The medical equipment itself has strict and precise attributes. Therefore, more sophisticated technical requirements have been correspondingly put forward for the production of medical equipment parts. In the production process of medical parts, the surface quality, precision and hygiene requirements of injection molded products ranging from hyperbaric oxygen chambers to hearing aids, anesthesia laryngoscopy, and medical buttons cannot tolerate any flaws.
If there is a demand, there must be a change. The yield rate of injection molded products is mainly related to the injection molding machine, mold, raw materials, and the temperature control system used. So how to improve the quality of medical and other high-precision products through the improvement of the source, the mold, while accelerating the production speed, has also become the focus of our many medical device mold manufacturers.
ESU Yisu will take the medical laryngoscope as an example to discuss together3D printingSpecific advantages and analysis in advanced projects such as the medical field. Medical disposable anesthesia laryngoscopy is more complicated and the most typical among many medical injection products. As shown in Figure 1.
1. The product structure is complex and the top space is small.
2. The tip of the top is in contact with the skin in the body, and the material hygiene requirements are strict.
Third, the size and quality requirements are strict, and surface defects are not allowed.
4. Injection laryngoscopes are generally disposable products, with large quantities and price costs within control.

Therefore, for mold manufacturers, how to balance the quality, efficiency, and hygiene of the laryngoscope mold has become the key.
As we all know, as far as the mold is concerned, the water system is one of the important factors of the mold product quality. The superior water system can shorten the product molding cycle and improve the product yield. But at present, the waterway is basically manufactured by machining processes such as milling machines, and it is impossible to process the curved waterway, and the waterway cannot cover the mold cavity.
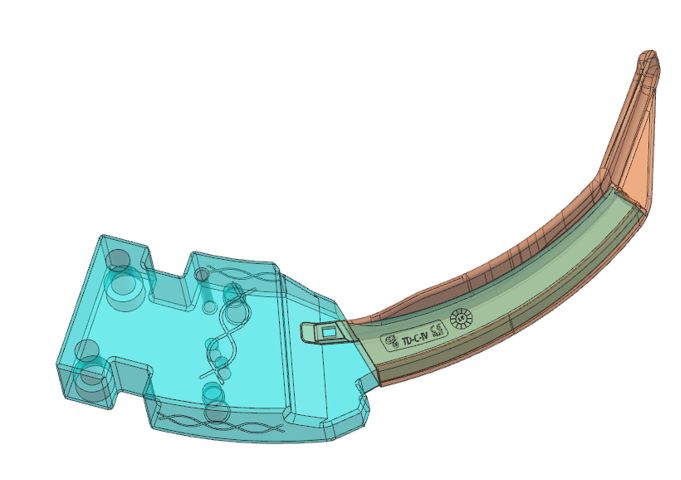
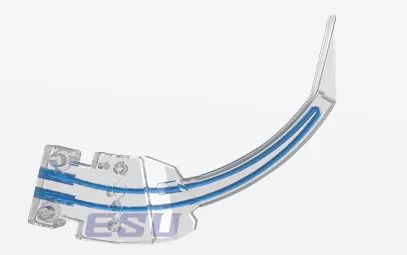
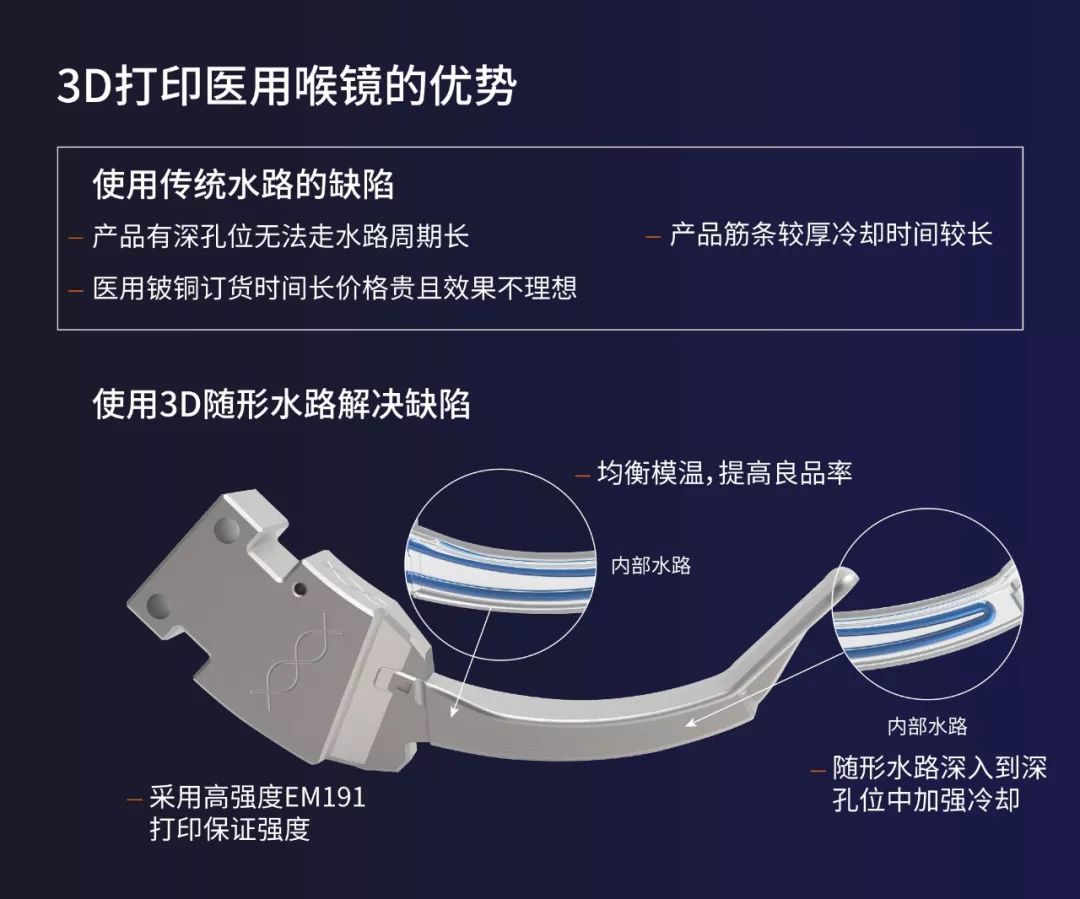
As shown in Figure 4, in view of the difficulties faced by common solutions, the conformal waterways designed by additive manufacturing technology can be solved one by one.
1. Molding cycle
Compared to traditional waterways,3D printingA waterway system covering the mold cavity can be designed to speed up cooling, shorten the molding cycle of the workpiece, and improve production efficiency.
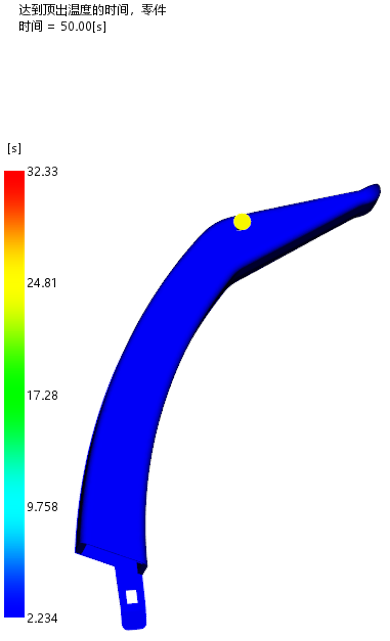
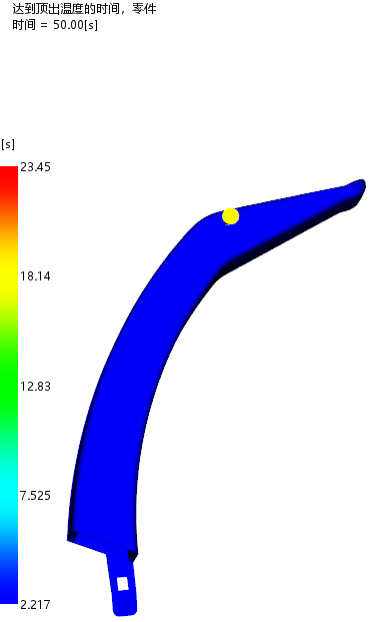
As shown in the figure above: the cooling time of the traditional waterway mold is about 32S, and the cooling time of the conformal waterway solution: 23S,3D printingCompared with the original solution, the time to reach the ejection temperature is 23% faster
2. Surface quality
The molding quality of injection products has a huge relationship with the mold temperature. The mold temperature is not balanced, and the maximum temperature and the minimum temperature are quite different. The high temperature is prone to defects such as burns and deformation, and the product yield is low.3D printingThe conformal water channel is evenly distributed throughout the cavity of the mold to reduce the temperature difference, balance the mold temperature, and improve the product yield.
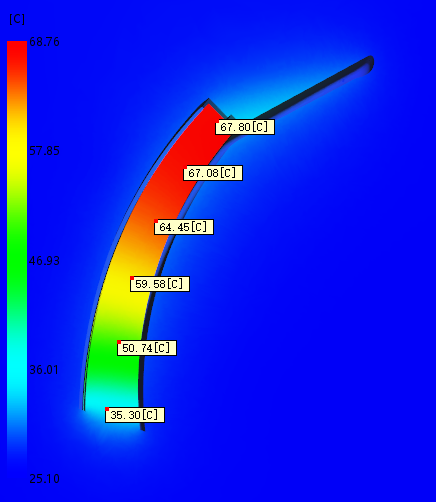
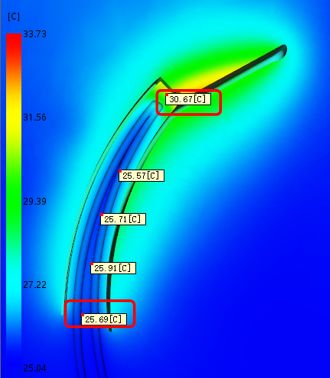
Also in the mold3D printingIn terms of materials, the EM191 metal powder material independently developed by ESU is selected. EM191 is a powder in the powder system independently developed by ESU Yisu, which has the functions of anti-rust, anti-corrosion, wear-resistant and durable, so as to ensure the service life of the printed parts.There are also EM181, EM201 and other molds in the powder system independently developed by ESU.3D printingSpecial metal powder materials, select materials for printing according to different needs.
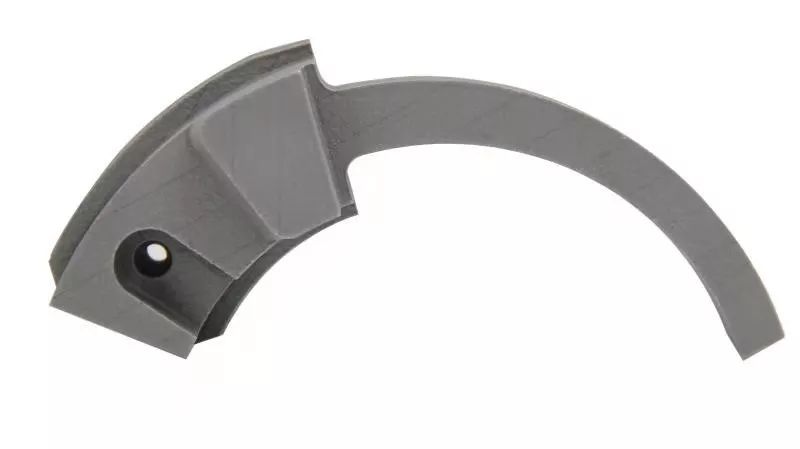
With the development and improvement of technology,3D printingIt will be applied to more and more fields, and mold manufacturing must use new technology to make up for its own shortcomings and limitations. ESU Yisu has always been adhering to the mission of opening a new era of mold manufacturing, and strives to inject fresh blood into traditional molds and revitalize traditional manufacturing.
(Editor in charge: admin)
0 Comments for “Application of 3D printing on medical laryngoscope mold”