The colloid processing group of the Spanish National Research Council (CSIC) uses COLFEED4Print’s printing technology on a daily basis to manufacture innovative products.They are currently focusing on a number of areas, including developing
biology
compatibility3D printingSilk achieves bone and tissue regeneration.
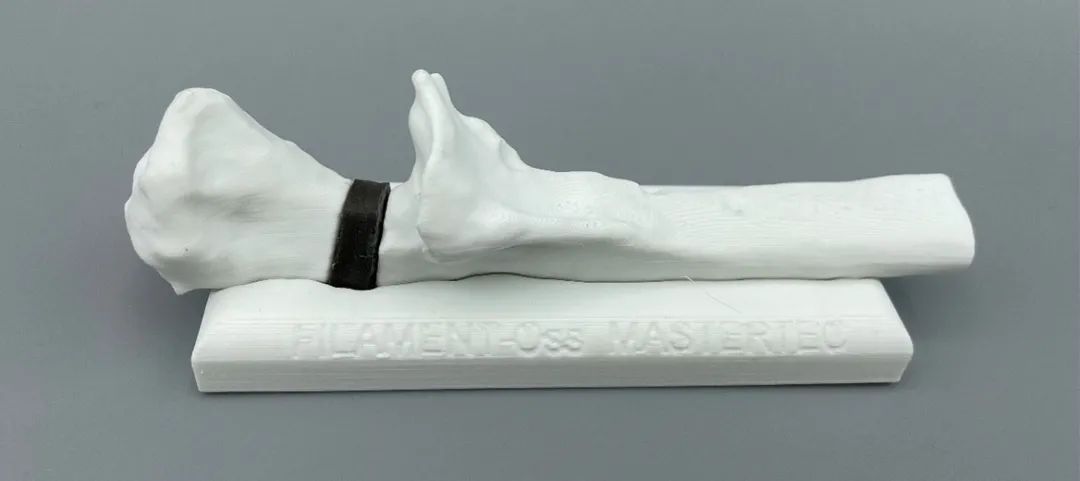
The future of R+D+I: Oss osteoinductive wire in innovative cases
Osteoinductive Oss is a biodegradable polymer filament containing highly dispersed bioactive components (TCP, HAp, Mg, etc.)3D printingIdeal for customized bone and tissue regeneration.
The main advantage of such filaments is that they can combine different properties.Such as biodegradability, biocompatibility or antimicrobial effects for transplant needs – such as UV disinfection and custom porosity, these properties make in vitro cell culture and
clinical
Ideal material for in vivo studies.
Thanks to the ability to print experimental advanced 3D filaments in a controlled environment,
medical
The application provides essential surface precision, and MakerBot METHOD and LABS equipment were used to print this biodegradable filament. In this case, Oss filaments were used as a graft solution after partial resection of the patient’s elbow. Throughout the process, we can see that for this type of application, the raw materials used are just as important as the controlled production process.
Regeneration of ulnar nonunionOperationprocess
In this theoretical case, a patient with an osseointegration plate noticed problems moving the elbow. Doctors perform CT scans of the affected limbs so that 3D images can be used to examine why the elbows are not bending properly.
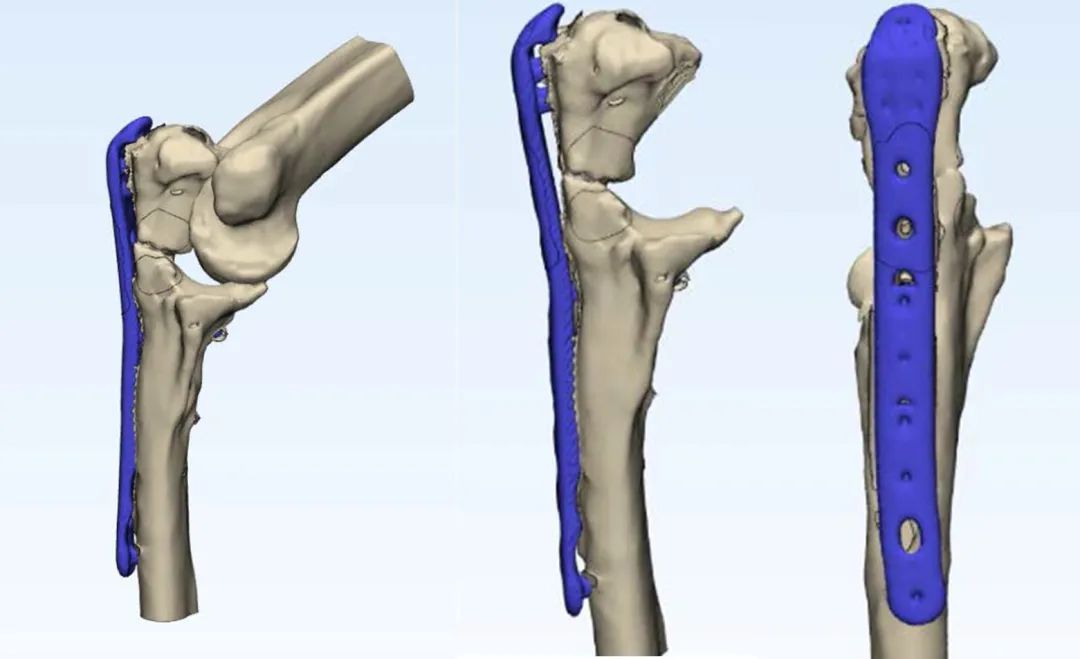
To ensure that the optimal solution was found, the doctor also performed a CT scan of the healthy limb, mirror-inverted the image, and then superimposed the two image results. In this way, the elbow of the affected limb can be compared with the healthy limb.
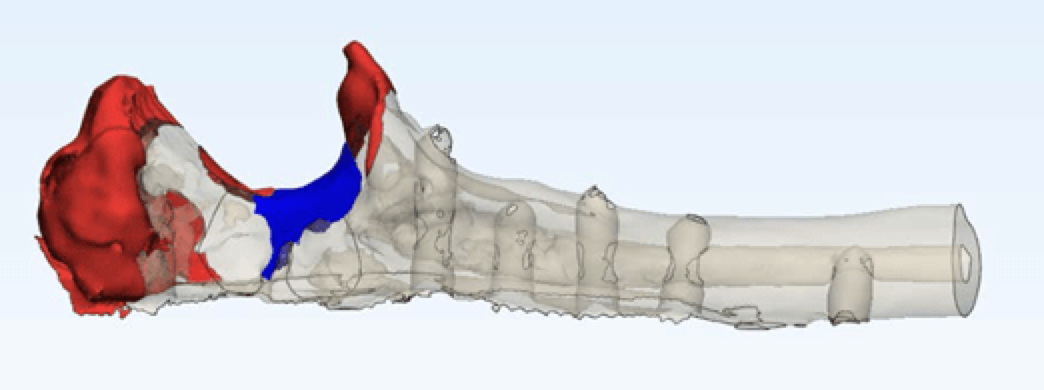
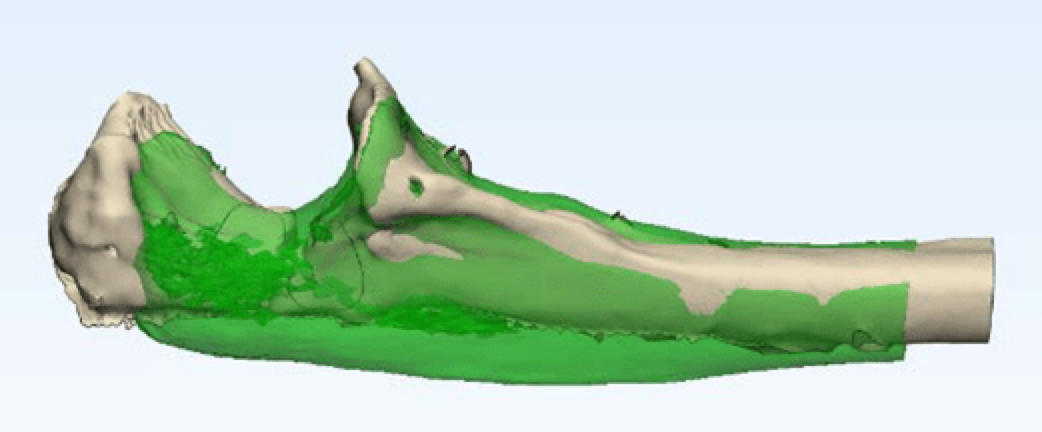
A comparison of the two images revealed that there should be no bone in some areas of the affected limb and no bone in others. So doctors decided to perform an osteotomy (removing the unhealthy part) and replace it with a bone graft.
So far, the operation process of the patient’s real case has been explained. After the decision to undergo an osteotomy is made, the doctor intervenes, manually correcting the deviation, and performing a bone graft for the patient.Implants are ground to size in the operating room, therefore, during the intervention
surgical
The doctor must grind the bone to perfectly fit the patient’s desired shape.
Using 3D printing and biocompatible filaments—in this case Oss filaments—the implants can be printed before the surgeon enters the operating room. As long as the correct 3D equipment is used, the shape and size of the implant will be completely accurate.
The image below shows a 3D printed implant made using a MakerBot METHOD LABS printer:
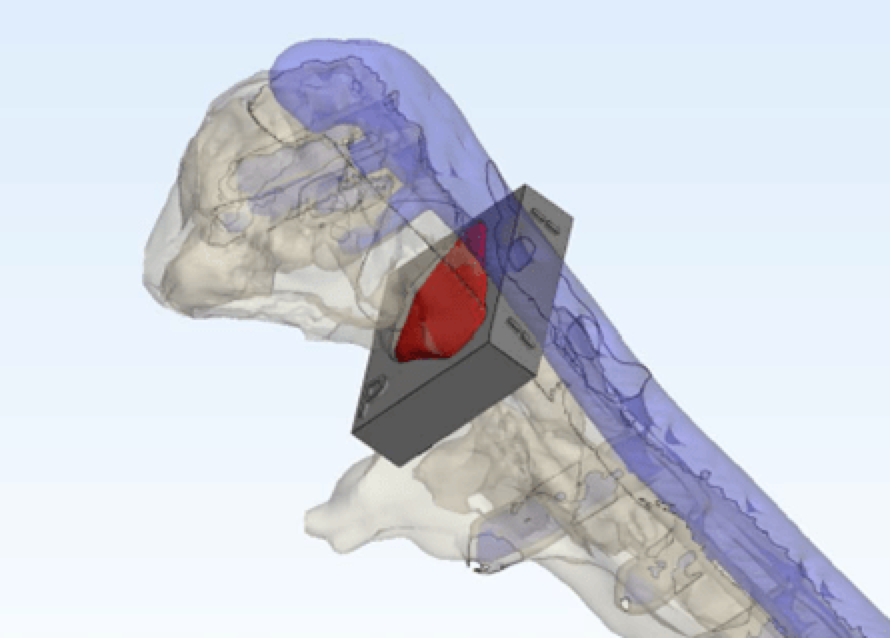
The results show that the finished surface quality is excellent. Even though this is a completely new ingredient filament, the MakerBot team has achieved the best results.
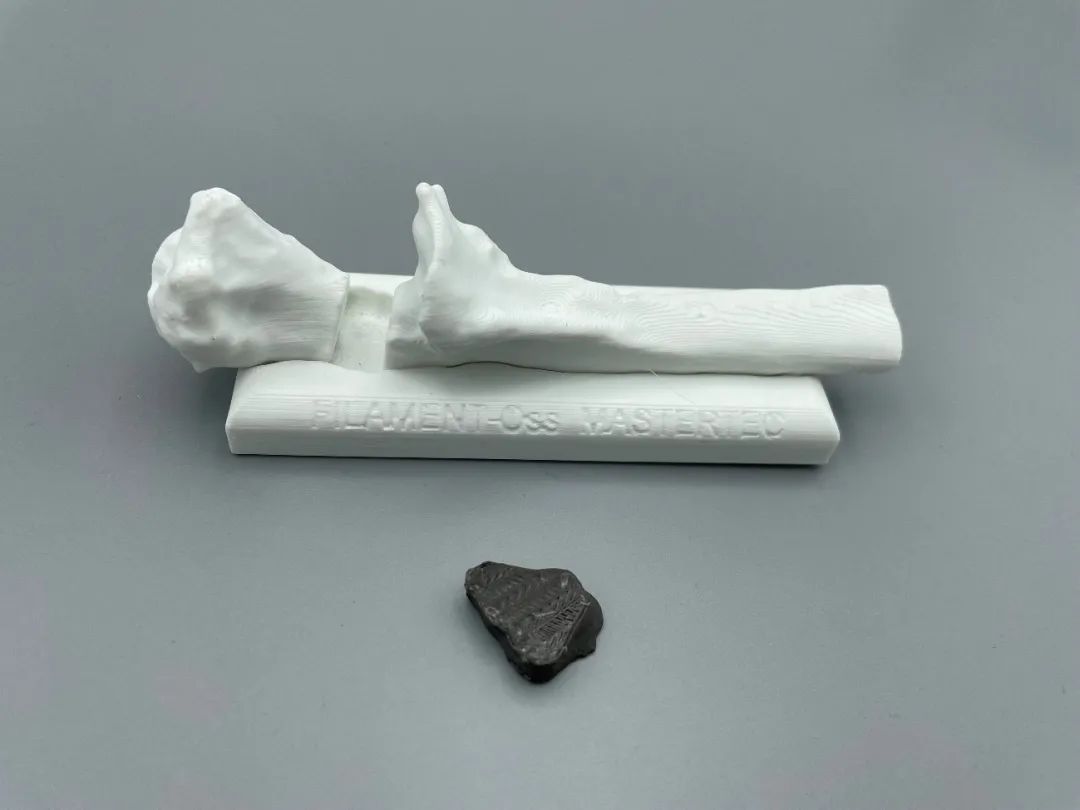
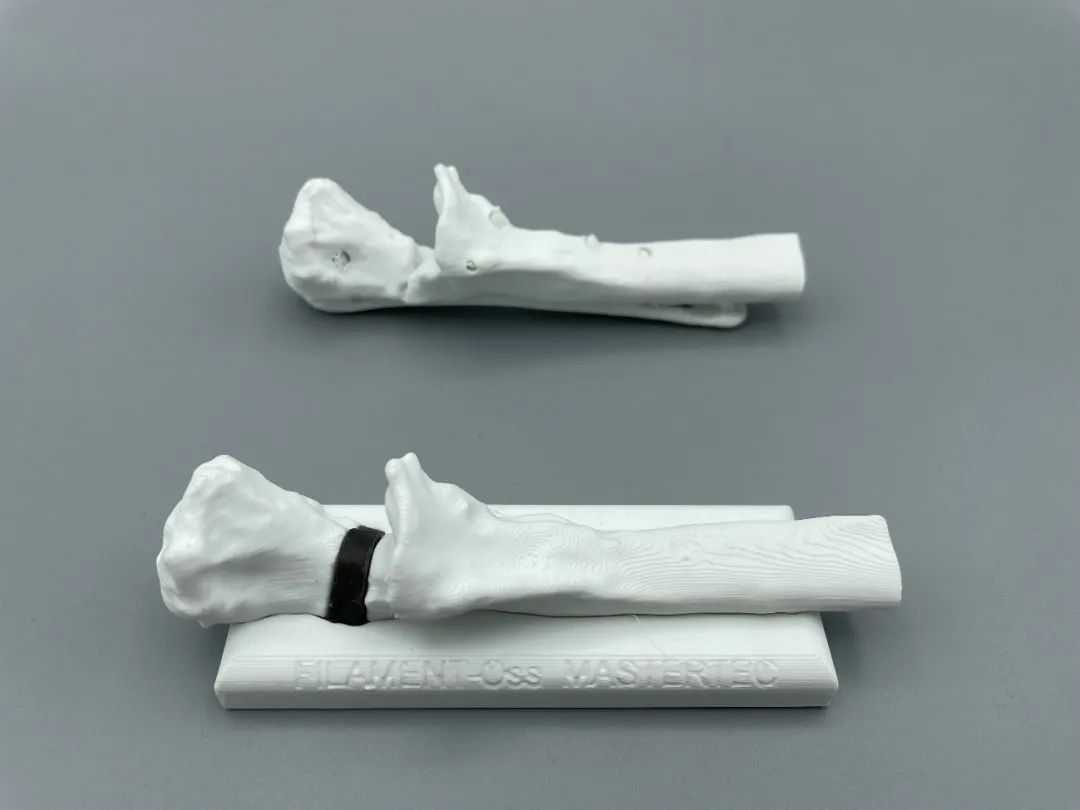
Personalized medicine is the future of healthcare. It is able to provide customized solutions that can guarantee better results and reduce the number of reinterventions.However, it is important to keep in mind that in
medicine
field, any solution must be safe and controllable. During research, it is also important to ensure the repeatability of the process in order to draw correct conclusions.
COLFEED4Print is a pioneer in the development of 3D filament for innovative applications, and MakerBot’s equipment provides the ideal 3D printing solution for such innovation-focused businesses.
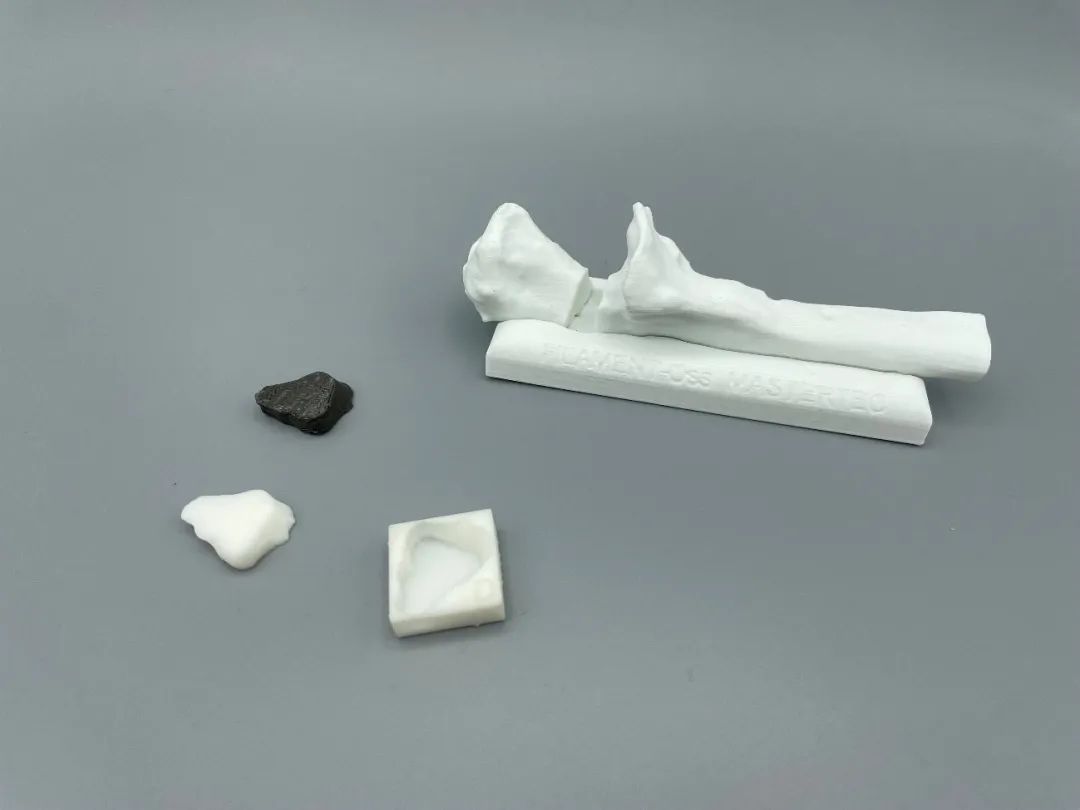
MakerBot METHOD, equipment for research
When researching and developing new applications or products, the repeatability, reliability, and accuracy of experiments must be ensured. Conducting research using incorrect methods may lead to inaccurate findings or conclusions. A similar situation occurs in the study of 3D printing, because there are many variables that most devices do not take into account, such as the printing environment and the state of the printing filament.
The ability to control the printing environment is essential in the development and testing of new materials. The MakerBot METHOD LABS is the only desktop printer with a heated chamber. Its heating chamber controls the temperature of the previous printed layer, which facilitates better layer-to-layer fusion. 3D devices with heated surfaces experience temperature gradients as the number of layers printed increases, resulting in non-constant and uneven layer-to-layer fusion. As a result, a controlled environment in 3D printing improves repeatability and enables more stringent and precise printing.
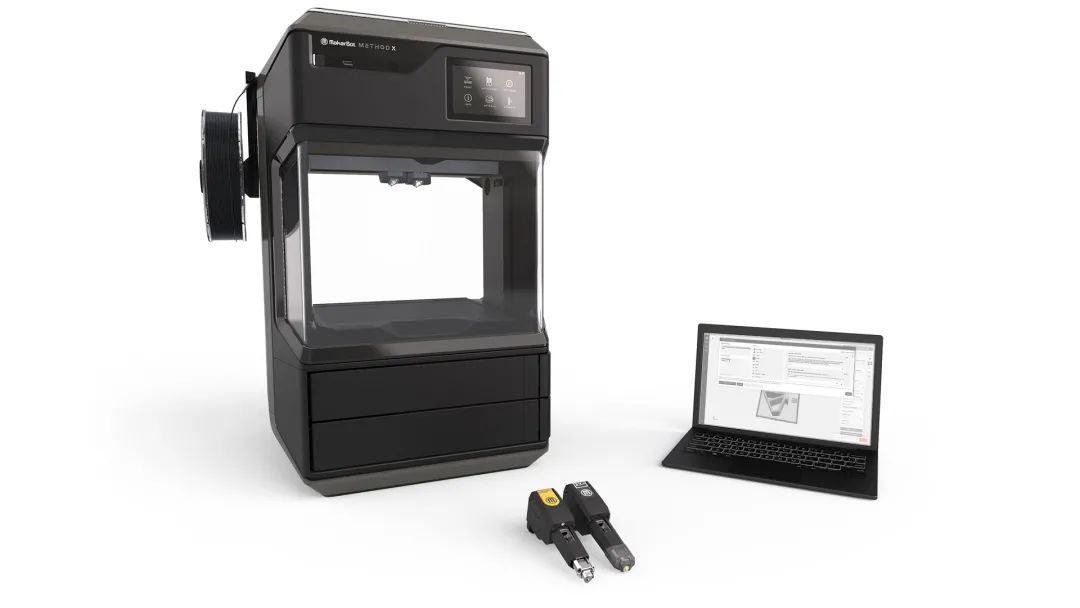
LABS Ecosystem
In addition, MakerBot equipment has extruders designed for experimental materials, and a one-piece, extra-long nozzle allows for better control of extrusion and retraction.Its gear system produces 200 Nm of torque and squeezes out the highest
standard
of wire. On the other hand, MakerBot 3D printerThere is also an air filter to deal with harmful particles emitted by the material.
These make MakerBot 3D printerThe ideal tool for developing and printing innovative products and materials.
(responsible editor: admin)
0 Comments for “METHOD 3D Printer and LABS Labs to Develop Bone-Friendly Biocompatible Materials for Elbow Implants”