Japan’s Tohoku University professor Honma and assistant Kobayashi Hiroaki and others developed the3D printingThe technology of machine-made all-solid-state batteries. When making, use materials that can freely change the hardness. It only takes a few hours to make a battery, and there is no need to carry out the high-temperature process that was required in the past. The trial-produced battery has withstood various performance tests and has certain performance, which is expected to contribute to the early practical use of all-solid-state batteries.
Electrolyte is one of the main components of the battery, usually in a liquid state, but the electrolyte of all solid-state batteries is solid, and the risk of fire accidents is relatively small. Another feature of this battery is that the battery can be stacked to increase the storage capacity per unit volume.As an extendable pure electric
car
(EV) The new generation battery with endurance is highly anticipated.
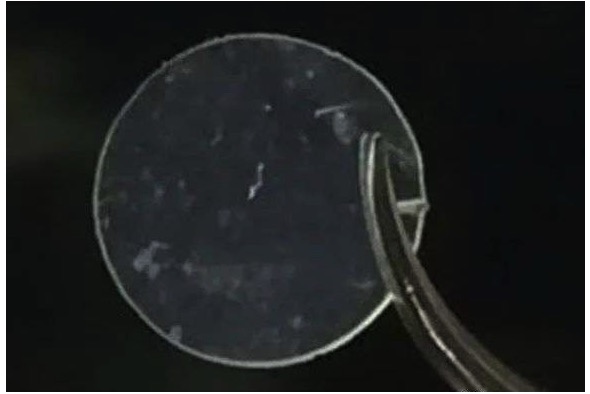
The mainstream of all-solid-state batteries is to forcefully press the electrodes and electrolyte materials together and heat them to hundreds of degrees Celsius. However, the heating process requires cost, and there are cases of thermal cracking. At the same time, there is a problem. Because the electrolyte is hard, when the positive electrode and the negative electrode repeatedly expand and contract with charging and discharging, the two cannot be closely attached, resulting in poor battery performance.
The research team carried out research on the production of soft electrolyte membranes for all-solid-state batteries. After mixing a special liquid that is conducive to the movement of lithium ions and silicon oxide, a glass film similar to soft contact lenses can be formed. As long as the amount of silicon oxide is changed, the softness can be adjusted.
This time, the research team reduced the amount of silicon oxide contained in the electrolyte membrane by half, turning it into a gel.Then mix it with the resin that will be solidified by ultraviolet radiation, and you can use it3D printingMachine shaping.
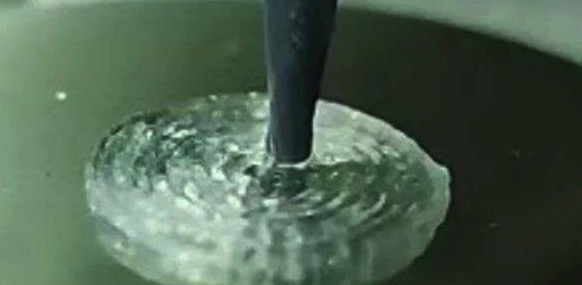
Experiments have proved that by turning the electrolyte, lithium cobalt oxide for positive electrode, lithium titanate for negative electrode, etc. into gel-like materials, only3D printerYou can make a battery. It is said that it can be manufactured in about two hours. It can be produced by coating the material and irradiating it with ultraviolet rays, without high temperature heating, which can greatly reduce the manufacturing cost. The flexible electrolyte is not easy to crack, and even if the component expands and shrinks, it can be softly attached.
The trial-produced battery can stably charge and discharge more than 100 times. Safety has also been confirmed by fire test etc. Professor Honma said, “As long as you input data, the size and shape can be changed at will.” The problem facing practical application is that the ionic conductivity of the electrolyte is not high enough. Because lithium ions cannot move smoothly, it is difficult to release huge energy instantly.
The research team will adjust the composition of the material with the goal of improving ion conductivity. The experiment of using the developed battery to drive the car has been successful, and the maximum speed of the experiment reached 30 kilometers per hour. Researchers will make improvements repeatedly to increase output power and consider installing it on pure electric vehicles. It will also vigorously develop cathode materials with high energy density.
The first phase of the goal is to achieve practical use in the power supply of sensors and wearable terminals.
(Editor in charge: admin)
0 Comments for “Japan realizes the use of 3D printing to manufacture all-solid-state batteries”