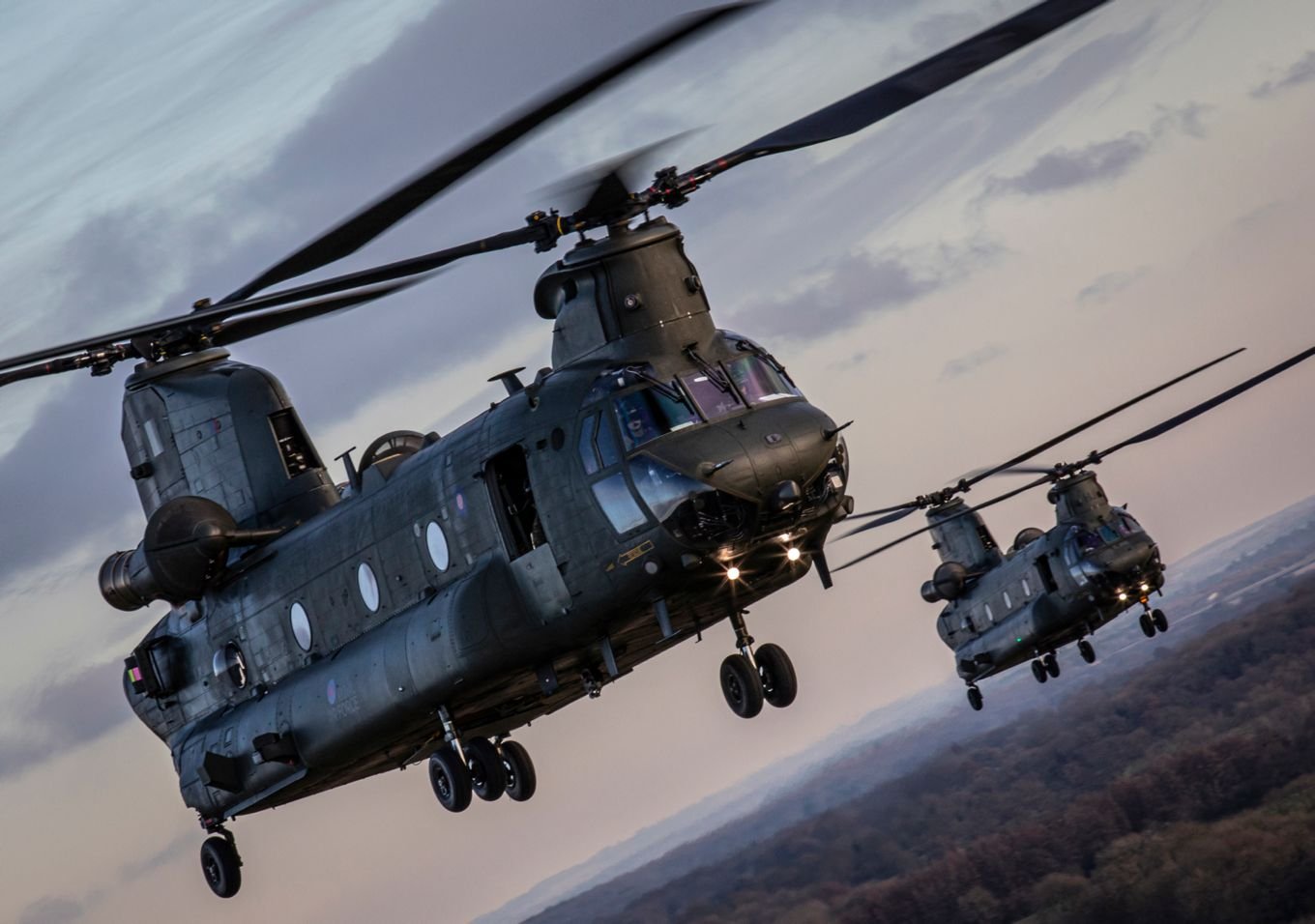
The first flight of the Boeing CH-4 Chinook dates back to the early 1960s. It is a heavy-duty helicopter with twin engines and tandem rotors.To this day, this gyroplane is still one of the heaviest lifting helicopters in the West, and is often used for air assault missions, troop and ammunition delivery, and
food
And water transportation. Chinook’s average manufacturing cost reached a jaw-dropping 35 million U.S. dollars, and its maximum flight speed was 302 km/h.
As a manufacturer, Boeing’s continued
invest
Feel proud. In particular, the demonstration of the new T408 engine aims to show that a new set of “Chinook” engines will be put into use again, and its horsepower is 50% more than the current equipment.More importantly, the key to the success of this flight test is3D printingThe aluminum gearbox housing is proven to be able to withstand the high pressures of rotorcraft flying.
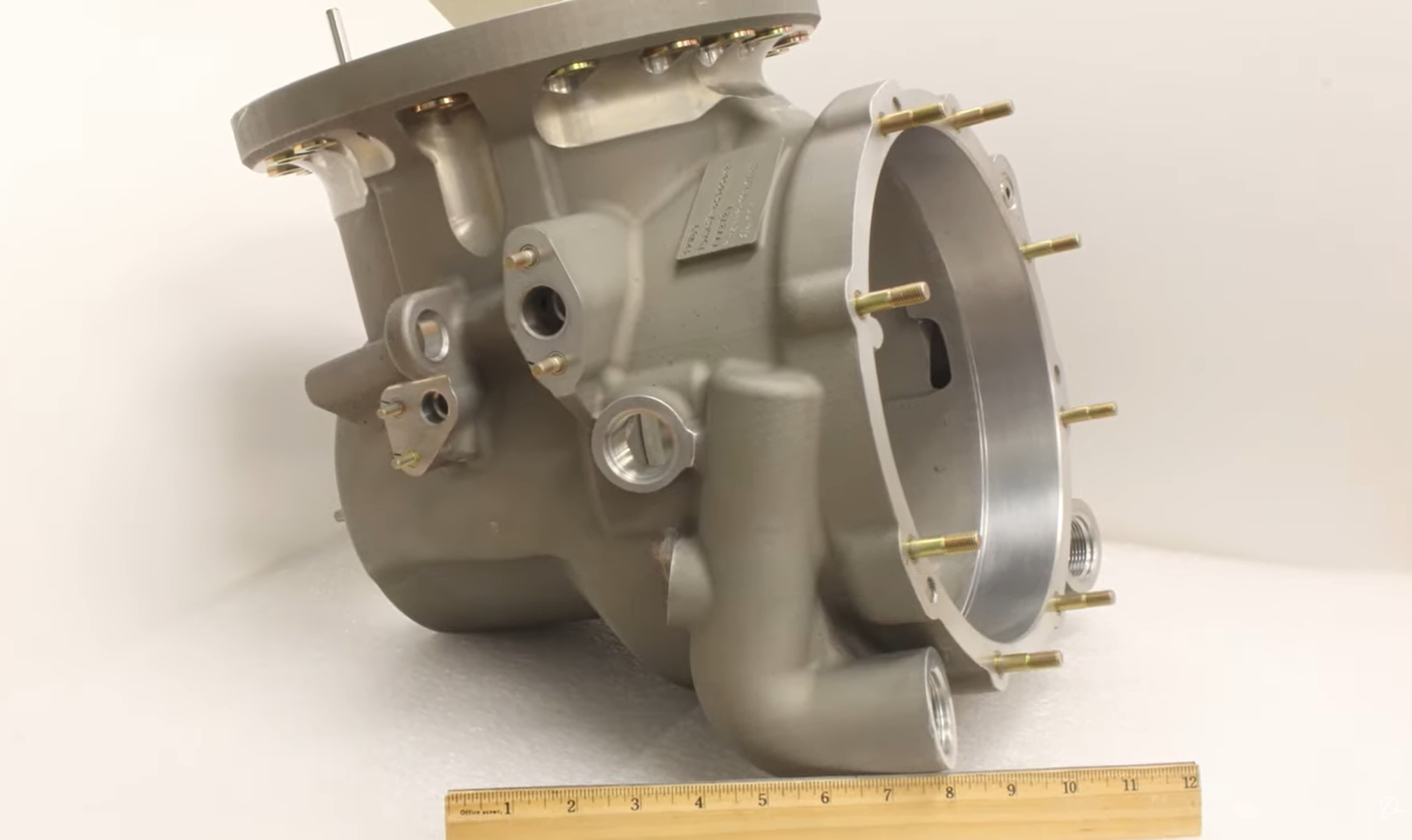
So, why should the key components of the helicopter be selected in the first place?3D printingWoolen cloth? In fact, heavy industry organizations such as the defense department are often notorious for their long delivery times, which may make the procurement of spare parts a difficult point for the military, especially when the parts in active service are out of date. Become more prominent.By internal use3D printingTechnology for terminal production, Boeing can avoid the long delivery time of traditional manufacturing, while ensuring that the cost of the gearbox housing is minimized.
Melissa Orme, Vice President of Additive Manufacturing at Boeing, explained: “AM allows creativity in design that cannot be achieved by traditional methods and is used to optimize the design of better aerospace products. We are constantly looking for opportunities in these opportunities. , We can use additive manufacturing technology to improve product performance by streamlining the vehicle, reducing its weight, and providing more durability.”
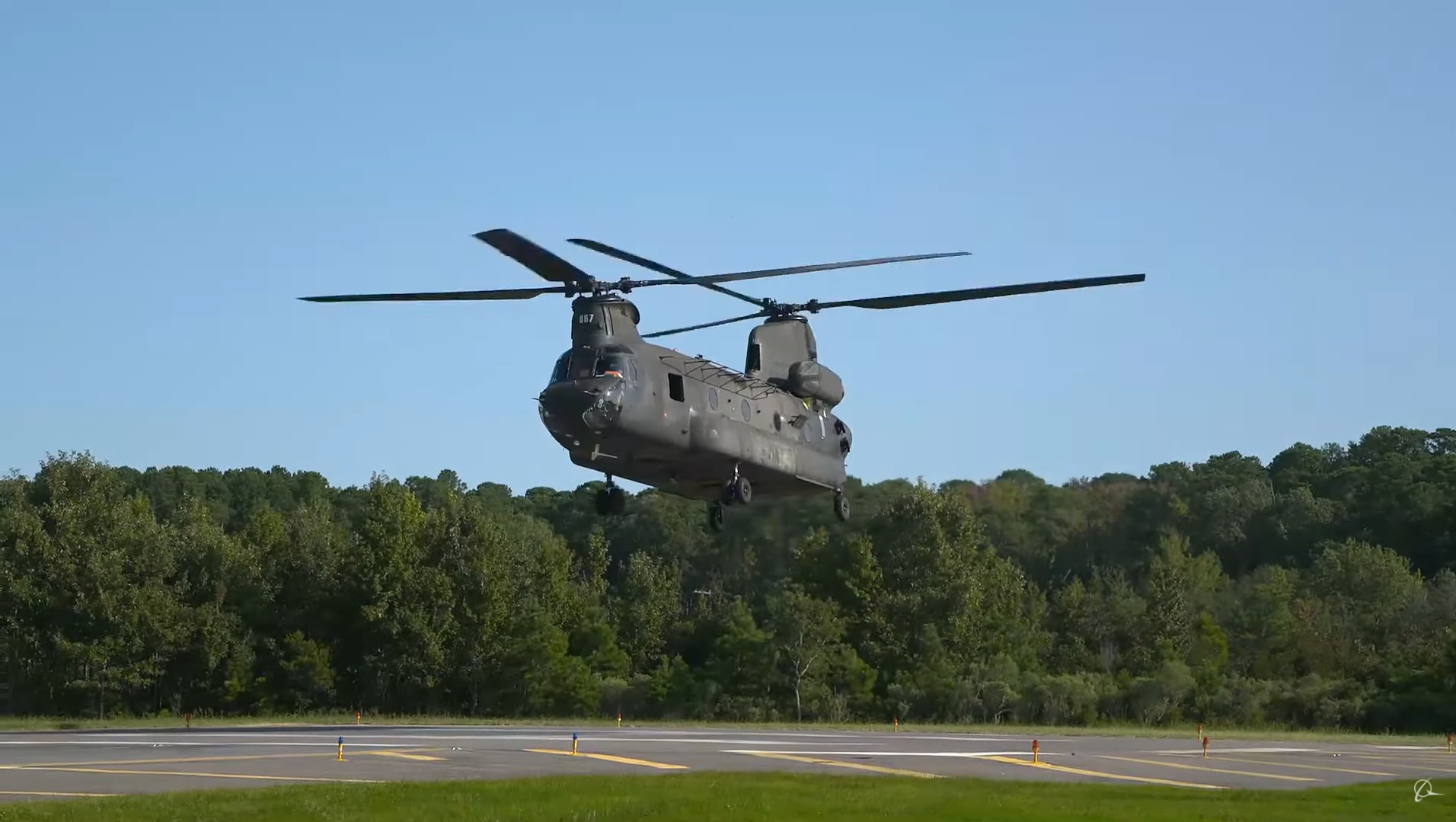
Elsewhere, students at Dade County Middle School in Trenton, Georgia, recently used their school’s
FDM
3D printingThe aircraft produces flightable parts for the International Space Station. These parts are printed on an industrial-grade Stratasys Fortus 450mc, using high-performance ULTEM filaments. This material is characterized by high strength, flame resistance, and good dielectric stability.
(Editor in charge: admin)
0 Comments for “Boeing’s first 3D printed aluminum gearbox housing was installed and helped Chinook helicopters complete flight tests”