Athletes of the German Luge Association are benefiting from BMW’s metal3D printing: German bobsleigh athletes have taken advantage of this new achievement for the Beijing Winter Olympics, and bobsled athletes have some improved sports equipment.
Since 2010, the German toboggan and luge teams have been supported by BMW: As part of the technical cooperation, the expertise, infrastructure and innovations required by BMW as a manufacturer of its premium vehicles are also available to athletes. Top performance is a uniform requirement, as is every detail, no matter how small, optimized with innovative technologies to ultimately outperform the competition. The technical partnership with BMW is especially valuable for the BSD bobsled team, because in sports where a fraction of a second determines victory, materials also play an important role here.
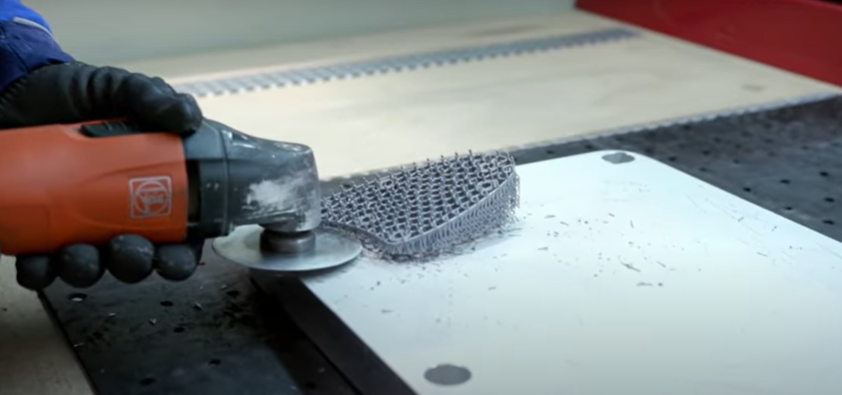
Additive Manufacturing since 1991/3D printingIt has been used in the BMW Additive Manufacturing Campus, initially mainly for development and prototyping. Due to the many advantages of this process, it now has a place in the entire product life cycle.especially in electric
car
field, 3D printing has become indispensable.from3D printerThe hardware components can be used in the early stages of development and complete their functionality during the test loop. This is because the process is inexpensive, flexible and quick to use.
On an ice track, the contact surface between the athlete and the ice generates traction and accelerates, and the state of the contact surface plays a decisive role. BMW focused on this and developed an all-new spike attachment, which developed rapidly just in time for the Beijing Winter Olympics.
For the new 3D printing results, the team first generated and analyzed digital images of the true toe geometry. This allows many different shapes to be tested to ultimately determine maximum traction on the ice.3D printercreates a filigree and stable structure that, on the one hand, enables
shoe
Lighter while also giving it the best grip across the entire forefoot area. In addition, the personal wishes of the athlete can be considered.
Since 2010, German bobsled athletes at the Winter Olympics have also benefited from BMW’s support. Here, the sled itself has to be optimized to be as light as possible without losing rigidity. For BSD, engineers made what’s called a support frame. By improving the topology and 3D printing process, it is possible to halve the weight of the structure without sacrificing function and durability. But why would you want to lose weight? More weight leads to more power for the same air resistance, which leads to higher speed. It all depends on where the weight is best placed in the sled system for maximum speed. Since regulations dictate maximum weights, every gram saved in the sled can be intentionally put in the right place to improve performance.
(responsible editor: admin)
0 Comments for “BMW pushes German bobsledders to metal 3D printing”