Based on the early success and momentum of the Pacer Edge program, the U.S. Air Force and General Electric (GE) have entered the third phase of this metal additive manufacturing pathfinder program in November 2021. This stage will face the behemoth that the Air Force will continue to support under the “cold start”. Aircraft engine components that are considered “cold start” are those that require more than 300 days of procurement time. It is estimated that the US Air Force has more than 800 engines to “cold start” each year.
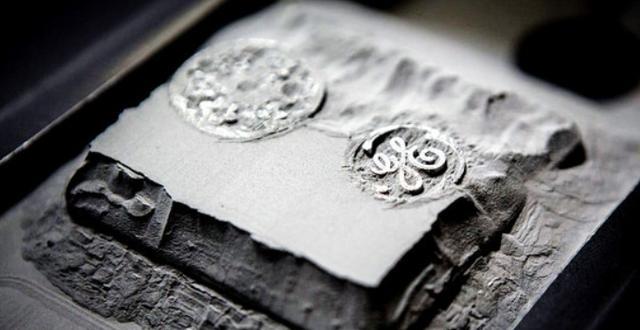
Seaworthy in less than a year3D printingMetalwork In June 2021, GE obtained the approval of the U.S. Air Force for the project change proposal (ECP) for the additively manufactured fuel tank bottom cover of the F110 engine. As the latest milestone of the “Front Runner” program, this component is the first engine component designed and produced using metal additive manufacturing and has passed the US Department of Defense’s physical airworthiness certification. Matt Zorwinsky, chief engineer of GE’s large military engineering team, said that the T25 sensor of the GE90 engine is GE’s role in commercial aviation.
aerospace
Like the Federal Aviation Administration (FAA) certified Pathfinder in the field of metal additive manufacturing components, the F110 engine fuel tank bottom cover has laid a solid foundation for GE’s airworthiness appraisal of more military additive manufacturing components.
U.S. Air Force official Nathan Parker stated that the plan is an important measure to reduce risks and demonstrate the application of additive manufacturing in the aerospace field. Additive manufacturing of aircraft engine components and military airworthiness are increasing. An important step in material manufacturing. US Air Force Advancement Director John Sneden said that the Chief of Staff of the Air Force issued a challenge to Air Force personnel, demanding “accelerate change, or fail.” The entire “Front Runner” program process is built around the concept of accelerated change. The development of the F110 engine fuel tank bottom cover and the execution speed of the airworthiness approval are a good proof. The program is demonstrating and proving that the capabilities will change military aircraft engines. The rules of the game for production and continuous support will solve many of the future air force’s combat readiness challenges.Spiral development based on experience and digital clues
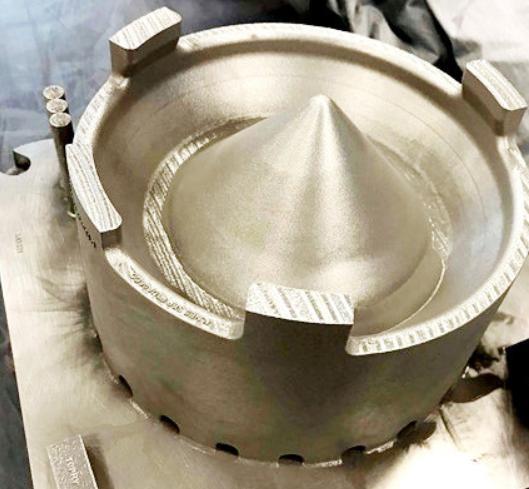
The airworthiness appraisal of the F110 engine fuel tank bottom cover brought the phase 1a of the plan to an end. The whole appraisal process was less than one year, but this is also the result of GE’s ten years of metal additive engineering and manufacturing expertise. The GE team is flying3D printingAn in-depth understanding of the airworthiness of commercial aircraft engines for metal components will help the Air Force establish its own strong military airworthiness process validation and certification process. Close collaboration and knowledge sharing have enhanced the Air Force’s spiral development approach, which is the continuous identification, reverse engineering, and development of technical data packages (TDP) for the increasingly complex and larger parts in metal additive manufacturing.
Matt pointed out that as part of its broader strategy for continued support and readiness, the U.S. Air Force’s strong vision for additive manufacturing enables the Air Force’s joint team to move forward quickly. They continue to share their own experience and develop an efficient and structured way of working-especially in the development of appraisal processes and accelerating design iterations. This lean operating efficiency has already promoted these results. Phase 1b of the plan includes the study of complex and large load-bearing structures, with a focus on additive manufacturing of the discontinued fuel tank sump cover for the TF34 engine, which has been in service for more than 40 years.
Lisa Koroya-Bokley, general manager of GE Advanced Materials Solutions, said that she is very happy to embark on this journey with the Air Force. The journey of additive manufacturing is great, but if you have a good itinerary and an experienced guide, so much the better. The company started with a relatively simple part, but a spiral development model is taking shape, which provides the focus for the team, and the company’s experts provide guidance and solve problems in the process.
GE’s experts also focus on digital twins, predictive analysis-based maintenance, and parts lifecycle management expertise, which can complement the U.S. Air Force’s digital engineering strategy and internal knowledge. Lisa said that interpersonal interaction and collaboration have added tremendous value to the company’s work, but digitalization is the enabler. Additive manufacturing is also a powerful digital technology, covering the entire process from design and modeling to in-situ monitoring to inspection and final quality level assurance. The addition of digital twins and predictive analysis at the top level brings new perspectives, such as on-site System management, diagnosis and maintenance of the system.
Tinker Air Force Base as airworthiness
Lauren Tussin, director of military projects at GE, the center of the metal additive supply chain, revealed that the follow-up phase of the “Front Runner” program involves the establishment of a metal additive manufacturing supply chain at Tinker Air Force Base in Oklahoma, capable of producing seaworthy products. Components to support the maintenance needs of the Department of Defense.Recently, the Air Force Advancement Agency
invest
US$10 million was allocated to provide funding for other phases of the plan. This funding will accelerate the development of additive manufacturing capabilities within the Air Force’s establishment, as well as the ability to design and print airworthy hardware for military engines, aircraft, and support equipment. The team implementing the plan is using 3D printing capabilities to alleviate the restrictions on spare parts that the old system is difficult to purchase and obsolete.
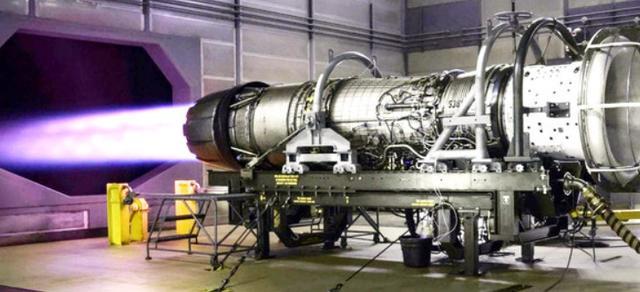
Melanie Jonathan, chief engineer of the U.S. Air Force’s Propulsion and Sustainability Department, believes that the F110 engine fuel tank bottom cover is a great pathfinder, allowing them to exercise the airworthiness of the U.S. Air Force.There are many parts in the aircraft queueMetal 3D printingThe ideal candidate. Next, it will focus on optimizing the airworthiness process, so it is as responsive as technology. Beth Dittmer, Director of Propulsion and Integration at Tinker Air Force Base, said that the plan is accelerating the Air Force’s widespread adoption of 3D metal printing to systematically solve supply chain shortages and fulfill its promise by drastically shortening deliveries. Time and create additional procurement options to improve support for combat personnel.
“Front-runner” plan to reach
The next milestone, Alexa, project manager of GE Additive’s “Front Runner” program, said that for the Air Force and GE teams, the first task is to create a digital 3D technology data package (TDP) for difficult-to-procure, outdated “Cold start” parts of the company, and provide four seaworthy, near-net-shape castings. These data packages will eventually mean that obsolete parts will become a thing of the past. In the next few years, the team plans to create at least five data packets on the Air Force’s continuous support platform, and the technical complexity continues to increase.
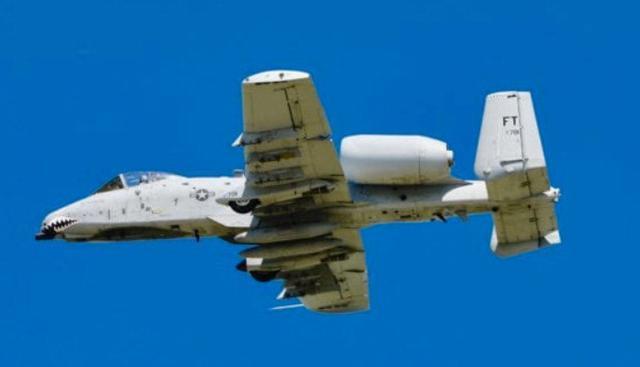
In Phase 3, the team has successfully printed two components, a crank and a horizontal arm, using cobalt-chromium alloys on the M2 series of the Concept Laser Company at GE Additives’ plant in Cincinnati, Ohio. Work on other components using alloy 718 has also progressed. The goal of the plan is to establish organizational capabilities at Tinker Air Force Base. The way to achieve this goal is to ensure that the intellectual property rights generated in the program are owned by the US government. This will enable the US Air Force and the Department of Defense to print these parts themselves in the future. The plan is still going on as planned, and the goal is to deliver airworthy production castings to the U.S. Air Force in the spring of 2022.
Zach Miller, director of the Advanced Manufacturing Program Office of the Air Force’s Office of Rapid Sustainability, said that the cooperation between GE and the Air Force has legalized the use of additive manufacturing to meet the critical needs of older aircraft that are currently not supported in the existing supply chain. Joe Franzen, GE Additive’s technical account manager, said that while creating the 3D data package, the company is working closely with Air Force counterparts to transfer production capacity to the maintenance depot at Tinker Air Force Base.This will establish the U.S. Air Force into an organizational and airworthyMetal 3D printingability.
(Editor in charge: admin)
0 Comments for “General Electric helps the U.S. Air Force form metal 3D printing capabilities”