3D printingTechnology originated in the 20th century and has gradually developed and grown in the last ten years. It has become one of the key technologies in the automotive manufacturing industry. Currently,3D printingThe widespread application of technology in the automobile manufacturing industry has become a general trend.3D printingThe application of technology in the automobile manufacturing industry is divided into three stages: prototype testing, production tool manufacturing and component manufacturing.In the product development stage, automotive design engineers use3D printingMake prototypes, simulate actual parts that have not yet been mass-produced, and use it for testing and improvement to achieve “what you see is what you get” and greatly improve the efficiency of car design. Besides,3D printingIt is also used in manufacturing production tools, such as labeling machines. Since only a dozen labeling machines are needed in each factory, the average cost of mold opening manufacturing is too high.In contrast, many car companies currently choose to use in the factory3D printingThe machine, ready to use, saves the cost of mold opening, inventory and logistics. In terms of parts manufacturing,3D printingA series of testable parts with subtle differences can be quickly produced to help develop the most suitable parts to ensure that the best parts are selected for final production, which improves the efficiency of the entire development process, shortens the car’s time to market, and Reduce time and production costs.
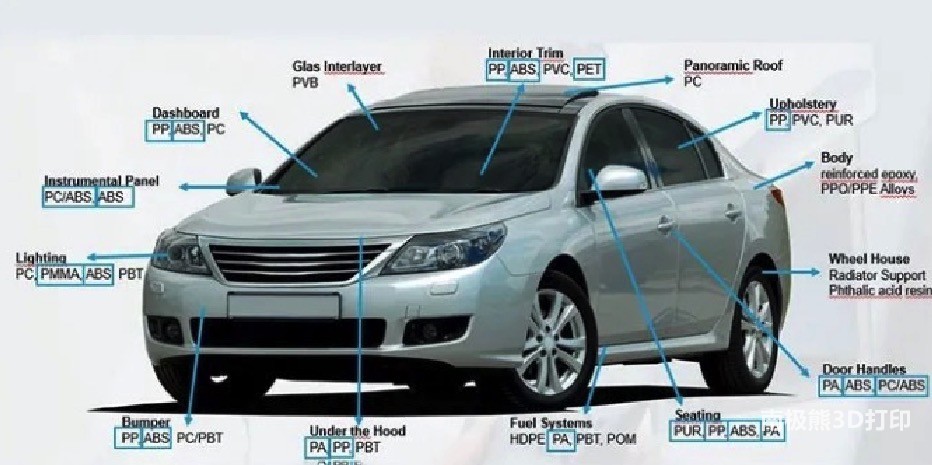
At present, whether it is a German car brand Volkswagen, BMW, or an American car brand Ford, Japanese car brands Toyota, Honda have their own3D printingManufacturing center and3D printingBrand manufacturers conduct in-depth cooperation.So3D printingHow is the technology currently used in the automotive industry? What are the technological breakthroughs and cases?Welcome to visit the Shenzhen International Convention and Exhibition Center on September 9-11, 2021
Formnext
+ PM South China Shenzhen International Additive Manufacturing, Powder Metallurgy and Advanced
ceramics
Check out the exhibition.
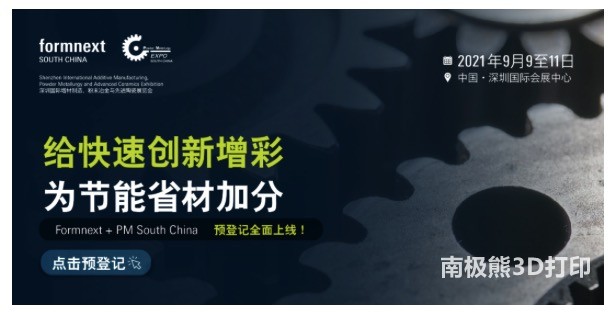
Equipment articles
SLM Solutions
(Booth No.: D46) As a regional laser melting leader from Germany, it has many applications in the automotive field, including automobile gearboxes, steering knuckles, engine cylinder heads, heat insulation brackets, radiators, engine covers, Exhaust manifolds, etc., greatly reduce the time consumption of parts manufacturing, reduce the weight of parts, improve the performance of parts, and reduce manufacturing costs.

Xinshan Aerospace/
ExOne
(Booth No.: E64) as head metal spray3D printingThe machine company, and Ford Motor Company announced the development of a fast and reliable binder sprayed aluminum alloy 3D printing and sintering technology, which can achieve performance similar to traditional die casting, and at the same time it is compatible with Ford’s first binder sprayed aluminum alloy. alloy3D printingAnd the successful research and development of high-density sintering, also applied for a patent. As an excellent partner authorized by ExOne, Xinshan Aerospace is willing to share ExOne global cases with you, and provide you with the most valuable additive manufacturing technology with great concentration and pragmatism.
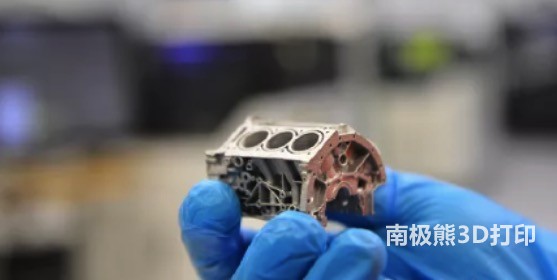
EOS
(Booth No.: D26) as3D printingThe global technology and quality leader in high-end additive manufacturing (AM) solutions for equipment. Use its equipment EOS P 396 to produce racing cooling systems for the DHBW Enginee-ring Stuttgart team. After the team used the system, the temperature in the battery box dropped from as high as 80 °C to only 50 °C. The cold air distribution is also more uniform, and the cooling performance is improved by more than 100%.
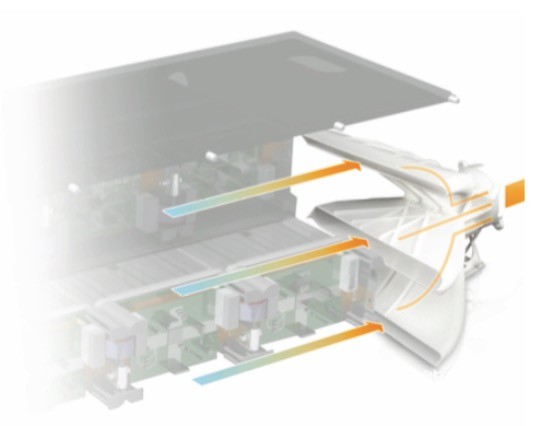
Anisoprint
(Booth No.: E69) is a company headquartered in Luxembourg, developing composite continuous fiber coextrusion3D printingTechnology technology company.Ford’s Valencia plant in its3D printingThe center introduces Anisoprint Composer A3 continuous fiber3D printingMachine to improve the efficiency of its industrial processes. Composer 3D printingThe machine speeds up the production cycle and reduces the downtime of the factory.
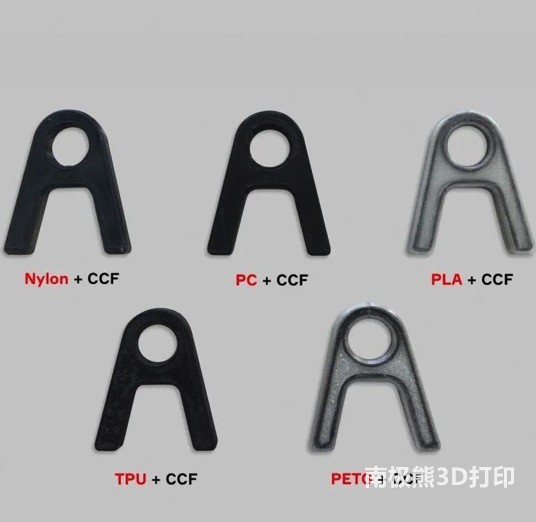
Beijing Longyuan Forming (Booth No.: F04) is the first to develop sand casting in China3D printingOne of the equipment manufacturers, Longyuan Molding’s independent research and development of the 3DP inkjet sand mold printing process for casting, has an absolute advantage in the small and medium batch production of large-size and complex structure automobile parts. Multiple parts are printed at the same time, the speed is about 4 times that of the traditional process, which significantly shortens the cycle of product development and trial production, saves development costs, and accelerates the time to market for products. It can realize the rapid casting of automobile engine volutes, cylinder blocks, cylinder heads, transmission housings, pipelines and other components.
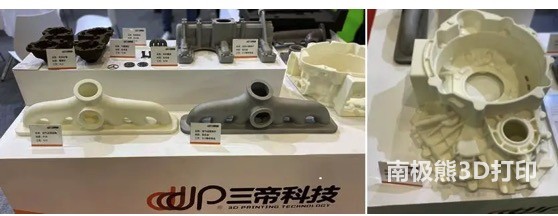
Easy Plus 3D
(Booth No.: D43) As a domestic metal3D printingAn excellent manufacturer of equipment, cooperated with the Delta racing team of Mannheim University of Applied Sciences, Germany, and printed and formed aluminum components through the easy-to-add three-dimensional EP-M260 precise numerical calculation method, topology and production optimization design Compared with the previous CNC milled parts, the weight of the whole vehicle can be reduced by more than 50%, which significantly improves the performance of the racing car.
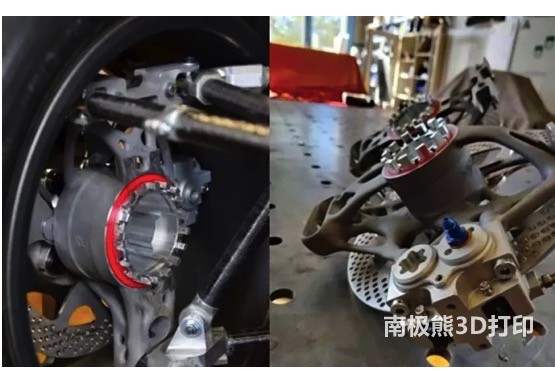
Shanghai
Far cast
(Booth No.: D49) As a focus on high-performance functional materials3D printingA high-tech company that develops, manufactures, and sells aircrafts has cooperated with SANKI Co., Ltd., a company located in Ishikawa Prefecture, Japan, that produces special vehicle cabs and compartment-related parts.Since parts such as air-conditioning vents used in special vehicles need to be custom-designed and manufactured, there is no way to purchase common parts from the market. The company uses
INTAMSYS
FUNMAT PRO 410 3D printingThe equipment only needs half the price of mold opening and injection, which can meet the parts used in special vehicles more efficiently, quickly and flexibly.
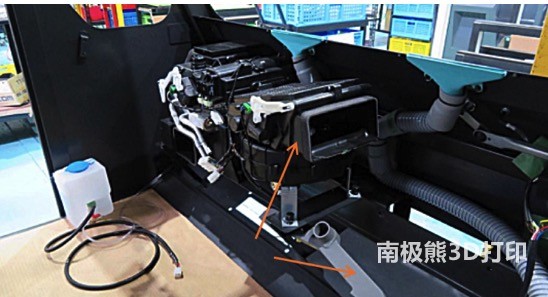
Materials
Evonik
Chemical (Booth No.: D56) As one of the chemical giants, Evonik provides a complete set of automotive metal alternatives. For example, a rigid foam named ROHACELL® can be combined with a carbon fiber skin to form a sandwich structure, which has the characteristics of light weight and high rigidity. It is a composite sandwich structure for automobile structural parts and body coverings such as engine room covers, doors, and roofs. The ideal foam core material. In addition to the body, Evonik is still exploring ways to use high-performance polymers to replace metal parts such as anchors, chains, and gears in vehicles. The high lubricity and wear resistance polymer VESTAKEEP® polyether ether ketone developed by it has been used in the underbody universal chain, transmission parts, supercharging system and so on. VESTAMID® polyamide 12, which has extremely high stability and wear resistance, exerts the effects of chemical resistance, high temperature resistance, noise reduction and shock absorption far better than metal parts in the steering angle sensor gear transmission mechanism.
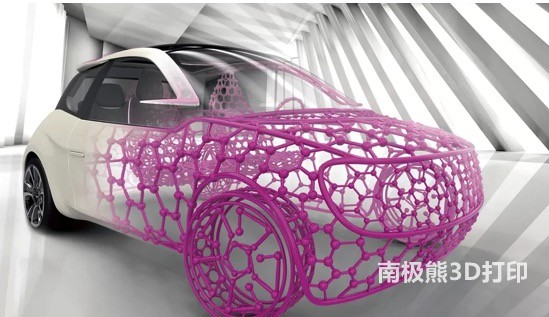
Markforged
(Booth No.: D137), a manufacturer of continuous fiber reinforced additive manufacturing (AM) technology, cooperates with DANA, a supplier of power transmission systems and electronic propulsion systems in the automotive industry with a long history of 115 years.Dana deployed a large amount of Markforged metal and carbon fiber3D printingMachine, Dana
invest
Additive manufacturing. It is worth mentioning that Dana’s team in Trentino, Italy uses Markforged X7 3D printingOn the platform, manufacturing customized gear parts printed by Onyx saves 70% of the cost, and the delivery time of each fixture is reduced by 90%. So far, these gears have not failed for more than a year.
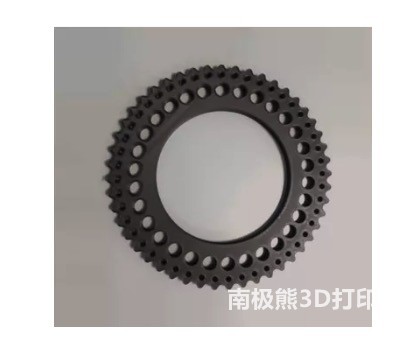
Polymaker (Booth No.: D140), a high-tech enterprise focusing on additive manufacturing technology and functional materials, and the electric vehicle company XEV from Italy have achieved3D printingMass production of cars, entering the Chinese market, this brand new3D printingThe car is called SLEV.In addition to some special parts such as the chassis, glass, steering wheel, and seats, the other main parts of this car are made of3D printingThe technology is completed, and its body material adopts enhanced
Resin material
, Both toughness and firmness are very good, and the strength of a single material is even stronger than ordinary stamped steel plates.
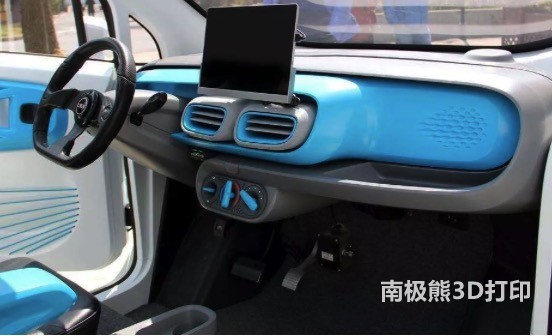
GKN Additive (Booth No.: F23), GKN Additive is the first to apply DP600 dual-phase steel material widely used in the automotive industry in the field of additive manufacturing. DP600 material is a low-alloy dual-phase steel, newly developed by GKN for additive manufacturing
mineral powder
The materials are DPLA (dual phase low alloy) and FSLA (free sintered low alloy). Applications include adjusting the design of automotive sheet metal parts or developing new structural parts. They meet the mechanical performance requirements similar to DP600 (HCT600X/C), and can realize diversified designs and applications in automobiles and other industries through additive manufacturing technology.
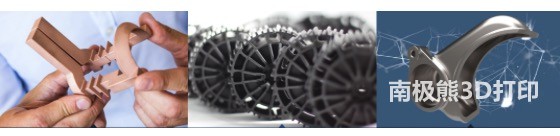
In summary, the Formnex + PM South China exhibition to be held at the Shenzhen International Convention and Exhibition Center on September 9-11 will fully present the current3D printingThe application of materials, equipment and technical solutions in the automotive manufacturing industry. All colleagues in the automobile manufacturing industry are welcome to visit and understand. You can scan the QR code at the end of the article to sign up for participation.
At the same time, with the new
energy
Automobiles are becoming more and more popular, and the lightweight manufacturing of automobiles has become an important direction for the development of the automobile industry.3D printingThe emergence of technology and the continuous deepening of its application have made it easier to achieve lightweight automobile manufacturing.Take Tesla as an example, it has been widely used in production3D printingTechnology, however, Tesla’s use of3D printingThe technology is strictly confidential, but the combination of structural integration and lightweight is a major direction for new energy vehicles to seize the forefront of technological development.
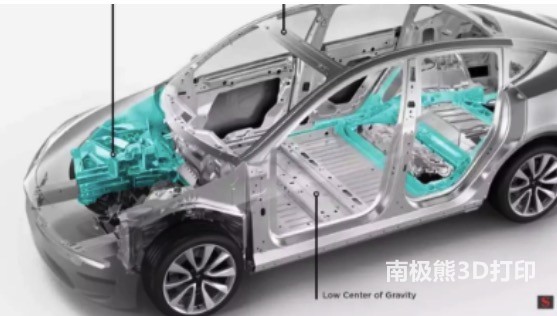
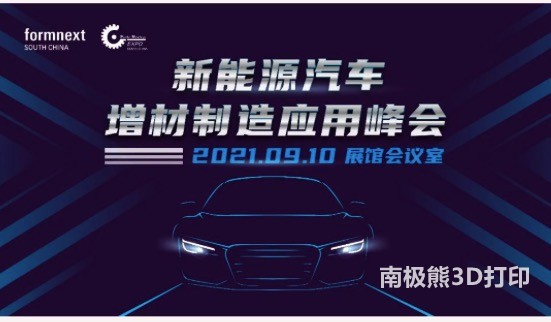
Formnext+ PM South China will also host a new energy vehicle additive manufacturing technology application summit. It is planned to invite SLM, Evonik,
Bright
, Yuanzhu, Yijia 3D and brand car manufacturers will discuss with you how to apply3D printingTechnology effectively reduces R&D and innovation costs, and effectively improves efficiency, responding to innovative and personalized customer needs. Want to know more? Welcome to communicate with major manufacturers in the new energy automobile industry on the spot.
(Editor in charge: admin)
0 Comments for “Demystify the cutting-edge application of 3D printing technology in the automobile manufacturing industry and its future development direction!”