In recent years, continuous carbon fiber reinforced composite materials have been increasingly used in aircraft fuselages and other high-end industrial products due to their superior mechanical properties such as high specific strength and high specific stiffness.For composite parts with complex geometries, you can
FDM
In the process, fibers are laid according to performance requirements. However, in the FDM printing process, some defects may occur during the turning process of the nozzle pulling the fiber, including out-of-plane wrinkling, blistering, pulling-up and shearing effects. This further affects the mechanical properties of the parts.
In response to this problem, Haoqi Zhang and others from the University of Edinburgh in the United Kingdom studied the formation process of fiber misalignment and breakage of 1K continuous carbon fiber filaments during the FDM printing process by printing single stripes of continuous carbon fiber reinforced composite materials with different corners and curvatures. The formation process of defects was analyzed.
The single stripe printing effect of composite materials with different steering angles is shown in Figure 1. When the steering angle is 30°, the composite material filaments are flattened, and the actual steering angles of most continuous fibers are the same. When the turning angle increases to 60°, the fiber bundles begin to fold, and some of the continuous fibers are turned from the outer circumference to the inner circumference. As the printing turning angle continues to increase to 120°, obvious folds can be seen at the turning point of the printing filaments, and the average width of the filaments at the turning corners decreases, resulting in a larger fiber-free area. When the turning angles were 150° and 180°, the fibers were severely twisted and misaligned, and fiber breakage was observed. Therefore, in actual printing, the use of a printing path with a steering angle greater than 120° should be avoided as much as possible.
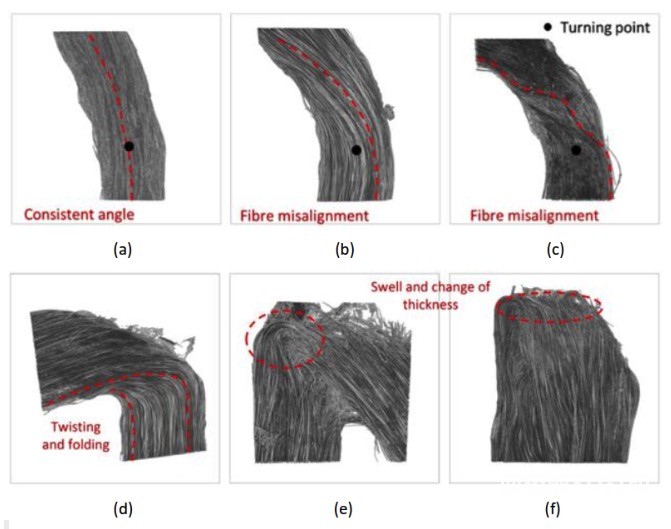
The single stripe printing effect of composite materials with different radii of curvature is shown in Figure 2. For a single stripe with a radius of curvature of 20mm, no obvious surface defects are observed, and the width of the single stripe is roughly the same along the printing direction. In the case of a diameter of 10 mm, the fibers on the inner circumference of the filament will be twisted and wrinkled. When it reaches 5mm, the frequency of these two kinds of defects is higher. In the case of a radius of curvature of 2.5mm, it is difficult to print a single stripe according to the designed path, and the phenomenon of fiber folding in which the inner and outer circumferences are completely transformed is observed. In addition, in the case of the radius of curvature of 5 and 2.5 mm, a small amount of fiber breaks. Therefore, in the actual printing process, the use of a printing path with a radius of curvature of less than 5mm should be avoided as much as possible.
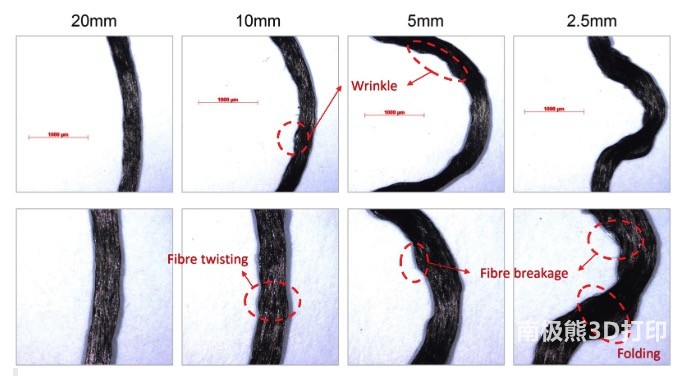
references:
H. Zhang, J. Chen, D. Yang, Fibre misalignment and breakage in 3D printing of continuous carbon fibre reinforced thermoplastic composites, Additive Manufacturing 38 (2021).
(Editor in charge: admin)
0 Comments for “Dislocation and fracture of fibers in 3D printed continuous carbon fiber reinforced thermoplastic composites”