October 29, 2021, heat exchanger3D printingExpert ConfluxTechnology announced the completion of a round of USD 8.5 millionFinancingIn addition, its research and development work has also made significant progress.With Australia’s “Synchronous Radiation” particle accelerator, Conflux Technology can inspect heat exchangers at a sub-microscopic level and identify3D printingAnomalies hidden in the components. At the same time, the company said that through the newly raised cash, it aims to accelerate its “transition from research and development to full-fledged production” and its “long-term plan” to launch its products.
Michael Fuller, CEO of Conflux Technologies, said: “TheseinvestWill enable us to substantially increase our production capacity and capabilities.We will increase the number of metal AM machines and invest in the latest series production platform, continue to develop our team, and further advance our relationship with partsPost-processingVertical integration. “
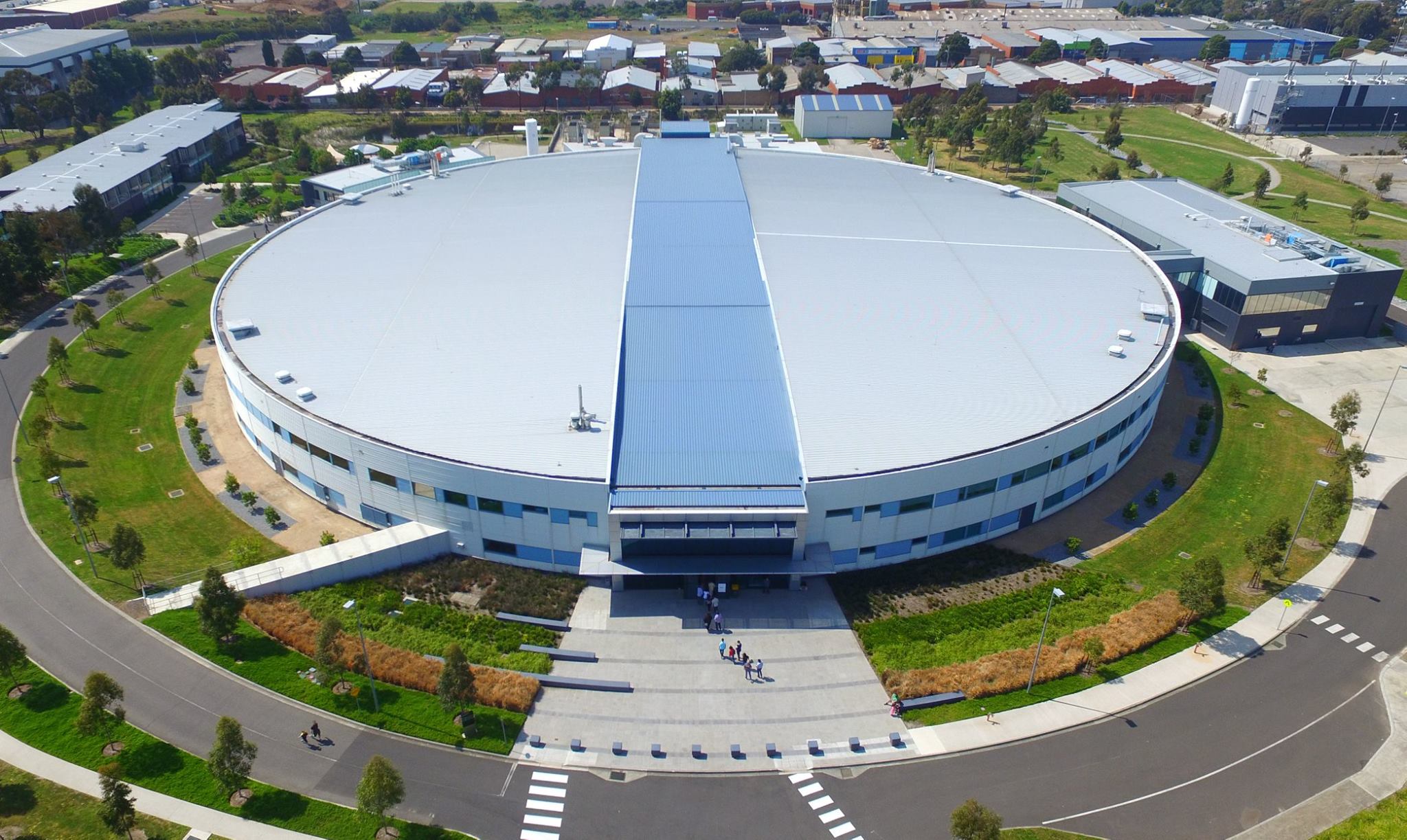
△Australia’s’Synchrotron’ particle accelerator. The photo is from ANSTO.
“Pioneer” in heat exchanger technology
Conflux Technology was founded in 2017 by Michael Fuller. He is an engineer and designer of Formula One, World Rally and Le Mans award-winning cars. He is proud to be a “pioneer of heat exchanger technology”.In order to bring the knowledge about heat exchangers he learned from the racing world to other industries, Fuller adopted metal3D printingTechnology, his company is now using this process to create optimized heat exchange components.
Specifically, Conflux Technology uses computational heat transfer simulation and processing technology tocar,national defense,aviationaerospaceCompared with the traditional equipment, the unique design provides them with the advantages of quality, performance, cost and delivery time.
Conflux also provides customers with a series of engineering services, from initial product design to post-processing support. For example, using its finite element simulation tools, the company can evaluate the durability of parts before production, and the CFD simulations they provide are said to provide insight into product characteristics, enabling customers to minimize printing errors.
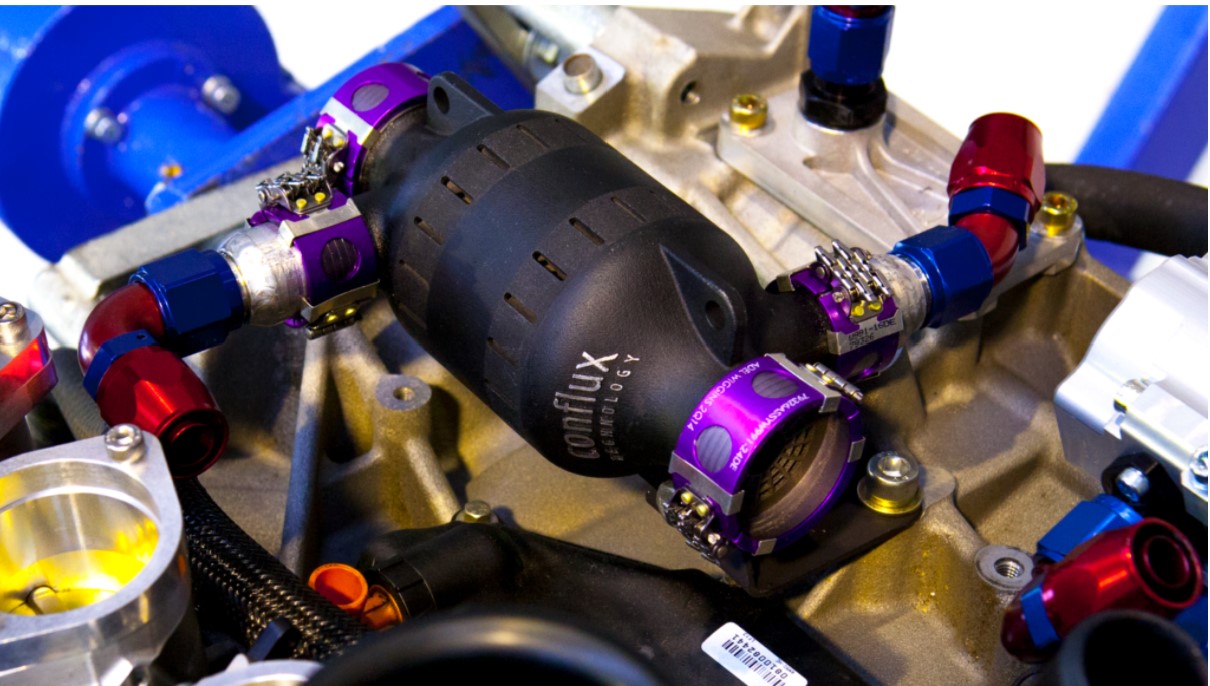
△Conflux Technology Company specializes in heat exchangers with optimized thermal performance3D printing. Photo courtesy of Conflux Technology.
Research and development progress of Conflux Technology
According to Conflux Technology, its3D printingThe heat exchanger manufactured by the dominant method has obvious geometric advantages, which cannot be achieved by brazing or subtractive manufacturing. However, it also added that these advantages also bring challenges, because optimized overall components often have complex internal structures, which makes it difficult to assess the probability of thin-wall failures.
In order to overcome this shortcoming, the company has turned its attention to the “Synchronous Radiation” equipment located at the Australian Nuclear Science and Technology Organization (ANSTO) Melbourne facility. ANSTO’s circular particle accelerator is about the size of a football field. It mainly emits electrons through a series of interconnected tunnels to produce a strong beam (more than one million times brighter than the sun).
Using a magnetic field, the synchrotron forces these electrons into a circular orbit, where they can be disturbed at certain points, producing infrared radiation and intense X-rays, and being guided into various instruments. In the case of Conflux Technologies, it has found a way to use this technology as a means for them to improve the resolution and scale of inspection heat exchangers.
In order to help screen the massive cross-sectional data provided by the synchrotron radiation experiment, Conflux has developed the “Conflux Quantify” analysissoftware, These data can generate up to 1M bytes of information. The company said that by using a proprietary program, it can now accurately assess the wall thickness, surface roughness, and feature accuracy of a given part, while detecting structural defects earlier than before.
To demonstrate the advantages of their method, Conflux Technologies shared two images of microtubes, one is traditionally manufactured, and the other is manufactured with parameters collected by a particle accelerator (see below). Not only does the latter have better density and a more consistent shape, but the company says its enhanced workflow makes parameter verification easier and minimizes part delivery time.
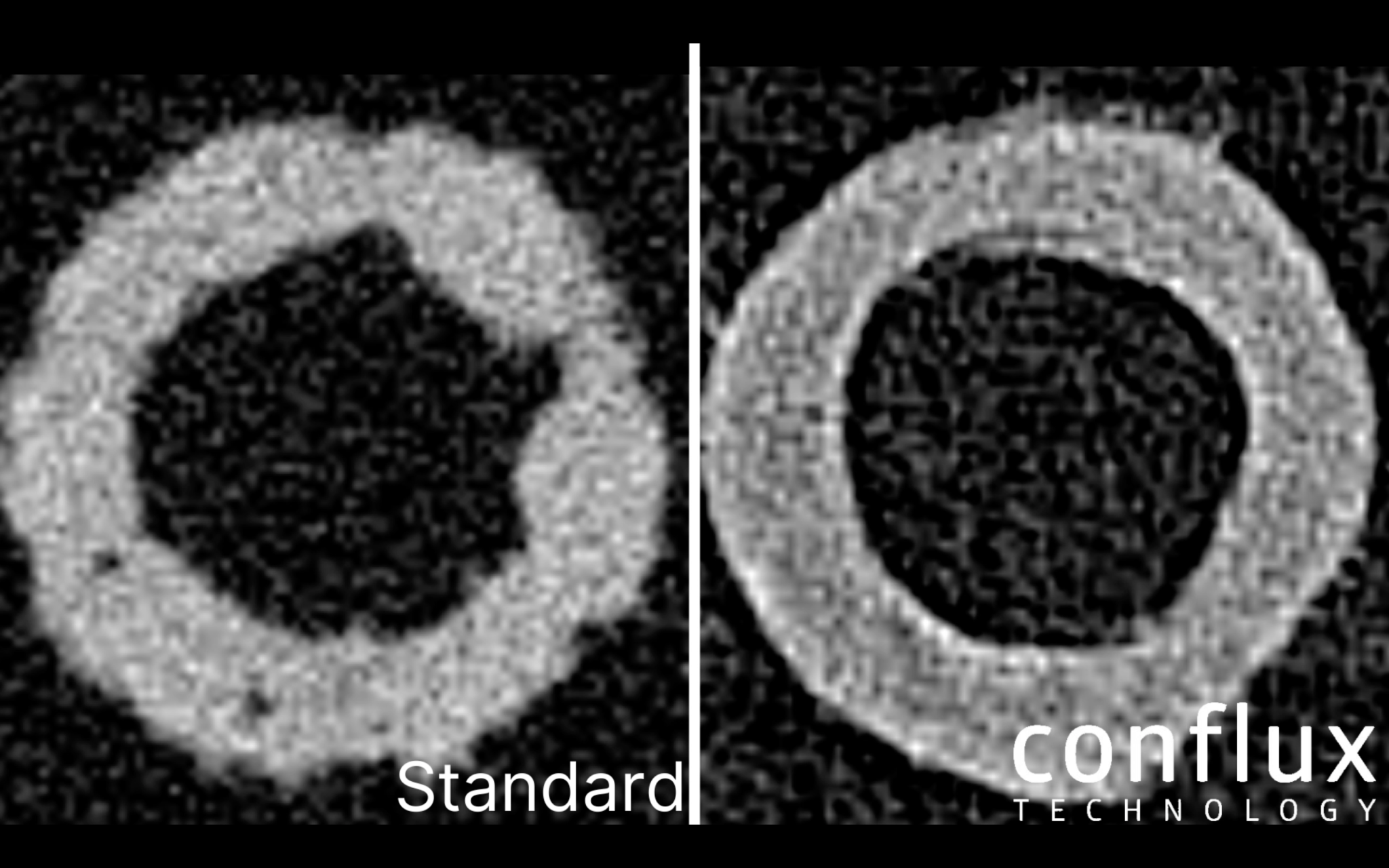
△Cross section of two microtubes-one usedstandardParameter construction, another custom parameter using Conflux. Picture from Conflux Technology.
Continuous support from AM Ventures
Since the breakthrough in research and development, Conflux Technology has also completed A round of financing, in which long-term supporter AM Ventures and financial company Acorn Capital provided it with 8.5 million U.S. dollars (Australian dollars) support. AM Ventures launched a 100 million euro venture capital fund earlier this year to support3D printingStartups, the company has a legendary history in accelerating the development of the most promising companies in the industry.
In the past, AM Ventures invested US$5.5 million in 3YOURMIND and contributedDyemansionContributed $14 million in financing, and it also provided seed funding for Conflux Technology in 2017. At that time, the heat exchanger expert said that capital would enable it to advance the functional application of its technology, and achieve quantifiable benefits conversion in the following years.
ArnoHeld, managing partner of AM Ventures, said: “Highly complex geometries enable more effective thermal management to reduceenergyConsumption and material waste require highly qualified experts who can master the best manufacturing technology and software tools.The heat exchanger is3D printingOne of the largest applications in Conflux, its complex geometric structure is also difficult to achieve by ordinary manufacturing methods, and this is where the Conflux team excels. “
According to Conflux Technology’s own statement, the success of its investment round reflects its3D printingProgress made in the design and application of heat exchangers. The company also pointed out that their ability to match the needs of aviation, microelectronics and racing customers is the key to their support.
Fuller concluded: “We are very pleased to work with such experienced and successful investors. Acorn and AM Ventures have enviable experience in accelerating business scale and implementing transformative technologies that have a positive impact on our world. We look forward to the next very exciting chapter in Conflux’s journey.”
(Editor in charge: admin)
0 Comments for “Conflux completes $8.5 million in financing, which will further promote the development of 3D printed heat exchangers”