The additive manufacturing industry continues to maintain a rapid growth trend due to recent technological advancements in materials and production processes. In fact, some studies show that3D printingIt is being widely accepted and integrated in various application fields.We also see that many companies are betting on developing new and innovativepost-processingTechnology, this phase of work is becoming more and more important. One of the representative companies is the additive manufacturing technology company (AMT), which was established in 2017 and specializes in3D printingAftertreatment system for components.itsThe main goal is to drive the adoption of this technology, not only to improve application performance, but also to scale up industrial production.
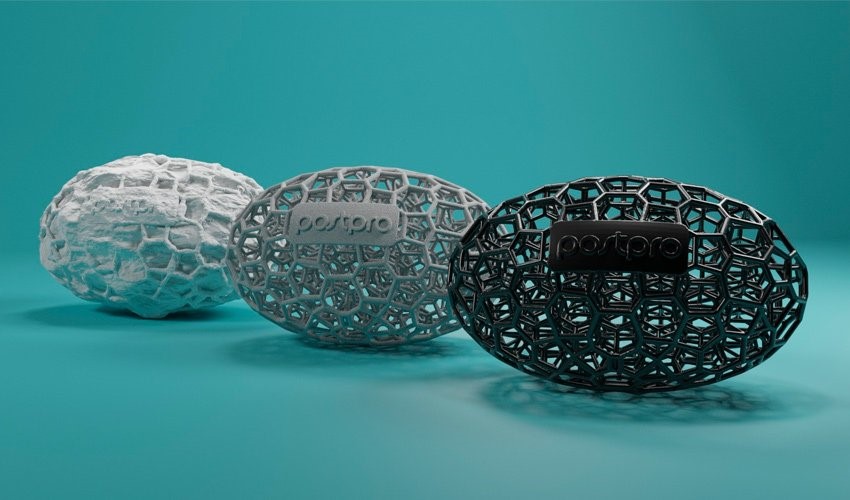
To learn more about their patented technology and their vision for the state of the additive manufacturing industry, 3DN interviewed their founder and CEO, Joseph Crabtree, and Antarctic Bear has compiled some of that to share.
3DN: Can you introduce yourself and tell us how you got the idea to create AMT?
My name is Joseph Crabtree and I am the CEO and founder of AMT.I’m a materials scientist by profession, and interestingly, this seems to be quite a few now3D printing companyProfessionalism of the CEO. Before AMT, I was in traditional manufacturing, including injection molding, CNC machining, forging, etc. When I started AMT in 2017, I came with the perspective of understanding traditional manufacturing and how to apply that knowledge to 3D printing. We see a great opportunity and I wonder how we can turn 3D printing into a viable manufacturing technology. I started to dig a little deeper and found that most companies focus on the printers themselves. Materials are starting to have more options, and that’s the focus of the industry. Then, there is the recurring theme that nothing after the printing process is discussed or addressed. It seemed like an obvious opportunity for me and our team to start a company and try to provide a solution.
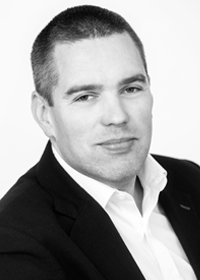
△Joseph Crabtree, CEO and Founder of AMT
3DN: Which 3D printing methods and materials are compatible with your solution?
We generally focus on thermoplastic polymers, especially plastics designed for powder bed processes, which are indeed the mainstream technology in industrialization today. Those planning to industrialize with additive manufacturing are also looking to powder bed fusion and thermoplastic polymers. Right now, polymers are our core focus, but I would add that we also have intellectual property patents around metals and thermoset polymers. Maybe there will be some expansion to these additional opportunities soon, and further, we intend to be able to post-process every type of 3D printed part.
3DN: What kind of users is your gas phase smoothing post-processing technology targeting? How effective is deburring?
We work with companies in different industries, geographies and sizes: from small service bureaus to large multinational corporations, with a wide range of clients, our technology portfolio can meet any form of requirement.
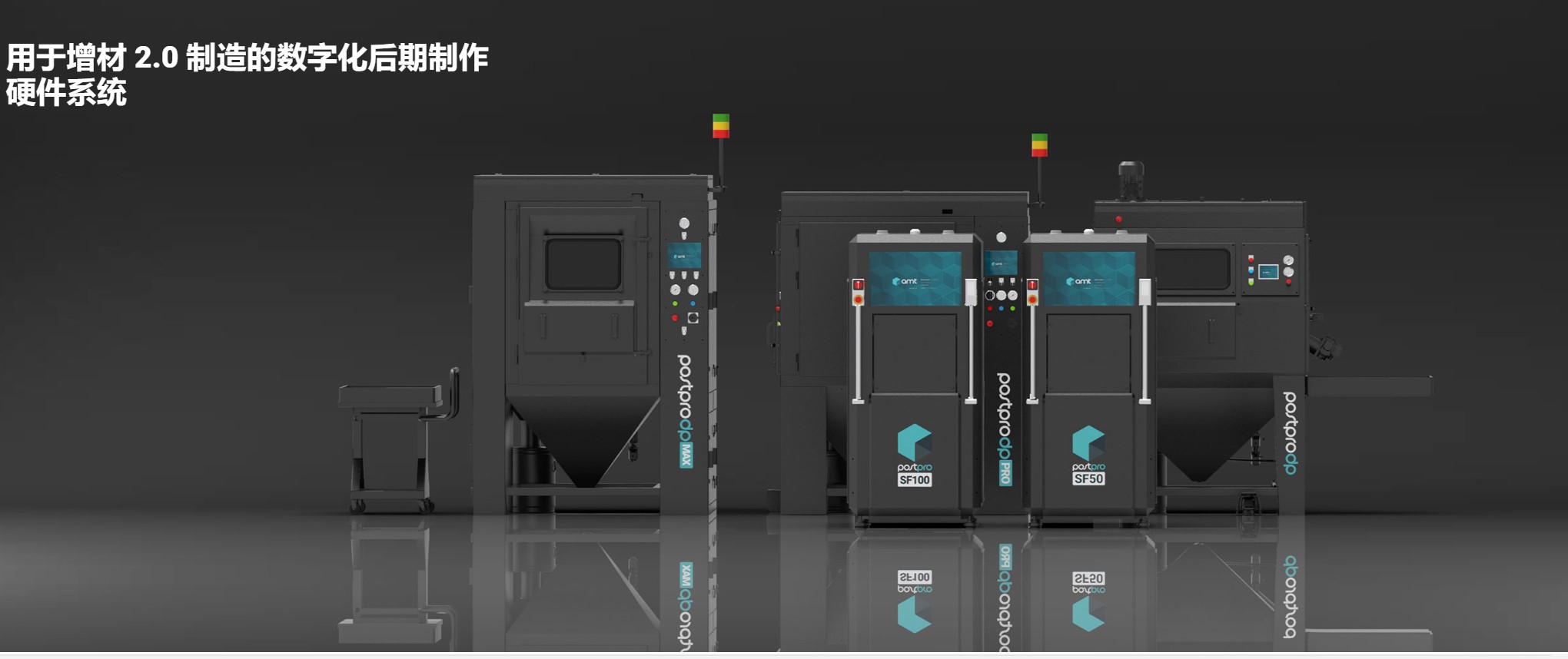
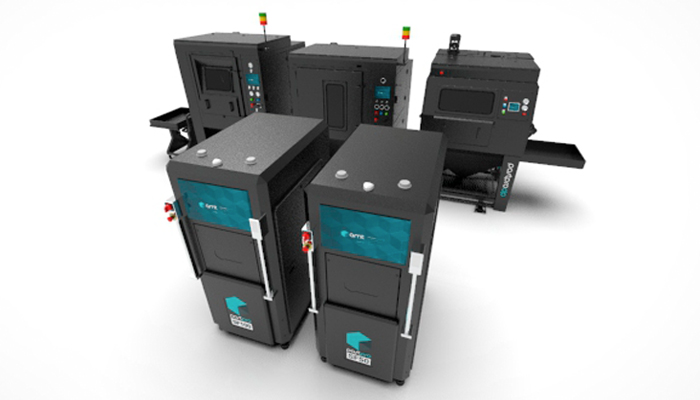
For powder removal or cleaning, this is an insurmountable hurdle. Everyone needs to clean their parts, which is a prerequisite for our core process,That is, the chemical vapor smoothing process – “surface treatment of PostPro SF”. Through chemical vapor smoothing, we can transform a part from a pristine printed part to one that looks, feels and performs like injection-molded or traditionally manufactured parts.As a result of the success of this technology, we realized that even before smoothing, cleaning was required, but there is no real solution yet. That’s why we have developed our own cleaning solutions. That said, we expect our future focus will be on high-volume additive manufacturing.
3DN: We are seeing a clear trend towards AM automation. How is AMT working to address this issue in its process?
From day one, we have believed that the only way for 3D printing and additive manufacturing to become commercially viable is to remove all manual labor, remove all manual steps. This doesn’t just mean post-processing, it means a combination of materials, printers and post-processing. to this end,We created our Digital Manufacturing System (DMS), what we call an end-to-end workflow. Although we sell individual modules of our technology, the real goal is to fully automate the end-to-end workflow,We have achieved this vision. Today, companies in the United States, Europe and Asia are already using these technologies. Again, if you look at traditional manufacturing, automating a complete end-to-end workflow is not new or innovative. Take injection molding, forging or CNC machining, they are all fully automated at scale, and 3D printing is now catching up.
3DN: What challenges do you see in the post-processing of 3D printing?
One of the biggest challenges remains education. Five years ago, when we started, nobody knew about post-processing, it was an afterthought. But now, it’s become a topic of debate, and it’s in people’s consciousness, which is great. While there are still some people going into 3D printing thinking that it’s simply adding materials to a printer, that’s clearly not true. Therefore, education definitely has a role to play in helping the market and the general public learn more about additive manufacturing.
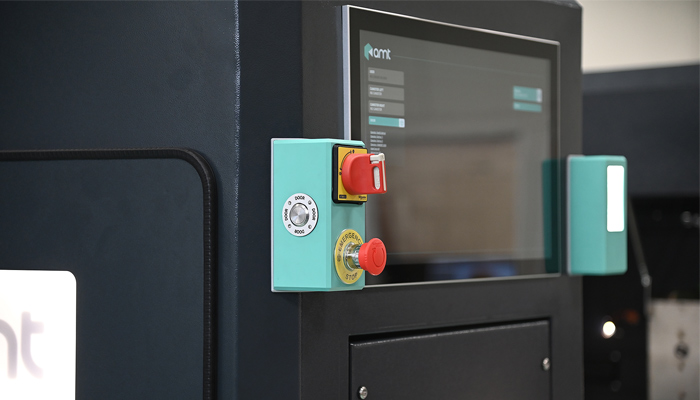
For what we’re trying to do, put physical machines,software, materials or processes into a seamless system is a challenge. In any other industry, it’s rare to buy five different products from different companies before trying to bring them together.Beyond that, we need all the specifications to actually drive the right application of the technology, including in specific end markets such asaviationaerospace,medicalWait. Because in these areas, there is already a lot of information about printing and material verification. But when it comes to post-processing, it’s just a black hole.For these reasons, we partnered with the American Society for Testing and Materials (ASTM) to help developstandardso that we can develop clear specifications for these processes as well.
3DN: Can you tell us about AMT’s upcoming projects/releases?
As I mentioned earlier, we’ve been working on the concept of this end-to-end automated system, our digital manufacturing system, since day one, but there are two big projects we’ll be working on this year. The first was with a company in the US called Custom Color, who developed a new consumer product that makes custom figurines in high volumes. We will develop and install end-to-end process lines.We are talking about dozens of industrialHPprinters, and we’re automating the entire workflow, from the printer’s point of view until the parts are packaged and ready to be shipped to the customer. We are gradually making these production lines a reality, not just a fantasy.
And then, we also have a big ongoing project that is related tocarindustry is closely related. A complete end-to-end system, including all unpacking and cleaning of parts, including deburring, chemical vapor smoothing, coloring, parts, sorting and inspection, is provided by AMT, which will be delivered to us again later this year car customers. Incredibly, in 2022, we will be exhibiting a fully automated end-to-end workflow, from on-site printing, through part machining, to collecting the final part, the culmination of six years of R&D.
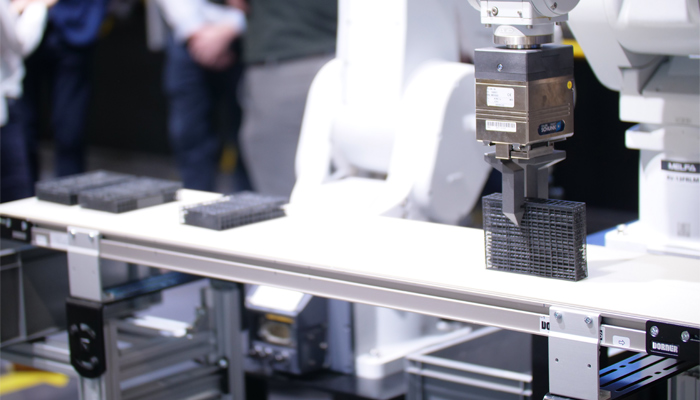
3DN: Is there anything else to say to our readers?
I really think,Over the next three years, the focus of 3D printing has to be on manufacturing, and we’ve been through various hype cycles. I think if we can get to the point where 3D printing is no longer a novelty, then we’ve succeeded.If we can get 3D printing to a level where it can be incorporated into the same types of factories as other manufacturing techniques, then we’ve really done our job.
(responsible editor: admin)
0 Comments for “AMT on current trends and challenges in 3D printing post-processing: making 3D printing more than just “hype””