In an electric motorcycle, the battery has a large working current and large heat generation, and at the same time the battery pack is in a relatively closed environment, which will cause the temperature of the battery to rise. There are two types of battery pack heat dissipation: active and passive, and there is a big difference in efficiency between the two. The cost required by the passive system is relatively low, and the measures taken are relatively simple. The structure of the active system is relatively complex and requires more additional power, but its thermal management is more effective.
So this involves a design expandable space: how to increase the thermal contact area between the cooling system and the battery and improve the cooling efficiency?In this issue, through the case of Voxeljet, together with Gu You, we will gain insights on how to pass3D printingOptimized shell makes the battery life of electric motorcycle longer.
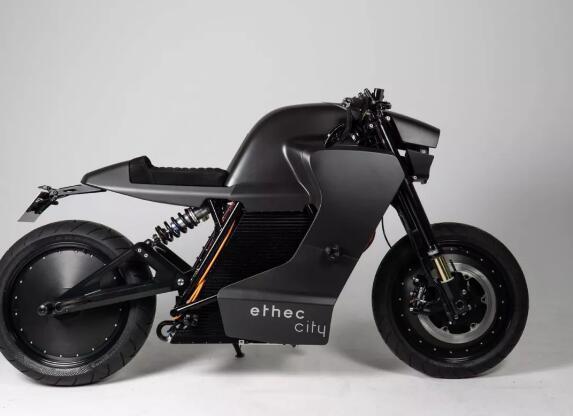
Product design that changes quietly
According to the Institute of Engineering Thermophysics of the Chinese Academy of Sciences*, due to the limited space for batteries on the vehicle, the number of batteries required for normal operation is also large. The batteries will be discharged at different rates and generate a large amount of heat at different heat generation rates. The accumulation of time and the influence of space will accumulate a large amount of heat, which will lead to complex and changeable temperature conditions in the operating environment of the battery pack. The temperature rise in the battery pack seriously affects the operation, cycle life, charge acceptability, battery pack power and energy, safety and reliability of the electrochemical system of the battery pack.
If electric
car
The inability of the battery pack to dissipate heat in time will result in excessively high temperature or uneven distribution of the battery pack system. As a result, the battery charge-discharge cycle efficiency will be reduced, and the battery’s power and energy will be affected. In severe cases, it will also cause thermal runaway and affect system safety. In addition, due to the dense placement of the heating battery bodies, the middle area will inevitably collect more heat, and the less edge area will increase the temperature imbalance between the cells in the battery pack, which will cause the battery modules and single cells. The imbalance of physical performance ultimately affects the consistency of battery performance and the accuracy of battery state of charge (SOC) estimation, and affects the system control of electric vehicles.
According to the Institute of Engineering Thermophysics of the Chinese Academy of Sciences, the liquid-cooled heat dissipation system of the power battery refers to the refrigerant that directly or indirectly contacts the power battery, and then the heat generated in the battery pack is taken away by the circulating flow of the liquid fluid to achieve the heat dissipation effect. Kind of cooling system. The refrigerant can be water, a mixture of water and ethylene glycol, mineral oil and R134a, etc. These refrigerants have high thermal conductivity and can achieve better heat dissipation effects.
A key project of ETH Zurich is implementing a new type of cooling system with the support of Voxel-voxeljet.3D printing, The research object in its project: the new cooling system in the ethec city electric motorcycle can ensure a longer battery life.
electric
transportation
The development of tools until 2021, where the high speed and long distance of electric vehicles are actually always associated with extremely heavy and huge energy storage systems. Cars and trucks may have provided the necessary space, but on electric motorcycles, the art of engineering still has some obstacles to overcome. Due to insufficient battery capacity, the relatively powerful electric motorcycles already on the market are more suitable for urban traffic than long-distance off-road travel.
The technical approach of the ethec city project may change this. ethec stands for “ETH Electric Cruiser”, an electric motorcycle concept developed by the Swiss Federal Institute of Technology in Zurich. The initiator of the project is inspire AG, a strategic partner of the university, which translates research results into practical applications. In the ethec project launched in 2017, its purpose is to significantly improve the efficiency of electric motorcycles by recovering braking energy and improving battery design.
Limited space makes battery cooling more efficient
Compared with large vehicles, it is more difficult to keep the heat generated during battery operation on a motorcycle at a constant level. Optimal temperature management is critical to battery life.
Battery cooling in electric vehicles is usually achieved by the coolant flowing through the battery through hoses or pipes. The disadvantage of this method is that only point or line contact can be made. In fact, immersive direct contact is not realized. In view of the limited space in the middle of the motorcycle frame, the ethec project can finally realize only one concept: all the batteries are completely embedded in the oil bath.
The ethec project team was divided into two modules and assembled a total of 1,269 lithium-ion circular batteries with a total output power of 15 kWh. Computer-aided flow simulation is then used to create the optimal structure of the battery casing. Not only must it be absolutely leak-proof, but it must also ensure perfect contact between the individual cells and the flow of silicone oil.In order to show the way from prototype to mass production, the ethec project team chose to fall3D printingIn terms of the combination of sand mold and metal casting, specifically, 3D printed sand molds are used as templates for casting aluminum-copper alloys.
When dealing with very complex designs,3D printingSand molds can also significantly save time, in the manufacture of complex sand castings
Mould
Time can save unprecedented time. Including the voxeljet-Voxel-based manufacturing process, it is now possible to economically construct parts of almost any size using a combination of binder injection technology and metal casting. The ETHEC battery case was finally cast at the Kupral Spa aluminum foundry in Brescia, Italy.
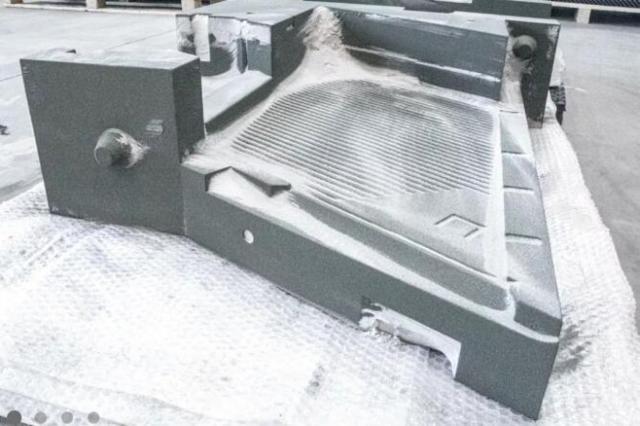
The concept of an energy-saving electric motorcycle designed by the ethec project shows amazing potential: the top speed should reach 160 km/h, and thanks to the energy recovery and novel battery concept, ethec city can achieve a cruising range of about 400 kilometers.
Not only in Europe, but according to market observations in 3D Science Valley, in China, voxeljet-Voxel Suzhou China Headquarters has also adopted innovative3D printingSand mold technology can realize the manufacturing process from model to product within 3-5 days. It can also realize the flexible and efficient production of key automotive parts through innovative processes, fixtures, tools, and complete line automation design. Innovation provides strong support.
In general3D printingThe components produced in this way can not only achieve exciting futuristic design, but also save a lot of cost, because they can not only have an optimized topology, but also can greatly reduce weight, and require fewer parts to assemble, and in terms of function Enhancements can also be obtained. Perhaps, soon, we will notice that the shape of the product we are familiar with is quietly changing.
(Editor in charge: admin)
0 Comments for “Insights into how to use 3D printing to optimize the shell to make the battery life of electric motorcycles longer”