Introduction: The use of laser powder bed fusion (LPBF) to print aluminum-lithium alloys has great potential for industrial applications. However, the high thermal cracking susceptibility (HCS) due to the addition of lithium remains a key factor restricting its rapid development towards such industrial applications. In this paper, the hot cracking behavior of 2195 Al-Li alloy fabricated by LPBF process was investigated by three-dimensional (3D) X-ray microtomography. The results showed large and interconnected cracks with a 3D mesh structure in the printed samples, extending layer by layer along the build direction from the layered cracks in the previous single track. The segregation between Al 6CuLi3 leads to the Al-Cu eutectic forming intergranular liquid film along the high angle grain boundaries. Furthermore, the interfacial layer (intradendritic liquid film) between 2 Cu and adjacent LiAlSi or AlCuMgAg was found to exhibit reduced microcrack resistance inside the grains. In addition, the high internal residual tensile stress provides the driving force for crack initiation and propagation.
Additive Manufacturing (AM) is a method to achieve three-dimensional (3D) near-net-shape forming of high-performance metal parts of complex shapes, advancing the3D printingthe next industrial revolution. In contrast to traditional subtractive manufacturing, additive manufacturing employs a step-by-step material processing strategy. It allows converting model slices from complex 3D designs to simple 2D geometry. Laser powder bed fusion (LPBF) is a typical powder-based additive manufacturing method. Al-Li alloys are more popular than traditional 2xxx or 7xxx series aluminum alloys because of their low density, high elastic modulus, high strength-to-weight ratio, high damage tolerance and corrosion resistance. In addition, Cu and Mg can be introduced to form Al-Cu-Li alloys, which can help to optimize the precipitation sequence, or by combining with Li to generate strengthening phases such as T 1 (Al 2 CuLi) and T 2 (Al 6 CuLi 3 ) , or by changing the solubility. However, the addition of Li and Cu also significantly increased the hot cracking susceptibility (HCS) of Al-Li alloys.
The main obstacle to achieving this goal may be the complex non-equilibrium solidification process of Al-Li alloys during LPBF. In this work it was shown that the final precipitation order of the Al-Li alloy directly affects the hot cracking behavior and mechanical properties of the printed samples. However, there are few studies on LPBF machining of Al-Li alloys. Optimizing laser processing performance by adjusting process parameters is an important step in the fabrication of crack-free Al-Li components.
Generally speaking, the contribution of thermal cracking mainly comes from two sources: liquid film and stress concentration. A stable liquid film is an essential prerequisite, and stress concentration is the trigger that initiates cracks and propagates them, ultimately leading to catastrophic failure. Perhaps one of the most important factors to consider is the change in the dynamic precipitation order due to the addition of lithium, which directly affects the distribution and stability of the liquid film. Therefore, establishing the relationship between microstructure evolution, liquid film stability and residual stress distribution is the key to reveal the hot cracking mechanism. in the LPBF process of Al-Li alloys. Therefore, the DC temperature tbr for the repulsive boundary depends on the misorientation angle θ as shown in Fig. 12a, where the reference value tb is defined as 759 K for the 2195 Al-Li alloy. The minimum DC temperature tb, min r and maximum DC subcooling Δtb, the maximum calculated as 562 K and 197 K, respectively.
Zhenglong Lei of Harbin Institute of Technology combines experiments and theoretical calculations to elucidate the hot cracking mechanism of LPBF-treated 2195 Al-Li alloy. The dynamic thermal crack evolution process of crack initiation, propagation and stopping is comprehensively discussed, which is of great significance for guiding process optimization. Intergranular cracks with a 3D network structure were captured in the printed Al-Li samples. The network crack is propagated layer by layer from a single layered crack. The Al-Cu eutectic produced by the segregation contributes to the formation of the intercrystalline liquid film. The thermal cracking susceptibility between grains is higher than that within grains. The tearing of liquid film under the action of stress concentration is the main reason for crack initiation. Related research results are titled “”
Link:
https://www.sciencedirect.com/sc…i/S221486042200166X
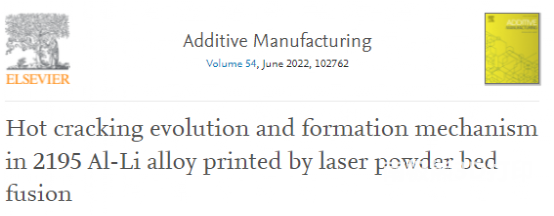
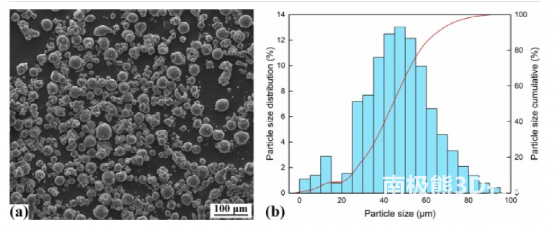
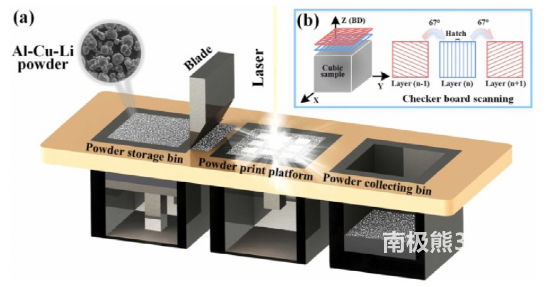
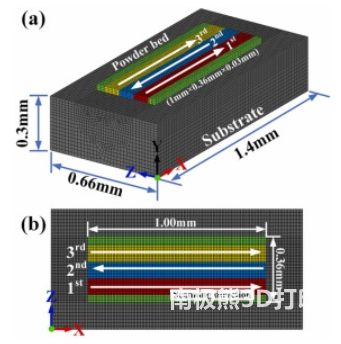
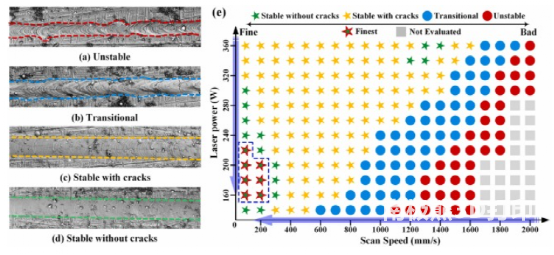
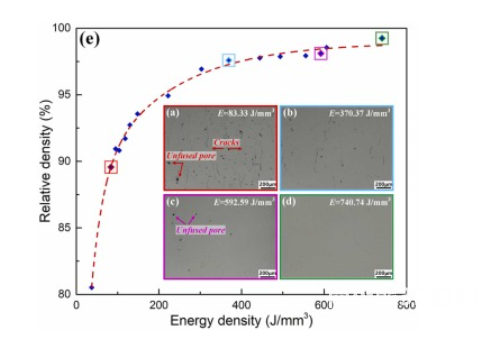
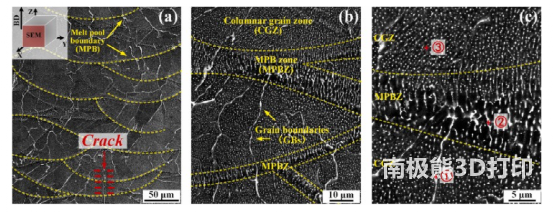
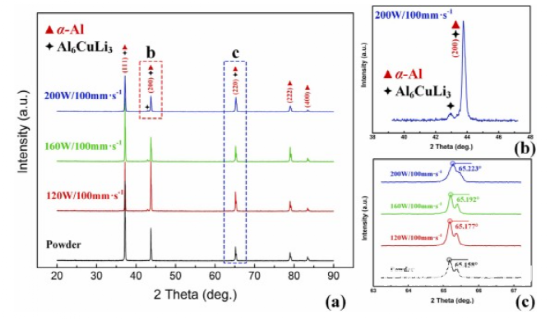
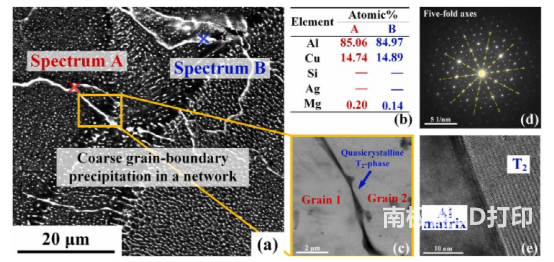
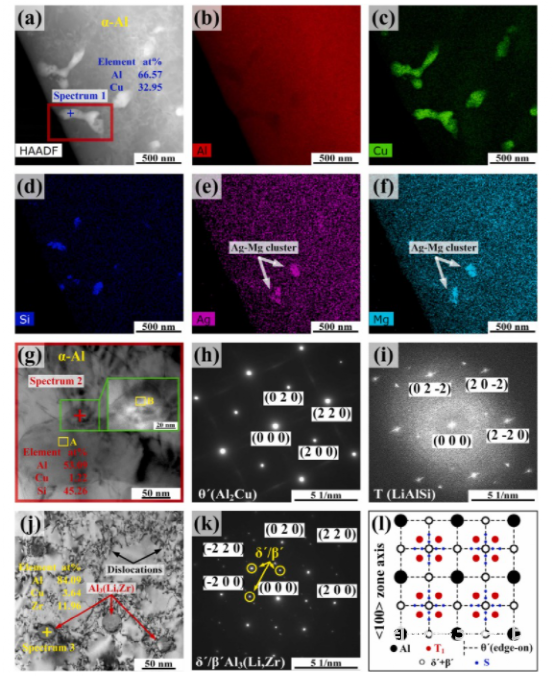

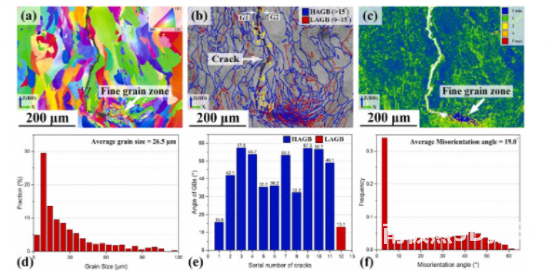
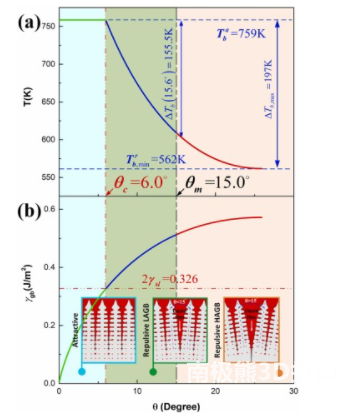
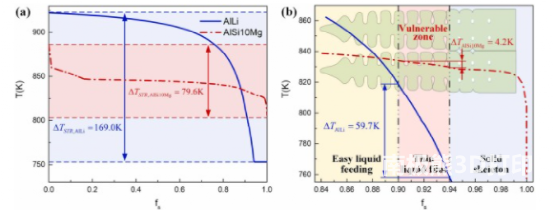
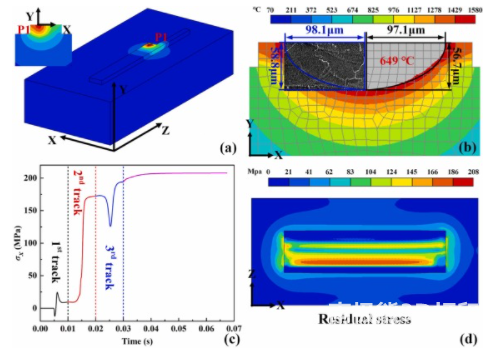
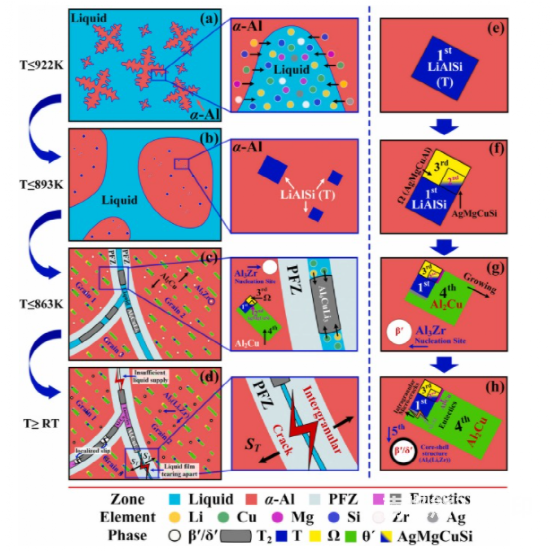
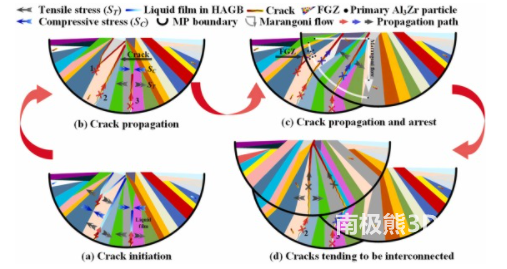
in conclusion
(1) Due to the layer-by-layer processing strategy, large interconnected cracks with a 3D network structure are encountered in the printed Al-Li alloy samples, which extend along the build direction from the previous layered cracks in the single track. The interconnected precipitates are dissolved out through intergranular cracks, resulting in more complex and regular crack paths, and significantly lower crack propagation resistance compared to the inside of the grains.
(2) LPBF-treated Al-Li alloys exhibit strong HCS, especially in HAGB, which is attributed to the existence of a stable liquid film and certain stress concentrations. The interfacial segregation between the T2 phase and the α-Al matrix promotes the formation of Al-Cu eutectic along the GBs (intercrystalline liquid film). The interfacial layer between the θ′ phase and the adjacent T phase or Ω phase (intradendritic liquid film) may have defects inside the grains.
(3) The (15.6°) (155.5 K) of the coalesced undercooled Δt bHAGBs is much larger than the temperature range of the vulnerable region (59.7 K), which indicates that the liquid film stability in the intergranular region and the HCS is higher.
(4) The calculated residual tensile stress of 208.0 MPa indicates a high level of internal residual stress within the printed sample, which constitutes the driving force for crack initiation and propagation.
(5) Crack-free samples are obtained by preheating the substrate and reducing the scanning speed, which is beneficial to reduce the temperature gradient, prolong the life of the molten pool, and prevent thermal cracks.
(responsible editor: admin)
0 Comments for ““AM”, the top journal of additive manufacturing of Harbin Institute of Technology: Research on the hot cracking behavior of aluminum-lithium alloys manufactured by laser powder additive manufacturing!”