On April 1, 2020, it was learned from foreign media that GKN Additive3D printingA hydraulic adapter block is redesigned, and its weight is 80% lighter than similar products manufactured by traditional manufacturers. The UK-based technology group uses Design for Additive Manufacturing (DfAM) principles to reduce the amount of material used, thereby reducing weight and cost, while also improving functionality.
As can be seen from the comparison chart below, they have done a lot of optimized design on the adapter block, reducing the weight from 30 kg to 5.5 kg, which greatly saves raw materials.
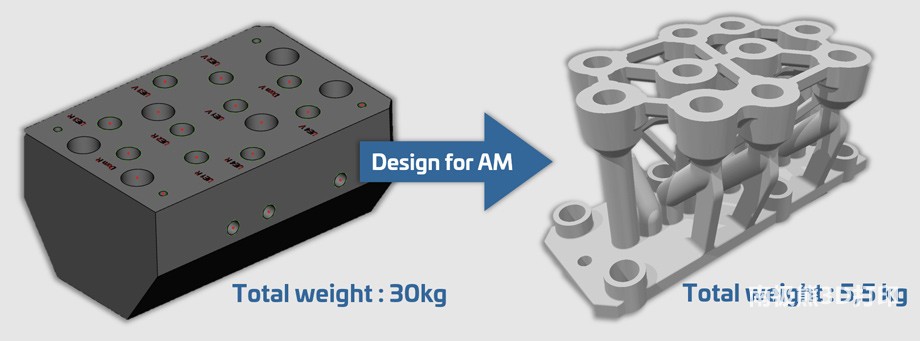
Traditionally manufactured hydraulic block
Hydraulic blocks often have a compact, block-shaped design, and a set of internal passages are drilled in it. Internal channels control the distribution of oil in the hydraulic system, allowing operators to control heavy machinery, such as the arms of cranes or excavators. First, drill holes from above and below. The vertical holes are then connected by horizontal channels and threads are cut into them. To prevent oil from leaking from the open horizontal channel, plug and seal it with grub screws.
The machining efficiency of these adapter blocks is extremely low, both in terms of cost and functionality. The edges of drilling and milling will produce sharp burrs, which are difficult to deal with in post-processing. These sometimes break during operation and cause system failure. In addition, sharp junctions generate turbulence, resulting in low energy efficiency. Dirt reservoirs can accumulate in unused horizontal channels, thereby shortening the service life of the hydraulic system.
Redesign the hydraulic block
GKN’s DfAM redesign takes advantage of one of the main advantages of additive manufacturing: complete design freedom. The weight of the project was reduced by 80%, from 30 kg to 5.5 kg, without sacrificing any functionality. The new design discards a lot of excess material and ensures that there are no overlapping holes in the part. Unused horizontal channels are completely omitted, so there is nowhere to accumulate dust. The sharp inner corners are replaced by smooth pipelines, which greatly reduces turbulence in the system.
In addition, if any modifications are to be made to the design, the additive manufacturing process will easily achieve this goal. CAD software can be used for rapid design iterations, which is the opposite of producing brand new tools to change the drilling position.
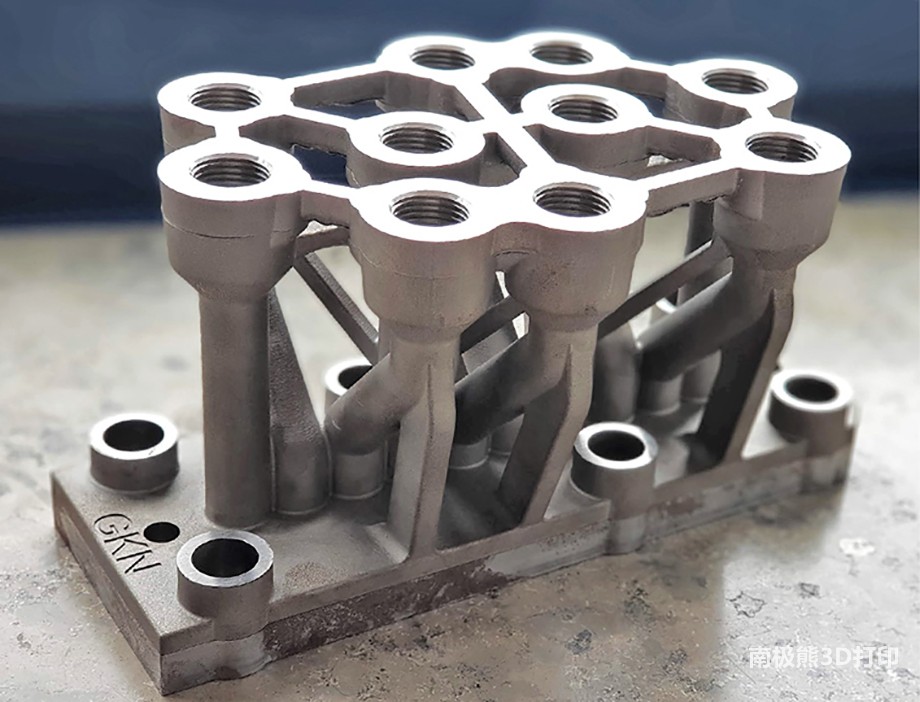
Compiled from: 3dprintingindustry
(Editor in charge: admin)
0 Comments for “GKN Additive redesigned the additive manufacturing hydraulic block, reducing weight by 80%”