On March 6, 2020, Due Pi Greco, an Italian product development service provider, used Stratasys’ FDM 3D printingTechnology has expanded from prototype manufacturing to production services.
This company will install five Stratasys FDMs 3D printingThe machine is used in its product development process together with Nylon 12CF, ULTEM 9085 resin, ST-130 and ASA materials. Therefore, Due Pi Greco can provide innovative production and application services for different industries, replacing traditional and more expensive processes with additive manufacturing.
Diego Pagnan, Founder and Owner of Due Pi Greco, explained: “The various production materials of Stratasys allow us to develop some innovative applications for our customers. For example, we recently became Zoppas, a global supplier of heating systems for household and industrial use. ) Design and3D printingA boiler assembly. This is made possible by ULTEM 1010 resin, which is a polymer that can work at high temperatures up to 216°C. ”
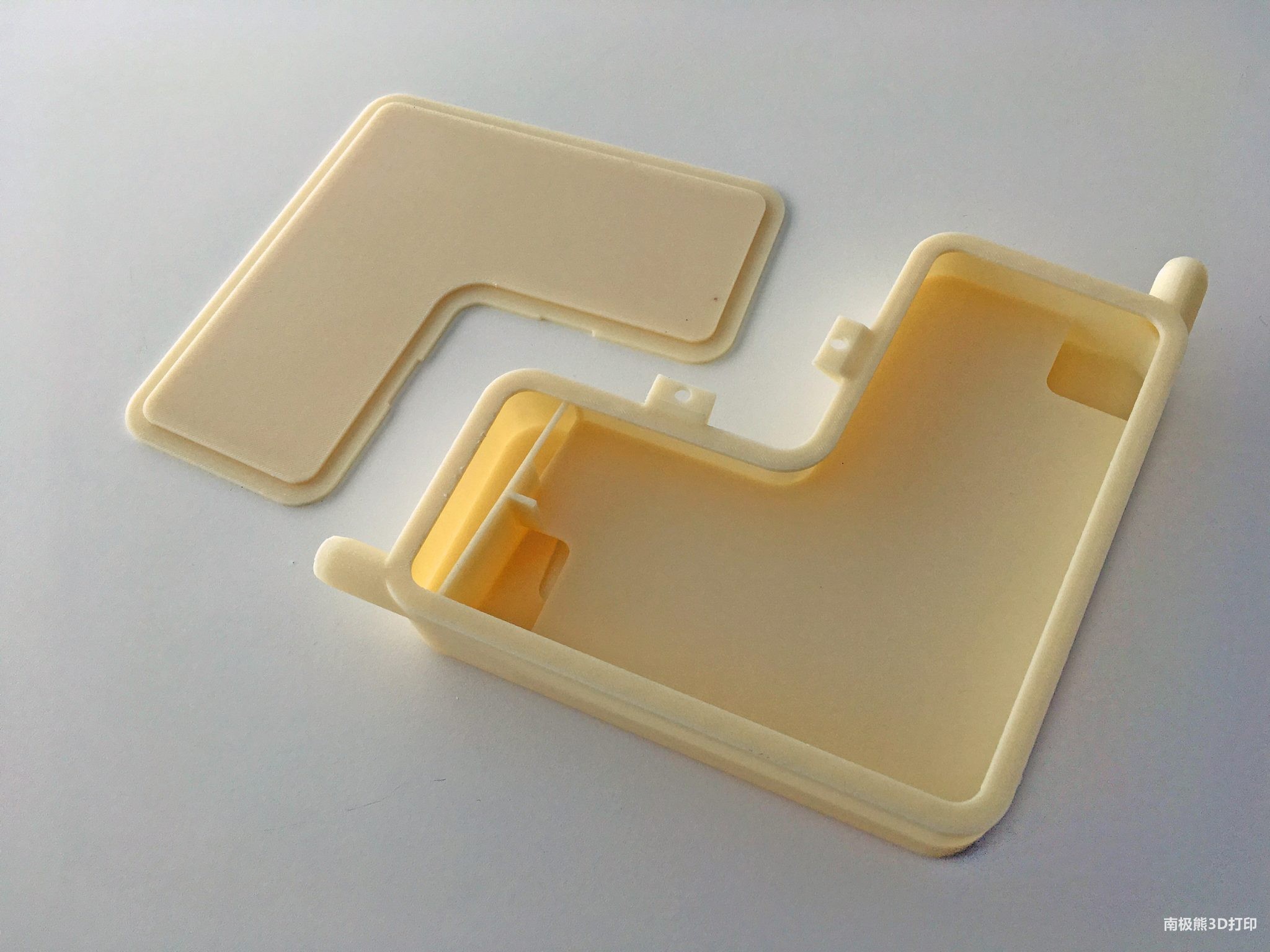
Substitute for metal CNC machining parts
Due Pi Greco has been providing product development services since 2010, specializing in the design, prototyping and manufacturing of functional parts and components.The company has since added3D printingSince the equipment, has been committed to component prototyping and optimized product design. Use Stratasys
3D printingThe machine enables Due Pi Greco to explore additive manufacturing for the production of final parts.
Pagnan added: “In the beginning, we mainly acted as3D printingService providers to meet prototyping requirements. And now, we use Stratasys in all our development work 3D printingMachine, so that we can better understand the huge potential of additive manufacturing in production. “
The company has used four Stratasys FDMs 3D printingRecently purchased the Fortus 380mc carbon fiber version (CFE) from Energy Group, an Italian distributor of Stratasys. Pi Greco chose to purchase a new system to use Stratasys’ FDM Nylon 12CF material, which is a3D printingComposite material, containing 35% chopped carbon fiber. With this material, it is possible to meet the performance requirements of new customers for parts, thereby increasing the number of customers.
Pagnan said: “Using FDM Nylon 12CF, we can perform3D printingParts, the performance of these parts is similar to the parts produced using CNC technology. “
Due Pi Greco recently collaborated with the University of Padua to develop the engine for the single-seater racing car that will be racing in Formula SAE.3D printing. Using FDM Nylon 12CF on Fortus 380mc CFE can improve the lead time and cost of traditional carbon fiber production.
In addition, Due Pi Greco also cooperated with an unnamed Italian bicycle brand, using Fortus 380mc CFE 3D printingThe machine optimizes the design and production of bicycle seats. Customers stated that the product exceeded expectations in terms of surface finish and resistance.
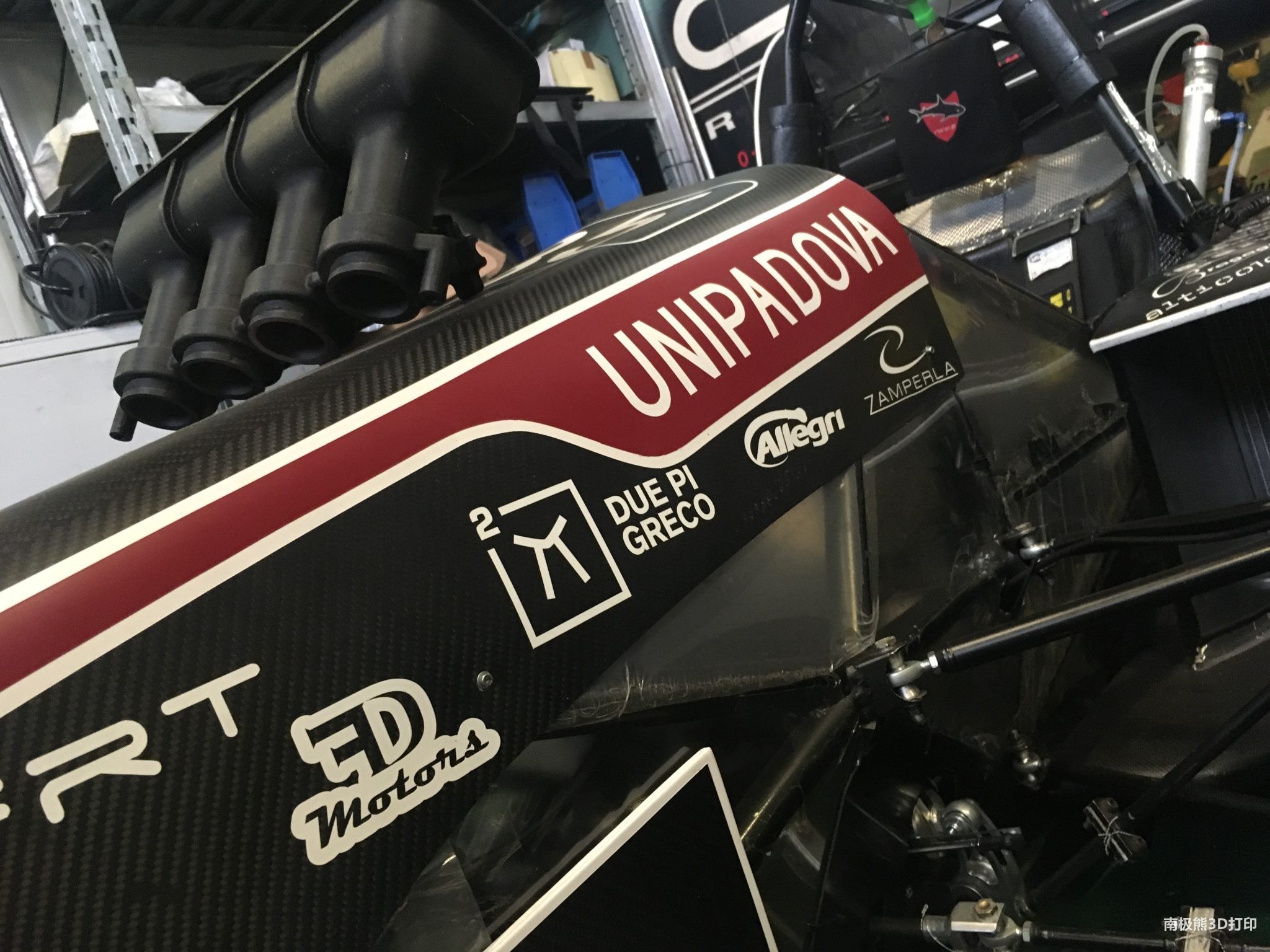
Stratasys Carbon Fiber3D printing
Stratasys’ Fortus 380mc CFE initially began shipping to customers in 2018.release3D printingThe machine is to meet the growing demand for carbon fiber composite applications. This system is dedicated to nylon 12CF material, which is designed for functional prototypes and end-use components in the automotive and aerospace industries.since3D printingSince the release of machines and materials, they have seen various applications in many industries, especially in the automotive field.
At RAPID + TCT 2019, Stratasys revealed that Arrow Schmidt Peterson Motorsports has been using Nylon 12CF to create functional prototypes, product components and robust tools for its racing cars. British supercar manufacturer Briggs Motor Company (BAC) has also used Nylon 12CF to produce components for its Mono R supercar. The American sports car racing team Penske uses the Fortus 380mc CFE to produce prototypes and production parts for vehicle testing.
(Editor in charge: admin)
0 Comments for “Italian service provider expands 3D printing from prototype manufacturing to production, replacing part of CNC”