According to foreign media reports, researchers at Oak Ridge National Laboratory (ORNL) use additive manufacturing (3D printing) Method to make a lightweight aluminum alloy, and demonstrated its ability to resist creep or deformation at 300°C.
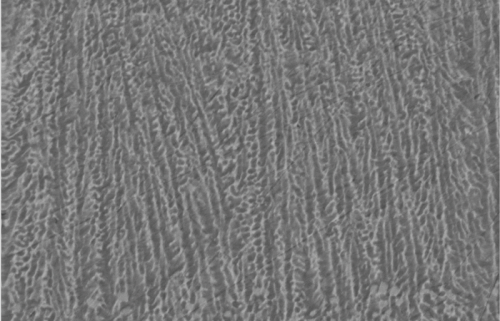
In the car,
aviation
aerospace
In defense and space applications, materials that can work normally need to be resistant to high pressure and high temperature. The ORNL research and development is made of aluminum, cerium and other metals, and is printed using a laser powder bed system. The system achieves precise results by depositing a thin layer of material at a time. The researchers printed out pistons made of alloy and used them in full-size engines. The printed pistons will undergo additional testing in a four-cylinder turbocharged engine.
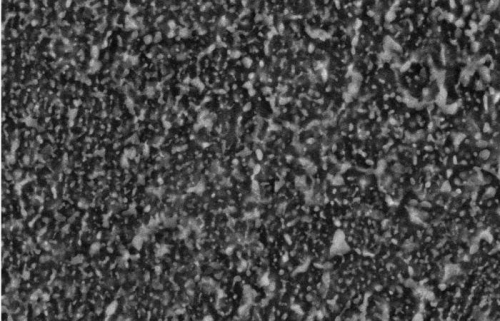
ORNL member Dr. Ryan Dehoff said: “Using a powder bed3D printingThe alloy rapidly solidifies into small, stable strengthening particles in the microstructure, resulting in the significant high-temperature creep resistance that we have measured. We have expected a significant improvement, but we are still surprised by the strength and stability of the alloy. “
The research background is as follows:
Through the use of additive manufacturing (AM), component production can have greater geometric flexibility and design space, so as to achieve complex cooling channels, grid geometries and complex near-net shape parts, which are not possible with traditional manufacturing techniques of. Specifically, in aluminum alloys, the use of AM can reduce the weight of structural components in aerospace and automotive applications. However, due to the tendency of solidification and cracking, the traditional high-strength forged aluminum alloy is not suitable for the complex thermal cycle of AM.
For example, AM of alloy compositions similar to 7075 and 2024 show significant processing limitations due to solidification cracking. Although the processing parameters can be carefully designed in simple parts (such as cubes) to reduce solidification cracks, the optimized parameters may not necessarily translate into complex parts.
The difficulty of traditional alloy processing has led to the widespread adoption of near-eutectic Al-Si in the aluminum additive community, specifically Al-10Si-Mg alloy. These alloys exhibit excellent castability and resistance to solidification cracking, but their strength is much lower than that of traditional wrought alloys, and their strength retention at high temperatures is poor.
Due to the above-mentioned problems in the traditional additive manufacturing process of forged aluminum alloys and the limited performance of aluminum-silicon alloys, people began to study new aluminum alloys specifically designed for additive manufacturing. Among them, the Al-Ce system has attracted much attention due to its high thermal stability and resistance to solidification cracking of castings.
(Editor in charge: admin)
0 Comments for “ORNL 3D printed pistons with aluminum alloy, tested in full-size engines”