Sierra Turbines is a small defense contractor from California that designs innovative, compact, and efficient turbines for use in large commercial and military jets. Recently, Antarctic Bear was informed that the company used NextFlex’s flexible hybrid electronic circuit (FHE)3D printingTechnology has developed a turbine engine with several designs and innovations, such as proprietary electronic control systems, engine health monitoring, and precise thermodynamic flow in compression and combustion, the assembly of features that make turbine engines excel in reliability .
The new technology in Sierra Turbines’ new turbo engine comes from NextFlex, a US-based flexible hybrid electronics (FHE) manufacturing institute. Formed in August 2015 by the DoD and the FlexTech Alliance, the organization includes companies, academic institutions, nonprofits, and state agencies with the common goal of advancing FHE manufacturing in the United States. Nextflex’s research focuses on
medical
, robotics, and communications markets to design a new lightweight, low-cost, stretchable FHE device. By adding electronics to new materials and creating compliant products, the organization aims to achieve “everything electronic” status, which aims to apply FHE to all aspects of everyday life.
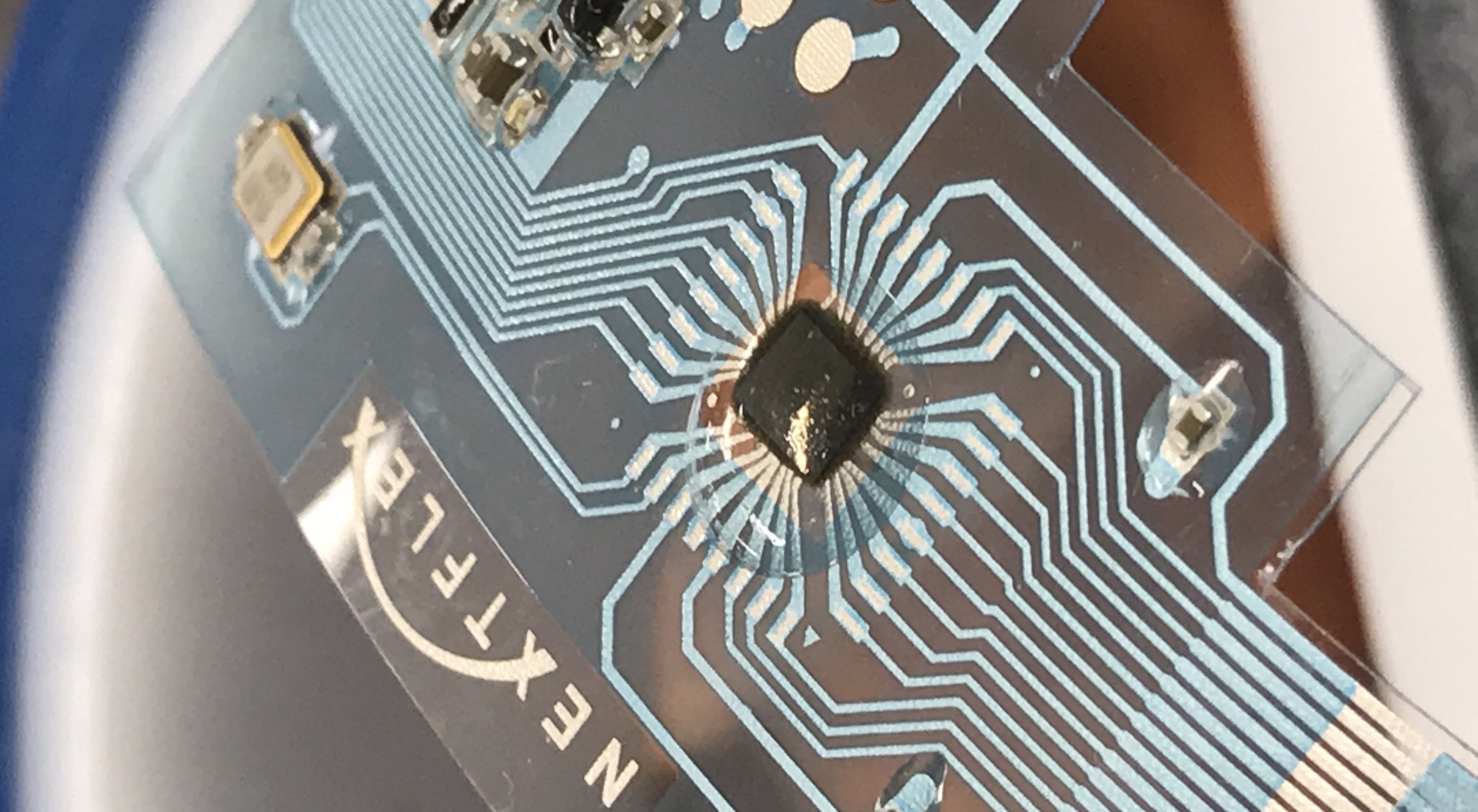
In the latest study, Sierra Turbines used NASA’s Langley Research Center’s SansEC sensing system on a turbine engine. SansEC is an open circuit resonant sensor that requires no electrical connection (hence the name SansEC or “no electrical connection”). The sensor structure consists of an array of conductive Archimedes spiral shapes printed on a flexible substrate. NextFlex fabricated these samples by writing silver conductive traces directly onto a flexible substrate. Given SierraTurbines’ equipment requirements and technology center capabilities, NextFlex developed the SansEC sensor’s mode, process, and materials as well as fabricated prototype proof-of-concept samples. In turn, SierraTurbines were assessed for purpose and application. NextFlex has further developed another mode, tuned for specific Sierra Turbine applications.
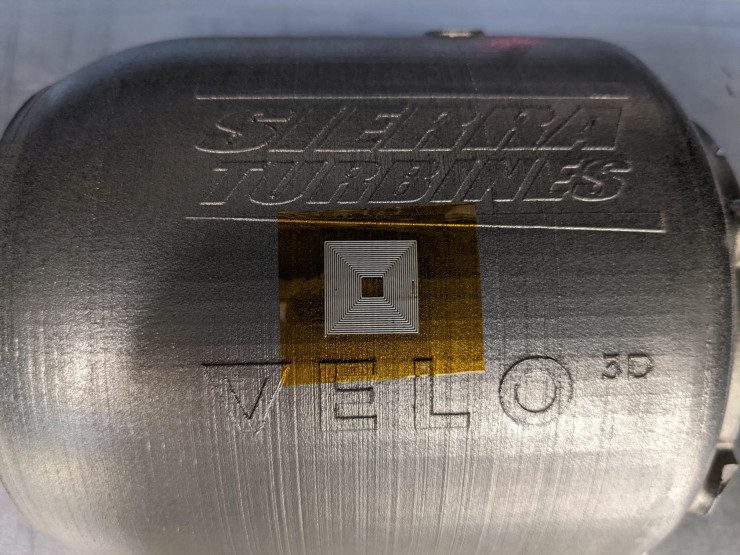
A successful demonstration of the SansEC device fabricated by FHE demonstrates the ability to fabricate electronic structures using an advanced additive manufacturing process. The special electronic structure SansEC can simultaneously measure different physical phenomena – such as temperature, liquid level, rotational speed or wear – and function properly even when severely damaged. Previous SansEC sensor variants were fabricated using traditional subtractive manufacturing methods and thus did not have the reduced SWaP (size, weight and power) properties inherent in FHE devices. By demonstrating that FHE tools and processes can be applied to this particular electronic structure, Sierra Turbines is now positioned within the FHE ecosystem and supply chain.
In addition to nurturing the workforce of the future and promoting a sustainable advanced manufacturing ecosystem, NextFlex is focused on accelerating innovation and commercialization of flexible electronics technologies through pre-competitive partnerships. Through a series of calls for projects, the agency provides cash incentives to proposal teams for tough flexible hybrid electronics (FHE) manufacturing projects, with NextFlex covering up to 50% of the development costs of the selected projects.The call for projects follows a structured selection process and a rigorous monitoring approach to ensure that all
funding
Diversity and breadth of project options.
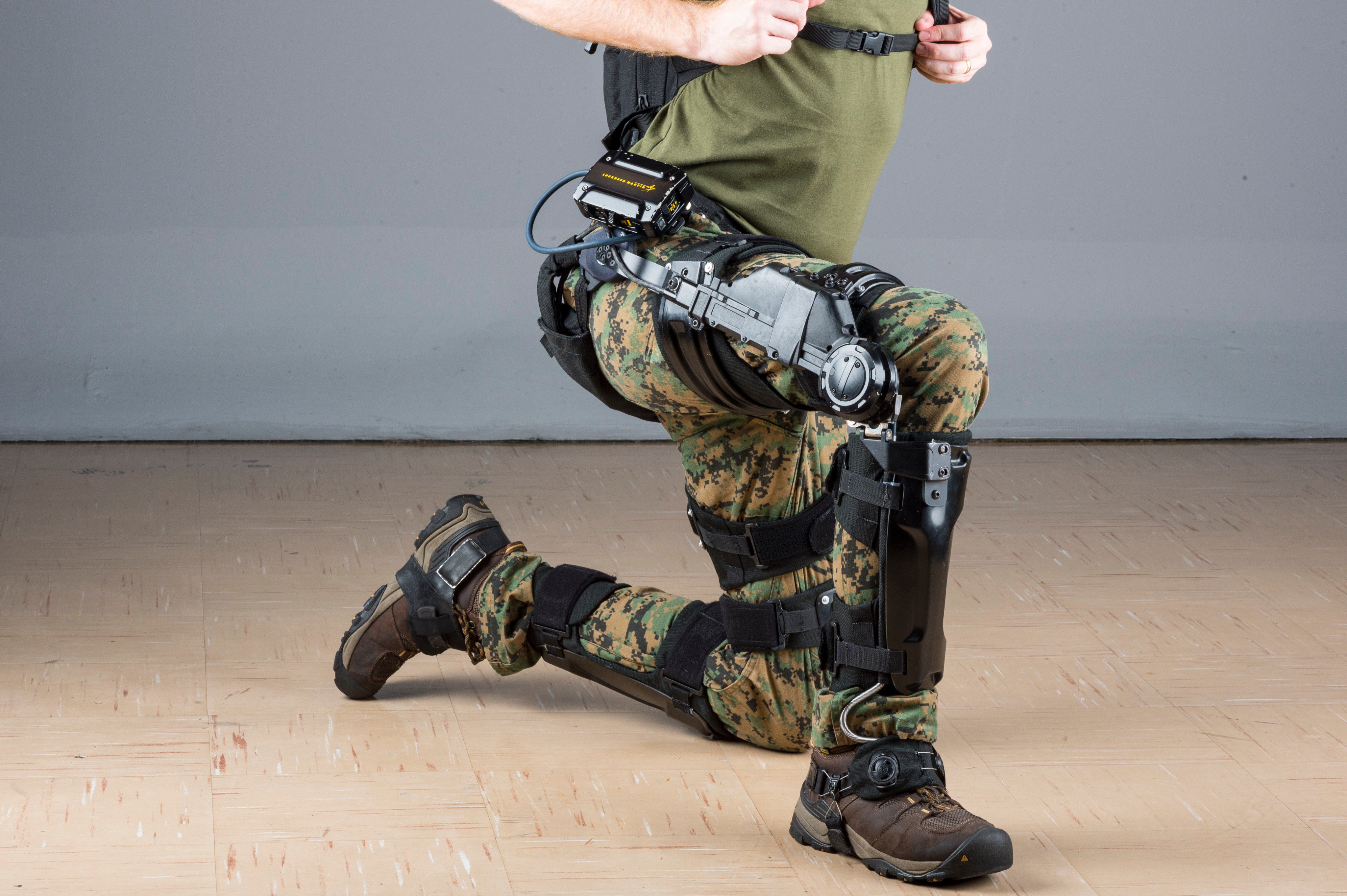
(responsible editor: admin)
0 Comments for “Flexible hybrid electronics 3D printing, NextFlex provides new ideas for turbine engine precision sensor manufacturing”