Global energy services company Shawcor uses Markforged Mark Two in the production process of its new project 3D printingmachine.by using3D printing, Shawcor can shorten the turnaround time required to produce parts and reduce costs.Therefore, the company stated that by adopting3D printingInstead of traditional supplies, it saved 1.6 million Canadian dollars (approximately 1.2 million US dollars).
The project mainly develops tools and fixtures for picking and placing machines. Shawcor’s senior mechanical designer Phil Minors (Phil Minors) said, “If there is no grinding machine to deal with the machine, Shawcor will lose approximately 1.6 million Canadian dollars in a year.”
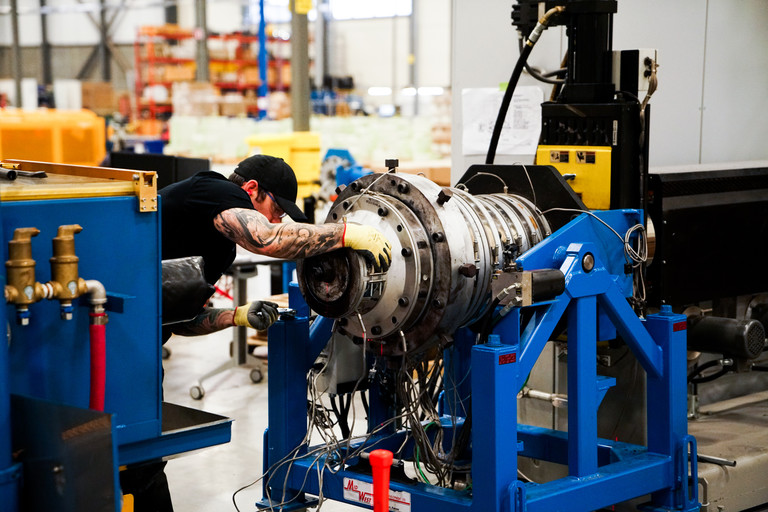
Continuous carbon fiber3D printingReduced the cost of Shawcor
Shawcor specializes in providing products and services to the pipeline and pipeline services sector in the oil and gas, petrochemical and industrial markets. Through its proprietary products, Shawcor aims to help maintain the smooth operation of construction projects, namely maintaining connection systems, pipeline coatings, integrity management and oilfield solutions.
One of the company’s most recent projects was handled by Shawcor’s Composite Production Systems department, which required moving objects weighing between 115 and 230 pounds. For one person, loading and unloading are too heavy, and the team needs a customized machine to handle it.
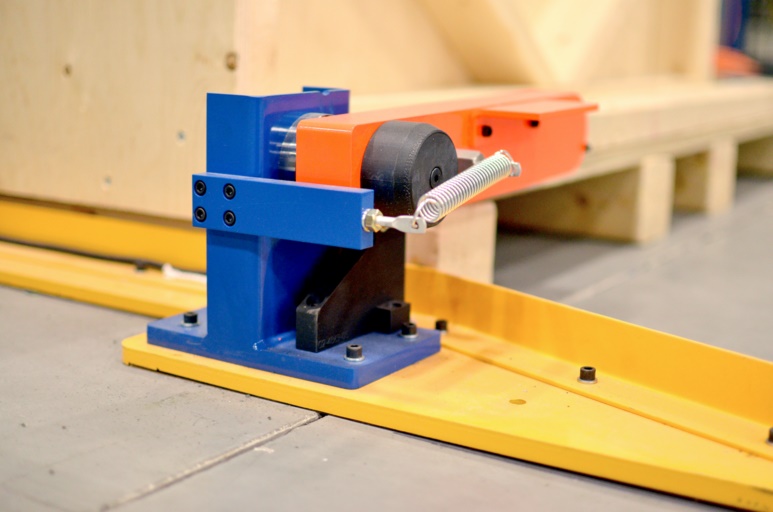
In order to overcome the cost barrier of the development of this machine, Shawcor adopted Markforged Mark Two, a continuous carbon fiber3D printingmachine.
Using this system, Shawcor is able to produce the customized parts needed to manufacture the machine, by replacing aluminum and metal plates with3D printingParts, saving 27,000 Canadian dollars in the process.
Shawcor used Markforged technology to perform a total of 53 unique parts3D printing, 45% of which are reinforced with Kevlar, HSHT glass fiber or carbon fiber to improve rigidity and service life.
Minors added: “We have completely eliminated the three to six weeks of conversion time required to replace parts.”
After this initial project, Mark Two is now used by the team for prototyping, testing and iterating new designs.
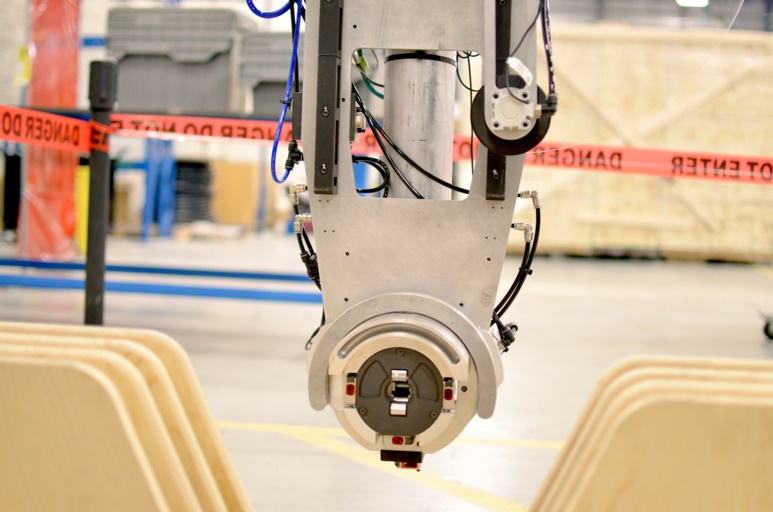
(Editor in charge: admin)
0 Comments for “Global energy services company Shawcor uses 3D printed carbon fiber parts to replace metal parts”