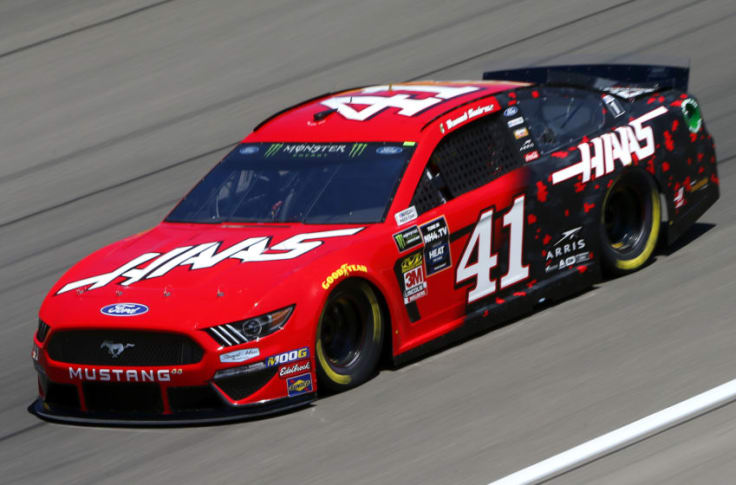
Walter Mitchell, engineering integration manager for the Stewart-Haas fleet, said: “The ability to use Autodesk’s generative design and Renishaw’s metal printing capabilities will open doors that were previously impossible to achieve with traditional manufacturing methods. This will improve performance and improve performance. Speed, reduce the lap speed.”
Like any motorsport, NASCAR is all about subtle
profit
And the team pushed their design to the absolute limit of the sports rules to gain a competitive advantage.The Stewart-Haas team’s cars are currently ranked 10th, 23rd, 24th and 28th in the championship. The team adopted3D printingThe purpose of technology is to develop upgraded products and improve the ranking of drivers.
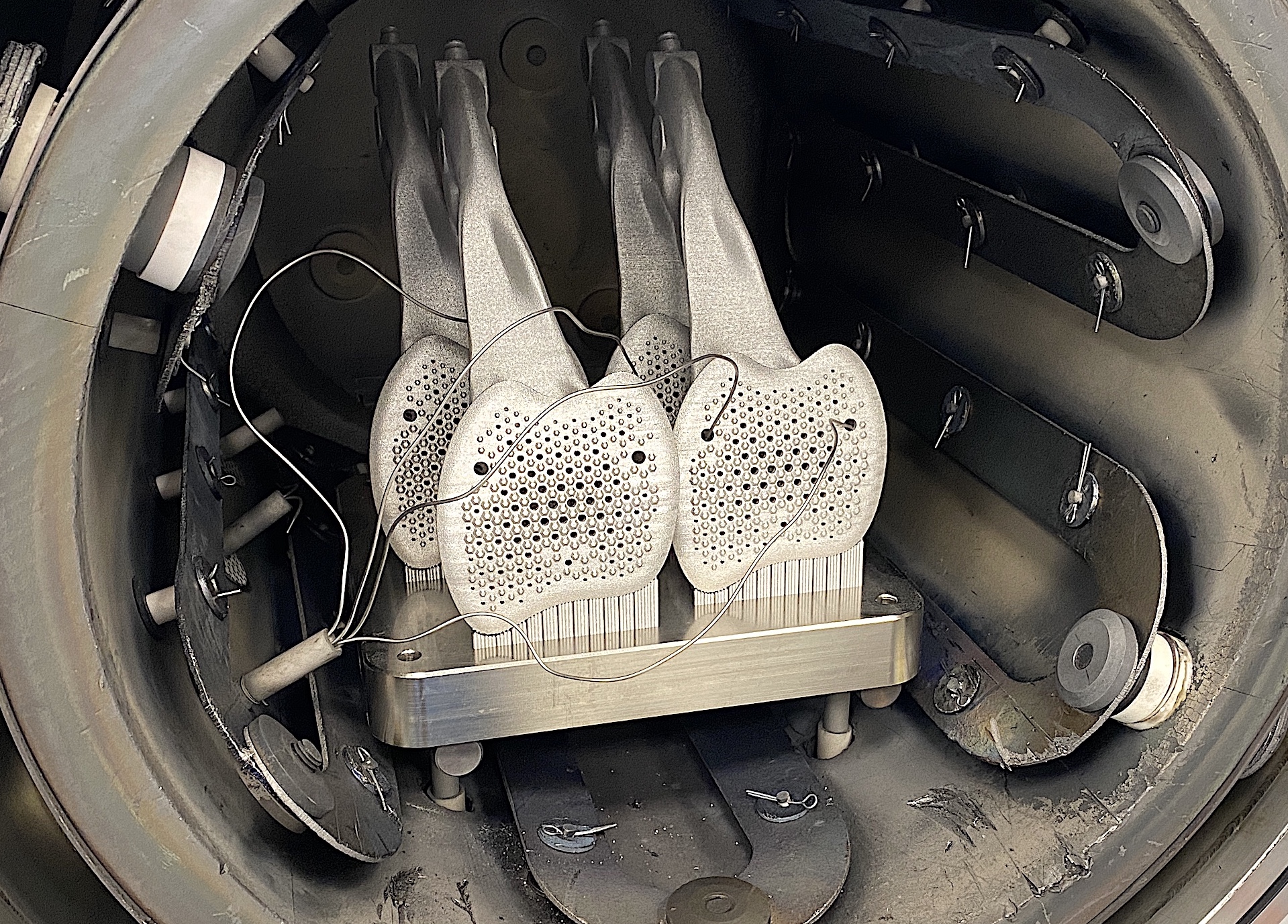
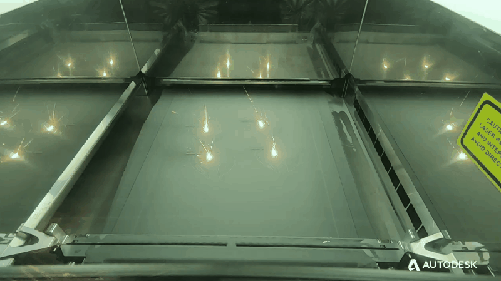
Grau concluded: “Initially we spent a day creating a cell. Two weeks later, we were able to create 30 cells in 30 minutes, but the computer crashed several times. After six months, we could create a cell in a few minutes. Complete the design of the entire lattice. If you look at our history and our work, the progress we have made is almost exponential.”
use3D printingBreak through barriers
carManufacturers are increasingly turningTopology OptimizationAnd generative design, as the development of end-use3D printingA means of parts.Just last year, Fraunhofer IAPT worked with Fiat Chrysler Automobiles’ engineers to integrate 12 parts of a sports car into a single3D printingAmong the suspension parts, its weight is 36% lighter than the original.

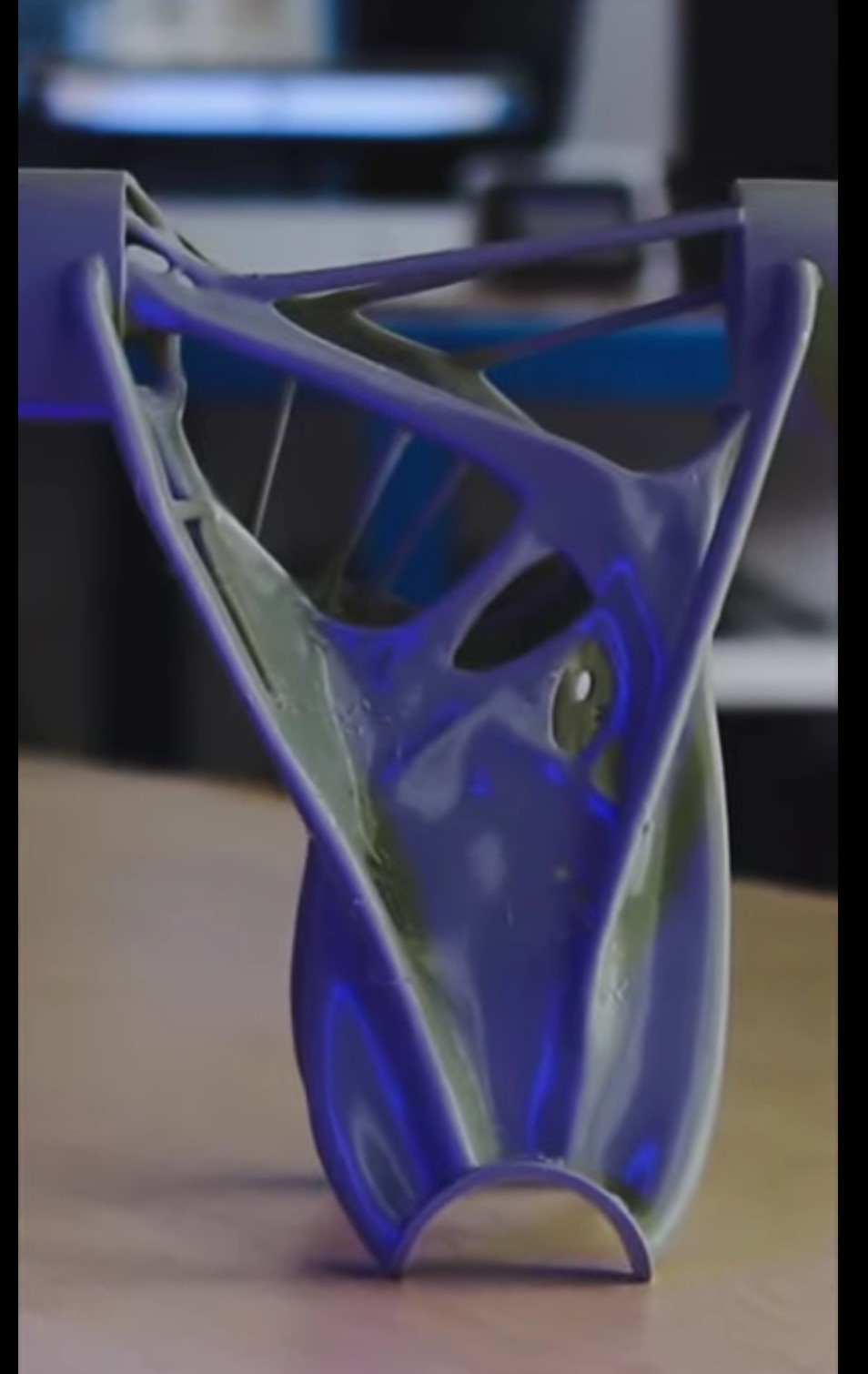
Specific to the brake system, in the past few years, some car companies have tried3D printingIdeas for related parts. In July 2019, CarbonPerformance used its proprietary SK3L370N platform to3D printingBrake calipers, Bugatti soon managed to achieve a similar goal, using the SLM 500 system to produce titanium calipers.
(Editor in charge: admin)
0 Comments for “NASCAR team uses 3D printed titanium alloy brake pedals to reduce weight by 32%”