AML3D signed a framework agreement with the Institute of Frontier Materials (IFM) of Deakin University on October 18, 2021. The two parties used the new agreement to formulate a new alloy material development project, using IFM’s facilities, capabilities and expertise to develop next-generation materials and high-strength alloys for WAM technology, further enhancing the technical and competitive advantages of AML3D.

The cooperation focuses on optimizing high-strength alloy technology and developing and producing3D printingAnd wire materials for the welding market.The project includes the development of new alloys and their use in the manufacture of high-strength coils without
Post-processing
. This will open up new markets and applications for WAM, such as applying WAM technology directly to maintenance and repair tasks of existing vehicles and structures (subsequent heat treatment may not be feasible).
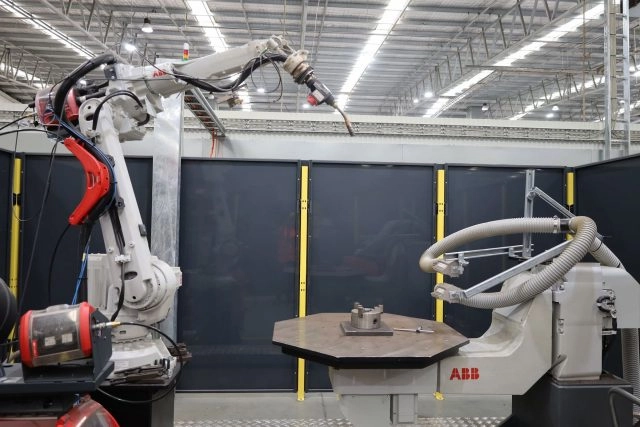
AML3D expects to develop new technologies from the cooperation, open up new target industries and departments, and support the company’s geographic and departmental expansion.For example, the goal of the two parties’ recent high-strength aluminum-scandium wire raw material project is to expand to marine, national defense, and
aviation
aerospace
In the Asia-Pacific region (Japan, South Korea), Europe (Germany, France, and the United Kingdom) and North American markets, and through specific IP and company brands, it creates opportunities for customized wire material sales. As projects related to the framework agreement are currently underway, AML3D has identified additional development opportunities for alloys with commercial results, which will be determined separately according to the agreement.
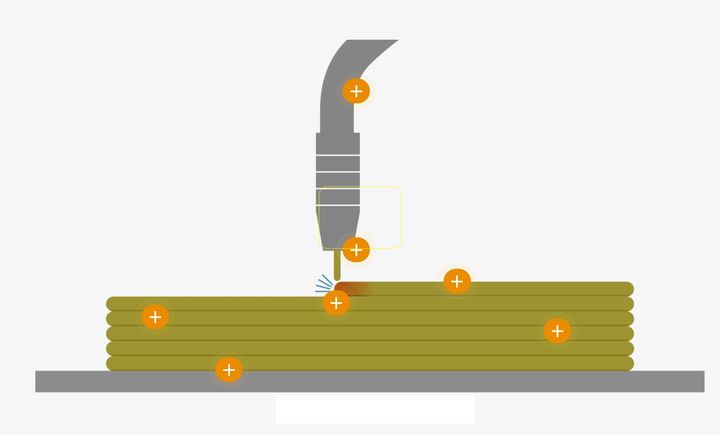
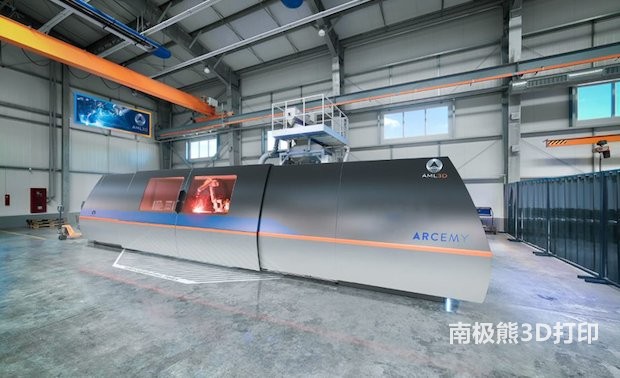
AML3D’s WAM process (US20210016381A1) passed the examination of the Australian Patent Office in June 2021. The patent covers methods and equipment for manufacturing 3D metal parts. The main coverage items include the use of any weldable metal to make parts through solid free-form manufacturing, and enhancements through atmospheric protection devices and cooperative heating and cooling equipment; computer-generated three-dimensional models of parts, and cutting the models into a set of parallel slice layers , Divide each layer into a set of virtual one-dimensional pieces to form a layered model of the part in a specific direction; and upload the layered model to the welding control system for manufacturing 3D metal parts. Similar to WAAM technology, the surface quality of printed products manufactured by WAM is very rough and requires the use of CNC milling equipment for surface treatment.
AML3D’s arc3D printingThe platform Arcemy® uses this wire additive manufacturing (WAM®) process.
WAM® uses electric arc as heat source and metal wire as raw material to produce free-form parts. Wire arc welding technology is combined with a specially programmed welding robot to manufacture large metal parts according to 3DCAD, which can be machined/polished after printing. WAM® brings together advanced welding, CAD
software
Design and robotics.
(Editor in charge: admin)
0 Comments for “Open up new markets and applications for WAM! AML3D and IFM sign a high-strength alloy development agreement”