May 9, 2022, recently GE Renewable (GE Renewable
energy
company) declared to be COBOD
invest
people, to this Danish
architecture
3D printingThe startup injected an undisclosed amount of funding. The exact content of the investment is unclear, though both companies note that the funds will be used to build on their existing partnership.
The two companies have been working together since 2019, and last month, GE Renewable opened the world’s largest additive manufacturing (AC) research facility, installing the world’s largest concrete3D printingmachine, specially designed by COBOD for GE.
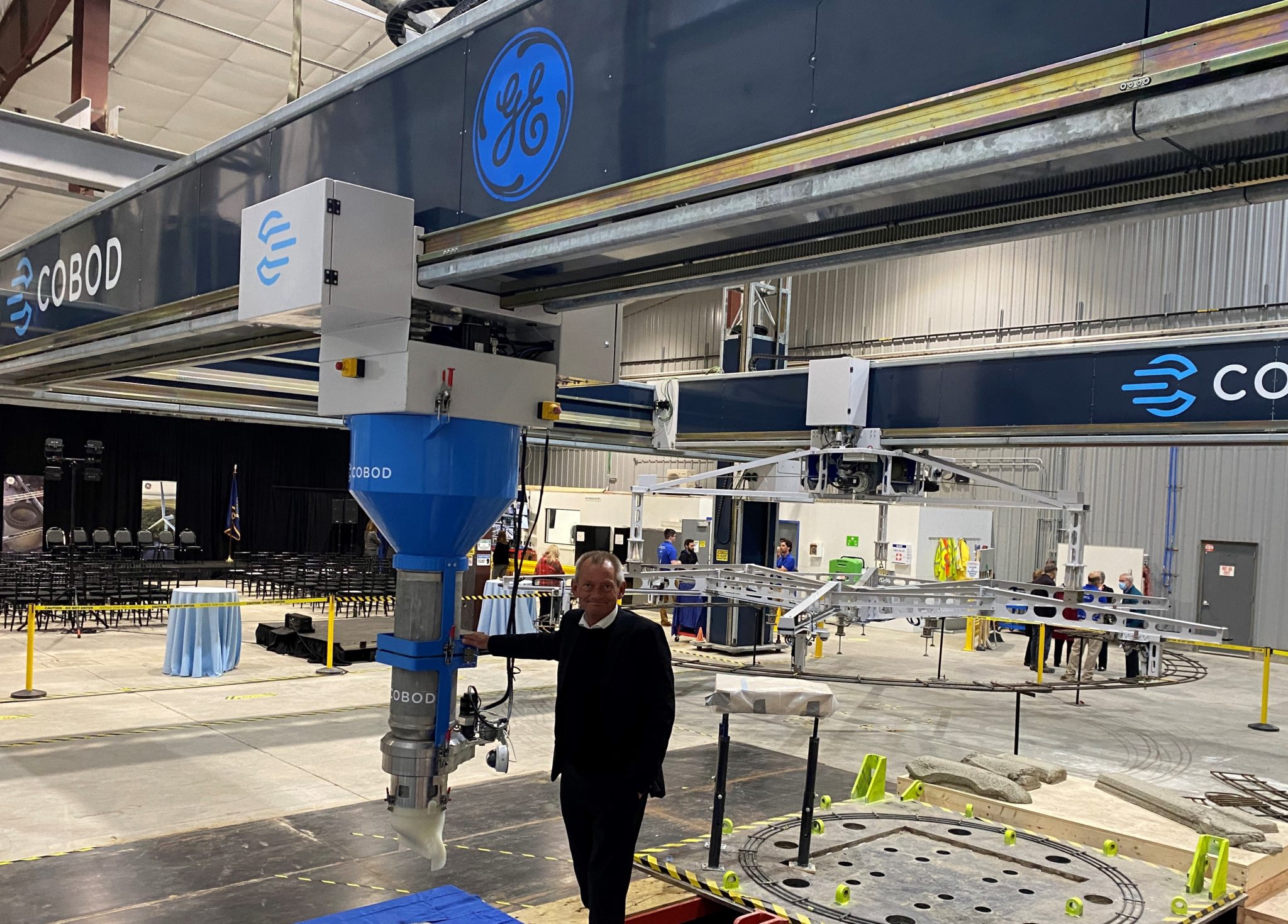
In a press release, COBOD founder and general manager Henrik Lund-Nielsen said: “I am very proud that a world-class company like GE is willing to partner with COBOD to help us deliver the automated building solutions of the future. Since 2019 Since we started working with GE, our R&D capabilities, engineering and industrial skills have grown significantly as a direct result of our collaboration, and we look forward to continuing to benefit from GE’s vast resources.”
The collaboration between the two companies has so far focused on 3D-printed bases for wind turbines, but COBOD notes that this is far from the only non-residential, low-rise application of the technology. COBOD has already printed office buildings in Denmark and Austria, schools in Africa, and structures in the oil and gas industry. This suggests that wind turbines may be just the beginning of a partnership between COBOD and GE Renewable, especially given the diversity of GE Renewable’s parent company’s businesses.
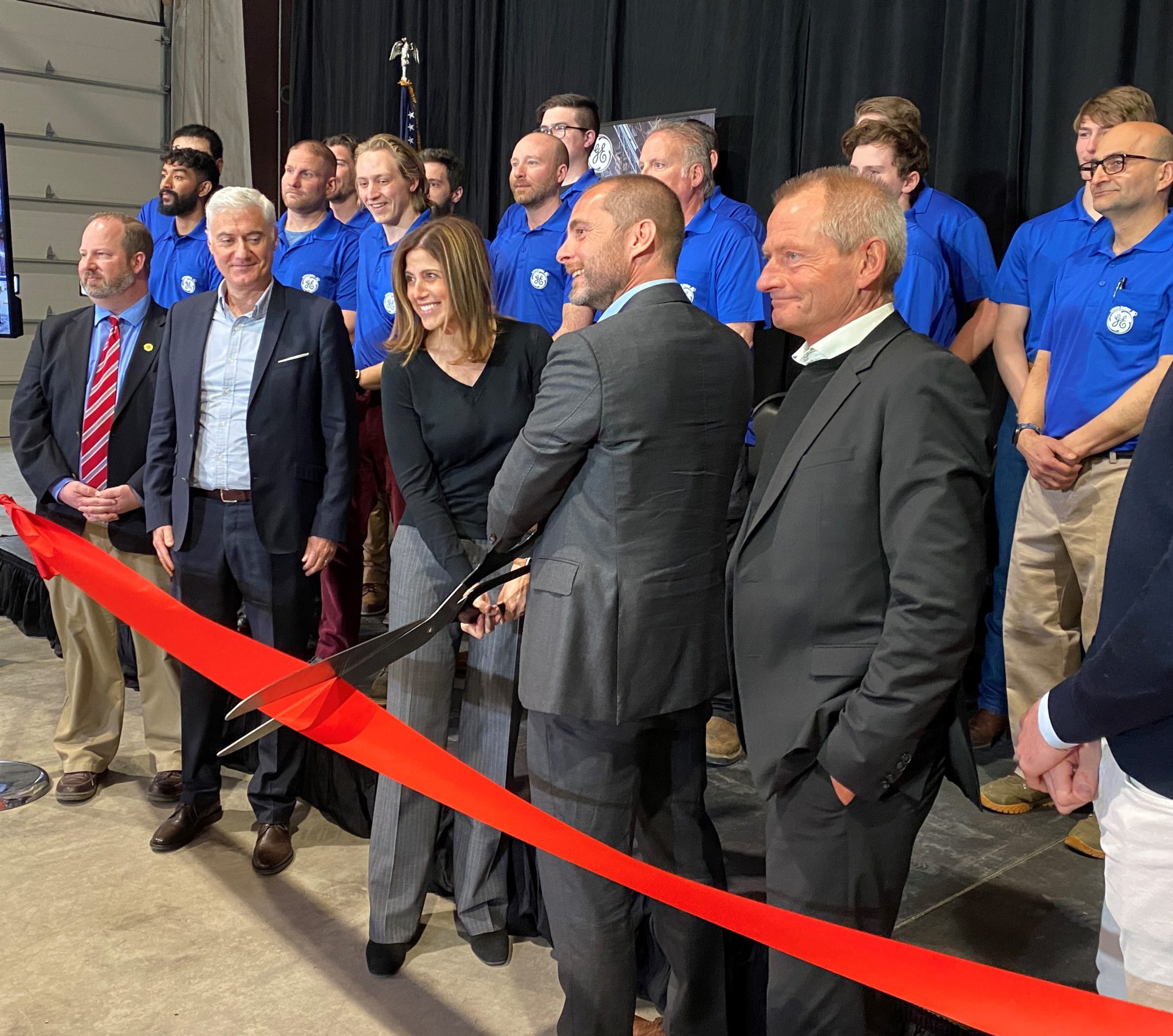
COBOD focuses on many different applications of concrete 3D printing: not only residential, but also apartment buildings and schools; not only renewable energy, but more sustainable solutions for the oil and gas industry. GE’s investment will further enhance the versatility of COBOD, opening up new possibilities for concrete 3D printing.
Furthermore, GE Renewable’s investment isn’t just a positive sign for COBOD: it’s a positive sign for the entire field, meaning money is flowing into the field of concrete 3D printing.
3D printing has strong application potential in the field of wind power generation
On April 23, 2022, Antarctic bears were informed that based on the
aviation
Rich experience in 3D printing of engine and gas turbine parts, Recycling under General Electric
energy
The company has started a new project to use a large concrete 3D machine to build the foundations of wind turbines, thereby reducing transportation and labor costs. According to estimates, by raising a 5MW wind turbine with a height of 80 meters to a height of 160 meters, the wind farm operator can increase the power generation by at least 30%.
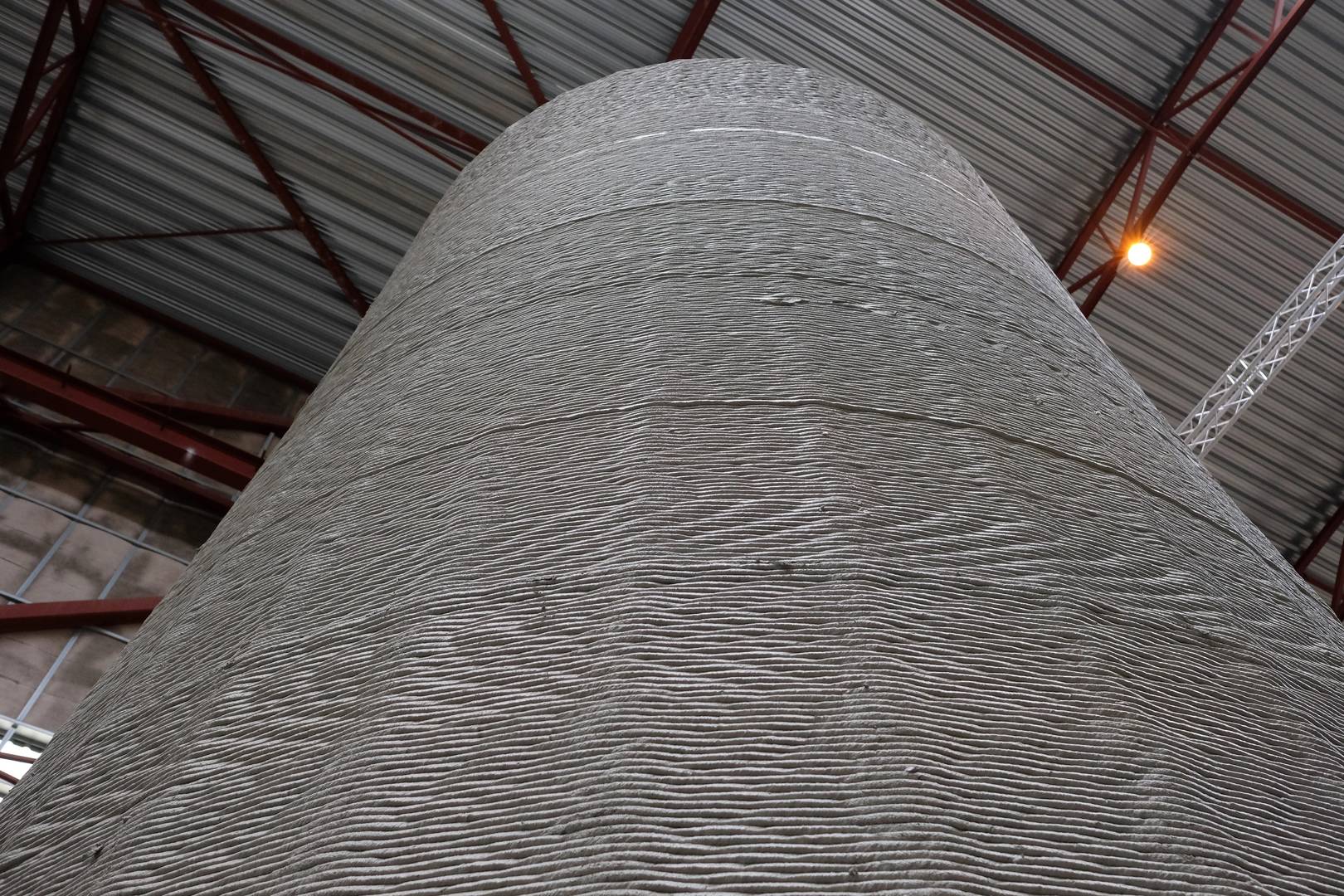
Wind energy is considered to be a clean and pollution-free renewable energy. As environmental problems such as global warming become more and more serious, wind power has become a key development project in some countries. In order to fully utilize wind energy, wind turbine generators are built relatively large. During construction, it is necessary to lay the foundation first, that is, to dig a deep enough pit, then build a steel structure in it, and finally pour concrete. The whole process requires a large number of workers to cooperate to complete.
The renewable energy company hopes to build the foundation by 3D printing concrete.Currently, they will use the existing concrete3D printing technologyBased on the optimization, the goal is to achieve commercialization within 5 years.
Renewable energy companies say that through 3D printing, the structure of current turbine wind turbines can be changed and innovations can be realized. Currently, the bases of wind turbines are level with the ground, on which large metal cylinders are built. The idea of Renewable Energy is to print not only the base, but also a portion of the tower body (the part that was originally a metal cylinder). This can reduce the transportation of large cylinders, save transportation costs, and reduce the difficulty of building wind turbines.
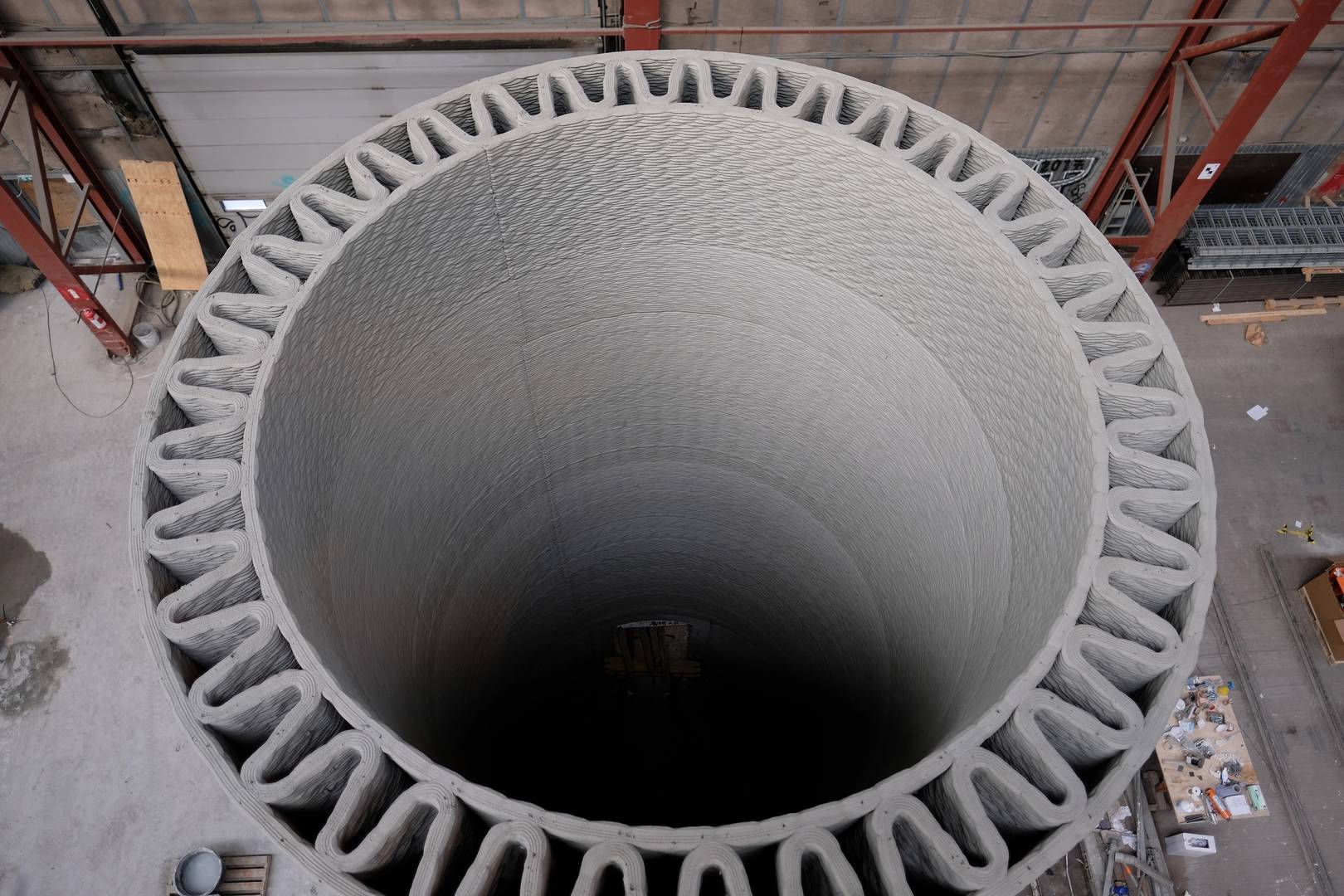
After making the fan higher, lighter is the next pursuit. More recently, GE has partnered with the U.S. Department of Energy to study the use of 3D printing to manufacture wind turbine blades.The 25-month, $6.7 million project will focus on how low-cost thermoplastic materials and3D printing technologyManufacture of the tip section of a set of fan blades. When complete, the GE team and its partners, Oak Ridge National Laboratory and the National Renewable Energy Laboratory, will test the product’s structural properties and install three sets of blade tips on the wind turbine.
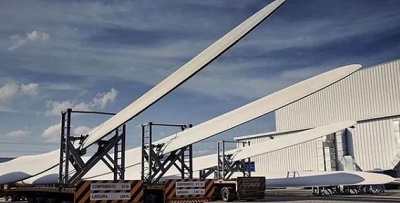
The blade tip is the most difficult part of the blade process. It is about 10 to 15 meters long, and its speed is about 85 m/s, which is close to 1/4 of the speed of sound, and can capture 40% of the energy required for the fan to rotate. The constant quest for technological innovation has led GE to seek ways to improve blade manufacturing, including combining 3D printing technology with advanced processes such as thermoforming, automation and thermoplastic materials.
Currently, wind turbine blades are mostly made of composite materials with epoxy or polyester resin added to glass fiber and carbon fiber, and the use of lightweight thermoplastic composites and 3D printed blades offers several advantages, including:
1) The light blade can drive the fan rotor to generate more power and increase the power generation of the fan;
2) Lightweight blades can reduce the load on the tower and axle, reduce the wear of gearbox, transmission system, bearing and base, thus reducing the whole life cycle cost;
3) Thermoplastic materials are more convenient for melting and recycling after dismantling.
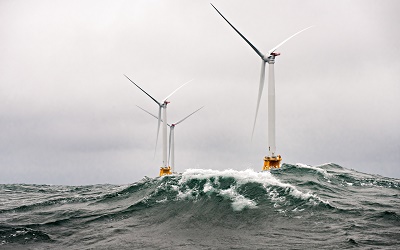
While the wind power industry is developing rapidly, many decommissioned blades end up in landfills, which also brings environmental problems that cannot be ignored. GE Renewable Energy previously signed a wind turbine blade recycling agreement with environmental services company Veolia. Veolia will recycle old wind turbine blades, shredding them, and then blending the glass fibers with ingredients such as balsa wood and transporting them to cement manufacturing plants to produce Portland cement as an alternative to coal, sand and clay. This approach can “turn” industrial waste into raw material for cement, and also helps reduce carbon dioxide emissions from the cement industry.
Cost savings can be achieved through the use of new materials and increased efficiency, while mass production can further help reduce costs. GE and its subsidiary Elm Wind Energy plan to bring the technology to market at scale.
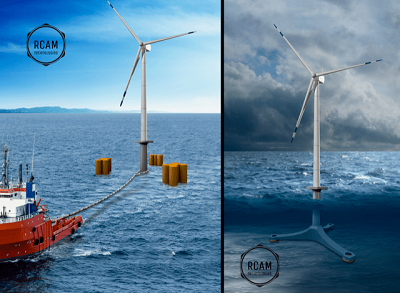
After the blade tip is complete, the GE team will then apply 3D printing technology to other parts of the fan blade. More than 20 years ago, GE started
aviation
Introducing lightweight composite fan blades into the engine. Today, through the joint efforts of our partners, we are applying more advanced material technology to wind turbine blades to reduce the cost of wind power, improve performance, and continue to promote the green and low-carbon development of the industry.
(responsible editor: admin)
0 Comments for “GE Wind Power invests in Danish architectural concrete 3D printing company COBOD”