Introduction: This article reports a new type of aluminum-lithium alloy specially developed for LPBF technology. The method of laser glazing on castings is suitable for the approximate solidification conditions of LPBF. Five Al-Cu-Li ingots with different Sc and Zr content were developed, and optimized chemical composition was obtained and converted into Al-Cu-Li-Sc-Zr powder. This newly developed Al-Cu-Li-Sc-Zr alloy is successfully processed by LPBF, with high build rate and low Li loss rate. This new alloy shows excellent tensile properties, including a yield strength of 482 ± 1 MPa, an ultimate tensile strength of 539 ± 1 MPa, and an elongation of 8.8 ± 0.7%.
In recent years, the laser powder bed fusion (LPBF) of aluminum alloys has developed rapidly. Previous research has focused on cast and forged aluminum alloys originally designed for traditional processes. The most widely studied aluminum alloy in LPBF is Al-Si cast aluminum alloy, of which AlSi10Mg has attracted the most attention. Due to the narrow solidification range and low shrinkage rate, these Al-Si cast aluminum alloys have good LPBF processing properties.forcarwithaviationaerospaceForged aluminum alloys commonly used in the industry, such as 2xxx, 5xxx, 6xxx and 7xxx series alloys, attempts to LPBF these alloys usually result in hot cracking during processing.
Traditional alloys designed for casting and forging processes cannot take full advantage of the potential benefits of LPBF’s high solidification rate. Therefore, the research focus of LPBF aluminum alloy is gradually shifting from the processing attempts of mature cast and forged aluminum alloys to the development of new aluminum alloy systems to adapt to the unique thermomechanical conditions in the LPBF process. The first commercial aluminum alloy specifically designed for LPBF may be Al-4.60Mg-0.66Sc-0.42Zr-0.49Mn, weight percentage. Scalmalloy alloy subjected to LPBF has the characteristics of fine grains and high tensile properties[TheLPBFprocessingresultsofthesecommercialalloyspointtotheimportanceofgrainrefinementtosolvethecrackingproblemItisworthnotingthatthecontentofinoculationelementsincludingScandZrismuchhigherthanthatoftraditionalcastandforgedaluminumalloys
The main challenge in developing alloys for LPBF is the high cost of producing alloy powders with various compositions, and LPBF processing experiments on these powders are very time-consuming.A commonly used method is to combine the existing malleableAluminum alloy powderIt is not mixed with inoculation powder, such as 2024+Zr, 2024+Ti, 7075+Si and 7075+ZrH 2. By controlling the amount of inoculation powder, it is convenient to adjust the composition of the mixed powder. However, the melting points of Si, Zr and Ti are 1414℃, 1852℃ and 1668℃, respectively, which are much higher than the melting point of aluminum alloy (463℃~671℃). The large difference in melting point may cause uneven melting of the mixed powder. Another method is to use the laser of the LPBF machine to melt an ingot with a design composition to approximate the solidification conditions of LPBF. This method is used to evaluate the microstructure and cracking of Al-Sc-Zr, Al-Er-Zr, Al-Ce, Al-Co and Al-Mn-Sc.
Due to its low density, good corrosion resistance, strength and toughness, aluminum-lithium alloys have gradually replaced traditional aluminum alloys in the aerospace industry. LPBF provides an effective method for manufacturing lightweight structures. Therefore, the application of aluminum-lithium alloy to LPBF has broad application prospects for further reducing the weight of aerospace structures.
Here, the team of Professor Zhu Haihong of Huazhong University of Science and Technology used casting and laser glazing methods to simulate the solidification conditions of LPBF. Five Al-Li alloys with different Sc and Zr contents were developed and converted into ingots, aiming to solve the high crack sensitivity and relatively high lithium loss rate of the aluminum-lithium alloy produced by LPBF. The newly developed Al-Cu-Li-Sc-Zr alloy was successfully produced by LPBF, which has both high strength and good ductility. Compared with the traditional 2195 aluminum-lithium alloy LPBF, this new alloy has a higher construction efficiency and reduces the lithium loss rate. The related research results were published on the top issue of Additive Manufacturing with the title “Highstrength Al-Li alloy development for laser powder bed fusion”.
Paper link:https://www.sciencedirect.com/science/article/pii/S2214860421004097
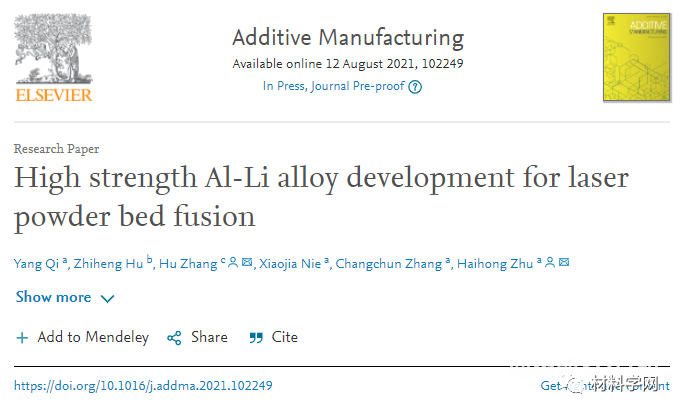
In this research, a new type of aluminum-lithium alloy specifically for LPBF technology was developed using casting and laser glazing methods. The newly developed Al-Cu-Li-Sc-Zr alloy has been evaluated and verified by LPBF treatment. When 0.8Sc-0.4Zr and 1.0Sc-0.5Zr are used to introduce Al-4Cu-1Li alloy, there is no crack in the laser area. As the content of Sc and Zr increases, the crystal grains in the laser area gradually become finer and become almost completely equiaxed when inoculated with 1Sc-0.5Zr. Refining the grain reduces the total pressure drop of the interdendritic liquid, so the alloy is more resistant to cracking.
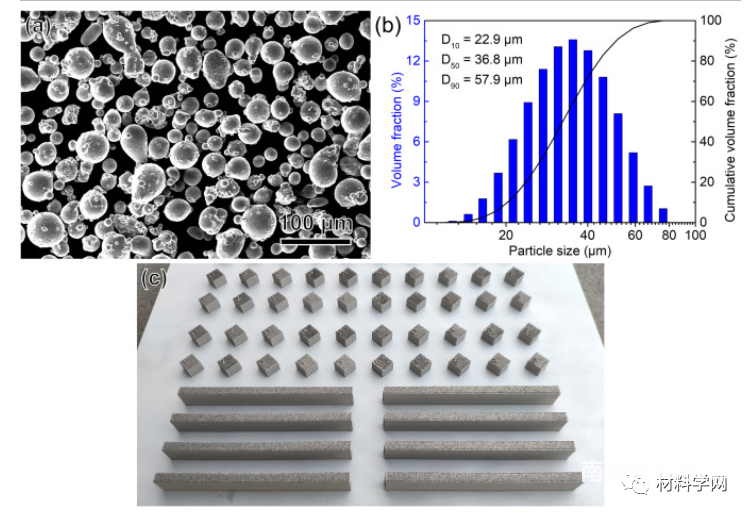
figure 1. (a) Scanning electron microscope image of Al-Cu-Li-Sc-Zr powder; (b) Powder particle size distribution of Al-Cu-Li-Sc-Zr powder; (c) Al-Cu-Li-Sc produced by LPBF -Representative cuboid samples and tensile plates of Zr alloy.
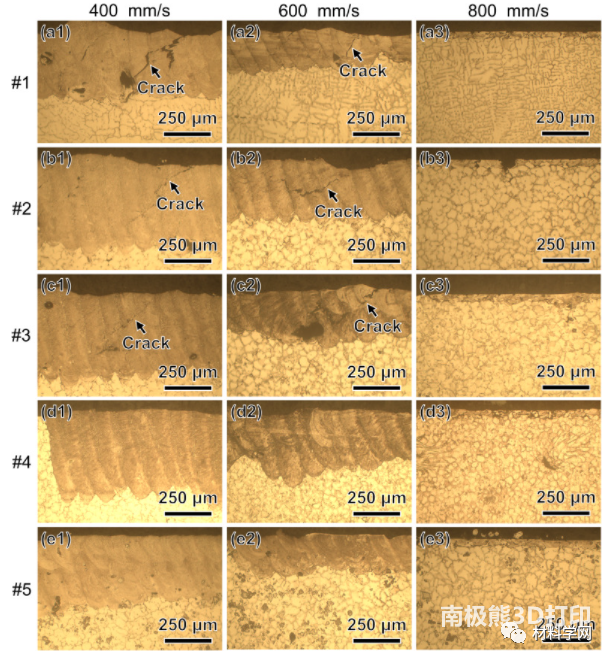
figure 2. Optical microscope images obtained from longitudinal sections of laser glazing samples with different scanning speeds: (a) Al-4Cu-1.25Li; (b) Al-4Cu-1.25Li-0.4Sc-0.2Zr; (c) Al- 4Cu-1.25Li-0.6Sc-0.3Zr; (d) Al-4Cu-1.25Li-0.8Sc-0.4Zr; (e) Al-4Cu-1.25Li-1Sc-0.5Zr.
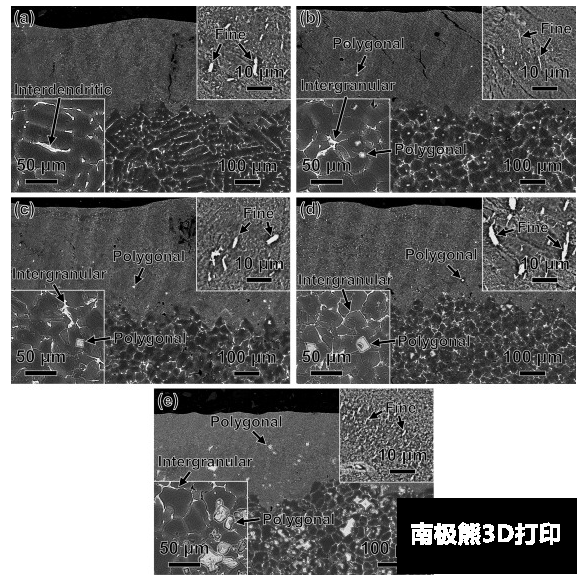
image 3. The backscattered electron image obtained from the longitudinal section of the laser glass sample: (a) Al-4Cu-1.25Li; (b) Al-4Cu-1.25Li-0.4Sc-0.2Zr; (c) Al-4Cu-1.25Li- 0.6Sc-0.3Zr; (d) Al-4Cu-1.25Li-0.8Sc-0.4Zr; (e) Al-4Cu-1.25Li-1Sc-0.5Zr. The illustration in the upper right corner is the high-magnification laser glass area. The illustration in the lower left corner is the casting area with high magnification.
(Editor in charge: admin)
0 Comments for “Huazhong University of Science and Technology Additive Top Issue: Additive Manufacturing of High-Strength, Crack-Resistant Aluminum-Lithium Alloy”