On April 4, 2022, metal 3D printing company Mantle announced that it is developing a collaboration with Westminster Tool, Wepco Plastics and Precision Laser Technology (PLT)3D printing
mold
.
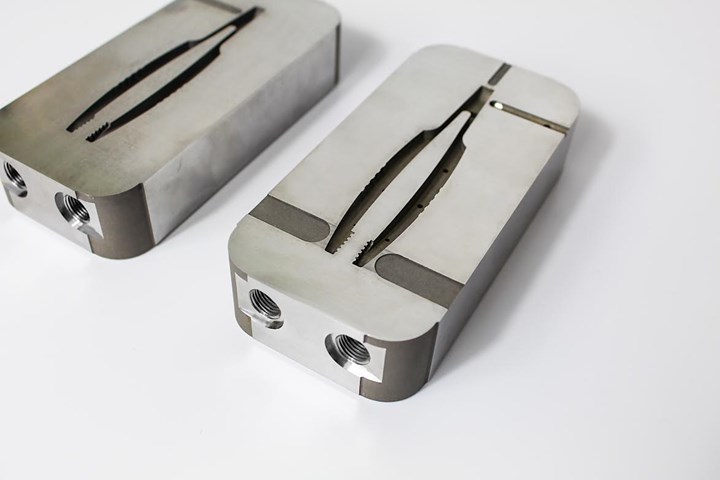
In 2019, the two companies began to cooperate to advanceMetal 3D PrintingTechnology. Westminster Tool (Westminster Tool) and Mantle (Mantle) recently participated in the exhibition (PTXPO) to promote their products.
At the event, moldmaker Westminster Tool unveiled details of a partnership with Mantle and medical materials compounder Foster Corp.They are filled with high-purity glass
biology
base polyamide compound to manufacture medical-grade tweezers using Mantle’s TrueShapeMetal 3D PrintingCavity injection molding process, the tweezers will be jointly tested in the future. Westminster announced it was one of only two test sites in the partnership, with plans to deliver a prototype this spring.
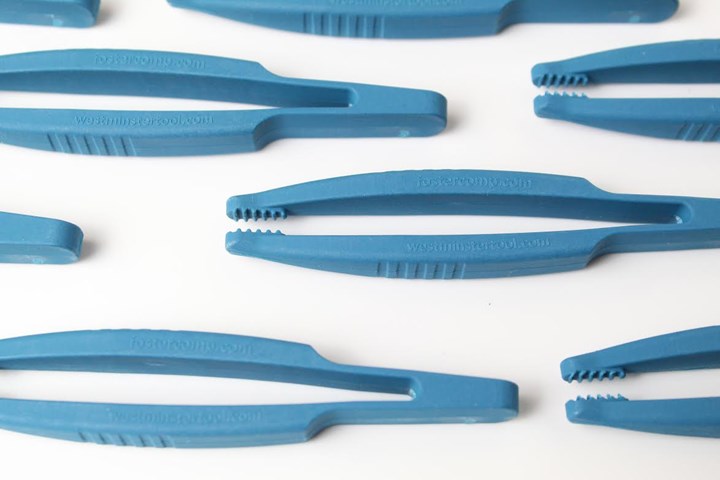
The tweezers were moulded from Westminster using Rilsan FKZM 65 O TD MED resin supplied by Foster. The compound is a 65 percent glass-filled bio-based polyamide material, Scott Kraemer, senior applications engineer at Mantle, said in a presentation at PTXPO. Using their technology to print the cavity and core in tool steel took a total of 86 hours, and the mold features conformal cooling. The two companies were able to laser etch the cavity, taking just three weeks from the initial design stage to the finished product.
In addition to the conformal cooling trough, Mantle’s print cavity can also use a substrate, allowing Westminster to cast thousands of parts without worrying about the highly filled and abrasive resin eroding the gate area, which is integral to using PA 11 material.
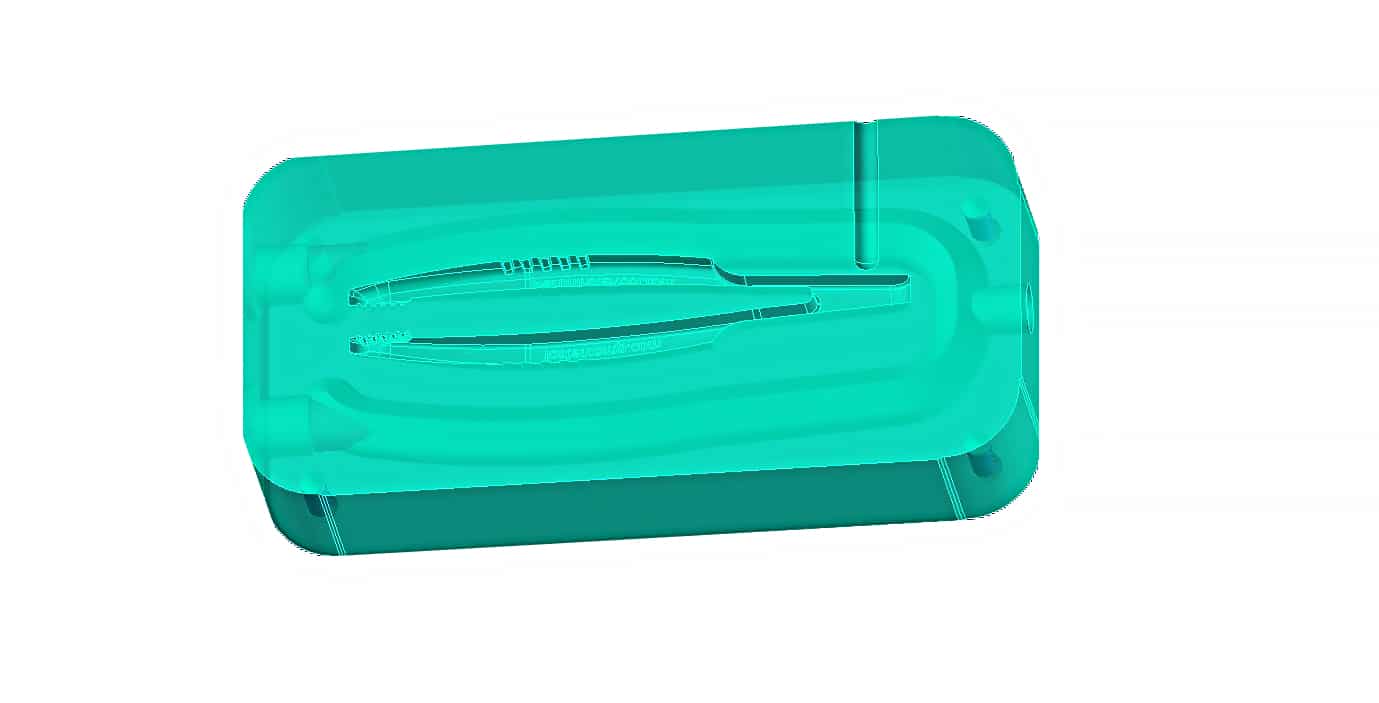
Mantle’s TrueShape printing system features 3-axis CNC machining, draw printing and
software
Design and other abilities. Comes with dedicated printing materials including H13 and P20 tool steels. The materials are housed in sealed cartridges and consist of metal particles and a toothpaste-like binder. The material is extruded in layers by the printer, then heated and dried. This cooks off the adhesive, leaving only the crayon-like sticky metal, which can then be machined.
The manufacturing process is quick, and molding parts in blue and black ABS plastic produces a smooth surface finish without the need for polished aluminum. Not only that, but the machine operator was impressed with how easily parts fell off the tool. “In the past, we had a lot of trouble with demolding in 3D printed plastic inserts,” says Wiriya.
The printed components are done in a sintering furnace, raising their temperature to just below the melting point of the metal. The resulting metal parts can be treated like any other tool steel and machined, welded, ground, polished, etc. TrueShape has a build area of 8 x 8 x 6 inches, and the largest part size is about 5 x 5 inches. Paul DiLaura, chief commercial officer at Mantle, said the3D printerThe optimal build size is 3 x 4 x 1 to 1.5 inches.
Through Mantle’s partnership with Wepco Plastics, TrueShape technology can advance the mold insert industry, which also features conformal cooling channels and a smooth matte surface finish suitable for molding, with a Ra surface roughness of only 1-3μm. There is another recent collaboration with Wepco Plastics (phone holder) where surface finish is often critical to quality.
(responsible editor: admin)
0 Comments for “Mantle announces partnership with Westminster Tool and other companies to jointly develop 3D printing molds”