Daimler-Benz and Germany3D printingThe machine brand EOS has established a partnership. Beginning in 2017, the two companies have launched the NextGenAM (Next Generation Additive Manufacturing) project together with other partners. The project developed a metal PBF technology industrialization process for large-scale automobile manufacturing, with a particular focus on aluminum alloys.Mercedes is still in motorsport3D printingAn important adopter of technology, in the past ten years, in its very successful F1 car, many components have used metal3D printingTechnology.
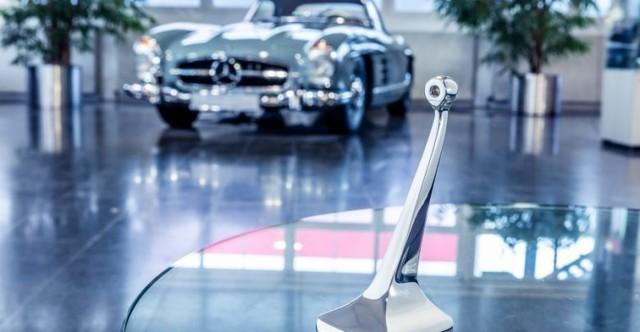
Daimler’s commercial vehicle sector3D printingThe technology has been fully integrated into the development process and mass production.Daimler trucks and buses3D printingAll technological-related innovations have deployed research and advanced development projects throughout the group, and have experienced vital development in a very short period of time.
In addition to the NextGenAM project implemented in the Siemens material solution production process, Daimler-Benz Group3D printingCarrying out serial parts production activities, these two activities are mainly concentrated on spare parts.
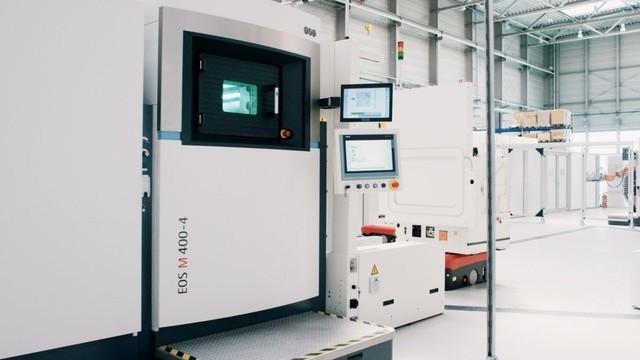
The NextGenAM project uses EOS M 400-4 four laser metal3D printingMachine for production
In the automotive field, the NextGenAM platform has been used in the production of truck parts, and its potential has been evaluated in the production of automotive and electric vehicle parts.The first replacement part for Mercedes-Benz trucks was the bracket for the truck’s diesel engine, while Daimler’s3D printingAluminum replacement parts are being carried out at Daimler Bus Technical Center3D printingCheck. A team in the passenger car field is also studying the application of additive manufacturing.
Daimler’s goal is to use an automated and scalable process to mass-produce3D printingOptimized parts, which benefit from reduced weight and lower costs. In terms of replacement parts, the company looks forward to further digitizing parts inventory to reduce storage requirements.
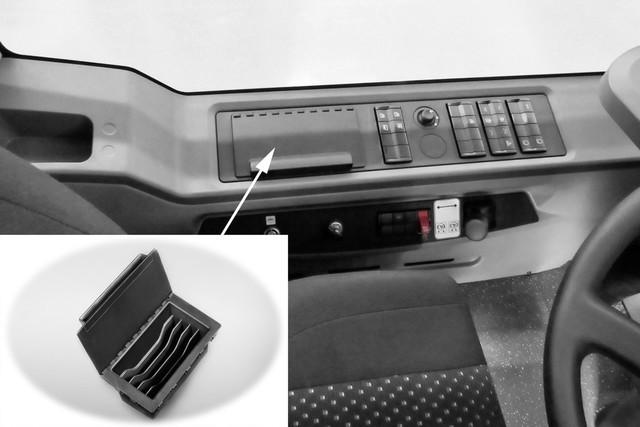
Daimler Bus also uses polymer SLS 3D printingTechnology produces passenger car interior parts for Mercedes-Benz and Setra brands.So far, it has been reported that3D printingThere are more than 1,000 components, including drawers, cover strips, fixing strips, adapters, and surround rings. Facts have proved that the process is particularly suitable for small batch production, with batch sizes ranging from 1 to 50 units.
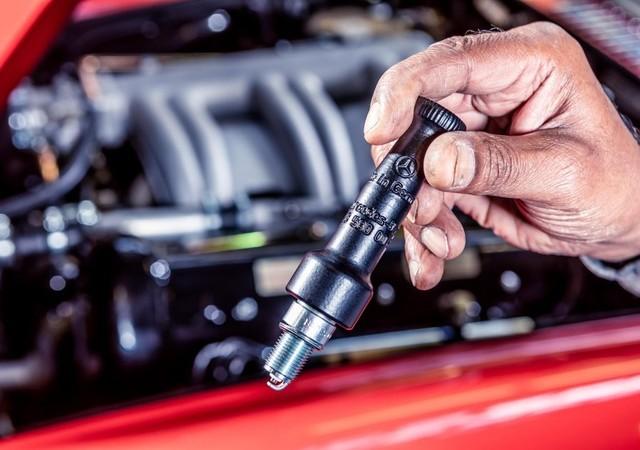
Mercedes-Benz classic cars also adopted3D printingpart. The base of the rearview mirror of the Mercedes-Benz 300 SL coupe (W 198 model series) is made of metal PBF 3D printing; W 110, W 111, W 112 and W 123 model series of the spark plug holders and sliding sunroof rollers in the tool kits are melted with nylon powder3D printingTechnology for manufacturing.
(Editor in charge: admin)
0 Comments for “Car manufacturing: How Daimler Benz uses 3D printing”