Introduction: British-based Bentley
car
Bentley Motors Limited, a manufacturer of luxury cars and SUVs, has announced that it will3D printingbase to carry out £3m
Invest
. The ultimate goal of this investment is to print vehicle components and further enhance the customization of customers’ cars. In 2021, Bentley will apply additive manufacturing to a wide range of applications, eventually producing more than 15,000 components. This fact, coupled with the investment, is a testament to the luxury car’s embrace of additive manufacturing.
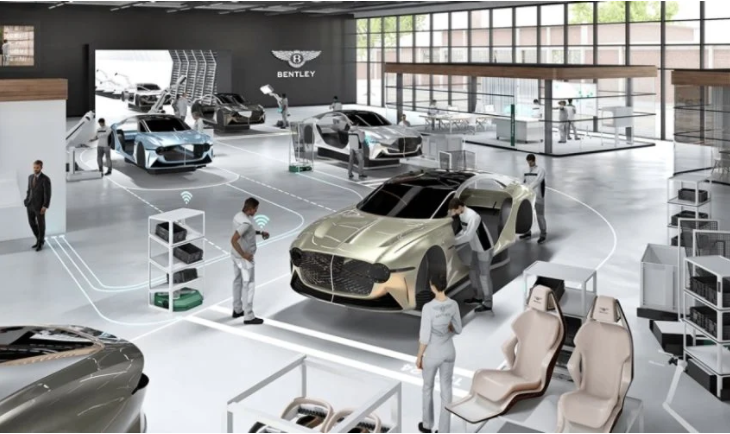
Details of Bentley Motors’ £3m investment to double additive manufacturing (AM) capacity at its corporate headquarters in Crewe. State-of-the-art additive manufacturing facilities are already in use for a wide range of purposes, producing more than 15,000 components in 2021 alone. This expansion will also enable Bentley to leverage advanced technology to create 3D printed automotive parts and enable greater personalization in customers’ cars. Crewe factory3D printingThe system is mainly powered by Stratasys’ latest generation industrial
FDM
(for advanced plastic polymer extrusion) and PolyJet (jetting materials for multi-material models) machines, including at least one HP Jet Fusion 5210 printer (for PBF polymers with nylon and TPU materials).
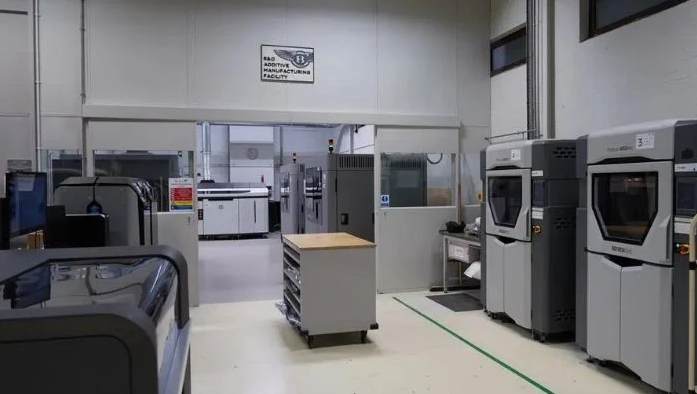
Additive manufacturing systems convert 3D CAD models into physical components and are recognized as one of the fastest growing technologies in the world. Bentley’s innovative R&D team has identified a wide variety of printable items, ranging from work aids for fabrication to lightweight sanding blocks for Bentley’s iconic carpentry shop.Additive manufacturing is also used to machine the precision tools needed to make parts for Bentley models, even with the coronavirus pandemic.
medical
The health department provided face coverings.
The latest methods help speed product development, allowing Bentley to produce large numbers of parts without outsourcing. It’s part of the company’s groundbreaking Beyond100 strategy to achieve sustainable mobility leadership by reinventing every aspect of the business. The state-of-the-art additive manufacturing equipment installed can save 50 percent on part costs, and by operating 24/7, the facility is capable of producing thousands of components in over 25 different material options. Bentley colleagues across the company are now embracing AM
training
to see how they can benefit from using state-of-the-art processes at work.
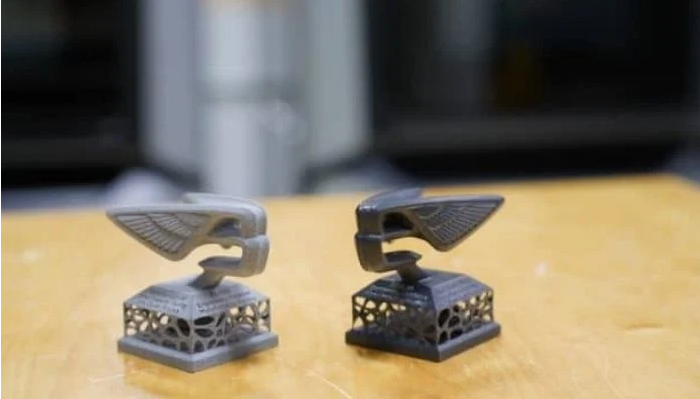
Bentley Manufacturing Council Member Peter Bosch added:
“Bentley’s approach to additive manufacturing is industry-leading, and this facility is quickly becoming the cornerstone of our ‘dream factory’ ambitions. One of the key benefits is that it is efficiency-oriented, reducing the cost and complexity of countless jobs.” The latest investment also has a significant impact on our colleagues across the company, helping to create advanced aids to drive continuous improvement throughout the manufacturing process. Going forward, this advanced technology does have tremendous potential for growth, including greater ability to provide our customers with personalized parts, as well as further enhancements to the personalization programs offered by each vehicle. “
(responsible editor: admin)
0 Comments for “Bentley Introduces New Technology, Expands 3D Printing Capabilities to Produce Thousands of New Components”