On March 4, 2020, Manchester Metropolitan University (MMU) conducted a 9.6 million euro project to convert disposable plastic waste into additive manufacturing (3D printing) Available raw materials.
It is reported that the purpose of this project is to provide a “sustainable life cycle” for waste and promote the development of recycled plastics.They will use these recycled plastic raw materials to produce new products such as tables, chairs and customized3D printingproduct.
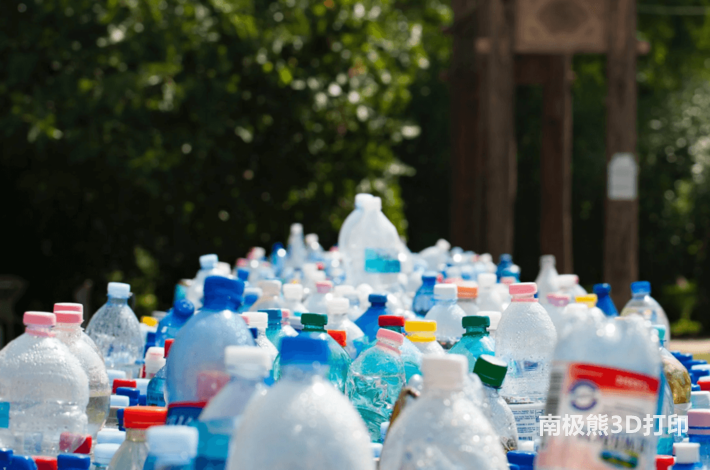
Manchester Metropolitan University will use its industry 4.0, next-generation materials,3D printingAnd the expertise in sustainable economics, leading this project called TRANSFORM-CE.
Manchester Mayor Andy Burnham expressed support for this new initiative because Manchester hopes to be carbon neutral by 2038: “Reduce single-use plastics is a key focus area for Manchester, and we support change and reduce Consumption and production of single-use plastics.”
This project has received 9.6 million euros in funding from ERDF, and TRANSFORM-CE will transfer thousands of tons of waste from landfills throughout Northwest Europe. In the process, they are also trying to create new economic needs to attract local and more distant businesses to use recycled plastics.
In addition, the project will also build two specialized plastic recycling plants, one in Manchester and the other in the Netherlands, which will start next year.
At Manchester Metropolitan University3D printingIn the factory (called PrintCity), the school will cooperate with local companies through3D printingTechnology uses recycled plastic materials to create sustainable new products.
PrintCity is a 3D additive manufacturing and digital manufacturing center that brings together manufacturing experts, designers, engineers and students from the MSc Industrial Digital Course of Manchester Metropolitan University. In 2018, Manchester Metropolitan University announced a cost of 6 million pounds, covering an area of 40,000 square feet3D printingThe plan of the factory, the factory is called Cheshire 3D Print Hub, as an extension of PrintCity.
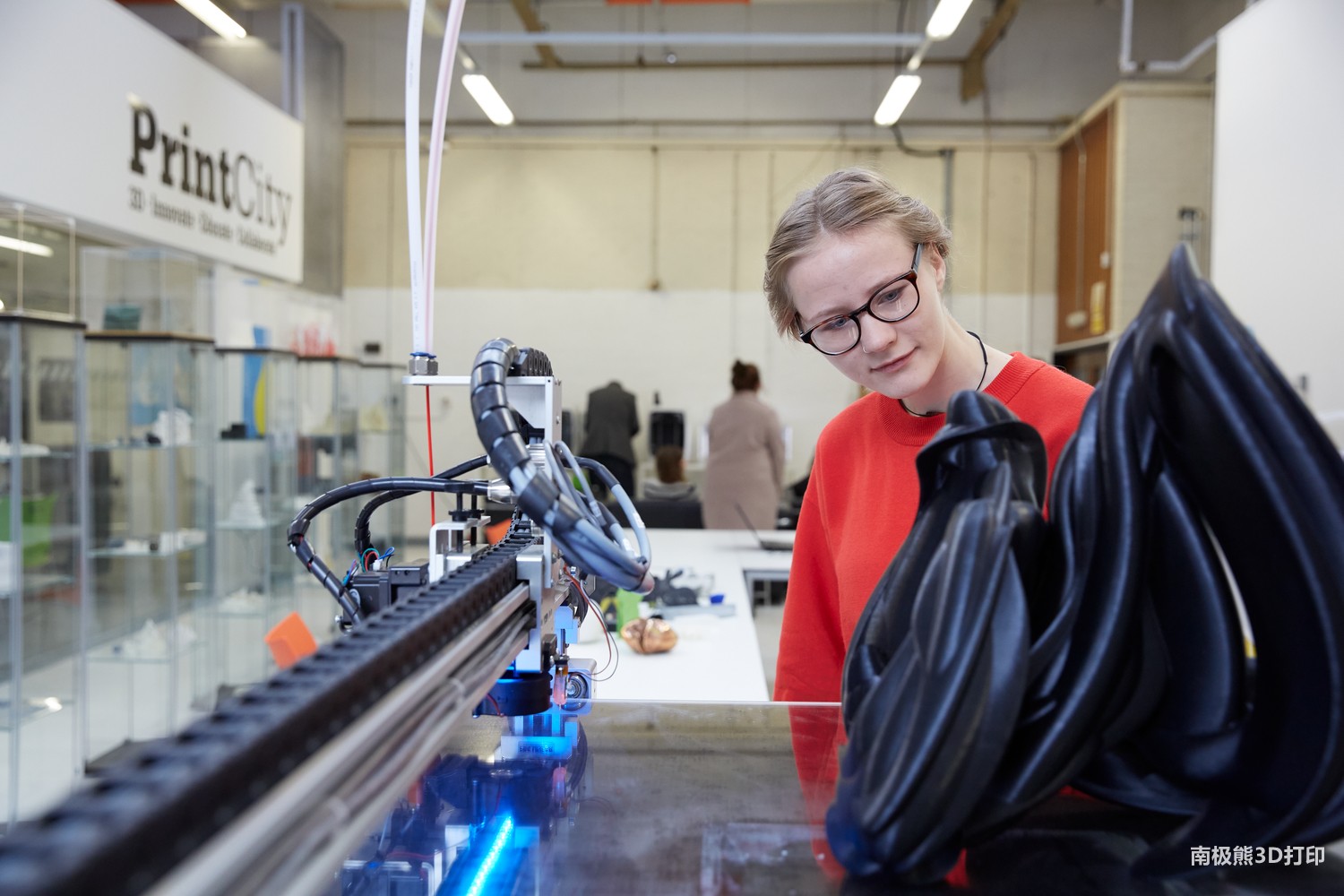
Disposable plastics cause a lot of pollution to the ocean and land. It is estimated that 8 million types of plastic pollution enter our oceans every day, and 79% of waste plastics end up in landfills or discarded. Most plastic products are produced from scratch using virgin materials and natural resources. These products are usually only used once, and in some cases, before turning waste into treasure, they will be recycled into another inferior product.
The purpose of the TRANSFORM-CE project is to transform this linear recovery model into a recycling model so that the product can maintain its value and be recycled. Amanda Reid, head of the University’s Waste Resource Innovation Network Program and Project Manager, explained: “By reassessing our existing single-use plastic raw materials and transforming our consumption and production model from a linear economy to a circular economy, We should be able to make a real difference with current single-use plastic products. By turning this change into a circular economy, and by decoupling economic growth from resource consumption, we can begin to make changes.”
In order to create a recycling model, the project uses3D printingConvert disposable plastic waste used in landfills into new products with higher value.Hard plastic products such as beverage bottles will be transformed into3D printingWire for3D printingA series of products. On the other hand, low-value plastics including films and foils will be used to make products such as tables and chairs.
TRANSFORM-CE is committed to providing enterprises with3D printingWire materials to replace pure plastic raw materials, thereby supporting them to adopt a circular economy. Professor Craig Banks, Project Director of TRANSFORM-CE, concluded: “We are leading this cyclical step change, working with EU research institutions, companies and governments to support the adoption of a circular economy and wider participation, which is really amazing.”
Recycling of other waste plastics becomes3D printingExamples of materials include:
August 2019,
Large format3D printingMachine manufacturer BigRep uses 100% PET material recovered from plastic bottles
,3D printingAn urban green habitat installation was established, and the project was named GENESIS Eco Screen.
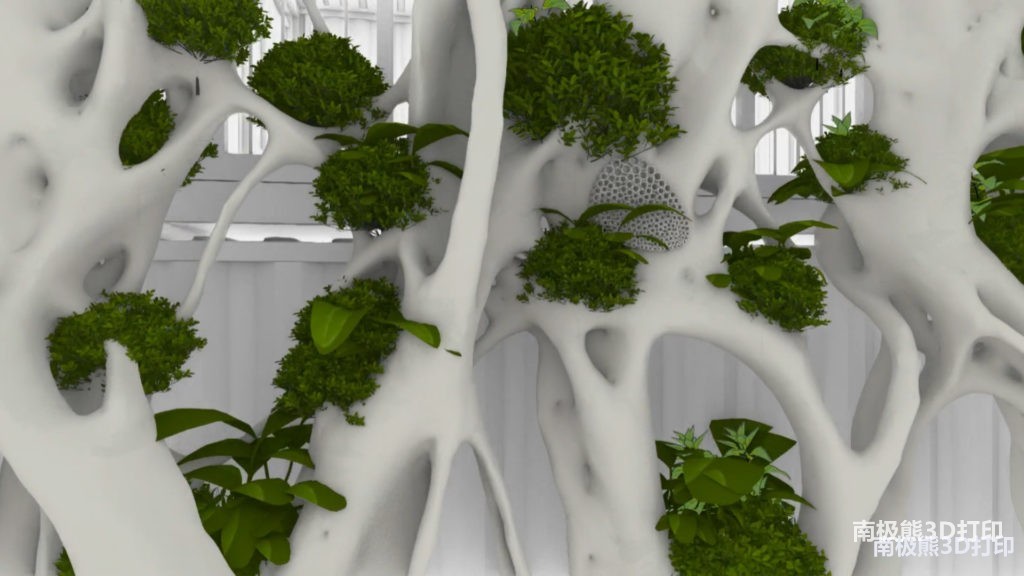
In December 2019,
Belgian designer and artist joachim froment uses plastic waste as a raw material in his latest sustainable furniture series
. “Strat” is made of locally recycled plastic, and3D printingInto a seat and a stool. The whole series of works include stools, lounge chairs and a variety of other furniture.
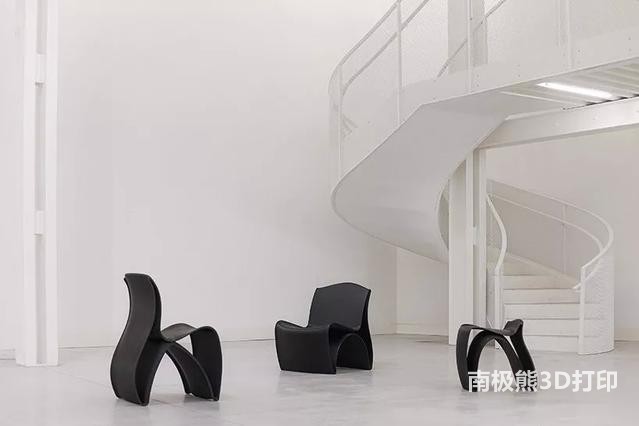
January 2020,
The British start-up Fishy Filaments provides local fishermen with a safe and sustainable way to recycle their old or no longer useable fishing nets
, And then turn these fishing nets into3D printingMaterials, while reducing the space occupied by the landfill and the potential hazards that may be caused.
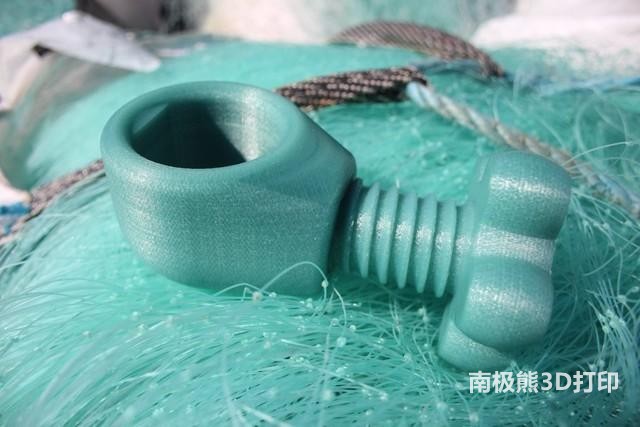
Compiled from: 3dprintingindustry
(Editor in charge: admin)
0 Comments for “Convert waste plastic bottles into 3D printing raw materials, Manchester Metropolitan University receives 9.6 million euros in support”