According to foreign media reports, leading3D printingcompany
ExOne
Cooperated with the start-up company Maxxwell Motors to develop a unique copper electronic winding design for the axial flux motor. This motor can be used in electric vehicles and a range of heavy vehicles and industrial equipment.
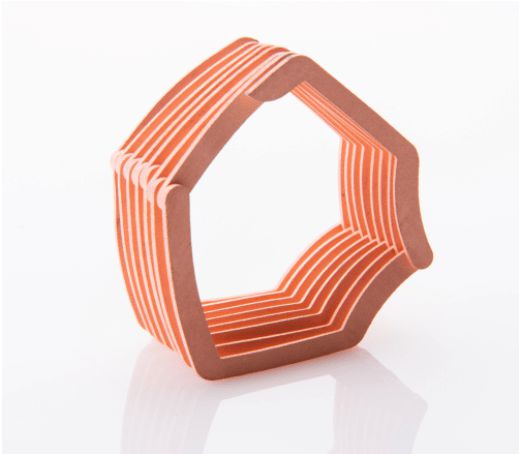
The two companies have adopted binder jet3D printing, Successfully designed high-efficiency copper electronic windings for motors without rare earth magnets. This new method can save time and cost while improving product performance.
Maxxwell was established in 2018 with a vision to improve motor design and manufacturing processes without using rare earth magnets. At present, the company has 9 US and global patents, and has launched two products, one is a 10kW air-cooled electric generator, and the other is a 150 kW liquid-cooled motor.
Optimizing the copper windings and rotors in the motors can promote the transition of the automotive industry to hybrid and pure electric vehicles. However, the current winding manufacturing method has high cost and low efficiency, and its performance is also affected by limited design approaches. ExOne and Maxxwell have successfully demonstrated binder jetting3D printingNew concept. This efficient copper design can eliminate many challenges brought about by traditional manufacturing methods. Currently, in-depth development and testing are underway.
Maxxwell’s ultimate goal is to spray3D printingManufacture complete winding parts, eliminating the need to wind, bend, process and weld individual parts.
Spray through adhesive3D printing, Can reduce the manufacturing steps and energy consumption of the final part, and produce less waste. This makes the components more efficient and can provide better performance. More importantly, the cost of high-speed adhesive injection is relatively low.
(Editor in charge: admin)
0 Comments for “ExOne and Maxxwell Motors collaborate to develop 3D printed copper windings”