● Is our QA process reliable and effective when parts are executed as designed?
● What is the cost to our business of out-of-spec parts?
● What opportunities are we missing because we cannot ensure the dimensional accuracy of the parts?
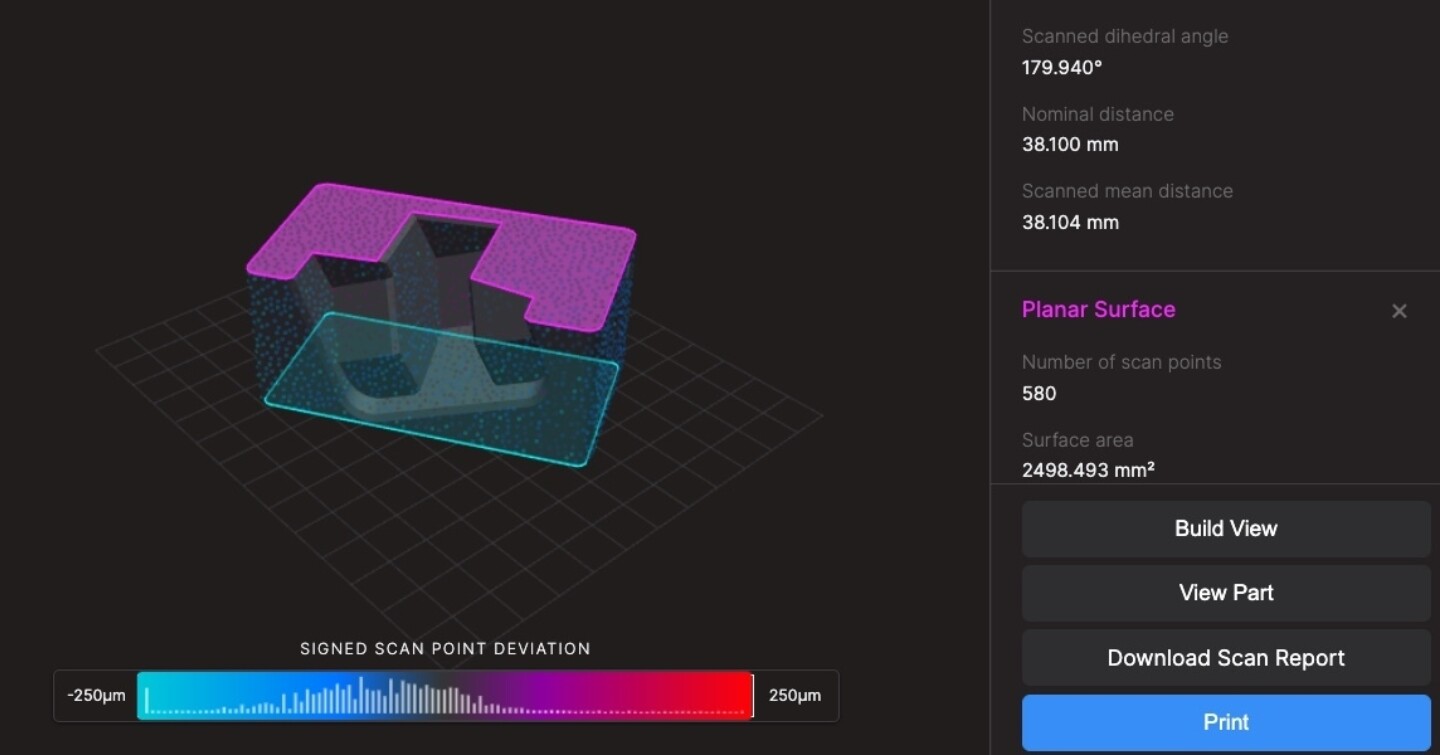
March 2021,
Markforged
To address these issues, the industry’s first automated control for digital manufacturing was introduced
software
, connecting part design, production and inspection with powerful artificial intelligence.This is a for inspection and analysis3D printingAutomation solutions for the exterior and interior of components. It replaces the often unreliable, expensive and time-consuming manual post-print inspection process. Guarantees that every printed part is the same quality every time, and wherever there is a Blacksmith-enabled X7 printer, without the need for a dedicated technician everywhere.
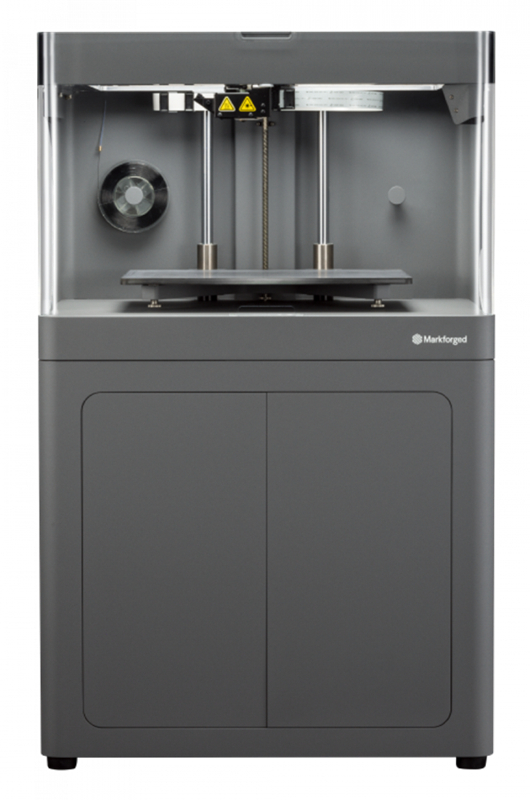
In January 2022, Blacksmith added two key improvements for clients.
Select different scan densities for different part features
At the launch, Blacksmith gave users the choice of low, medium or high density scans, which determined the resolution of the dots generated and used to compare the printed part with the designed part. This selection of scan density applies to the entire part. With the new Variable Scan Density, users can select an overall scan density and then visually identify one or more sets of features scanned at different density levels. For example, a high density may be chosen to examine and analyze a small complex feature, while a low or medium density may be sufficient for other features. This will allow users to balance the need for higher resolution scans and inspections with overall print and scan time requirements for higher part yields. It will also help Blacksmith get smarter as it learns from the data which part features are really important to customers.
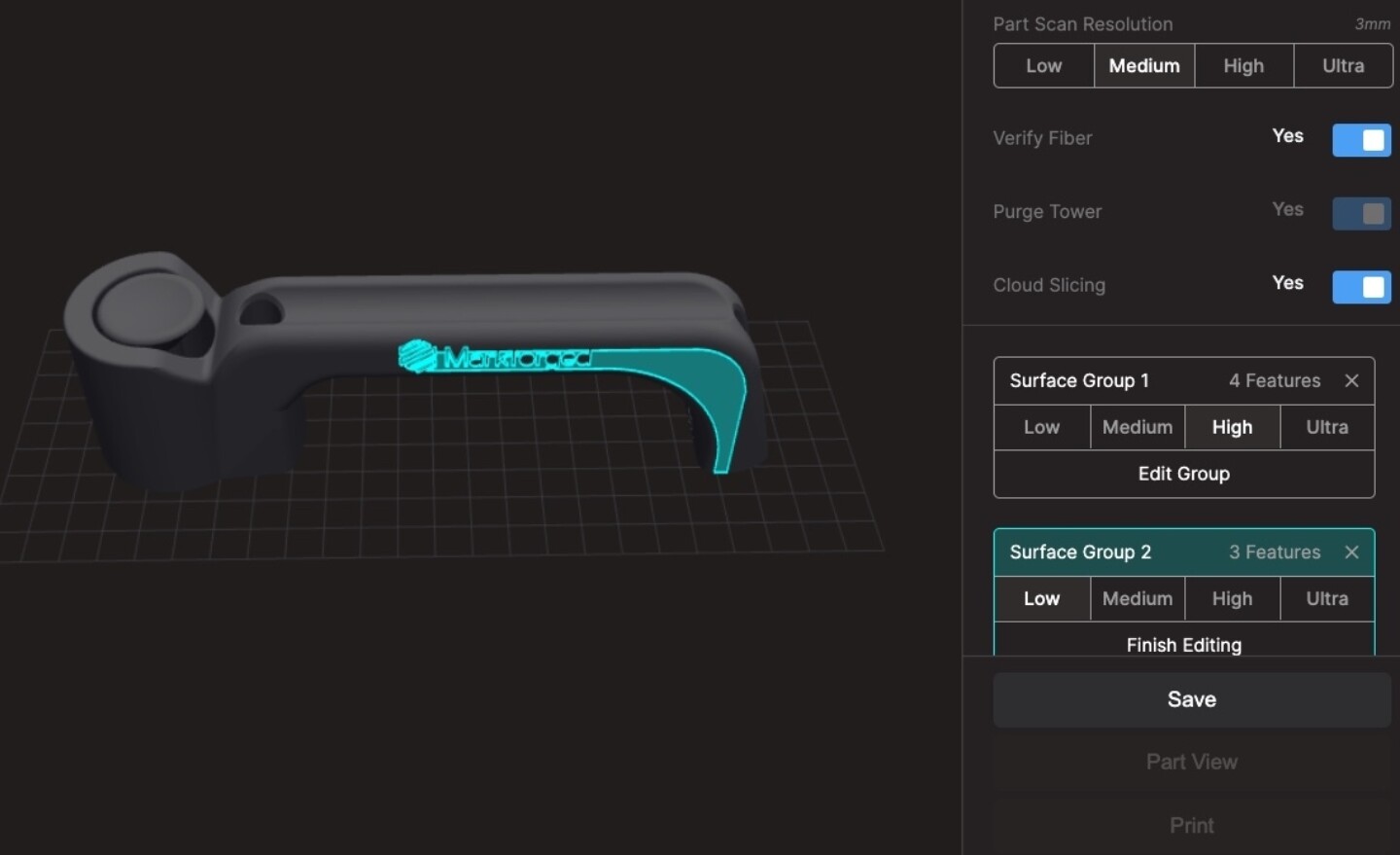
Validate fiber placement in the part
Blacksmith provides users with the ability to inspect many aspects of printed parts, including walls, planes, fills, and supports. For parts reinforced with fibers, users cannot check the accuracy of fiber placement in the part with Blacksmith. With the new Fiber Placement Verification, users can now automatically check the accuracy of carbon fiber placement in a part and get a visual indication on the Project Details panel that fiber placement has been verified. Previously, if customers needed to inspect parts for internal features and fibers, they had to use very expensive inspection equipment, such as CT scanners, or disassemble a large number of parts to do statistics. Blacksmith’s non-destructive part inspection saves customers time and money.
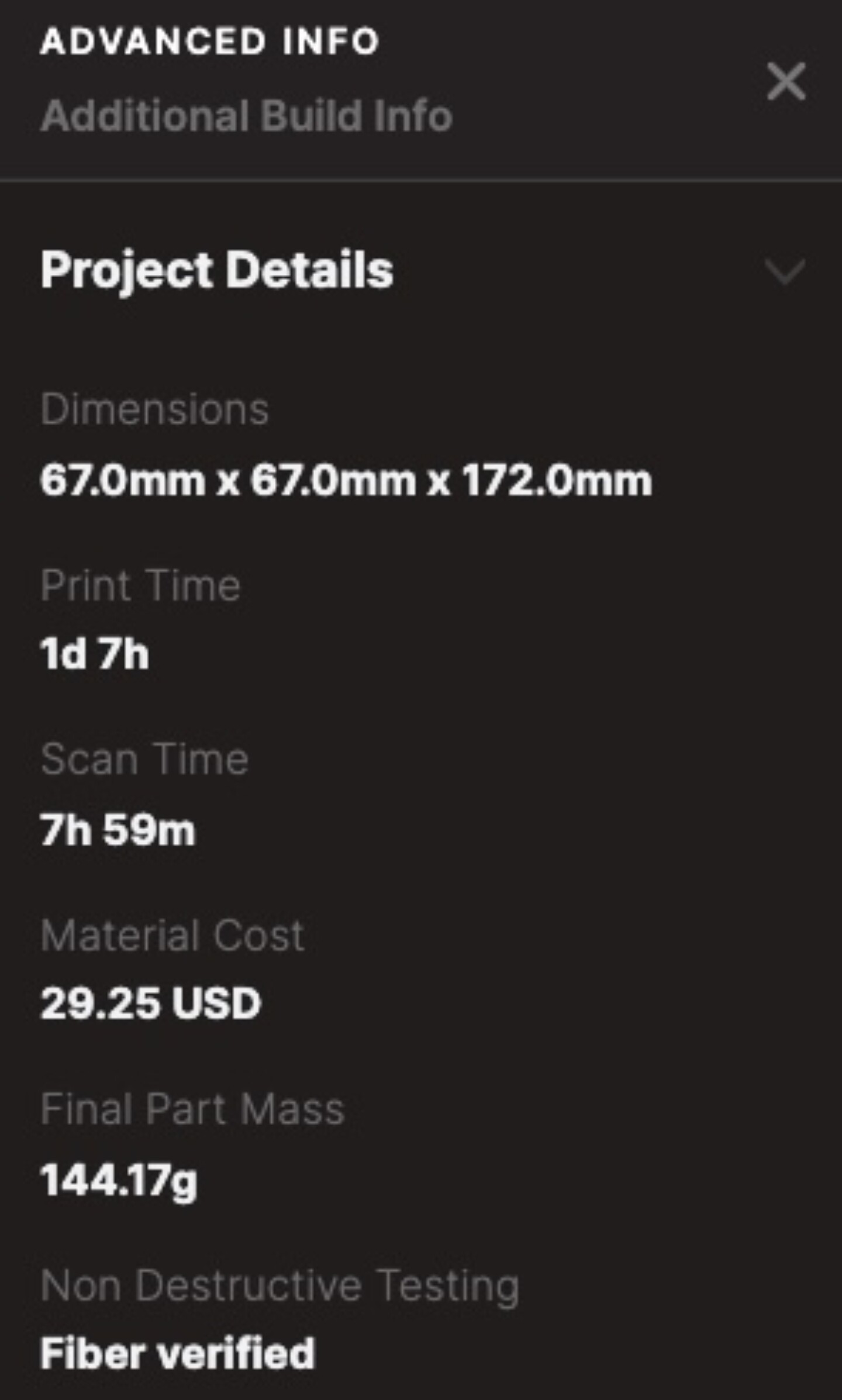
Blacksmith has been continuously updated with new features over the past 10 months, and here’s a review of the 2021 updates.
● Diverse feature detection–detect various types of part features, including flat, spherical and cylindrical surfaces
● Custom Feature Measurements – select one or more features and view various measurements on screen
● Quality Report – Download a PDF report with part scan data and images
● 3D parts – easier to understand measurements with on-screen lines connecting surfaces and measurements
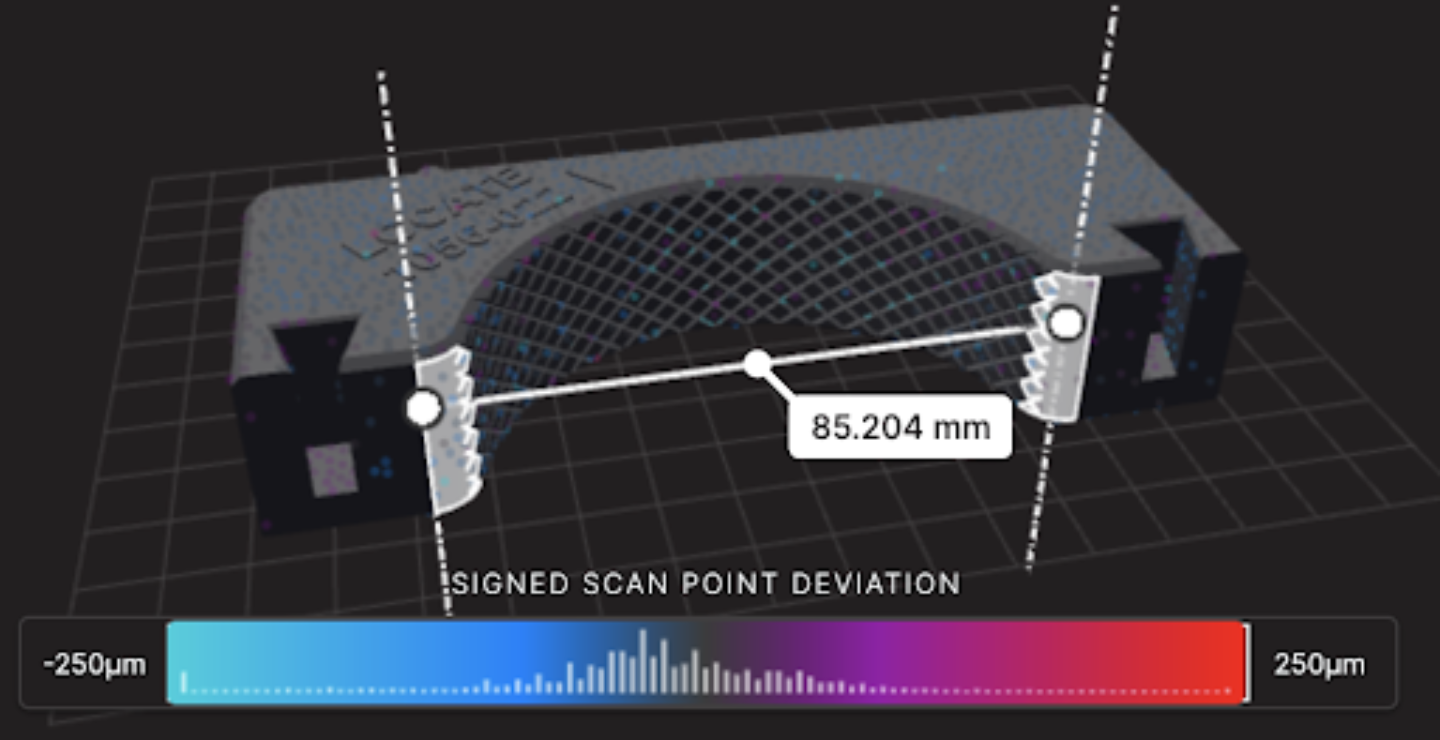
(responsible editor: admin)
0 Comments for “Markforged’s digital manufacturing automation software Blacksmith releases two key updates”