Introduction: Texas3D printing
architecture
Technology company Icon plans to create a community of 100 3D printed houses near Austin, Texas next year. This is the largest development of 3D printed houses in the United States so far.
It is reported that ICON cooperates with the leading American house builder Lennar and construction company BIG-Bjarke Ingels Group to provide deployment3D printingrobot technology,
software
And advanced materials to build these houses, the project is expected to break ground next year. This architectural project is in Lennar
invest
ICON’s latest round of US$207 million
Financing
The aim is to provide more affordable and technology-driven housing to meet the growing demand in the area.
housing
need.
Eric Feder, president of Lenx’s internal investment arm LENX, said: “The shortage of labor and materials are the two biggest factors that prevent many American families from realizing their home ownership dreams. Lenner has been expanding the boundaries of technological innovation to maintain the quality of housing. Affordability, while3D printingIt is a very exciting technology. We are very happy to work with ICON to develop solutions for emerging challenges in the coming years.”
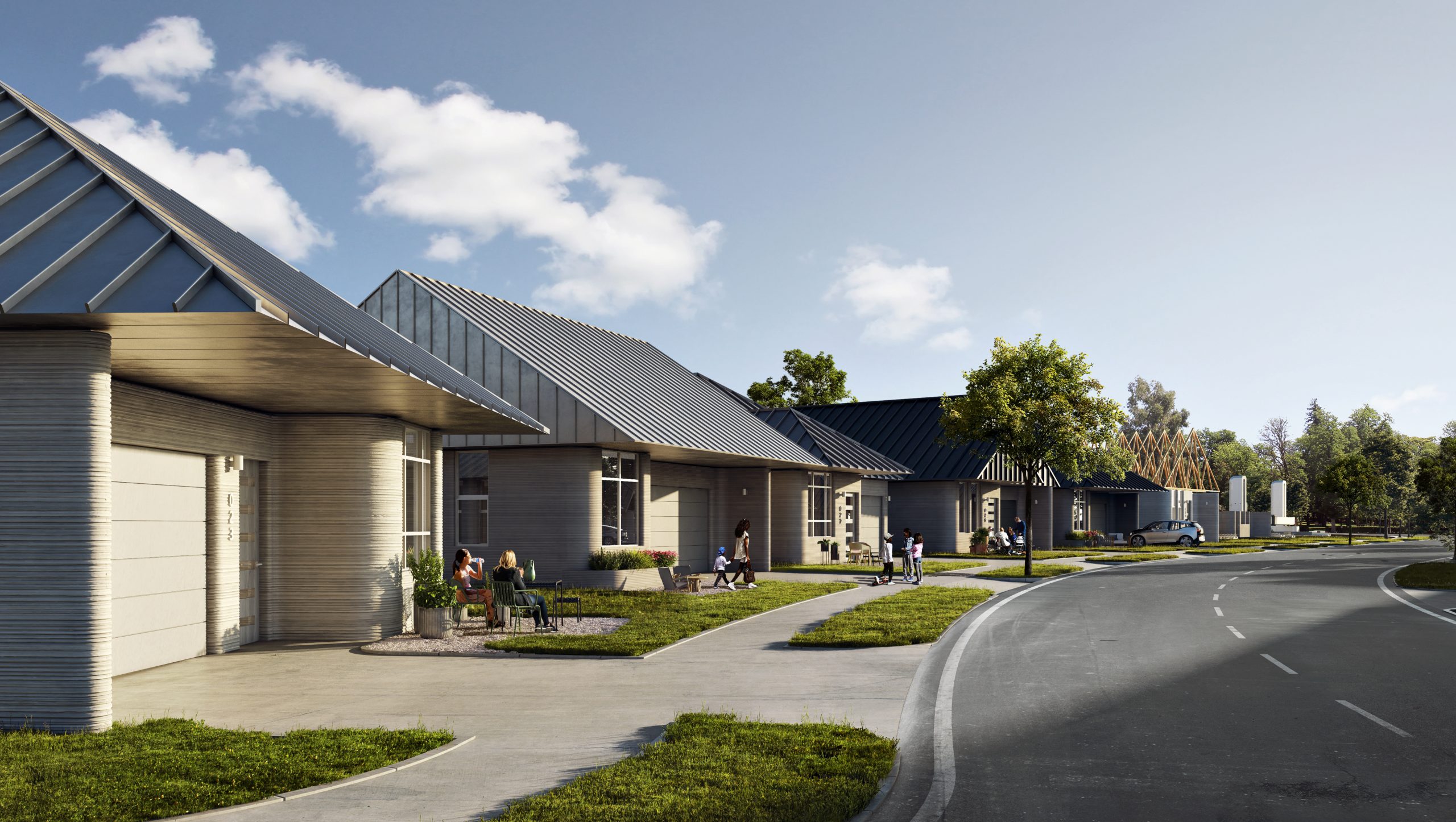
Icon3D printingArchitecture Technology
So far, ICON has used their company’s proprietary Vulcan 3D printingIt has built more than 20 residences in the United States, and there are many abroad.One of the projects includes cooperation with the non-profit organization New Story, which established a3D printingHousing in the Latin American community.
ICON has also worked with the U.S. military to demonstrate3D printingPotential for military applications, built a3D printingBarracks for the troops to live during the training period. ICON also found that its construction technology is
aviation
aerospace
Field application potential, the “world’s first” was produced earlier this year3D printingThe lunar launch pad, in cooperation with NASA, used its technology to create a simulated Martian environment and a non-world building system.
Earlier this year, an upgraded version of Vulcan’s “Next Generation System” was announced. Compared with traditional construction methods, it can effectively achieve faster and more flexible construction of houses.
ICON’s new machine has a larger build capacity and a printing speed of 5-10 inches per second, twice that of the previous generation, and can print structures with an area of 3,000 square feet. The upgradeability of this machine has allowed the company to carry out more bold applications in the past few months, including the construction of four multi-storey buildings in East Austin, which is expected to be listed on the US housing market.
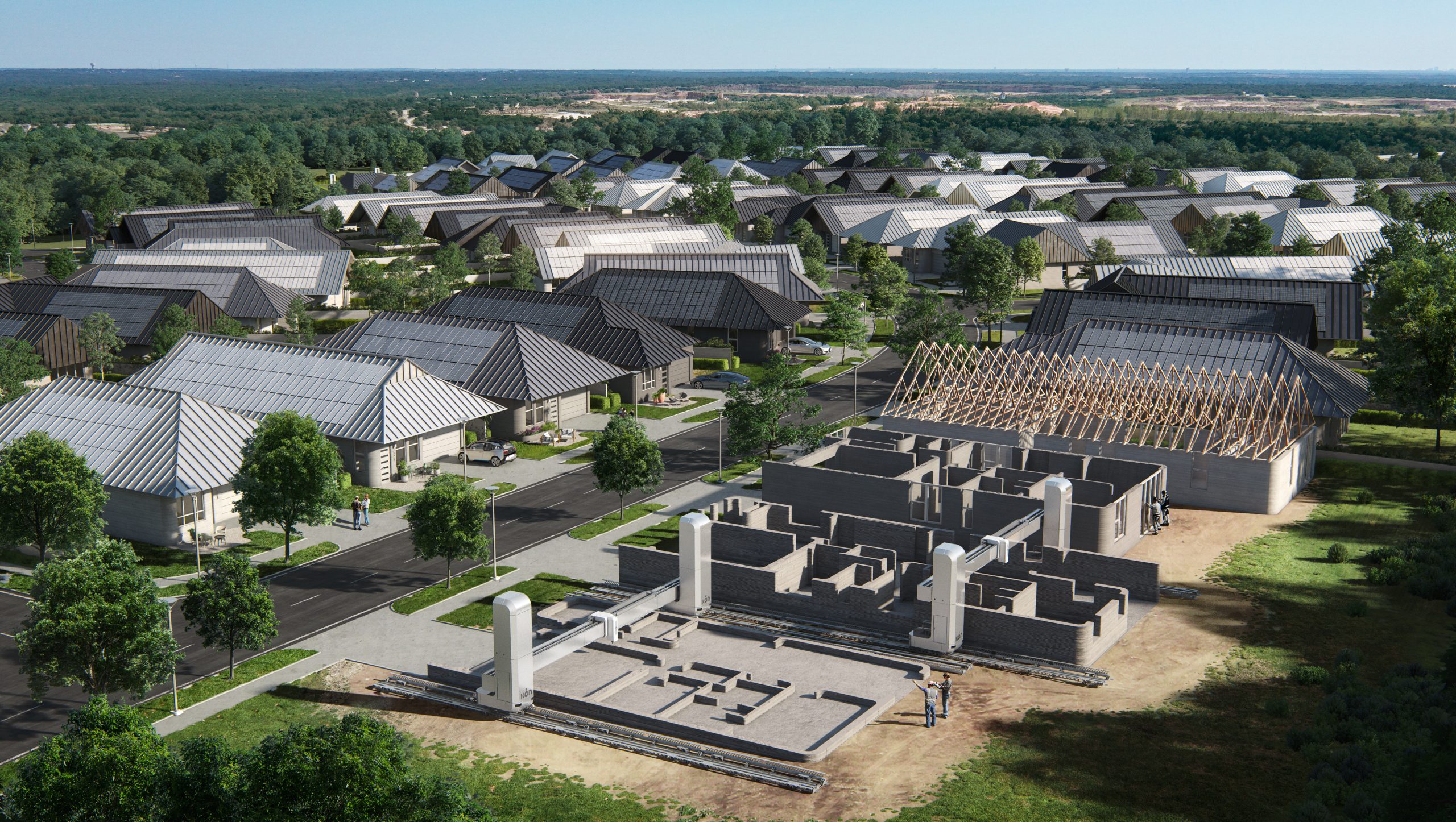
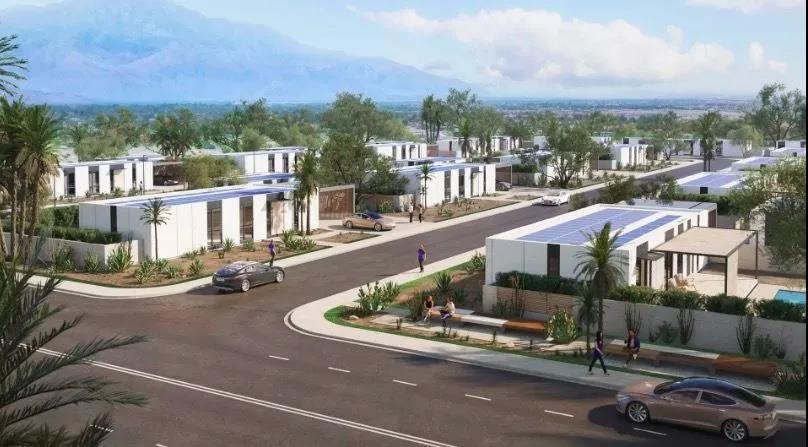
From dozens of households to hundreds of households
ICON’s latest project, a community of 100 families, will begin in 2022 with the goal of building the largest3D printingResidential community.
BIG-Bjarke Ingels Group will design these houses together, and ICON will use its Vulcan
3D printingMachine and proprietary Lavacrete material3D printingOn the first floor of the building, the Lavacrete material combines typical Portland cement with advanced additives to help it be used in extreme weather.Internal and external concrete3D printingThe air space between the walls will be injected with spray foam insulation to provide a comfortable environment for residents.
Once ICON3D printingOut of the first floor of the house, the finishing will be done by Lennar using traditional wood construction technology. According to Jason Ballard, co-founder and CEO of ICON, ICON is seeking to respond to the global housing crisis by increasing housing supply while improving the sustainability of the construction industry.
He said: “Building-scale3D printingNot only can it provide higher-quality houses faster and more economically, but the fleet of printers can change the way the entire community is built and make it better. The United States is facing a deficit of approximately 5 million new homes, so it is a deep demand to rapidly increase the supply without compromising quality, aesthetics or sustainability, and this is where our technology is superior. “
ICON hopes3D printingWill make the construction cost of new homes lower and faster than traditional construction methods.Currently, ICON can3D printingOut of the first floor of a residence.
Ballard continued: “For ICON, cooperating with Lennar is an honor and a huge milestone. Lennar is an elite top residential builder committed to innovation. We believe this will be a watershed in the history of community-scale development. It’s even the flag of future architecture.”
Martin Voelkle, partner of BIG-Bjarke Ingels Group, also believes that as the construction industry continues to adopt the technology on a large scale,3D printingIt is possible to “completely change the built environment”.
He added: “Through cooperation with ICON and Lennar, we can see this new technology spread to the widest audience.3D printingBuildings and photovoltaic roofs are innovations, important steps to reduce waste in the construction process, and also make our houses more resilient, sustainable and
energy
An important step for self-sufficiency.
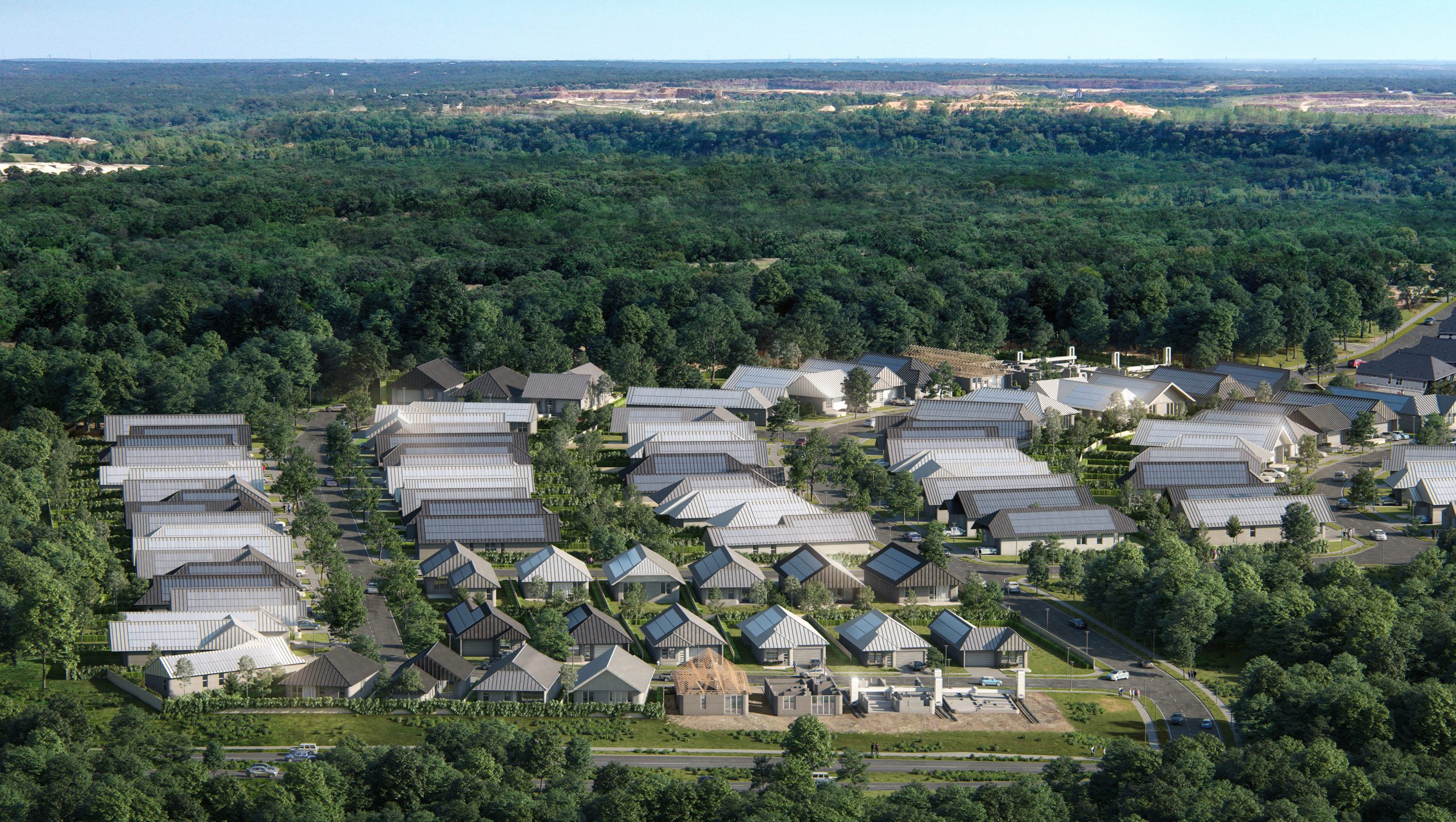
(Editor in charge: admin)
0 Comments for “ICON will build the largest 3D printed residential complex ever in Austin”