OECHSLER
OECHSLER
Utilize industrial scale3D printingtechnology and
BASF
The company’s high-performance hyper-printed TPU01 has developed a new generation of hiking backpacks.The main purpose is to use3D printingThe Lattice Comfort Elements replace traditional foam-based back pads to enhance the hiker’s carrying experience. The result is an innovative design of a hiking backpack that provides the comfort experience strongly demanded by outdoor enthusiasts.In addition, Yuk
Xerox
OECHSLER also uses 100% recycled materials to satisfy hikers’ desire for a sustainable lifestyle.
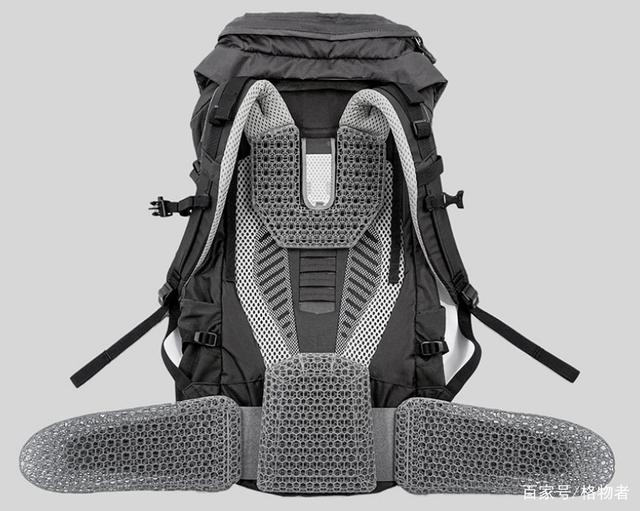
Dr. Leonhard Klein, one of the 3D printing project managers at OECHSLER, spends his summer hiking trips. After hours of loitering, his shirt was uncomfortably damp in his backpack. As usual, he changed his shirt and kept walking.
Even with very high-quality equipment, unpleasantly wearing comfort is still where the pack and body fit. Other hikers have the same problem. Back at the office, he took a closer look at how to address this potentially inevitable problem.
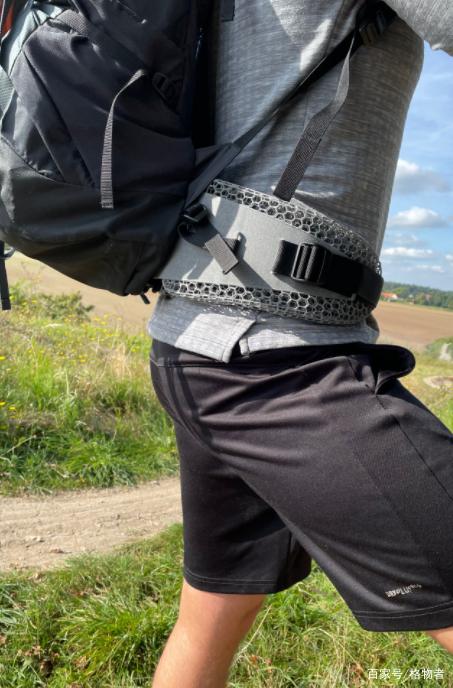
What would a perfect harness look like to minimize warmth and friction? After that, the additive manufacturing team went down and redesigned the traditional rear liner, tested to eliminate the various analyses of pressure points, established the perfect geometry, started the file programming design and the first print test.
After a few weeks, they tested the first printed back pads, including the abdominal belt, and felt a huge improvement.
Thanks to the freely designable lattice structure, through the use of 3D printing, a fully integrated cushioning experience unlocks superior comfort. The open-cell structure of the 3D-printed pads and hip fins strongly enhances air ventilation and minimizes heat build-up, resulting in significantly lower temperatures (3-5°C) and a rise in relative humidity in the contact area of the hiker’s back.
In addition, the maximum pressure and average contact pressure were significantly reduced.
The damping properties of the lattice structure can be tuned by the geometry of the lattice, the thickness of the struts, and the size of the lattice. 3D printing allows different regions of the lattice to have varying degrees of stiffness, increasing damping performance and comfort.
The four different examples below showcase O’Cold’s versatile materials and design options, which offer limitless flexibility in function, comfort and visual impact.
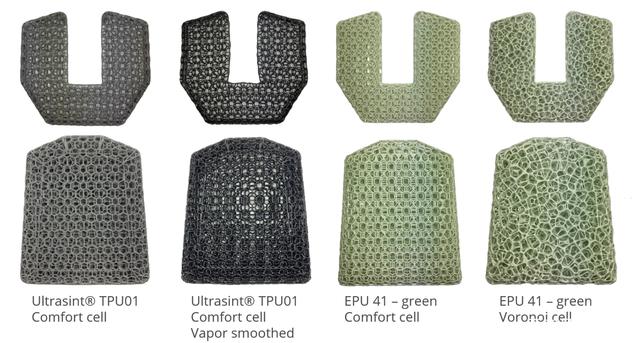
Driven by the idea of providing customers with more flexibility and productivity, OECHSLER’s 3D enables small batches, high-volume series production and complex components. The special ultra-short TPU01 material is a versatile TPU that provides strong, flexible and very durable component performance combined with excellent surface quality.
In addition, the material is very easy to print, has high process stability, is3D printing marketOne of the highest throughput flexible materials available. As an additional material option, Carbon’s EPU41 is a production-scale elastomeric material especially suited for elastomeric lattices that require high elasticity. The duration of a print depends on the lattice structure and is therefore very variable.
Thanks to the design flexibility offered by additive manufacturing, back pads and hip fins can be produced in one shot — reducing assembly steps, assembly time, and ultimately cost — no longer needing gluing or sewing.
In addition, the unprocessed ultra-smart TPU01 powder is completely reused in subsequent print jobs. Also, printed parts are 100% recyclable at the end of their life cycle. This makes the OECHSLER 3D printed hiking backpack elements a completely sustainable solution.
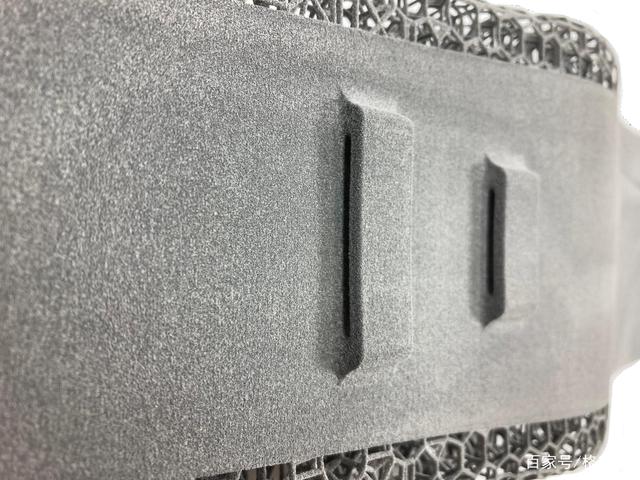
The dorsal pad and anal fin represent the key interface between the hiker and the hiking pack. By using additive manufacturing, we can achieve superior comfort and functionality – and as a passionate hiker, I believe this will revolutionize backpack manufacturing.
0 Comments for “OECHSLER’s 3D printed travel backpack for hiking will fill your soul with wanderlust”