Additive manufacturing (AM) has historically been limited to the manufacture of low-volume, high-cost, or high-complexity parts. This has been a roadblock to wider adoption of AM in production, and the reason seems to be good. From a purely direct cost perspective, low build rates often result in equipment accounting for more than 50% of production costs.The effort and time invested in preparing for AM assignments and the laborious
post-processing
The requirement further narrows the window in which additive manufacturing makes economic sense.
Nexa3D
is an additive manufacturing solutions company with a complete set of mature technical solutions for each stage of the photopolymer additive manufacturing process. With higher print speeds and a larger 16-liter (61-cubic-inch) build chamber, Nexa3D says they can print 6.5 times faster than comparable printers, but that’s still nowhere near the 20x productivity boost claimed in the title Far.
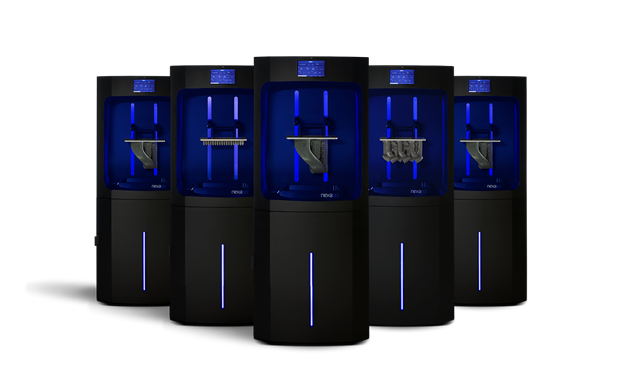
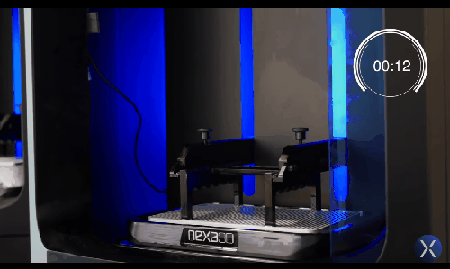
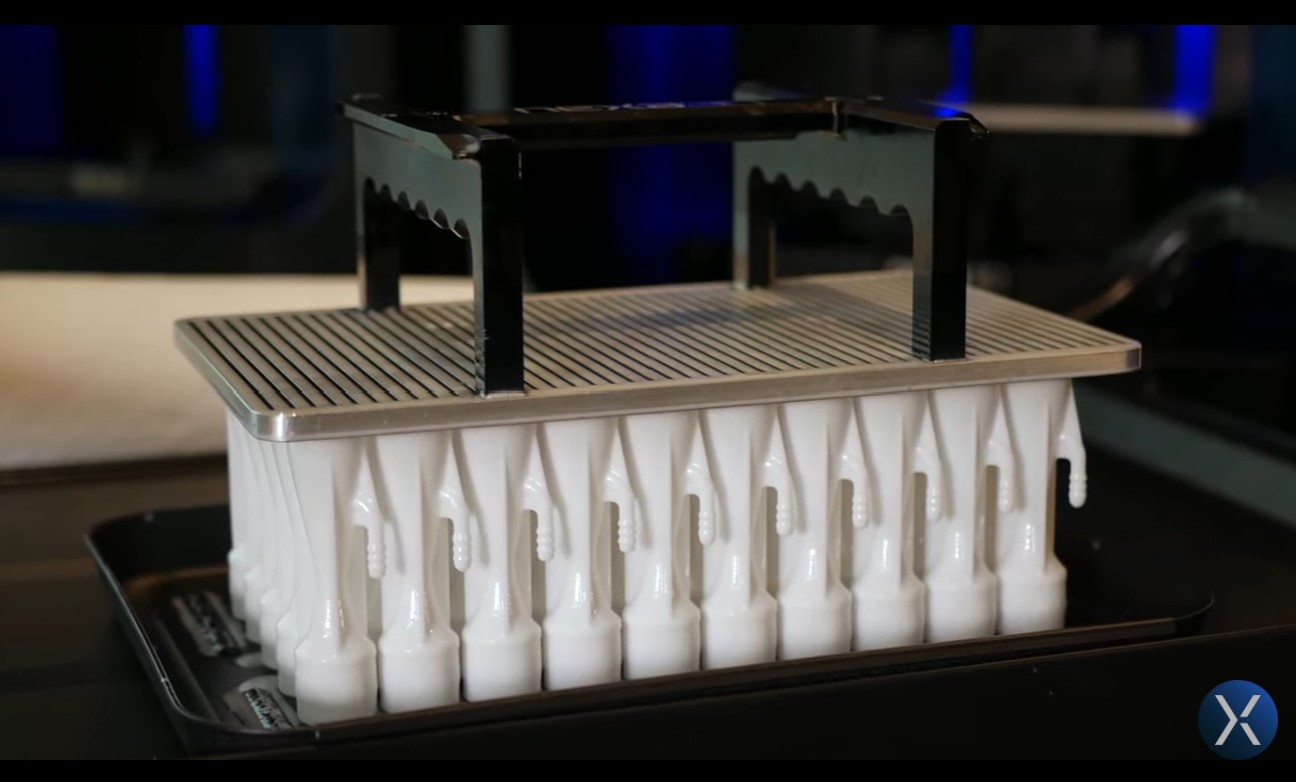
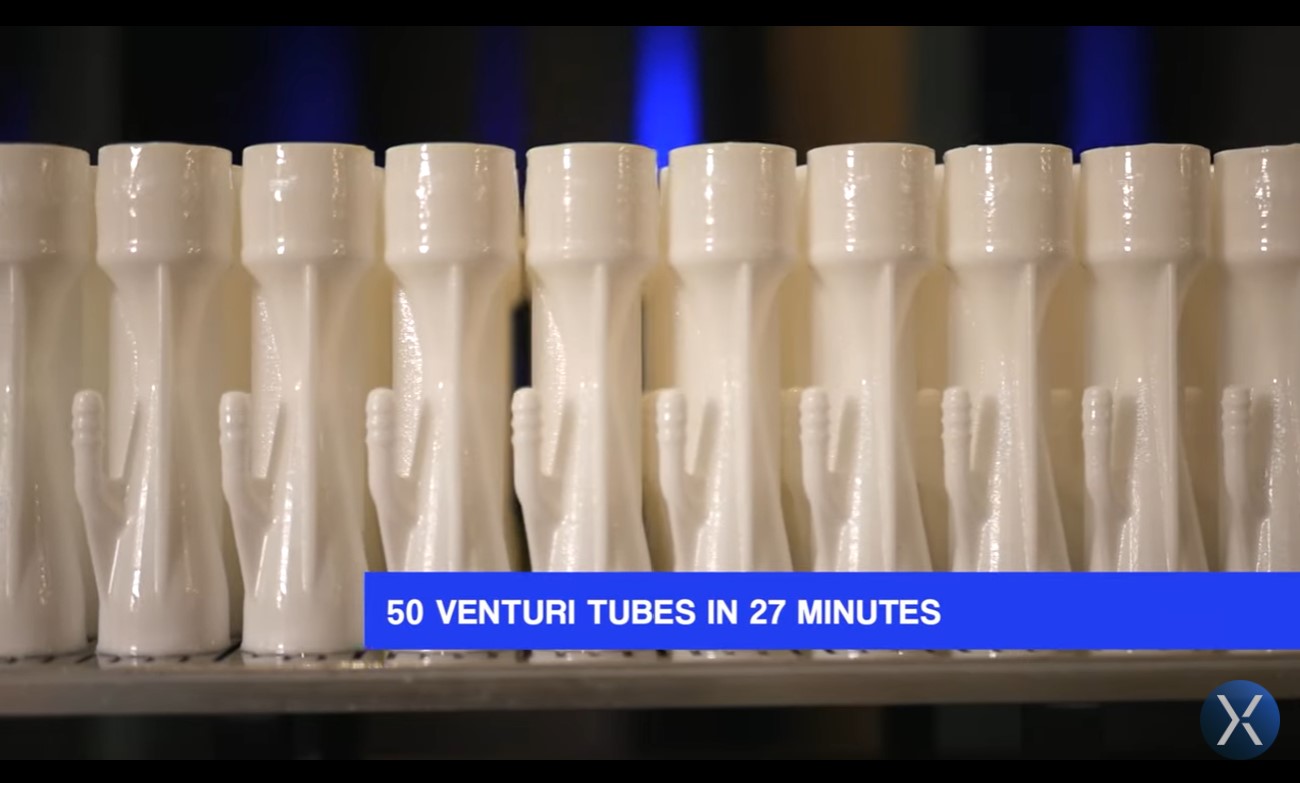
Economics in Additive Manufacturing
depreciation of capital – this includes3D printer, but also any necessary post-processing equipment. Capital utilization is directly affected by the speed and size of the printer, which determines the number of parts that can be produced in a day.
Material cost – The material cost of AM often requires a different calculation method than traditional manufacturing. Initial material costs may be higher, but yields are usually higher and scrap is low. However, some AM processes have hidden material waste processes, which may depend on material properties, production geometry and post-processing methods used.
Labor Costs – AM operations include document preparation, machine loading/unloading, and post-processing.Labor costs depend heavily on equipment productivity, hardware and
software
automation and specific post-processing requirements for each part.
Improving AM productivity involves addressing each of these issues.For example, a faster and more predictable build program preparation process can reduce labor, make jobs run faster, and can reduce the cost of achieving desired quality
standard
difficulty. Faster printing and the ability to manufacture more parts at a time increase equipment utilization. The ability to print more accurately and predictably, can greatly reduce post-processing costs through more efficient support removal and possible elimination of secondary processing (such as machining). All of this adds up, and doing it all right is the way to achieve huge improvements in 3D printing productivity.
The ability to design and manufacture more complex parts is perhaps the most discussed economic benefit of AM, as it is able to replace an assembly with a printed part, and these cost benefits can be substantial. But selecting the right parts for AM and getting those parts into an efficient production process quickly is another matter, because how you go about preparing the build program is critical.
It all starts with AM software. NexaX 2.0 is an AI-based software application that provides print preparation and 3D printer management through the interaction of hardware, software and chemistry. With the integration of the API with other software, NexaX enables new properties of printed parts while achieving process stability, production scale, consistent product quality, higher yields and outstanding mechanical properties. It provides a variety of tools to help improve overall process efficiency, such as quick document preparation, how to stack parts for maximum yield, and even how to place supports for easy disassembly.
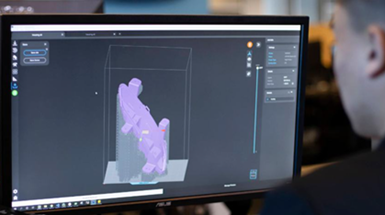
With exceptionally fast proprietary slicing algorithms and automated support generation, NexaX software combines process and geometry algorithms with an end-to-end workflow to optimize part production. The software includes a wide range of automation features, including:
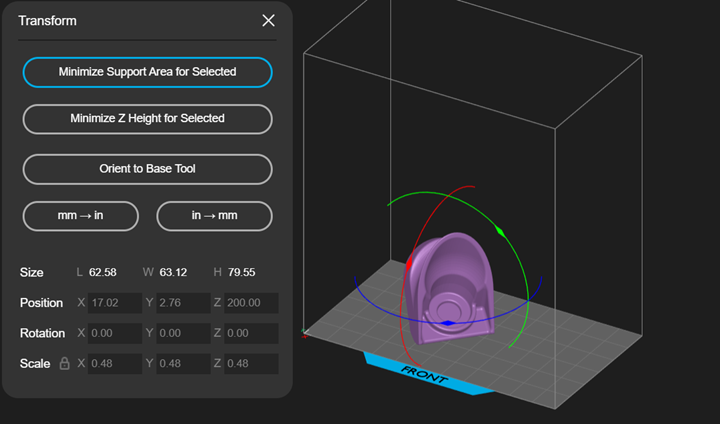
NexaX 2.0 software is also fully compatible with Ximplify™, Nexa3D’s automated 3D printing decision support portal that accelerates the ability of designers and manufacturers to adopt additive manufacturing at scale. Ximplify scans bills of materials consisting of thousands of parts in minutes to select ideal candidates for additive manufacturing. It identifies breaking points where 3D printing can match or exceed the production costs of other process alternatives, and can make recommendations on when it is appropriate to work with a service bureau and when it is appropriate to produce in-house. The software also includes seamless integration with Nexa3D’s large and growing material portfolio, and can even suggest material alternatives for any given part.
The photopolymerization process of Nexa3Ds is very fast, and it is based on LSPc technology (Lubricant Sublayer Light Curing), which greatly speeds up the time from one layer to another. SLA printers are “inverted”, which means they print upside down, and they cure against a barrel bottom or barrel film. In the Nexa 3D printer, light is projected upward through channels and light guides to ensure uniformity across the build area. The light passes through an LED reticle, where it gets finely pixelated to ensure edge-to-edge part consistency and accuracy. Often, parts must be carefully stripped from the vat, often a slow and delicate operation. LSPc technology utilizes a self-lubricating, flexible film that prevents sticking to the print and the underlying screen, allowing for significantly faster printing. To ensure process consistency, a thermal management system is also integrated to overcome heat build-up from high-speed printing.
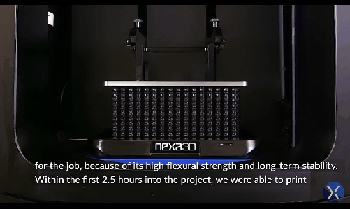
LSPc technology has resulted in dramatic improvements in production cycle times and yields. Since the speed of the output is based entirely on the vertical height of the build, the total print time is the same no matter how many parts you print. At top speed, the process can achieve one vertical inch every 2.5 minutes. Even at this speed, the printer achieves injection-molded quality with sharp angles, smooth surfaces and perfectly round holes. Overall, the LSPc process enables production speeds up to 6.5 times faster than other 3D printers in its class.
Integrated cleaning and curing
xWash is a cleaning station designed for Nexa 3D printers that uses proprietary cleaning agents optimized for 3D printing and sustainability. To move a part from the printer to the wash station, you simply slide the base plate with the part out, slide it into the washer, and it will be processed automatically. The scrubber offers a fully adjustable cleaning cycle, starting with a pre-programmed cleaning recipe, enabling the user to optimize the cycle based on part geometry and material. This facilitates efficient and consistent cleaning of various parts within minutes. To maximize throughput, it can accommodate two build plates simultaneously.
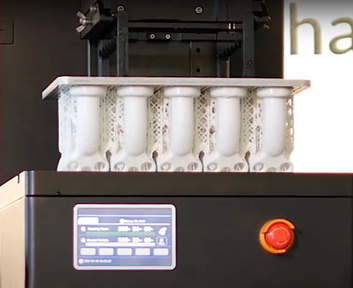
xCure was designed to enable mass production of photopolymer parts with good performance, while also allowing for easy part and printer consistency. It also comes with a prescribed part machining menu with the same process controls for high dimensional accuracy and structural integrity, regardless of part size or complexity. Like the washer, this unit also serves as a companion to Nexa3D’s 400-series printers, curing three build plates simultaneously, or placing parts on translucent racks and curing them individually.
The curing station uses high power LEDs, operates at dual wavelengths, and continuous UV and thermal curing modes. It is built to global industrial structural and safety standards and operates in three curing modes: UV only, heat only and UV + heat.
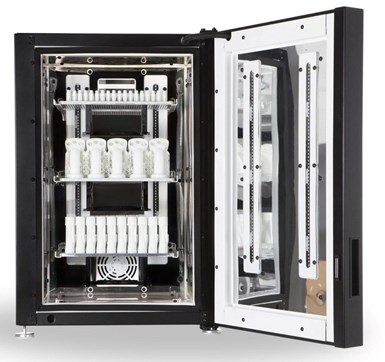
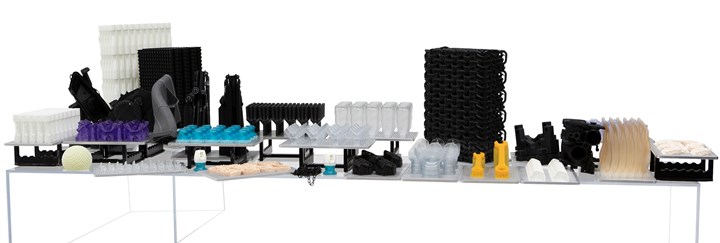
These materials are custom-made for the LSPc process to provide high-speed machining, durability and accuracy. Included in the current resin lineup are:
As for picking materials, Nexa3D helps through its Ximplify automated 3D printing decision support portal.In addition to analyzing which parts are best for 3D printing, Ximplify will recommend the best printers and materials to maximize performance, and provide complete part cost and
invest
Return Analysis. The application will recommend materials for a part, taking into account functional requirements and material machinability. Simply put, it finds the fastest way to make the part you need. After each session, Ximplify automatically generates a report to support the entire decision-making and implementation process.
(responsible editor: admin)
0 Comments for “Nexa3D: Unlocking how to increase polymer additive manufacturing productivity by 20 times”