May 2, 2022 Lincoln Electric Holdings taps large metal3D printingTechnology provides Chevron USA with an instant parts solution to help a refinery resume production on schedule.
During a recent routine maintenance outage, Chevron found that supply chain instability and extended lead times for traditionally manufactured parts prevented their refineries from resuming production as originally planned.So Chevron’s additive engineering team partnered with Lincoln Electric to use3D printingTechnical manufacturing of the same quality
standard
key replacement parts.
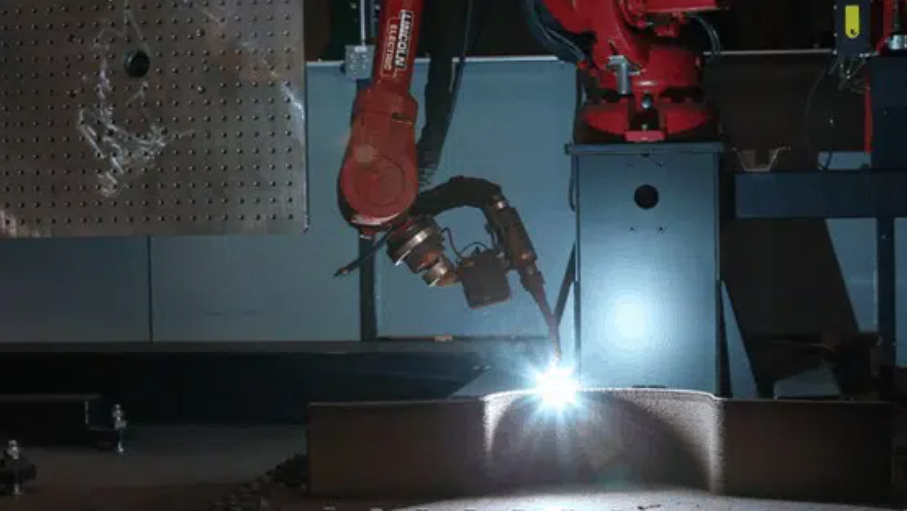
largeMetal 3D Printingtechnology
“Due to current supply chain issues, our maintenance schedule cannot be completed,” said materials technology engineer Robert Retew. “When we realized this supply crunch could impact operations and maintenance. We immediately worked with Lincoln Electric to explore how to make parts faster so we could resume production on schedule.”
Working together with industry experts at Stress Engineering Services, the two teams printed eight nickel alloy replacement parts (approximately 226 kilograms) with an average length of approximately 3 feet (0.9 m) and a weight of over 500 pounds in just 30 days in total .
“We are excited to partner with Chevron to demonstrate the unique instant production value of 3D printing and its ability to manufacture on-site,” said Christopher L. Mapes, chairman and CEO of Lincoln Electric.
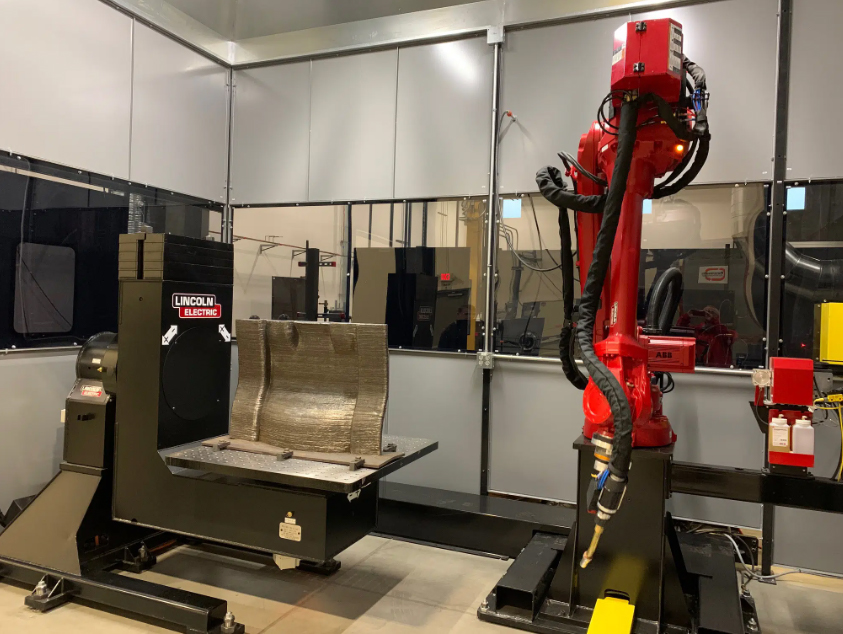
He added: “Metal 3D Printingis a kind of large metal parts,
mold
tools and product prototypes, a game-changing solution for applications including industrial manufacturing,
energy
and
aviation
aerospace
various end markets. Design flexibility and cost reduction are also advantages of this technology while speeding time to market. “
As one of the largest wire 3D printing plants in the world, Lincoln Electric has additive manufacturing solutions for a wide variety of low-volume applications. Capable of printing metal structures up to 7 feet (2.1 m) long and weighing in excess of 5000 lbs (2265 kg). This innovative technology significantly reduces manufacturing time, shrinks the supply chain, and enables designability beyond traditional manufacturing capabilities.
About Lincoln Electric
Headquartered in Cleveland, Ohio, Lincoln Electric has 60 manufacturing sites in 19 countries around the world. The company specializes in the development and manufacture of arc welding systems and plasma cutting equipment, including a range of automation equipment.The company’s new additive manufacturing service, due to launch later this year, will expand Lincoln Electric’s automation expertise and leverage
software
Core competencies in development and metallurgy.
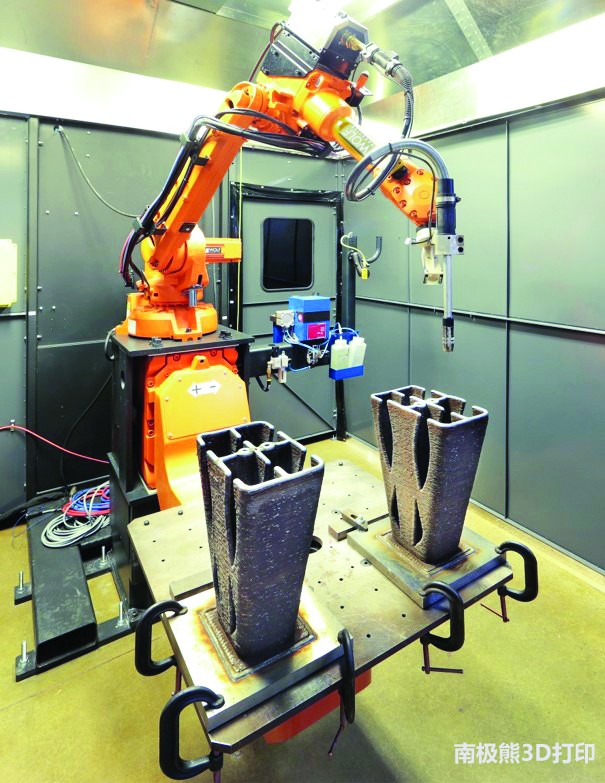
In 2019, it acquired Baker Industries, a Michigan-based mold supplier. The company provides polymer and metal additive manufacturing services, as well as traditional processing and fabrication.
“We are delighted to welcome Baker Industries to Lincoln Electric and our new additive manufacturing platform,” said Christopher L. Mapes, chairman, president and CEO of Lincoln Electric. “Additive manufacturing is a key strategic growth area for automation, and BAKER’s expertise and capabilities will help expand our additive manufacturing services and enhance our presence in aerospace and
car
attractiveness in the market. “
Along with Baker, Lincoln Electric’s additive manufacturing services will be supported by the new Additive Manufacturing Development Center in Cleveland. The company also said its service will be able to produce large metal parts using robotic arms.
(responsible editor: admin)
0 Comments for “Lincoln Electric partners with Chevron to use 3D printing to solve supply chain problems”