Introduction: This paper describes the challenges associated with DED processing and provides key perspectives on the technology. This article is the third part.Keywords: Additive Manufacturing (AM), Directed Energy Deposition (DED), Laser Engineering Net Shaping (LENS), Laser-Material Interaction Defects
Defects in deposited materials and their characterization
DED is a non-equilibrium processing technology with fast cooling rate and large thermal gradient. These thermal conditions can lead to complex phase and microstructural changes, non-uniform residual stresses, deformation, porosity, cracking, and consequently corrosion resistance degradation, mechanical behavior (such as ductility and fatigue strength), and premature failure. These are the topics of this section. The formation mechanism, measurement, modeling, and mitigation of these defects are discussed. Table 3 summarizes some of the major defects, their sources, their impact on material properties and component selection, and their characterization techniques. The following subsections discuss them in more detail.
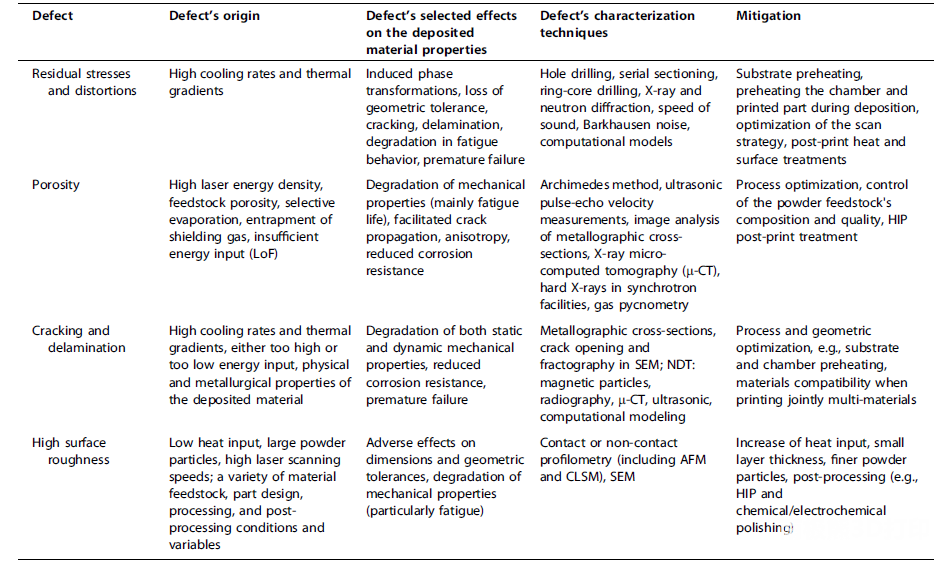
Residual Stress and Deformation
Sources of Residual Stress: All thermomechanical manufacturing processes inevitably lead to the formation of residual stress. Due to the layer-by-layer nature of the DED process, parts go through a very complex thermal history, including melting, remelting, and reheating. Figure 11a is a model for the formation of residual stress during heating and cooling cycles. Figure 11b shows the in-situ thermocouple readings during H13 steel box LENS deposition.Each peak represents when the laser passes through the thermocouple[57]thermocouple response. DED is a non-equilibrium processing technology with a rapid cooling rate of 102
0 Comments for “Directed Energy Deposition (DED) Additive Manufacturing: Physical Properties, Defects, Challenges and Applications (3)”