The metal lattice structure has been widely used in various industrial fields due to its excellent properties such as low elastic modulus, high stiffness-to-weight ratio, low thermal expansion coefficient and large specific surface area.
Recently, Professor Zhang Laichang from Edith Cowan University in Australia and Associate Professor Chen Liangyu from Jiangsu University of Science and Technology jointly published an online publication entitled “Additive manufacturing of metallic lattice structures: unconstrained design, accurate fabrication,” in Materials Science and Engineering: R: Reports (IF=36.214). fascinated performances, and challenges” review paper, which systematically traces the traditional manufacturing methods and new additive manufacturing methods of metal lattice structures, expounds the design, optimization, performance and application of additive manufacturing metal lattice structures, and Based on the current research results of the metal lattice structure of additive manufacturing, its limitations and future development directions are discussed.
Paper link:
https://www.sciencedirect.com/sc … i/S0927796X21000437
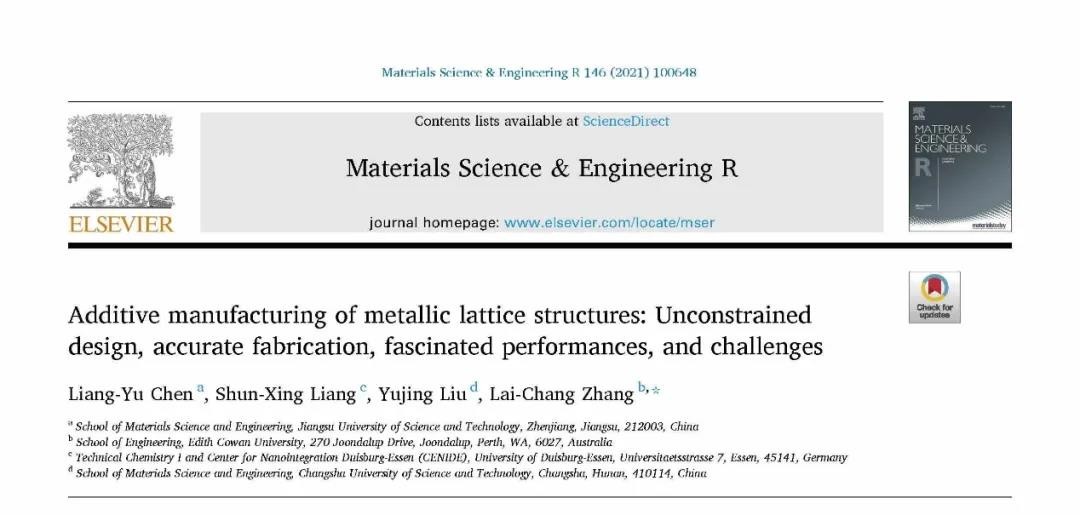
The traditional manufacturing methods for preparing metal lattice materials usually include foaming technology, precision casting, metal wire weaving technology, powder metallurgy, electroplating and so on. These preparation methods often involve complicated process control, additional assembly steps or other uncontrollable factors. For example, although traditional foaming technology can quickly manufacture porous structures, it cannot precisely control the pore distribution and pore size; precision casting technology can well control the complex structure of the metal lattice, but it cannot achieve the preparation of fine structures; metal wires Although the weaving technology can weave the metal lattice structure according to the designed pattern, the connection between the metal wire nodes requires additional processing, so it is difficult to achieve large-scale industrialization, and the patterns that can be used for design are also very limited.
Additive manufacturing technology, commonly known as3D printingTechnology is a combination of computer-aided design, material processing and molding technology, based on digital model files, through
software
With the numerical control system, the dedicated materials are piled up layer by layer according to the methods of extrusion, sintering, melting, light curing, spraying, etc., to produce the manufacturing technology of physical objects.3D printingTechnology is different from the traditional processing mode of removing, cutting, and assembling raw materials. It is a “bottom-up” manufacturing method through the accumulation of materials, starting from nothing. This makes it possible to manufacture complex structural parts that were restricted by traditional manufacturing methods in the past. The additive manufacturing technologies commonly used to prepare metal materials include powder bed fusion technology, direct energy deposition, fused deposition molding, layered solid manufacturing, direct writing molding technology, adhesive injection, and so on.
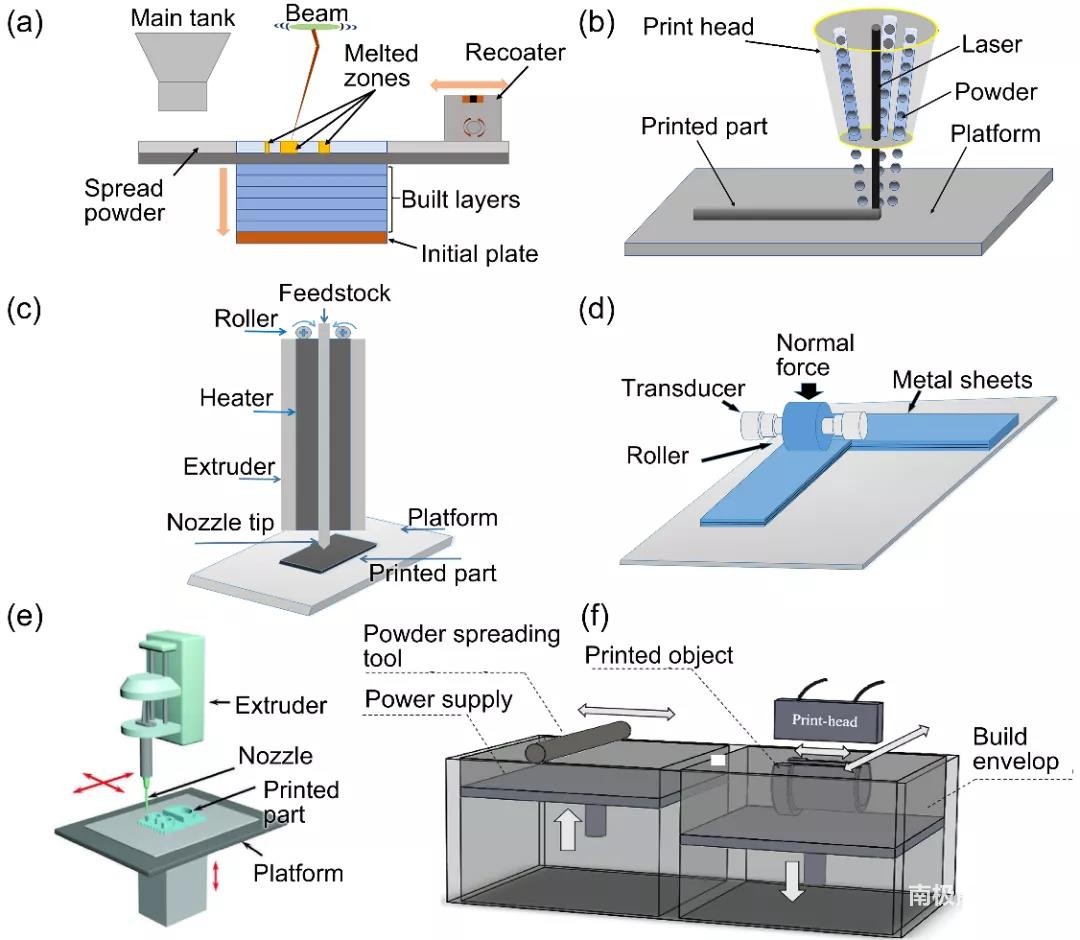
In the past, although many complex lattice structures with potentially excellent properties could be designed, their manufacturing was still limited by traditional methods. Fortunately, due to advanced manufacturing capabilities, the development of additive manufacturing technology has in turn promoted the design of more complex structures, and the design goals have also changed from the original manufacturability to functionality. From the perspective of structural design, the lattice structure is a collection of unit cells that repeatedly appear in a certain space. Therefore, in the design of the lattice structure, both the unit cell design and the overall pattern design must be considered.On this basis, proceed
Topology Optimization
In this way, a lattice structure with excellent performance can be obtained. For the design of the unit cell, it mainly includes three kinds of unit cells: rod base, shell base, and triple curved surface.
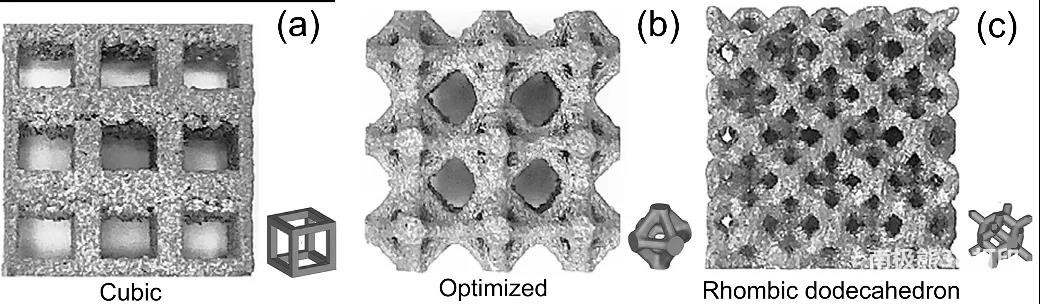
In general, the performance of the metal lattice structure is mainly determined by the configuration of the unit cell, the porosity, the types of materials used, and different additive manufacturing technologies. The design and manufacture of metal lattice structures with different properties can play a role in different industrial fields.For example, a metal lattice structure with a low elastic modulus can be applied to
biology
Medical
orthopedics
Implants
; The metal lattice structure with higher rigidity and energy absorption capacity is suitable for lightweight structural design and energy absorber; the metal lattice structure with higher specific surface area is suitable for the carrier of catalytic structure. And there are other industrial applications.
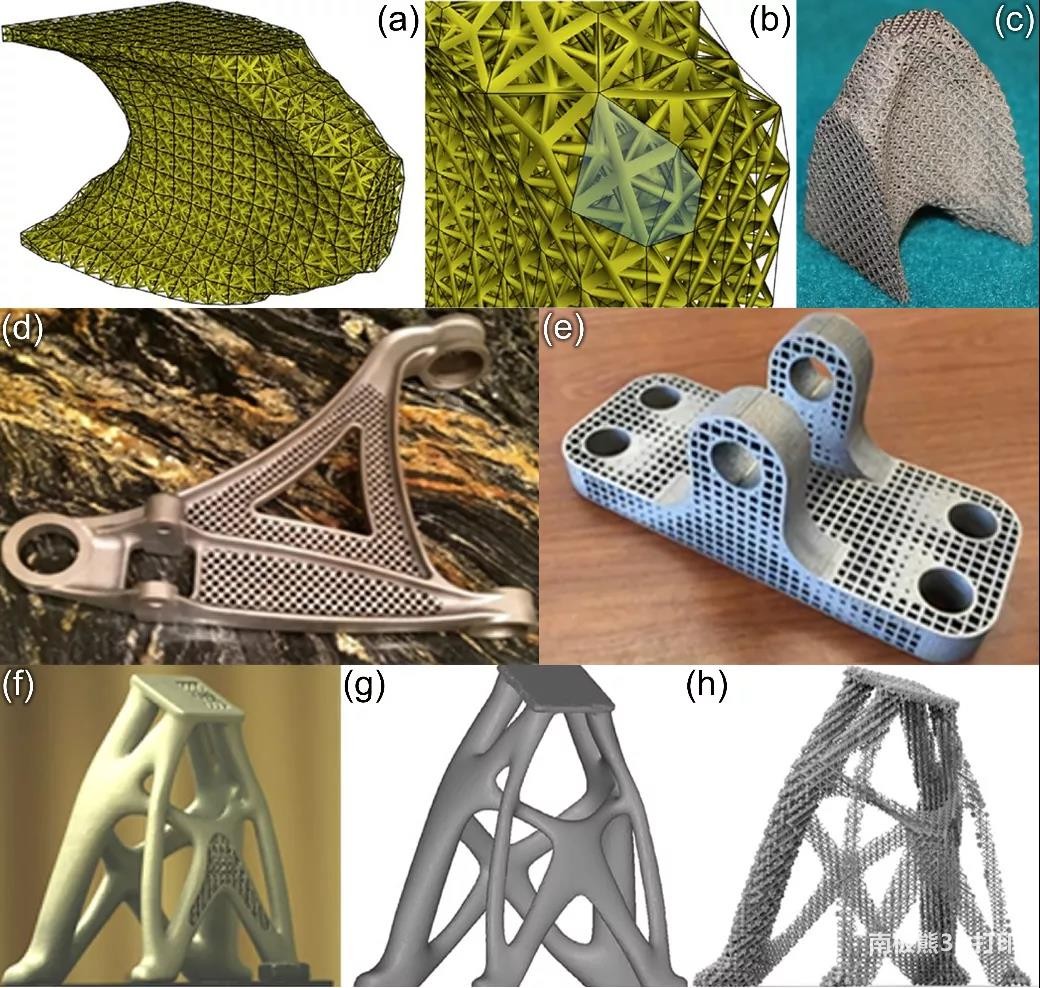
However, additive manufacturing technology is not a panacea, and there are still some limitations and challenges in preparing metal lattice structures. For example, the crystal lattice structure of the metal prepared by additive manufacturing has a high surface roughness, and the surface roughness needs to be reduced before it can be put into use; the powder bed melting technology usually needs to be processed in a specific atmosphere cavity, so the processed workpiece generally has a small volume. The precision of direct energy deposition and fused deposition is slightly lower, and the processing fine structure is slightly insufficient; the metal lattice structure often requires surface treatment to have better surface functionality, but due to the complex structure of the metal lattice, it has not yet been Targeted surface treatment technology.
In the past ten years, the combination of metal lattice structure and additive manufacturing technology has received more and more attention. In order to ensure the reliability of the metal lattice structure prepared by additive manufacturing technology in various industries, the relationship between its modeling, optimization, materials, process parameters, structure and performance still needs to be further understood.
(Editor in charge: admin)
0 Comments for “MSER (IF=36.214) Top Issue Review Paper: Additive Manufacturing of Metal Lattice Structure”