Introduction: Polymer foam materials have a wide range of applications in production and life, and are a large class of important porous materials. At present, polymer foam is mainly prepared by using foaming agent to directly expand and foam inside the resin, just like making bread. First, yeast and flour are mixed and kneaded to form a dough. The CO2 produced by the yeast expands under the action of heat to make it solid. The dough becomes fluffy. However, the inevitable and difficult-to-control cell nucleation, merging, rupture and other factors in this process will cause greater damage to the structure and morphology of the cell, which will affect the performance, how to precisely control the microscopic cell shape The appearance and macro-foam structure are still a difficult point.
Combined with computer program-assisted additive manufacturing technology (3D printing) In recent years, it has developed rapidly. Compared with traditional molding technology, its biggest advantage is that it can accurately and rapidly shape three-dimensional complex structures as small as micro-nano size.In order to solve some of the problems in the process of preparing polymer foams by direct expansion foaming, Dr. Claas Willem Visser (corresponding author) and Professor Jennifer A. Lewis (co-corresponding author) from Harvard University in the United States will3D printingThe technology was applied to the preparation of polymer foams, and for the first time, a directly writeable polymer (polyethylene glycol diacrylate) bubble “ink” was developed, and microscopic cells were prepared by a combination of direct writing and UV curing. The shape, distribution and macroscopic foam structure are precisely adjustable polymer foam, and by changing the composition of the bubble “ink”, it can also give the foam new functions. The research results were published in “Advanced Materials” as a paper entitled “Architected Polymer Foams via Direct Bubble Writing” (see the original link after the article).
Principle of preparing foam by direct writing method
In order to realize that the “ink” for direct writing is a single microscopic bubble that forms a macroscopic bubble, as shown in Figure 1, the researchers designed a special nozzle with an inner and outer double-layer structure: the inner tube contains polymer monomers, initiators and surface activity. The polymer precursor solution of the agent, the outer tube conveys the gas, and the two are mixed at the nozzle mouth to form a writable bubble “ink”. A single bubble drops from the nozzle to the substrate and accumulates. After UV-initiated polymerization, the bubbles are bonded Form a macroscopic foam block. Among them, the “ink” dripping flow rate and gas pressure are the keys to preparing foams with different microscopic cell morphologies: Based on theoretical calculations and experimental results, the author draws a phase diagram of the influence of the precursor liquid flow rate and pressure on the bubble “ink” morphology. In the follow-up study, the author chose a constant rate of liquid flow Q = 10 mL min−1, and studied the influence of parameters such as liquid composition, gas composition and pressure, and nozzle movement rate on the micro and macro structure of the foam.
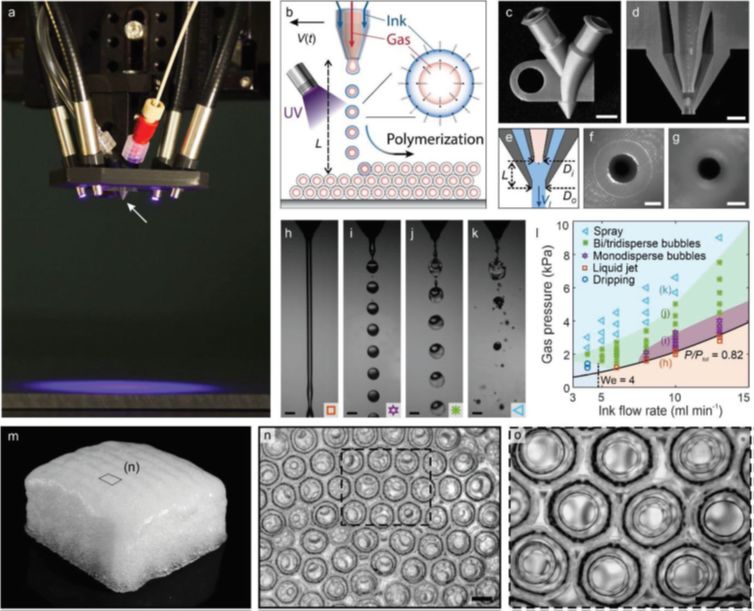
Compared with the traditional foam preparation method, the direct writing method has the following 4 advantages:
Advantage 1: Controllable cell morphology and distribution
Most of the properties of foam are directly related to the morphology of the cells. Precisely formulating the morphology of the cells and preparing foams with excellent properties are the biggest innovations of the direct writing foaming method. The cell morphology mainly includes three elements: open/closed cell structure, pore size and distribution. The author controls the open and closed cell structure by the type of gas: when O2 with polymerization inhibitory effect is used as the gas, the monomers that are in contact with the O2 surface and the depth is within the range of about 40um can stop or delay the polymerization, so that the bubble wall becomes thinner. Eventually it becomes an open-cell foam; when inert N2 is used as a gas source, polymerization occurs normally, and the foam wall is thicker to form a closed-cell foam. The pore size and distribution are adjusted by air pressure. Lower air pressure will produce monodisperse (2 ≤ P ≤2.7 kPa) bubble “ink”. The resulting pore diameter is approximately 0.5 mm and the distribution is very uniform; when the air pressure increases, The bubbles become double-dispersed (2.8 ≤ P ≤ 3.4 kPa) or even tri-dispersed (P > 3.6 kPa), and the resulting pore diameters are between 0.3-0.7 mm and the distribution is wider.
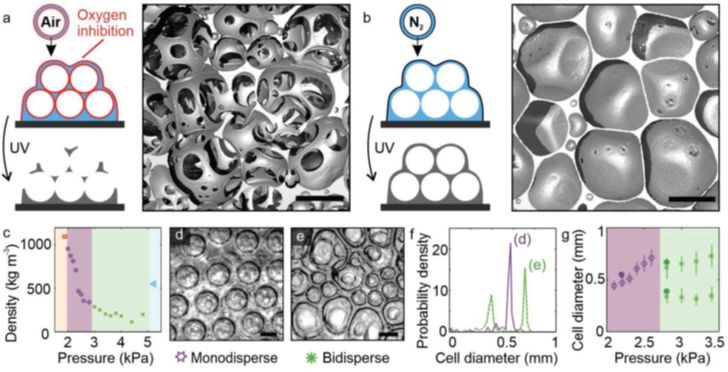
Advantage 2: Preparation of multi-layer structure foam
Changing the space position of the nozzle and the size of the air pressure while writing the nozzle can prepare multi-layer structure materials with different 3D structures, such as the triangular grid in Figure 3. By increasing the air pressure or slowing down the movement speed of the nozzle, the single element of the grid will become wider, and vice versa.
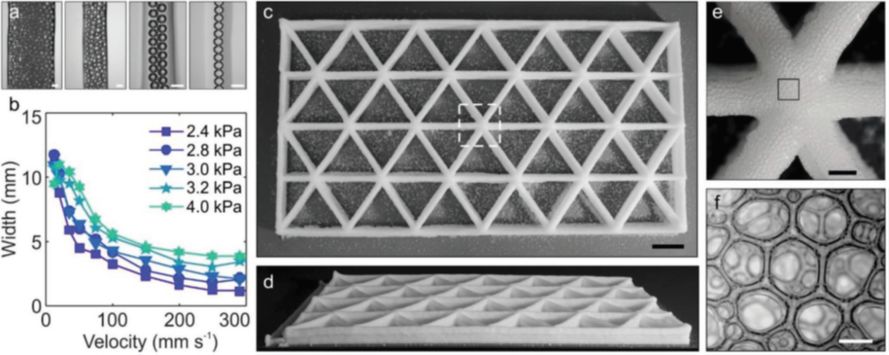
Advantage 3: Preparation of mechanical properties gradient foam derived from structural gradient
During the continuous writing process, the process parameters were adjusted intermittently to change the density and modulus between the local foams, so that the final foam showed a gradient of several orders of magnitude in the overall mechanical properties, realizing the same as a pile of wood. Several different small component structures are combined into a large macroscopic body. Foams of this structure are difficult to obtain by conventional foaming methods.
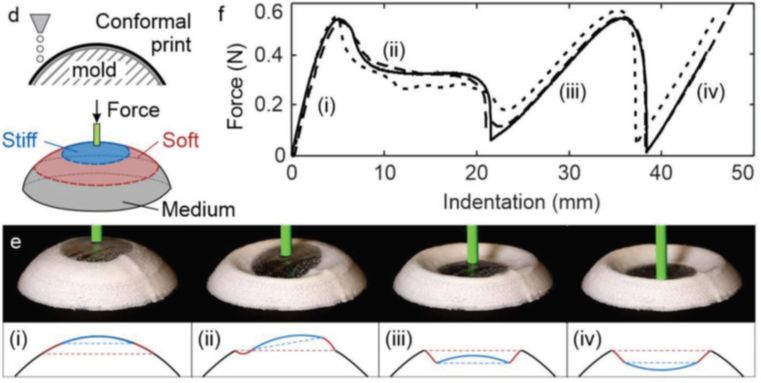
Advantage 4: Preparation of functionalized foam
Changing the composition of the precursor solution, such as adding a certain functional substance, can give the foam new functions when the substance remains after the foam is formed. For example, the author adds AgNO3 to the precursor solution in advance, and after curing, it turns into a flexible foam containing nano-silver. The resistance becomes smaller during compression, and it has a good linear relationship to pressure and high sensitivity. It is expected to be used for pressure. sensor.
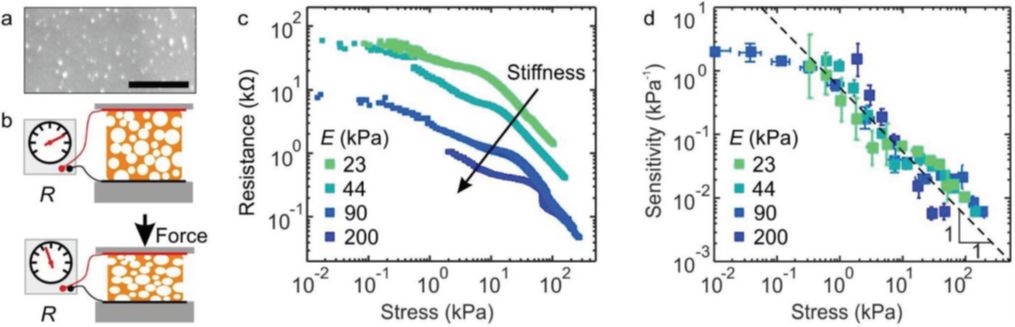
Summarize
The research results show that the direct writing method can accurately control the microscopic cell morphology and the macroscopic foam structure, program the mechanical properties of the foam, and can conveniently give the foam new functions, which will improve the foam preparation methods in the future. Active promotion.
(Editor in charge: admin)
0 Comments for “Harvard University: 3D printing technology quietly breaks into foam materials”