On November 3, 2021, Lawrence-Livermore National Laboratory (LLNL) engineers have developed an optimized liquid metal injection (LMJ) new3D printingMethod, they can realize real-time monitoring of droplet ejection. The LLNL team did not use the usual high-cost method based on high-speed cameras, but designed a method that combines near-field detection and simulation, focusing on only one parameter when analyzing the ejected material. The researchers say that using their method, it is possible to determine the cause of nozzle problems in real time before adjusting the printer settings to correct the quality of the parts.
Tammy Chang, the lead author of the study, said: “Our results show that the LMJ can be monitored in situ using millimeter wave detection methods. This is exciting because it means that we can replace the previously expensive high-speed, high-resolution optics. Distinguish the instrument, realize real-time performance evaluation and feedback control to ensure high-quality metal printed parts.”

Identify LMJ problems in real time
Liquid metal injection is a new3D printingThe method is to launch tiny metal droplets from a nozzle at a high speed, forming lines from dots, and layers forming layers from lines, which can then be built into uniform parts. The method is similar to that of an inkjet printer. However, compared with laser-based systems, LMJ machines do not require the use of dangerous metal powders, so they may provide a safer means to achieve the same purpose.
With the continuous development of new applications for jetting technology, its performance has also received more attention. Facts have proved that in some applications, it is difficult to determine the best parameter set. This is mainly because the spray material is affected by many factors, from droplet size and spray time to speed, flow rate and temperature.
Although high-speed camera is often used to analyze the operation of LMJ, this method can only really be used for a few seconds, because due to processing limitations, a large amount of data takes several days to filter. In order to make real-time analysis more reasonable, the LLNL team therefore developed a scalable method that relies more on simulation rather than capturing gigabytes of information.
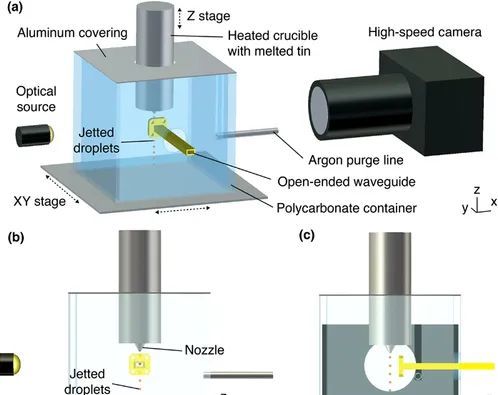
△The experimental material injection monitoring device of the LLNL team. Picture from “Journal of Applied Physics”.
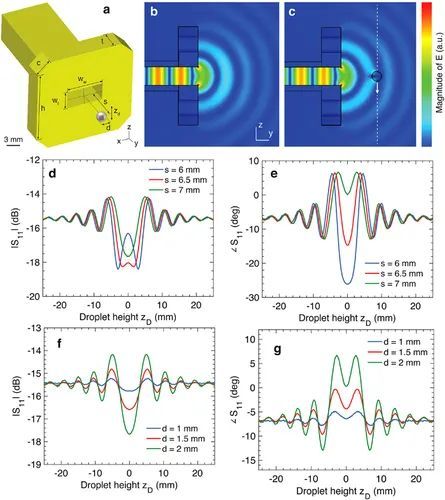
△Simulated open waveguide result. All dimensions are in millimeters. (a) The size of the rectangular waveguide hole, the diameter of the metal droplet is d, the height is zD¼0, and the distance from the edge of the waveguide is s. wW¼ 7:11, wL ¼ 3:56, c ¼ 3:46, t ¼ 3:81, h ¼ 14:26. Height zD ¼0, distance s from the edge of the waveguide. (b) The instantaneous electric field size of the open waveguide. The instantaneous electric field size of the open waveguide. (c) The instantaneous electric field when a droplet with a diameter of 800 microns is located at s ¼ 7, z ¼ 0. (d) and (e) Return loss magnitude and phase as a function of different drop heights. A function of droplet height at different distances from the waveguide s. (f) and (g) Under different droplet diameters, the magnitude and phase of the return loss are a function of the droplet height.
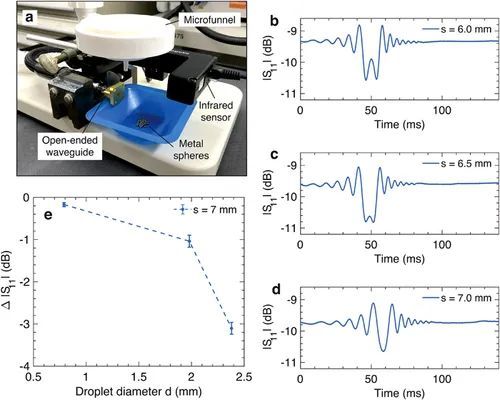
△Control experiment with metal spheres of known diameter. (a) Experimental device. (b)-(d) The time-domain results of the time-domain results of measuring S11 under different droplet spacing. Droplet diameter: 1.98 mm. (e) The relative change of S11 for three sphere diameters (0.79, 1.98, and 2.38 mm)
LMJ monitoring tool that can be used for factory-level production
The engineer’s improved monitoring method is mainly to put an open waveguide perpendicular to the printer during the production process, so that any ejected droplets will pass through the electromagnetic field of the aperture. By doing so, it is possible to capture the dynamics of metal droplets on site. The data collected in this way is far less than the data required when using video analysis alone.
To put their method into practice, the LLNL team inserted an aluminum waveguide into the LMJ 3D printingIn the machine’s construction room, cameras are set up on both sides of the system to capture the results. Interestingly, by focusing on one parameter at a time, researchers can accumulate enough data to obtain microscopic resolution of droplet behavior through electromagnetic simulation.
For example, during the jetting process, the research team was able to non-invasively determine the precise effect of droplet spacing and diameter on the characteristics of the printed layer. By further evaluating their data, the engineers were also able to find the cause of the clogged print nozzle in their experiment, because when it happened, there was an observable change in the captured wavelength.
It turns out that a kind of tension builds up on the nozzle surface, which hinders the emission of the material and causes the droplets to stick in place until the next pulse of the printer ejects them. Therefore, the researchers believe that if deployed in a factory environment, their method can be used to determine the quality of deposited droplets in real time, enabling manufacturers to minimize printing failures.
Andy Pascall, co-author of the research report, concluded: “Getting a clean, direct drop jet is the key to achieving good print quality. High-speed cameras work well in our laboratory-scale environment where we test new printing parameters. But it will never play a role in production, and this type of discrimination will be very applicable under production conditions.”
Although LLNL’s resolution tool can currently detect droplets with a size of 400-500m. In addition, using other signal processing methods, it is even possible to turn it into a closed-loop system, where the data can be used to adjust printing parameters on the fly.
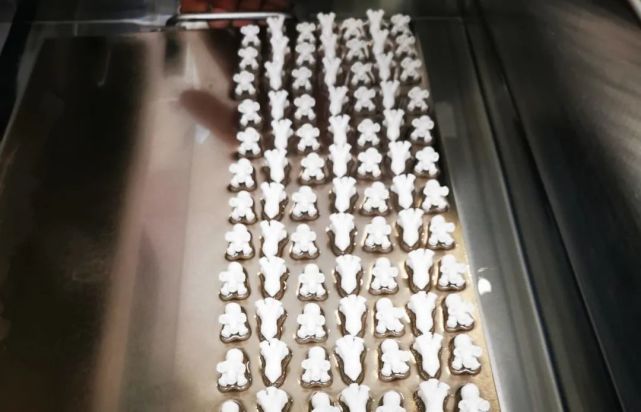
△A post-processed XJet 3D printingParts, material jetted parts continue to find new end uses. The photo is from XJet.
AM’s material injection technology
Like many advanced production processes, material injection3D printingIt is a subject of constant research and development, and engineers are trying to develop its large-scale manufacturing capabilities. That being said, if you think that jetting technology has not found an end application, you are wrong, because the technology sold by several companies in the entire industry can be reasonably called material jetting.
For example, Stratasys continued to make significant progress in its Polyjet technology and chose to launch the desktop J35 Pro earlier this year. The launch of this system is designed to enable those who work in the office to use their company’s material injection process, and it is said to be an ideal prototype for consumer and electronic products as well as academic applications.
In addition, HP has developed another well-known material jetting technology-Multi Jet Fusion (MJF), which has been3D printingThe supplier adopts. More importantly, as the compatibility of its machines continues to expand, its applications are also expanding. Companies such as Materialise have previously introduced special materials to unleash the potential of HP systems.
Elsewhere, XJet, a material jetting expert, has cooperated with Straumann for its ceramic-compatible Carmel 1400
3D printingThe machine found the terminal dental application. The high throughput of this printing system and compatibility with soluble supports are said to be beneficial to the company because its dental professionals are now able to spend more time with patients because they do not have to worry about the post-processing of printed parts.
3D printingThe machine found the terminal dental application. The high throughput of this printing system and compatibility with soluble supports are said to be beneficial to the company because its dental professionals are now able to spend more time with patients because they do not have to worry about the post-processing of printed parts.
The research results of the researchers are detailed in their paper, entitled “Millimeter-waveelectromagnetic monitoring for liquid metal droplet-on-demand printing,” which was written by T. Changa, S. Mukherjee, NN Watkins, E. Benavidez, AM Gilmore , Co-authored by AJ Pascall and DM Stobbe.
Related paper links: https://aip.scitation.org/doi/10.1063/5.0065989
(Editor in charge: admin)
0 Comments for “Liquid metal jet 3D printing in-situ monitoring tool to ensure the quality of part forming”