OEM Meltio’s leading product portfolio includes its Meltio M450 small-scale industrial metal3D printingThe machine and Meltio engine are designed to seamlessly integrate with CNC machine tools, robotic arms and gantry systems to provide customers with affordable and available hybrid manufacturing capabilities.
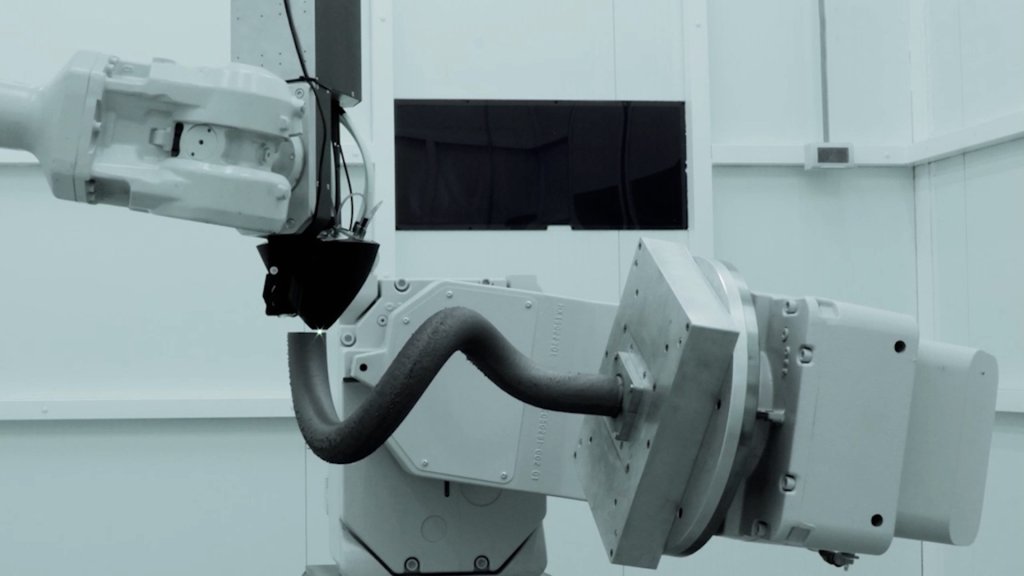
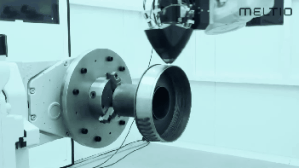
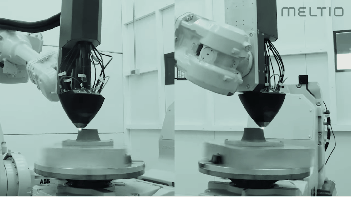
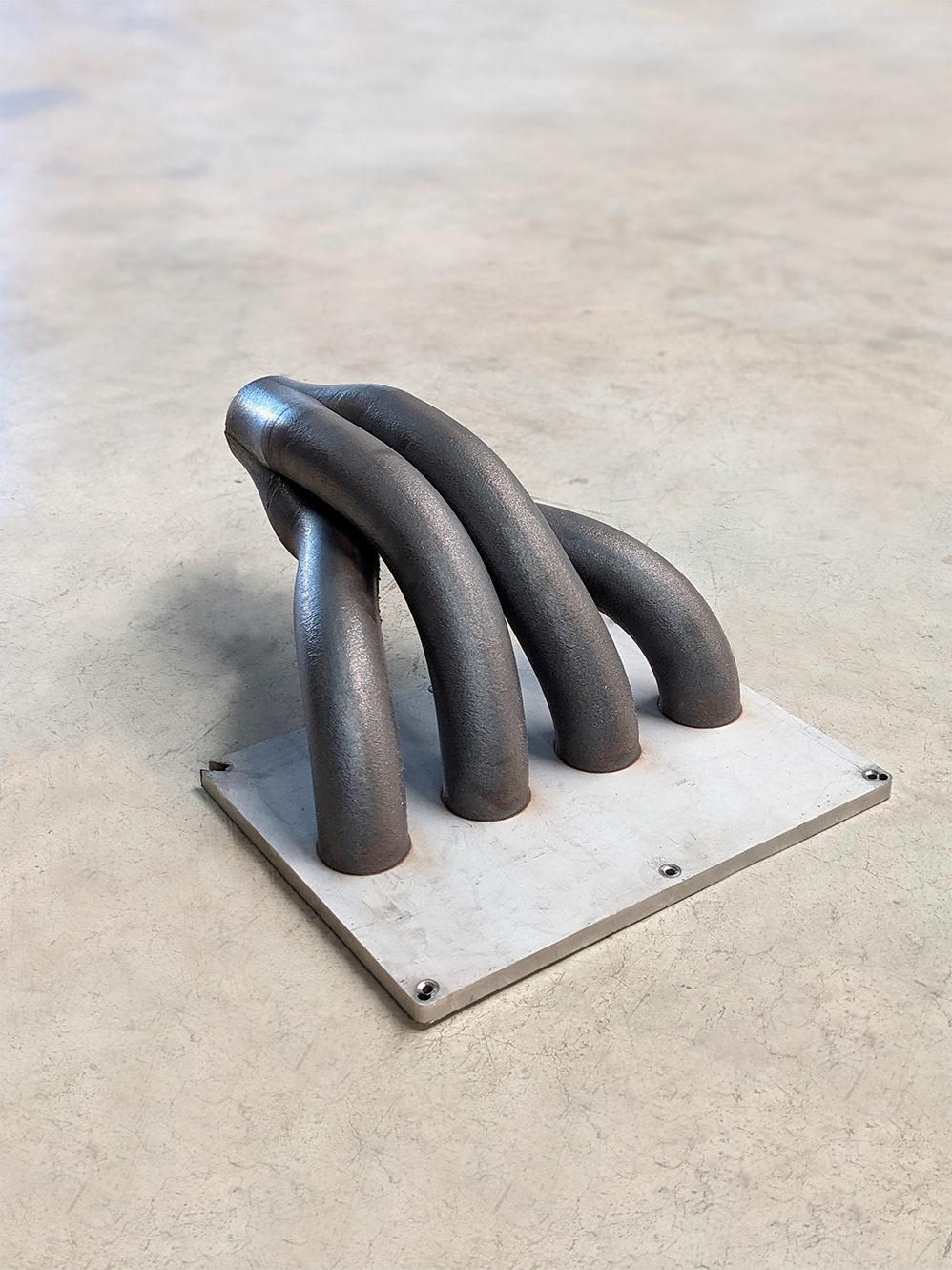
Matthews said: “In the field of metal printing, silk is almost the cheapest printing material. Conventional PBF systems have very high requirements on the quality of the powder. They must have very small particle sizes, and the particles must be spherical. This means a lot. The powder is rejected because it is not spherical, which increases the cost. For example, the cost of goods of 3 or 4 US dollars per kilogram eventually becomes 50 to 100 US dollars per kilogram, while the cost of using wire only increases a little, for example, per kilogram. 5 or 6 dollars per kilogram.”
The framework of Meltio Engine is only limited by the motion system. It can be easily integrated in any workshop and is driven by Meltio’s LMD technology. Since no special equipment is required, users who choose raw silk materials can benefit from cleanliness.
Meltio Engine robot integration turns the robot arm intoMetal 3D printingSystem, there is no inherent size limit, because the working range is only limited by the size of the motion system. The robot integration system is ideal for large-scale and complex 3D printing, repair, cladding and function addition, and can be integrated with any robot arm manufacturer and interface on the market.
Nieto said: “We have an open platform, which means that the motion system, in this case, the robot, is something that customers can choose. This means that they have more geometric freedom and Greater work volume. Customers can add value to their business by bringing more applications.”
Robot integration system provides
FDM
Similar user experience, but for metal printing, the material can easily provide feedback parameters to the user through the sensor. Some other key advantages of using dual external axis positioners are the ability to print vertically, provide the best surface quality for the part, and provide multiple solutions for the same part.
The system prides itself on its reliability, allowing mass production and manufacturing of multiple prints of the same quality. There are also some upgrades to the robot integration system, including a programmable power supply that can preheat the material to increase the deposition rate, and a dual-line option that can simultaneously perform 3D printing of dual-line materials through rapid line change.
With its Meltio engine robot integration, OEMMeltio has been able to achieve a variety of novel applications, show stronger mechanical performance, or can be manufactured more efficiently in terms of time, cost and material usage. For example, they can 3D print a plate that is usually found in the turbine industry. As a demonstration application, it is usually very expensive to manufacture by traditional methods.
Nieto explained: “In fact, our company is able to produce blades at a much lower cost than the traditional blades ground from metal blocks. We really want to show that it is possible to manufacture with our technology and it is very cheap. This method of manufacturing is interesting because it can produce hollow, lightweight parts compared to milling.”
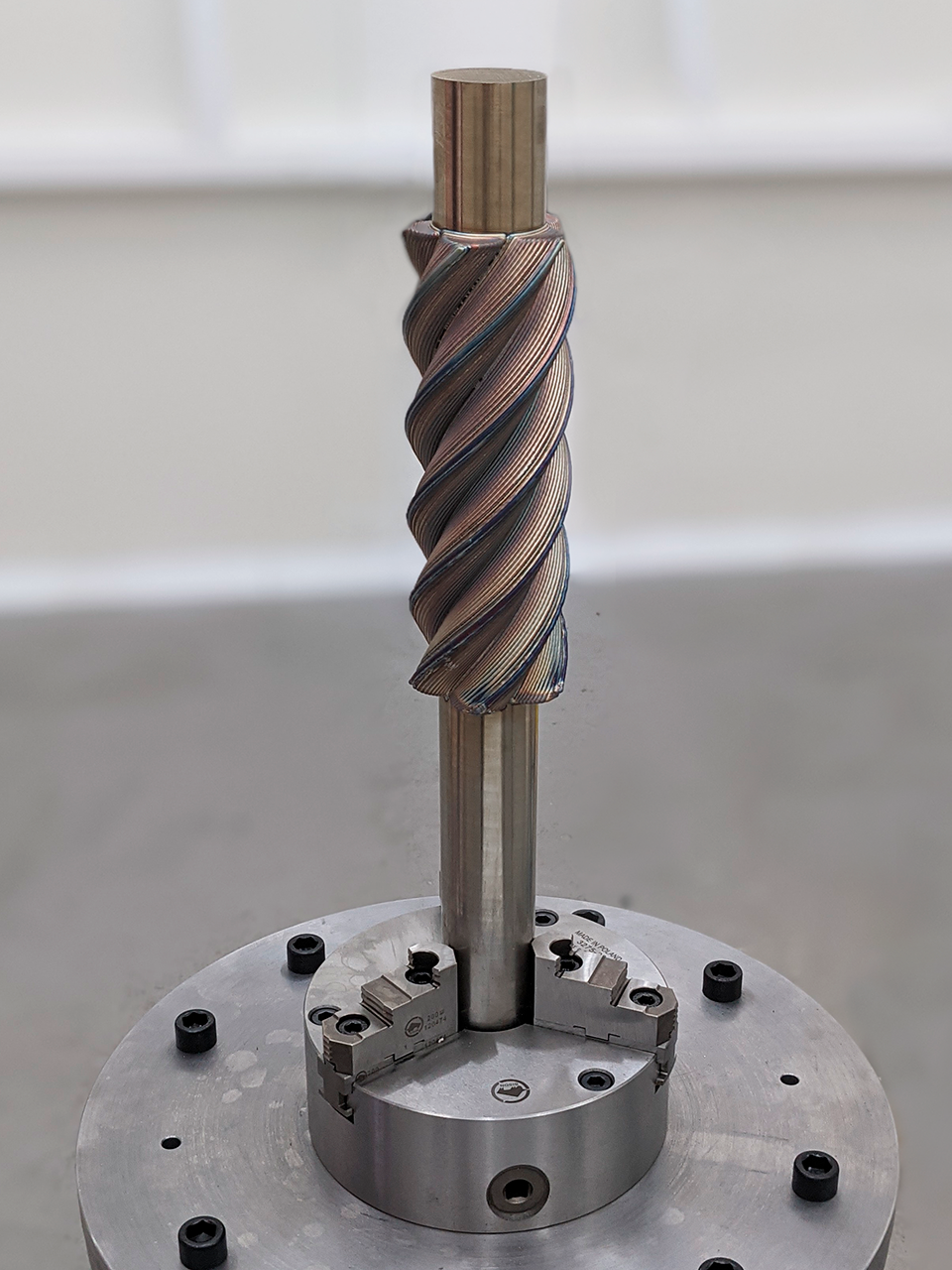
Looking forward to the future, Meltio hopes to continue its rapid growth trajectory, while expanding into new markets such as China and India, while striving to double the number of employees in the company next year.
Matthews said: “We plan to open showrooms in at least India and China in 2022. There are other markets. We may open four to five showrooms around the world next year. Of course, we will also establish a channel in these regions. The increase in personnel is a well-thought-out measure that will continue to strengthen the company’s R&D capabilities and increase the number of machine sales. Both aspects require the company’s production capacity to grow. This is a considerable project that we will undertake next year.
invest
, But this investment is driven by what we are truly proud of. As a company, we have every opportunity. “
Finally, he added that demand determines the company’s development, and it is precisely because of demand that they can sell so many machines, which in turn has achieved the company’s performance today.
(Editor in charge: admin)
0 Comments for “Automatic additive system with integrated DED technology, Meltio opens up new applications for large-scale metal manufacturing”