polyurethane diacrylate (PUA) oligomers as the matrix, which contained low molecular weight bifunctional crosslinking agent butanediol diacrylate (BDDA) and plasticizer phthalate diacrylate. Octyl ester (DOP Figure 3a), and encapsulate the printed electrode material in a dielectric matrix. DOP not only reduces the uncured viscosity of the dielectric matrix to facilitate its filling between the printed electrodes, but also reduces the mechanical loss tangent (tan δ) of the cured dielectric matrix (Figure 3b), which indirectly affects the frequency response of the actuator. In addition, DOP can also repair the dielectric matrix after electrical breakdown and is fault-tolerant. After the breakdown event occurs, DOP will diffuse from the surrounding area, allowing the device to return to its normal operating state (Figure 3c).
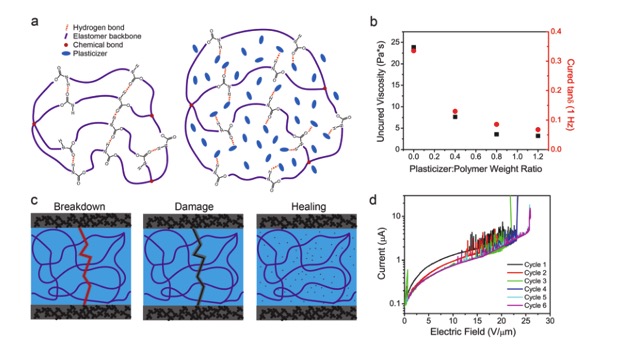
Finally, the researchers used the electrode materials and dielectric materials prepared above to print the crossed vertical electrodes and encapsulate the dielectric substrate using DIW direct writing, and measured the in-plane shrinkage by optical measurement methods. The ideal DEAs actuator should have a small elastic modulus and a large breakdown field strength (the maximum excitation strain (sz) is given by sz = ε0εr(EEB)2/EY, where EEB is the breakdown of the dielectric matrix Field strength.). And when printing large-size devices, the stability of the electrode material printing process is particularly important, and any local defects in the thinner dielectric segment will reduce the breakdown field strength.For the method3D printingWith the increase of the number of dielectric segments from 3 to 7 or even 15, the breakdown field strength remains at ≈25V·μm-1, while the excitation strain increases from 4.1% to 5.8% to 9.1%. (Figure 4d). Compared with the passive deformation of the electrode material, the increase in driving strain is caused by the increase in the area occupied by the active deformation of the dielectric matrix. Importantly, these devices showed consistent drive over 2000 cycles (Figure 4e, f). And if you use multi-nozzle DIW direct writing, you can print DEAs actuated devices at a faster speed (Figure 5a, b). These devices can be printed at a printing speed of 2.5mm s-1 within a few minutes, which is equivalent to the electrode manufacturing speed close to 1cm 3min-1. same,3D printingIn this way, printing electrodes at different positions on the plane produce specific deformations with characteristic in-plane electric fields in different directions, such as rotating actuators (Figure 5c, d).
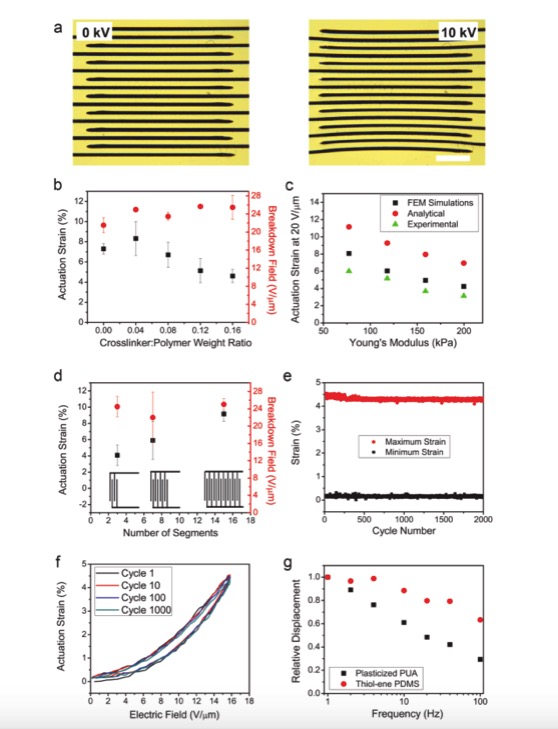
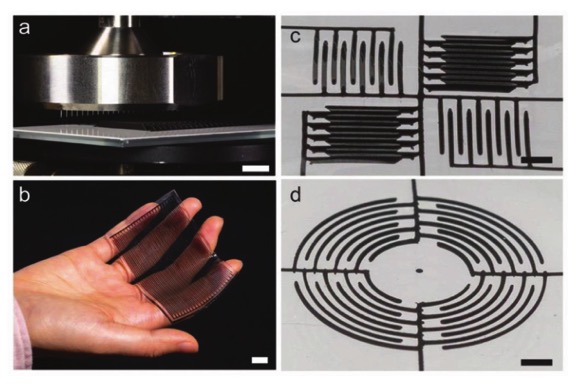
In general, take advantage of3D printingThe technology allows the use of arbitrary design geometries and high-fidelity full 3D electrodes to manufacture specific DEAs actuators, assisting in the optimization of electrode materials and dielectric matrix performance. 3D DEAs actuators may have stronger driving performance and in software Robotics and biomedical fields play a huge role.
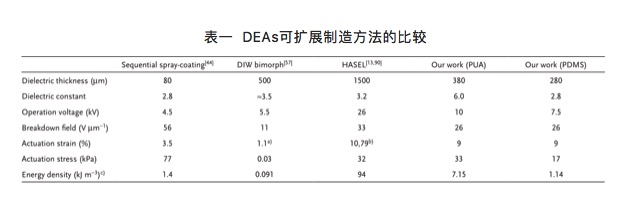
(Editor in charge: admin)
0 Comments for “AFM: 3D printed cross-type dielectric elastomer actuator”